1. Introduction
Concentration detection, a process of obtaining information about the concentration of a liquid or gas, is an indispensable element in biological detection, chemical production, and the food and security industries[1–3]. Various advanced sensing techniques, including electrochemical analysis[4,5], spectral analysis[6–8], and mass flow meter, are proposed with the rapid development of measurement techniques. Compared to other methods, spectral analysis is a more convenient and rapid concentration detection method. In principle, the absorption, scattering, or molecular vibration of the excited light induced by the detected object will be recorded directly via spectrometers or transformed into an electrical signal via photodevice. The sample’s concentration will be obtained by observing the variation of spectra or the photocurrent. However, the large volume of the measuring equipment and the high cost of the spectral equipment limit the application of devices, such as ultraviolet spectrophotometers and Raman spectrometers, in low precision and outdoor concentration detection[9,10]. Therefore, there is an urgent need for a compact, low-cost, and fast response concentration sensor.
GaN devices, including the LED and photodetector (PD), have drawn great research attention in illumination, display[11,12], and optical communications[13,14] due to their success in epitaxial growth, processing technology, and structural design compatibility[15–17]. On the other hand, researchers have also observed the coexistence of light emission and detection in multiple quantum wells light emitting devices (MQW-LEDs)[18,19]. This makes the GaN-based platform suitable for developing low-cost, integrated optical sensing devices that consume less power. For example, GaN-based optical sensors have been recently reported for image sensing[20,21], motion and hardness sensing[22,23], and audio cast applications[24]. It will be of great significance to combine the GaN photonic chip and the principle of concentration detection. Then, a miniaturized and inexpensive concentration sensor will be prepared.
This paper presents a concentration sensing system by attaching a monolithic InGaN/GaN photonic chips array to a cuvette with a silver reflector. By utilizing LEDs as the light source and photodetector, the change in photocurrent caused by solution absorption is converted into concentration information. Additionally, different from other reports, we consider the influence of crosstalk between chips on the sensing characteristics of the device. The relative position of the LED and the PD, the number of PDs, and the drive current of the LED are optimized to realize an excellent sensing performance. Finally, a demo prototype with a sensing module of less than 5 cm and a data processing back-end of less than 10 cm is built to further confirm the utilization potentiality of the system.
Sign up for Chinese Optics Letters TOC Get the latest issue of Advanced Photonics delivered right to you!Sign up now
2. Experiments
2.1. Fabrication of InGaN/GaN LED array
Similar to previous work[25], monolithic InGaN/GaN photonic chips are fabricated with photolithography, inductively coupled plasma (ICP) etching, and evaporation with 4-inch GaN sapphire-based GaN (Fig. 1). From top to bottom, the structure of the epitaxial sheet is as follows: the Mg-doped p-GaN, the InGaN/GaN multiple quantum wells, the Si-doped n-GaN, the unintentionally doped GaN (u-GaN), the aluminum nitride buffer layer, and the sapphire substrate. During fabrication, a mesa region with a unit arrayed square () is defined by photolithography and ICP etching to expose the n-GaN surface first. Then, with a second photolithography (a little larger than the previous mesa) and ICP etching, the samples will be further etched into the sapphire substrate to form isolated PN junction devices [Figs. 1(a) and 1(b)]. The transparent indium tin oxide (ITO) current spreading layer was deposited on the p-type GaN region, and Au ohmic contact electrodes were followed to form the LED [Figs. 1(b) and 1(c)]. To protect and improve the light emission properties of the as-fabricated devices, a layer was deposited onto the top surface of the device by plasma-enhanced chemical vapor deposition. The back sapphire substrate was polished down to 200 µm, and the Ag reflector layer was deposited to the backside of the device [Figs. 1(c) and 1(d)]. Enlarged individual device structures are shown in Figs. 1(f)–1(h). The CCD image of individual devices can be seen in Fig. 1(e). The U-type surface p-electrode was introduced to improve the current uniformity.
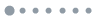
Figure 1.(a)–(d) Schematic diagram of the sample preparation process. (e) CCD image of the actual sample. (f)–(h) The enlarged individual device structure of each step. (i) Schematic diagram of the liquid concentration sensor module and (j) the principle of the sensing system.
