1 Introduction
Vehicle lightening has been one of the priorities of the automobile industry in recent years, especially after the AEPA (American Environmental Protection Agency) and The NHTSA (National Highway Traffic Safety Administration) have established greenhouse gas emission and average fuel consumption standards for the year 2017-2025, as lightening is considered an essential element of possible compliance pathways (Cecchel1 and Chindamo, 2018). Among all the commercially available lightening technologies, is that the substitution of materials with lightweight materials offering the greatest potential to reduce vehicle weight (Andure et al, 2012; Bhattacharyya, 2014). Therefore, the changes observed in the curb weight of the vehicle were consistent with changes in the composition of the vehicle material (Kelly et al., 2015). Designing components with low-density materials is one the most common methods for reducing CO2 emissions. Research into the manufacture of lightweight automobiles is driven by the need to reduce fuel consumption to preserve dwindling hydrocarbon resources without compromising other attributes such as safety, performance, recyclability and cost (Andure et al., 2012).
Several works have been focused on the use and comparison of different materials in the automotive industry. They can be mentioned that Cecchel and Chindamo (2018) have presented in their work a modelling system to evaluate the impact of weight reduction in light commercial vehicles with diesel engines on air quality and greenhouse gas emissions in 2018. Dubem (2016) also has stipulates in his study that despite some disadvantages bumpers composite materials (nylon-6 nanocomposite and polyethylene/palm kernel shell-iron filings), compare to conventional bumper (steel, aluminum), allow a reduction in weight; cost and impact on the environment. Other research works have studied environmental performance of lightweight materials in automobile application (Goede et al., 2009; Caffrey et al., 2015; Cischino and Di Paolo, 2016; Sooa et al., 2018).
The Life Cycle Assessment (LCA) methodology is the most indicated approach to performing the environmental assessment of lightweight solutions. Many LCA studies already exist in the transportation sector and interest is continuously growing, particularly in the automotive field (Goede, 2006; Berzi et al., 2016; Delogu et al., 2016).
Considering the automotive lightweight LCA context, literature provides several examples of comparative studies based on Fuel Reduction Value (FRV) coefficient (Konrad et al., 1996; Duflou et al., 2009; Ferreira1 et al., 2015). All the research wors are a follow-up to the studies that started initially to introduce life cycle analysis in the automotive industry (Konrad et al., 1996; Vanalle et al., 2011; Klockea et al., 2014).
In Algeria, LCA is starting to be introduced into the corporate culture, these remains difficult given the complexity and the amount of data that it requires. Nevertheless, several LCA studies have been conducted in various sectors (Boureghda et al., 2012; Cherifi, 2012; Younsi and Louhab, 2017). In 2016, the Algerian Group of Ecodesign and Life Cycle Analysis, was founded by a group of industrialists, university experts and research laboratory in food technology (LRTA), to create a forum for exchange and knowledge transfer in the field of product life cycle and ecodesign.
For our study, we will present to the company an environmental analysis of the bumpers studied and show the impact of the modification made to them. The purpose of this work is to be able to put at the disposal of an Algerian industry an ecodesign method that will permit it to integrate the ecological dimension up-stream of manufacturing processes and thus helping it in its choices and decisions. The National Company of the Industrial Vehicle SNVI, has decided to introduce more plastic material in its products in order to reduce the weight of its and reduce their environmental impacts.
The study aims to compare the environmental impacts of two bumpers, one designed in steel for more than 60 years in the mechanical workshop of the company, and the second is a prototype made of polyester in the polyester workshop of the same company. The first part of this work presents a “gate-to-gate” approach to life cycle analysis, aimed at comparing the environmental impacts only of the design stage of the two bumpers manufactured within the SNVI.
The second part is dedicated to the study of the dust resulting from the manufacture of a bumper and this for the sake of confirming the results of the first part. Indeed, the results obtained after the processing of the inventory data with the SimaPro 7.1 software, led us to realize a battery of analysis namely: a chemical composition, a particle size and a DRX of the dust of the polyester workshop. Such a modification includes the use of a new contact molding process and the consumption of new materials. The new and existing component has been benchmarked by performing a LCA from the design stage and using the SimaPro software, to check if the new component offers a lower environmental load. So this study will answer the following question: this change of materials and process will have; in the future, a positive environmental and economic impact or perhaps there will be a shift of pollution and new environmental impacts.
