Introduction
The III-V semiconductor material InGaAs has a direct band gap and high optical absorption efficiency in the near-infrared band,which can be matched with the lattice of InP materials with good collisional ionization properties as one of the replaceable indirect band gap silicon-based materials[1]. Avalanche photodiodes(APDs)fabricated of InP and InGaAs materials for quantum key distribution[2],deep-space communications[3],3-D light detection and ranging[4,5],etc.,have many advantages such as high performance,high reliability,and low cost making a promising development outlook as optical signal detector applications. However,the performance of APDs is often limited by lattice defects in InP and InGaAs materials and the process conditions as the improvement of the structures. Therefore,preparing high-performance InGaAs/InP APD material remains challenging for researchers.
Molecular beam epitaxy(MBE)technology which has become more advanced in recent years,can control the parameters in the material deposition process,such as temperature,gas flow rate,sputtering,and deoxidation conditions,and precisely control the material thickness at the atomic layer scale,thus effectively regulating the material crystal structure and properties such as mobility,dark current and light saturation current[6,7]. In the MBE process,the atmosphere of evaporative sources is used to remove natural oxides from the substrate surface and protect against As evaporation damage,thus avoiding pollution from oxygen and other gases,known as deoxidation protection[8,9]. However,the effects of deoxidation atmospheres such as As and P sources on the performance of materials and devices,like impurities at arsenic-phosphorus heterojunctions,still need further research and optimization.[10,11].
In this paper,InP substrates were deoxidized under the atmosphere protection of As4 and P2,respectively. An ultra-high vacuum solid source molecular beam epitaxy(MBE)system grew lattice-matched In0.53Ga0.47As film and APD full-structure materials. The material minority carrier lifetimes were characterized by time-resolved photoluminescence(TRPL). The variation of As and P atoms and impurity concentration with thickness at the material structure interface were gauged by SIMS. The fluctuation of the In0.53Ga0.47As/InP heterojunction interface and necessary geometrical information is observed by scanning transmission electron microscopy(STEM). Finally,planar APD devices were prepared,and the IV characteristics were measured.
The effect of As-source deoxidation conditions is superior to that of P-source deoxidation conditions in terms of material surface morphology,lattice quality,minority carrier lifetime,and dark device current. This work offers a practical foundation for identifying optimal epitaxial growth and device processing parameters for InP-based InGaAs/InP.
1 Experiments
1.1 Material growth
The left side of Figure 1 shows the InGaAs/InP APD device structure cross-section,and the right shows the electric field distribution. To evaluate the effect of different deoxidation atmosphere conditions of As4 and P2 on the APD device performance,we grew high-quality InGaAs/InP APD epitaxial materials on AXT(100)InP substrates using the MBE(DCA P600)system. A three-temperature valve-controlled solid-state phosphorus cracking source and a two-temperature valve-controlled arsenic cracking furnace were used as the group V sources,and conventional Knudsen cells for Gallium and Indium are used as the group III source.
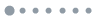
Figure 1.Profile diagram and internal electric field distribution of InGaAs/InP APD structure
The InP substrate was first put into the load lock and baked at 200°C to remove the adsorbed water vapor and then degassed in a pretreatment chamber at 300°C for 20 min. In the growth chamber,the intensity of the beam flux of each source at different temperatures was corrected to determine the growth temperature of each source. The beam flux ratios of group V and group III elements were determined using the beam flux monitors(BFM). The substrate was then transferred to the growth chamber. The substrate temperature of sample A was elevated under the protection of the As4 atmosphere,and sample B was performed under the P2 atmosphere to desorb the oxides from the surface. A clear 2×4 reconstitution stripe appeared on the reflection high-energy electron diffraction(RHEED)fluorescence screen,indicating desorption of the oxide layer on the substrate surface[9]. Afterward,the sample holder temperature continued to be raised by 30°C(thermocouple temperature ~640°C)and maintained for 6-7 min to allow complete desorption of the oxide film and flattening of the atomic layer on the substrate surface. After cooling down to the growth temperature,the beam equivalent pressure(BEP)ratios of each beam source furnace were controlled by valves to epitaxially grow 1~2 μm lattice-matched unintentionally doped In0.53Ga0.47As/InP film materials,and APD structured wafers. The APD material was based on a separate absorption,grading,charge,and multiplication(SAGCM)structure,including an n-InP buffer layer,an intrinsic In0.53Ga0.47As absorber layer,an InGaAsP component gradient layer,an n-type highly doped InP charge control layer,intrinsic InP cap layer,divides into Sample A(As4 deoxygenated)and Sample B(P2 deoxygenated)[4].