2.2. Design of concentration sensing system
A sensing system is built with the InGaN/GaN photonic chips as the sensor module and a matching back-end circuit for data processing and display. As shown in Figs. 1(i) and 1(j), the LED array was bonded to a PCB substrate and then attached to a cuvette with a silver reflector about 1 cm away to form the sensing module. In theory, the band structure in the InGaN/GaN multiple quantum wells makes the emission and absorption of the device overlap[26]. The photocurrent of an individual LED (receiver) can be controlled by a nearby LED (emitter) and realize a sensing channel. Since the light will pass through the liquid in the cuvette, the solution-induced optical changes in the channel will be transformed into changes in the photocurrent of the receiver. Unlike other designs, we use two receivers relatively far from the emitter to increase the photocurrent while reducing the crosstalk between chips, and a silver back reflector is used to enlarge the sensing signal further. After optimizing the properties of the sensing module, a well-designed data processing circuit with data acquisition, amplification, filtering, concentration calculation, and display functions was used to form the final prototype. All the experiments were conducted at 20°C and in dark conditions.
3. Results and Discussion
3.1. Luminescence and detection characteristics of the InGaN/GaN LED
The first decisive element of a photoelectric integrated sensing module is the electroluminescence (EL) properties of the individual units as emitters. The current-voltage (I-V) properties of the individual InGaN/GaN LED are measured by an enhanced Keithley source meter (B2901 of 100 fA) and shown in Fig. 2(a). The turn-on voltage is about 2.4 V. The EL spectra of the sample are measured with a spectrograph (Acton SP2500i) and shown in Fig. 2(b). The InGaN/GaN LED shows broad spectra peaked at 475 nm, full-width at half-maximum (FWHM) of 29.3 nm, and chromaticity coordinates (0.136, 0.1423) in the CIE 1931 chromaticity diagram of Fig. 2(c). Based on the design principles in Figs. 1(i) and 1(j), the front light output characteristics of the LED can highly influence the sensing properties of the device. Polarizability , defined as with and as the EL intensity parallel to the and directions[27], can be used to evaluate the front light output characteristics of the LED. Based on the polarization properties inset in Fig. 2(a), the calculated polarizability of the devices is 0.56. It is larger than typical GaN LEDs with in-plane structures[28,29] and is attributed to the Ag mirror on the back.
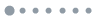
Figure 2.EL properties of the InGaN/GaN LED as an emitter. (a) I-V and polarization properties. (b) Drive current-related EL spectra. (c) Coordinates in the CIE 1931 chromaticity diagram. (d) Spectral responsibility and normalized EL.
The second decisive element of a photoelectric integrated sensing module is the optical response properties of individual units as receivers. The photocurrent response decreases gradually for the incident light (400–600 nm), as shown in Fig. 2(d). The overlap between the EL and response spectra (about 40 nm) makes the receiver excited by the LED on the same chip, and this is the key to realize a miniaturized on-chip integrated sensor[30,31]. I-V curves of the individual InGaN/GaN LED as the receiver are measured under irradiation of the nearby LED. Without the exciting light, the receiver exhibits low photocurrent levels of nA, as shown in Fig. 3(a). The photocurrent will be increased to a µA level under light illumination. The photocurrent will increase with the addition of the exciting power and bias voltage of the nearby LED, as shown in Fig. 3(b). Although the photocurrent is higher while adding the bias voltage, we use a bias voltage of 0 V for further study since the later system design will be more straightforward, and the background noise will be less. The dynamic photocurrent response of the proposed LED and PD channel with water is shown in Fig. S2 (Supplementary Material). For a driven period of 1 s at the light source side, the readout signals from the PD side are highly stable throughout 200 cycles, and the photocurrent profiles of the two different periods in the figure inset are almost identical, which confirms the durability and stability of the sensor. The transient photo-response in Fig. 3(c) implies the recovery time, defined as the time required for 90%–10% change in the photocurrent, is 3.8 ms. It is fast enough for steady state sensing applications.
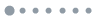
Figure 3.(a) I-V curves and (b) photocurrent variation with different currents of the LED. (c) Transient photoresponse. (d) PD number-related and (e) distance-related photocurrent. The inset is the experimental setup.