2 Materials and methods
2.1 Life cycle assessment
In the Hitchhikers guide to LCA, Baumann and Tillman write that “in an LCA study, the whole industrial system involved in the production, use and waste management of a product or service is described”, International Organization for Standardization 2006. The first step of an LCA study is the goal and scope definition, in which the purpose of the study and the modeling aspects are described. This is followed by the life cycle inventory analysis, in which the inputs (resources used) and outputs (emissions) of the included processes are identified. These inputs and outputs are then classified and characterized in order to calculate the life cycle environmental impact of the product or service. Finally, the results are interpreted (Vanalle et al., 2011).
The gate-to-gate LCA study was conducted according to the ISO standard (ISO, 2006). Life Cycle Impact Assessment (LCIA) and LCA were performed using SimaPro 7.1 (Netherlands). This software contains US and European databases on a wide variety of materials (Tan and Khoo, 2005).
The methodology selected to conduct LCIA was Ecoindicator 99 (Goedkoop and Spriensma, 2000).
2.2 Aims of the study
The aim of this study is to establish a robust data set to assess the main potential environmental impacts of the two bumpers studied. The main goals of this study were:
1) To compare the environmental impacts of two bumpers.
2) To put at the disposal of an Algerian industry an ecodesign method that will permit it to integrate the ecological dimension up-stream of manufacturing processes and thus helping it in its choices and decisions.
3) To allow the company SNVI to make specific comparisons and confirm its choice of materials in relation to the studied products.
4) To release the possibilities for environmental improvements of the product, this can touch several weak points of the product and especially can relate to all the range of the products manufactured within the company (all metal furniture).
The bumper is a component of the body of a vehicle used to cushion front and rear impacts. It can be attached to the body or be integrated (Prabhakaran et al., 2012). The bumpers produced by SNVI, are intended to take place on small trucks type K66. The first, named for the study “steel bumper”, consists of a steel body (60%), two metal end pieces and undergoes a surface treatment and paint at the end. Its competitor, named polyester bumper, consists of a resin (40%), fiberglass, and chemical additives. The bumper produced by SNVI has been made of steel for the K66 truck for more than 50 years, and the second is a polyester prototype manufactured in the polyester workshop of the same company. The validity limits of this study are related to the assumptions established jointly with the company SNVI.
Knowing that, there is no pre-LCA study in Algeria concerning the automobile industry. In addition, the software SimaPro is software produced in Europe, some data concerning Algeria are not in the database.
2.3 The functional unit and the studied products
The functional unit is the reference unit in life cycle analysis. It makes it possible to compare two scenarios, the compared elements having to respond to the same function for the same duration.
In our case, the selected functional unit is a 30-year bumper installed on the truck K66. This duration is a so-called average duration, since the bumper can hardly go up to 50 years of life, but it depends on what climatic conditions it was subjected to.
The two compared bumpers use two different manufacturing technologies, but fulfill the same function:
The steel bumper consists of a steel body and two other elements. Its lifespan is estimated at 30 years.
The “prototype” polyester bumper consists of a fiberglass and epoxy resin structure. Its life is estimated at 15 years. It is therefore necessary to use two to fulfill the desired lifetime in the functional unit, i.e. thirty years.
2.4 System boundaries
The boundaries of the studied systems: Systems corresponding to the reference scenarios.
The “ACV Gate to Gate” approach was used, since it involves comparing two products that make the same service and designed at the same company; but these later are composed of different matters and with two different processes. So the life cycle will concern the production stage of the two bumpers (Fig. 1 and Fig. 2).
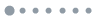
Figure 1.Fig. 1
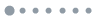
Figure 2.Fig. 2
2.5 The excluded stages of the life cycle
According to the ISO 14040 standard, it is possible, clearly explained, to exclude certain steps or operations of the studied systems, in order to avoid any misplacement in details that are not significant in terms of impact on the environment (International Organization for Standardization, 2006). The component “fitting bracket”, representing only 1.37%, will not be taken into account. It was noted that, the same thing for certain chemical additives for surface treatment for the steel bumper and certain other products for the polyester bumper since they are not found on the software database. The safety data sheets were consulted for the needs of the study.
2.6 Waste and by-products
To become a waste or a co-product:
If the data are available, they are taken into account.
Otherwise, the end of life of the product is not taken into account.