1.2 Material characterization
After growth,the materials were characterized using XRD to determine the component values and the lattice quality. Van der Pauw method Hall test(Ecopia HMS-3000)was performed to characterize the carrier transport properties of epitaxial In0.53Ga0.47As/InP materials of different thicknesses.
TRPL can characterize the direct electron-hole recombination(band-to-band recombination),Shockley-Read-Hall(SRH)recombination,and other non-radiative recombination information of materials absorbing pulsed laser radiation. [12]. The time-correlated single-photon counting(TCSPC)is a crucial technique for fluorescence lifetime imaging due to its high signal-to-noise ratio and high temporal resolution[13]. The dynamics of carrier recombination in APD structure materials were studied using the TCSPC method with a 1064 nm laser,and the results were compared with samples from the anti-reflective coating(ARC)SiNx passivation treatment(front-end process)[14]. The single-photon detector is a Hamamatsu H10330C -75 microchannel plate detector with a time resolution of 20 ps.
The SIMS principle is to use a focused ion beam sputtering the surface of semiconductors and then use a time-of-flight or mass spectrometer to analyze the secondary ions formed in the sputtering process,which allows for high-precision detection of the elemental distribution and interface impurities in the film materials from nanometer to tens of microns in depth[15,16]. We used the SIMS(Cameca IMF 5F,Evans Analytical Group)test to observe the high-precision measurement of different elemental concentrations in structural samples to analyze and determine the growth behavior and quality of InGaAs lattice epitaxy on InP substrates. The detection limit(DL) is over 1.0×1010 to 1×1016 atoms/cm-3.
Interfaces and defects in MBE-grown InGaAs/InP films were further examined using aberration-corrected STEM. Cross sections of STEM sample A(As4 deoxygenated)and sample B(P2 deoxygenated)were prepared using the focused ion beam(FIB)technique(Helios-G4-CX,Thermo Fisher Scientific). The STEM investigations were performed with a field-emission STEM(Themis Z,Thermo Fisher Scientific)fit with a probe and an image aberration corrector(SCORR and CETCOR,CEOS GmbH). The microscope was operated at 300 kV. For HAADF-STEM imaging,the probe semi-convergent angle was set to 21.4 mrad,and the semi-collection angle of the detector was arranged from 76 to 200 mrad. The STEM images were collected with[101]zone axis.
1.3 Device preparation and characterization
After characterization,the incident surfaces of APD materials were coated with SiNx ARC to eliminate reflections from the air-InP interface. The wafers were fabricated into 20 µm diameter planar InGaAs/InP APD by front-end processes such as Zn doping and UV lithography,including Device A(As4 deoxygenated)and Device B(P2 deoxygenated)[11,17]. The IV characteristics were measured by a semiconductor parameter analyzer(Keysight 4200)at room temperature.
2 Results and discussions
2.1 Hall effect analysis
Figure 2 shows the carrier concentration n and Hall mobility μ of epitaxially grown unintentionally doped In0.53Ga0.47As/InP films under different deoxidation atmospheres at 330K and 77K. Four samples exhibit lower carrier concentrations at 77K than 300K. In contrast,μvalues at 77K are higher than that at 300K,with mobility even exceeding 6.0×104 cm2/Vs. This is due to the decreased lattice vibration scattering caused by low temperatures(),fewer impurity scattering noises from the In0.53Ga0.47As intrinsic growth(),and lower transport energy of the thermally activated carriers. Thus,the In0.53Ga0.47As/InP materials with As4 protective atmosphere possess superior carrier transport capability than those with P2 deoxidation protection,with higher mobility and lower carrier concentration. This suggests that As4 deoxidation can help reduce impurity contamination and associated point defects introduced by the growth process.
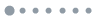
Figure 2.Hall carrier concentration and mobility plot
2.2 TRPL analysis
Figure 3 shows the time instrumental response function(IRF)fluorescence decay curves generated and extracted under a single laser pulse for the TRPL test. For the APD structured wafer,the 1064 nm light pulse is mainly absorbed by the InGaAs layer,and the minority carrier lifetime is reflected in the InGaAs layer. It is generally believed that the InP cap layer has little impact on the absorption layer of the 1064 nm light[10]. The double exponential fit(ExpDec2)using the nonlinear least squares inverse convolution method is set to obtain the minority carrier lifetimes t1 and t2,which generally correspond to the SRH recombination t1(shorter lifetime)and radiation recombination t2(longer lifetime)of the InP charge layer or InGaAs layer of the APD materials. Although the model presents several limitations and drawbacks,it is accepted due to its simplicity [18].