The three lights in Fig. 1(j) are the lights transported directly from the sapphire substrate, the light from the nearby LED through the solution, and the reflected light from the attached mirror, respectively. They will influence the photocurrent of the receiver. The whole photocurrent is doubled for dual-PDs [Fig. 3(d)]. Thus, increasing the number of PDs can further improve the sensing properties. In principle, only the light transported in the solution will benefit the latter sensing application. Tuning the distance between the emitter and receiver is a helpful strategy for reducing the crosstalk between chips. For a fixed drive current of 5 mA, as shown in Fig. 3(e), if the emitter and receiver are near to the emitter (1.5 mm), then the light transport directly to the PD from the sapphire substrate plays a dominant role. The photocurrent can reach 5.75 µA. If the gap distance is 4.5 mm, then the light transport in the solution mainly contributes to the photocurrent, and the current will decrease to 0.275 µA. The photocurrent summary in Fig. 3(e) also indicates that the Ag reflector in the back of the cuvette will slightly increase the photocurrent in the 80–110 nA region for all situations. This value is at a similar level of photocurrent for the far coupling distance of the PD and the LED.
3.2. Realization of liquid concentration sensing system and device optimization
Based on the discussion in Figs. 2 and 3, double PDs, a far distance gap between the PD and the LED, and the introduction of a silver reflector may help improve the sensing performance of the device. The actual photograph of the sensing module is shown in Fig. 4(a), and the size detail can be seen in Fig. S1 (Supplementary Material). The solution to be detected will be added to the cuvette to assess its concentration. Any solution influencing the light-transporting properties of the LED and the PD will make the system work. EL spectra data are in the absorption region of the methyl orange, as shown in Fig. 4(b). Thus, methyl orange is set as the tracer agent of the concentration detection system. Measurement position-related EL spectra of the LED as an emitter are presented in Fig. 4(c).
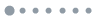
Figure 4.(a) Actual photograph of the sensor module. (b) EL and absorption spectra of the InGaN/GaN LED. (c) Position-related EL properties of the InGaN/GaN LED. (d) Position-related absorption spectra of the methyl orange in the cuvette.
The EL intensity is symmetrical and uniform for the whole region of the device, as shown in Fig. 4(c). To further evaluate the uniformity of the dye in the cuvette, with the help of a homemade angular resolution system[32], the position-related absorption of the methyl orange solution in the cuvette is measured (see details in Supplementary Material).
For an exciting area of about 8 mm in diameter, the position-related absorption shown in Fig. 4(d) indicates a uniform light absorption with the whole area in the 400 nm to 550 nm region. Together with the data in Figs. 4(b)–4(d), our sensing system’s mechanism can be concluded like this: the emitter’s light will be coupled to the receiver from the solution in the cuvette and transformed into the photocurrent. The concentrated related light absorption will reduce the photocurrent and realize a sensing process.
The sensing properties of the sensing module are further optimized. As demonstrated in Fig. 5(a), with the experimental setup inserted in Fig. 5(c), the photocurrent for double and far-coupled receivers will increase linearly with the addition of the drive current. Due to the absorption of the methyl orange, the photocurrent decreases after adding methyl orange to the system. Methyl orange-induced photocurrent variations in Fig. 5(a) also indicate that, for the LED drive current from 0 to 9 mA, the methyl orange will cause a photocurrent decrease in the 11.1 to 84 nA region.
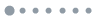
Figure 5.(a) Photocurrent variation under different emitter currents and methyl orange-induced photocurrent variations of the sensing module. (b),(c) Photocurrent variation at different liquid concentrations with double PDs and different coupling situations. (d) Relationship between photocurrent and concentration and linear fitting. The inset shows the corresponding experimental diagram.
Another advantage of double and far-coupled receivers lies in stabilizing the sensing signal. As shown in Figs. 5(b) and 5(c), for a fixed drive current of the emitter at 8 mA and solution concentration region of 0 to 6 µmol/L, the photocurrent changes of the doubled receivers at the near situation are in the region of 0 to 30 nA. This value is 0 to 45 nA at the far couple situation. More interestingly, the signal in Fig. 5(c) is more considerable and stable. With the experimental setup in Fig. 5(c) and fixed drive current of 8 mA, the relationship between the photocurrent and the concentration is shown in Fig. 5(d). It presents a well-linear relationship between concentration and photocurrent.
To make the sensing system more convenient, a demo prototype based on the sensing module is built with the optimized sensing module and the matched back-end circuit (see details of the whole system in Fig. S3 and the components list in Table S1 of the Supplementary Material). As shown in Fig. 6(a), integrated circuit boards are designed to collect the photocurrent from the sensing module and perform further concentration calculations and display. The size of the sensing module is less than 5 cm, and the size of the data processing back-end is less than 10 cm [Fig. 6(b)]. The solution concentration is first transformed to the photocurrent with the sensing module. Then, the photocurrents will be enlarged with the current-voltage conversion unit (OPA627APG4), the operational amplifier (NE5532D 8R2G), and a series of electrons. In order to simplify the circuit design, the detector works at a bias voltage of 0 V, which can reduce the influence of the background signal on the data acquisition and improve the signal-to-noise ratio. After amplification and filtering, the data will be sent to the data processing chip (STM32F103).