The main steps described in the different subsystems of the study do not involve any co-products. Co-products for metal scrap are recovered by (SNVI), and reused for small parts (such as hardware) or sold to other private companies for regeneration. In addition, the amount of metal waste (falls) is negligible.
On the other hand, the waste resulting from the surface treatment and the paint remain untreated and stored at the level of the company while waiting to be evacuated. For the polyester workshop, there are two types of waste; dust from the cutting of the fiberglass and finishing stations. For cutting stations; these dusts are collected manually. For finishing workstations; the latter are equipped with suction devices; and so the dust is collected in silos.
The company does not have a waste management plan, so it was impossible for us to have representative data about the reality on site.
2.7 Life Cycle Inventory Analysis (LCIA)
The life cycle of the automotive component involves several important processes and a relevant number of interested parties (i.e. raw materials manufacturers, sub-components manufacturers, component manufacturer, transportation
companies, recyclers). The quantity of data is therefore very high. To have access to the necessary data set, information from project partners (the component manufacturer, for instance), literature and specialized databases are used according to tables (Table 1, Table 2 and Table 3).
2.8 Flow and environmental impacts studied
Life cycle impact assessment method: The SimaPro 7.1 software uses different impact calculation methods allowing us to translate the information obtained in the life cycle inventory into environmental impacts, including: CML, Eco- indicator, and Impacts 2002. For the purposes of the study, the Eco-indicator 99 calculation method was chosen because it offers a choice of indicators relevant to the prob lematic posed by the bumpers. Eco-indicator method is widely applied in many LCA studies (Yusoff and Hansen, 2007; Huntzinger and Eatmon, 2009; Liu et al., 2010; Song et al., 2013). Eleven impact categories are taken into account in Eco-indicator 99 method, including carcinogens, respiratory organics, respiratory inorganic, climate change, radiation, ozone layer, ecotoxicity, acidification/ eutrophic ation, land use, minerals, and fossil fuels.

Table 1.
Steel bumper component
Table 1.
Steel bumper component
Part number | Subset | Nature of sheet | Metal weight (kg) | Process | Operation range |
---|
668085 (A) | - | TC | 14.10 | 55190 8 kW 6 bar | Cut flan, punch, smash, Notching, controlfold one edge R = B, fold R = 15, control | 55820 2 ch 6 bar | 55170 11 kW 6 bar | 56170, 56540, 56540 | 668086 (B) 668087 (C) | - | XES | 0.866 | 55120, 56180, 56180 | Cut blank, Cut out blank, Coining, Controlled | 668088 (D) | 668089 (D′) | XES | 0.866 | 55120, 55820, 56180, 56180, 56540 | Cut blank, Punch, Notch (4 angles), Fold, Control, Bend ends, Control | 663302 (D″) | XES | 0.192 | 55190, 55820, 56180 | Cut blank, Punch, Fold 2 edges, Control |
|

Table 2.
Products used for surface treatments and painting (steel bumper)
Table 2.
Products used for surface treatments and painting (steel bumper)
Products | Major chemical constituents | Quantity |
---|
Systoclean 2118/504 (dégraissage) | Sodium hydroxide NaOH (C>10 %) | 45 g | Addistrip 2252 (décappage) | Hydrochloric acid HCL (C>25 %) | 0.5 L | Neutrax n°1 | Sodium nitrate NaNO3 (C>20 %) | 20 g | Systophose 4605 | Phosphoric acid (C>25 %) | 0.020 L | Rinspas 19 | Hydrofluozirconic acid and acid Fluozirconic | 0.002 L | Water | H2O | 60 L |
|

Table 3.
Materials used for the polyester bumper
Table 3.
Materials used for the polyester bumper
Products | Major chemical constituents | Quantity |
---|
Fiberglass layer | Fiberglass | 1200 g m-2 | Resin | Polyester | 2800 g | BUTANOX M-50 | Methyl Ethyl Ketone Peroxide PMC | 56 g | Oc6 | Cobalt octoate | 56 g | Gel coat | Paint resin | 448 g | Acetone | Diluent | Small quantity | Wax | Release fat | 20 g |
|
3 Results and discussion
3.1 Exploitation of results and interpretation
Unless otherwise stated, all the numerical results and the following graphs relate to the chosen functional unit. This part allows us to directly visualize, thanks to the graphs and trees, the weak and strong points of the studied bumpers.