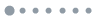
Figure 3.TRPL spectra of APD wafers
The smoother the decay of the measured TRPL curve,the larger the τ value,indicating the stability of wafer quality. The smaller the variation of the τ value,the better the wafer quality. We can see that As4 deoxidation has a longer minority carrier lifetime t2 than P2 deoxidation,indicating that the wafer of As4 deoxidation is of better quality than that of P2 deoxidation,with relatively fewer lattice defects and impurities and less radiation recombination. The t1 of the samples is tiny,which indicates that the carriers in the wafer are rapidly quenched after capture,with strong non-radiative recombination,and there may be many deep energy level recombination with high doping concentrations or background concentrations.
2.3 SIMS analysis
Figure 4(a)shows the depth distribution of Ga,As,P,In(right axis)and O,C,H,N,Si(left axis)in the MBE-grown InGaAs/InP APD wafers. The near-surface trailing in the SIMS profiles,especially for C,O,and H,can be explained by the kick-on of the impurity atoms from the surface contaminations into the depth by the primary ion beam and no more than 20-50 nm[19]. Different deoxidation conditions do not distinctly affect the concentrations of Ga and P,As,and In of sample A(As4 deoxidation)and sample B(P2 deoxidation). However,O and Si impurities increased when switching the valve sources for GaAs and InP growth(d = 2-3μm,d = 4.8-5.6μm). C and H content increase significantly at deoxidation(d = 4.8-5.6μm). In Figure 4(b),the increase in O content at d = 4.8-5.6μm is more significant for sample B than sample A. This tailing could represent impurity concentration in the matrix,or it may be caused by impurity segregation at grain boundaries and dislocations and secondary implantation of the surface contaminants. Therefore,we perform a retest to avoid the interference caused by the surface contaminants. Table 1 summarizes the peak results of the two SIMS tests for C,O,N,H,and Si impurities,with no change in the data values. However,sample B has an O concentration nearly an order of magnitude higher than A,despite being close to the detection limit. This implies that P2 deoxidation during MBE may have more negative effects than As4 deoxidation,which may cause impurity accumulation on the rough surface,lattice,and interfacial dislocations of the material[19].
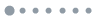
Figure 4.(a) Comparison of SIMS depth distributions for Samples via As4, P2 deoxidation,(b) Bulk regions (d = 4.8-5.6 μm) of comparison of deoxidation interface

Table 1. Average peak concentrations (cm-3 ) of impurities in bulk regions (d = 4.8-5.6 μm) from SIMS measurements.
Table 1. Average peak concentrations (cm-3 ) of impurities in bulk regions (d = 4.8-5.6 μm) from SIMS measurements.
Sample | O | C | H | Si | N |
---|
A | 2.25E+17 | 9.76E+18 | 2.08E+18 | 1.56E+17 | 1.86E+16 | B | 8E+17 | 9.09E+18 | 1.34E+18 | 3.74E+17 | 6.61E+16 | DL | 1E15 | 1E15 | 1E16 | 1E14 | 5E14 |
|
2.4 STEM analysis
Figure 5-6 shows the HAADF-STEM images of the epitaxial cross-sectional structure of sample A(As4 deoxidation)and sample B(P2 deoxidation). According to the Z-contrast imaging mechanism of HAADF-STEM,the elements of Ga,and As shown brighter contrast than P atoms,giving InP,InGaAsP,and InGaAs their distinct differences in atomic resolved images[20]. Figures 5(a)and 6(a)show the wafer epitaxial cross-sectional structure. Figures 5(b)and 6(b)show a detailed scan of the InP buffer layer and InGaAs absorber layer heterojunction interface. Figures 5(c)and 6(c)show the InP buffer and substrate homojunction interface. Sample A clearly shows the sharp and straight interface between InGaAs and InP buffer layer and InP substrate,which is atomically smooth. Sample B shows only a slightly floating heterogeneous interface. And the homogeneous interface could not be characterized with grayscale fluctuations. Stacked layer dislocations or lattice distortions may lead to interface roughness[20,21]. This indicates that sample A has a more explicit interface and better interfacial quality than sample B.
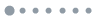
Figure 5.STEM-HAADF image of APD sample A(As-deoxidation)(a)an image of the APD structure on FIB grid,(b)the image of InGaAs and InP buffer,(c)zoom region of InP homojunction interfaces,(d)high-resolution images of the region marked with a red frame in(a)
As shown in Fig. 5(d)and Fig. 6(d),the InGaAs layer appears as dumbbells at the atomic-scale resolution,InP appear as single dots,and the interfacial atomic layers are regularly arranged[22]. It indicates that the initial growth of MBE under As4 deoxidation conditions is controlled precisely,and the InP buffer layer can be stably controlled at the atomic scale. However,the unevenness of the heterogeneous interfaces of Sample B causes some heterojunctions to be identified in atomic resolution hardly. Therefore,the As4 deoxidation process avoids more defects and improves the lattice quality. This may be because As atoms are more challenging to stay on the substrate surface than P atoms. Sufficient or excess As4 sources can ensure adequate absorption of impurities such as oxygen of the substrate surface by reducing the In-O bonding on the surface while avoiding the metallization of the As atoms on the InAs surface by desorption[23-25].