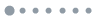
Figure 6.(a) Circuit board diagram, (b) actual image, and (c) data processing flow chart of the concentration sensing demo prototype. The inset shows the actual image of the sensing module. (d) Relationship between the photocurrent and collected ADC voltage. (e) Relationship between concentration and collected ADC voltage. (f) Real-time display of the system working status.
With the help of a single-chip computer, the photocurrent is mapped to the corresponding concentration and displayed through the monitor [Fig. 6(c)]. To evaluate the stability of the data processing module, the relationship between analog-to-digital converter (ADC) voltage and the input current is plotted in Fig. 6(d). This implies that the ADC voltage increases linearly with the addition of current. Moreover, the voltage from the ADC is linearly increased with the concentration below 40 µmol/L with a conversion factor of 6.993 mV/(µmol/L), as shown in Fig. 6(e). The corresponding voltage range is 3645 mV to 4052 mV. Since the max system error of voltage is 2 mV, the calculated system resolution is 0.286 µmol/L (see details in Fig. S4 of the Supplementary Material). During the concentration measurement, the sensing works at 9 mA, and the measured results for pure water and a solution concentration of 5.04 µmol/L are shown in Fig. 6(f).
For comparison, Table 1 lists the tested object, sensitivity, concentration range, effective area, and signal strength information of other designs, including optical sensors, spectral analysis-based sensors, and microwave-based sensors. With a similar chip area, the method proposed in this article has a high sensitivity of 13 nA/(mg/L) and a comprehensive and linear measurement range of 0–40 µmol/L. Due to the design of the back-end processing circuit, which converts the weak current signal into a voltage signal, the design can operate independently without the need for expensive and bulky current acquisition equipment, achieving more portable sensing.

Table 1. Comparison of the Proposed Liquid Concentration Sensor and Previously Reported Ones
Table 1. Comparison of the Proposed Liquid Concentration Sensor and Previously Reported Ones
Sensor Type | Tested Object | Sensitivity | Concentration Range | Effective Area | Signal Strength |
---|
Monolithic optoelectronic chip[33] | NaCl | 2606 nA/(mol/L) | 0–6 mol/L | 1 mm × 1 mm | 0–15.58 µA | Monolithic optoelectronic chip[34] | Glucose | – | 5%–40% | 1 mm × 1 mm | 8.7–8.545 µA | Spectral analysis[35] | Engine oil | – | 0–7 g/dL | Diameter 3 mm | −0.04–0.83 V | Monolithic optoelectronic chip[36] | Nitrite | 0.6 nA/(mg/L) | 0.2–1.2 mg/L | 12.5 mm × 12.5 mm | – | Microwave[37] | NaCl | 400 Hz/(mg/L) | 1%–5% | 7 cm2 | 11.427–11.414 GHz | This work | Methyl orange | 13 nA/(mg/L) | 0–40 µmol/L | 1 mm × 1 mm | 3.645–4.052 V |
|
4. Conclusion
In conclusion, a miniaturized and integrated concentration sensing system is designed and realized with an InGaN/GaN-based optoelectronic integrated sensing chip and a well-designed circuit module. The LED array on the sapphire wafer is fabricated for the emitter and receiver. As an emitter, the device’s turn-on voltage, EL peak, and FWHM are 2.4 V, 475 nm, and 29.3 nm, respectively. As a receiver, the photoresponse spectra peak at 400 nm with a cut-off wavelength of 470 nm and a falling edge of 3.8 ms. The chip is attached to a cuvette with a silver reflector to form the sensing module. Light from the emitter will be transported to the receiver through the solution. The variations in the solution’s concentration modulate the receiver’s photocurrent, thus realizing a sensing system. The gap distance between the PD and the LED and the number of receivers can highly influence the sensing properties of the system. Our results indicate that a large coupling distance of the double PDs and the LED can realize a consistent and reliable photocurrent signal. Finally, a demo prototype was built for the liquid concentration sensor. The size of the sensing module is less than 5 cm, and the size of the data processing backend is less than 10 cm. Additionally, taking methyl orange as the tracer agent, the system resolution is 0.286 µmol/L, and the measurement range is 0 to 40 µmol/L.