3.2 Tree of both steel and polyester bumpers by SimaPro
Figure 3 and Figure 4, represent respectively the tree of the manufacturing process of steel bumper and that of polyester, each box (in blue or gray) represents a process (used material, manufacturing processes, etc.) and the arrows represent the links between processes. Thermometers (or histograms) in red indicate the contribution of each process, which allows us to distinguish between important and less important processes.
All products in this tree are not visible.
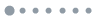
Figure 3.Fig. 3
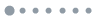
Figure 4.Fig. 4
3.3 Impacts from the manufacture of the steel and polyester bumper by Eco-indicator 99
According the SimaPro software, the inventory analysis results are obtained in the tables form then they are represented in histogram form which are given in Fig. 5.
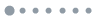
Figure 5.Fig. 5
Figure 5 shows the contribution of different subsystems to different impact categories. The main environmental impacts related to the manufacture of the steel bumper are as follows (using the eco-indicator 99 method, Fig. 5a):
Carcinogenic substances (local or regional effect), mainly generated by steel sheet (more than 75%) and paint.
Organic substances (local or regional effect), mainly generated by metal sheet and the use of electricity.
Inorganic substances (local or regional effect), mainly generated by steel bumper sheet.
Climate change (global effect), mainly generated by steel sheet (more than 75%) and painting.
Radiation, mainly generated by the use of paint.
Destruction of ozone (overall effect), mainly generated by steel sheet and paint.
Ecotoxicity (local or regional effect), mainly generated by steel sheet and paint.
Acidification (local or regional effect), mainly generated by steel sheet and electricity.
Land use (local or regional effect), mainly generated by steel sheet.
Mineral substances, mainly generated by steel sheet.
Most of the related impacts to the manufacture of the steel bumper are attributable to steel sheet is the main metal frame of the studied product, this is explained by the importance of its mass and especially by the amount of data inventoried and used to model the life cycle of the framework.
The main environmental impacts related to the manufacture of the polyester bumper are as follows (using the Eco indicator 99 methods, Fig. 5b):
Carcinogenic substances (local or regional effect), mainly generated by fiberglass (30%) and electricity (55%).
Organic substances (local or regional effect), mainly generated by the use of electricity and the use of styrene.
Inorganic substances (local or regional effect), mainly generated by fiberglass with 40%; and styrene (30%).
Climate change (global effect), mainly generated by the use of electricity.
Radiation, mainly generated by the use of electricity.
Destruction of ozone (global effect), mainly generated by the use of electricity.
Ecotoxicity (local or regional effect), mainly generated by fiberglass.
Acidification (local or regional effect), mainly generated by electricity.
Land use (local or regional effect), mainly generated by fiberglass.
Mineral substances, the use of electricity.
For our study we will try to compare for the two products only three environmental impacts that are:
Carcinogenic substances (local or regional effect).
Inorganic substances (local or regional effect).
Climate change (global effect).
These indicators were chosen in collaboration with the HSE team of the company and the head of occupational medicine in the industrial zone. Why this choice? The site visits allowed us to notice that for the polyester workshop, the company went from the manufacture of small parts to large parts such as hoods and bumpers, unfortunately the workshop was not prepared for this change, so we end up with more raw materials to process and more waste to evacuate. In addition, several research projects were carried out for this workshop, but they dealt with the risks related to chemicals used, in particular resin and additives.
For the first impact, carcinogenic substances, we notice that it is attributable to the metal sheet given its weight and inventories data for the steel bumper and carcinogens are mainly due to fiberglass and electricity for the polyester bumper.
The second impact, inorganic substances (local or regional effect), mainly generated by the metal sheet (80%) for the steel bumper and they are due to fiberglass for the bumper polyester (40%).
The third impact, climate change (global effect), mainly generated by metal sheet for the steel bumper (83%) and for the polyester bumper, it is due to the use of electricity (90%).
We can conclude for this first part, that indeed the change of materials and processes, has led to environmental benefits including the global impact “climate change”, effectively the substitution of steel with polyester allowed a decrease in weight of the bumper of 10 kg, which means a reduction of at least 1 gr of CO2 km-1 for a bumper. In addition to lightening the weight of vehicles resulting in fuel economy (rejected CO2 reduction), polyester offers other advantages: Greater freedom of design, lower costs, increased safety in case of shocks, and better comfort for users. Unfortunately, this change can have a negative impact on the health of workers, since it is noted that the risk of cancer and inorganic products are mainly due to fiberglass and styrene.