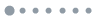
Figure 6.STEM-HAADF image of APD sample B(P-deoxidation)(a)an image of the APD structure on the FIB grid,(b)the image of InGaAs and InP buffer,(c)the zoom region of InP homojunction interfaces and stacking fault(circled). Circles indicate dislocations with different core structures,(d)high-resolution images of the area marked with a red frame in(a)
2.5 Device IV analysis
Figure 7(a)shows the current-voltage (IV)characteristics of InGaAs/InP APD Device A(As4 deoxidation)and Device B(P2 deoxidation)operating in linear mode. Based on the collisional ionization principle of phonon scattering,the hot carriers in the InP collide with the lattice to generate dark current and zero photocurrents at lower reverse bias voltages. When the APD reaches the punch through voltage (near 15 V),the depletion region extends to the InGaAs absorption region. When the reverse bias voltage is between 15V and 60V,electrons move toward the substrate and holes toward the InGaAsP grading layer and the InP multiplication layer. At the same time,the number of carriers in collisional ionization increases until the breakdown voltage(near 60 V)is reached,the current is wholly transferred to the multiplication layer,and the APD enters the Geiger mode from the linear mode[26-28]. The main components of dark current include the generation-recombination current,tunneling current,and leakage current. Generation-recombination current is affected by carrier concentrations,minority carrier effective lifetime and temperature. Tunneling current is mainly affected by band gap and trap energy levels. Higher carrier mobility and a longer lifetime can usually reduce the dark current of the device. Considering that surface leakage and weak external natural light interference have little effect on device applications,we ignore the differences in the dark current below the punch-through voltage[11,29].
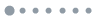
Figure 7.(a) I-V and gain characteristics of the InGaAs/InP APD,(b) TRPL spectra of ARC-APD
Compared to device A(As4 deoxidation),device B(P2 deoxidation)has a lower punch-through voltage,a slightly higher breakdown voltage,and a more extended linear region(less than 1 V). This is mainly due to the small thickness difference of the InP multiplication layer[28,30]. The elevated bias voltage increases the tunneling current in the absorption layer,which can lead to a significant increase in the dark current,thus affecting the performance and power consumption of the device. We note that near the punch-through voltage,the dark current of device B is 2.62×10-9 A,an order of magnitude larger than the dark current of device A of 1.62×10-10 A. From figure 2,the carrier concentration of the InGaAs layer with As4 deoxidation is lower,thus resulting in a lower dark current at the punch-through voltage. Meanwhile,the higher carrier mobility of InGaAs layers implies fewer intrinsic defects in the As4 deoxidation materials. Therefore,the generation-recombination current caused by defects is relatively small.
The carrier lifetime measured for wafers is not the bulk carrier lifetime but rather the effective lifetime,including surface and bulk recombination. When the surface layer of the wafer is coated with SiNx passivation,it can reduce the surface recombination and reflection loss,enhance the absorption of light,and suppress the surface leakage,which makes closer to[31,32]. Figure 7(b)shows the TRPL curves of APD wafers after ARC. Both t1 and t2 increase significantly,and the effective lifetime with As4 deoxidation is longer than that with P2 deoxidation. This indicates that ARC has improved the performance of APD,but As4 deoxidation still maintains better performance than P2 deoxidation.
Combined the IV analysis with the above Hall test and TRPL results,the APD with As4 deoxidation has lower carrier concentrations,higher Hall mobilities,and higher minority carrier lifetimes compared to the P2 deoxidation,which produces some suppression of the dark current caused by point defects or impurity defect energy levels. The SIMS and STEM results also support this view further.
3 Conclusions
In summary,we used the MBE technique to deoxidize InP substrates under As4 and P2 atmosphere protection and grow In0.53Ga0.47As/InP epitaxial layer APD structures. The material quality is evaluated by STEM,TRPL,Hall test,SIMS,and other characterization methods. The APD devices were prepared by a front-end process. The IV characteristics were measured at room temperature. The effects of MBE deoxidation conditions on the material surface morphology,lattice quality,minority carrier lifetime,and dark device current were analyzed. The results show that compared with P2 deoxidation,As4 deoxidation can significantly improve the MBE material quality,make the heterogeneous interface structure stable and sharp,improve theHall mobility,reduce thecarrier concentration,lengthen the minority carrier lifetime,and have a specific suppression effect on the device dark current caused by point defects or impurity defects. This study provides valuable information on InP/InGaAs APD material devices prepared by MBE.