The exploitation of the results of studies carried out by the occupational medicine within the SNVI allowed us to note that there were a good number of cases among the workers of the polyester workshop who suffered from dermatosis and various irritations. At this stage of the study, we have asked the following question: polyester as a substitute material and contact molding as a manufacturing process is it the best solution to address the environmental problematic, despite the fact that the company owns a polyester workshop and measures the manufacturing process.
The results led us to make a dust analysis battery of the polyester workshop in order to confirm the results of the LCA study.

Table 4.
Chemical composition in cutting and preparation of fiberglass
Table 4.
Chemical composition in cutting and preparation of fiberglass
Chemical composition | Concentration (%) |
---|
MgO | 1.141 | Al2O3 | 10.298 | SiO2 | 44.161 | SO3 | 0.764 | K2O | 0.476 | CaO | 35.048 | Fe2O3 | 1.872 |
|
3.4 Dust analysis
a) Dust sampling protocol
In order to analyze the dust for the three workplace, we collected the amount of dust required in resealable bags after a determined period of work and this was followed by the recommendations of the body (laboratory) which carried out the analyzes (Chemical composition, particle size and X-Ray Diffraction). For this study, three positions were chosen:
- Workstation 1: cutting and preparation of fiberglass;
- Workstation 2: deburring the finished part;
- Workstation 3: finishing.
b) Chemical composition
Table 4 shows the chemical composition in cutting and preparation of fiberglass, Table 5 shows the Chemical composition in deburring the finished part, and Table 6 shows the Chemical composition in finishing part.

Table 5.
Chemical composition in deburring finished part
Table 5.
Chemical composition in deburring finished part
Chemical composition | Concentration (%) |
---|
MgO | 0.230 | Al2O3 | 1.775 | SiO2 | 7.314 | P2O5 | 0.910 | SO3 | 0.118 | K2O | 0.118 | CaO | 7.488 | TiO2 | 0.630 | Fe2O3 | 0.448 | Cl | 13.770 |
|
c) Particle sizes of studied dusts
The Fig. 6 shows the particle size distribution of the dust for each workstation (P1, P2 and P3) in the polyester workshop obtained by Laser granulometer. It is remarkable that the dust of station 3 contains more fine than that of the other stations. Indeed, the particles having a diameter <10 μm represent more than 30% in the dust of the post and those of the other stations represent only 5% (see Fig. 6).

Table 6.
Chemical composition in finishing part
Table 6.
Chemical composition in finishing part
Chemical composition | Concentration (%) |
---|
Cr2O3 | 0.010 | MgO | 0.087 | Al2O3 | 0.598 | SiO2 | 2.656 | P2O5 | 0.460 | SO3 | 0.088 | CaO | 4.498 | TiO2 | 0.371 | Fe2O3 | 0.698 | PbO | 3.673 | Cl | 8.981 |
|
We note that the dust from the P3 workstation is loaded with silica contained in the fiberglass (see Fig. 6). Indeed, the presence of silica in the dust of station P3 is due to the completion of the part during the manufacture of bumpers of the vehicle.
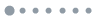
Figure 6.Fig. 6
d) XRD analysis of studied Dusts
From each workstation, studied dusts were analyzed by XRD (X-Ray Diffraction) to identify presence of the chemical element content in particular the silica (Fig. 7). The obtained results are given in Fig. 7. According to results, it is clearly that presence of silica was identified and observed in P3 workstation compared to other workstations. Also, it is noted that peak of Chrome oxide was observed in P3 workstation.
The route of entry of crystalline silica into the body is the respiratory tract. Dangerous dust is the one with the smallest dimensions, which can reach and settle in the lungs.
Crystalline silica dust can induce eye and respiratory tract irritation, chronic bronchitis, and irreversible pulmonary fibrosis called silicosis. This serious and debilitating pulmonary involvement generally appears only after several years of exposure and its evolution continues even after cessation of exposure.
It can also be noted, given the chemical composition and the XRD, the presence of certain other toxic elements, with important percentages such as:
- The content of CaO is 35% in P1, 7% in P2 and 5% in P3, knowing that this substance is classified as irritating to the skin and respiratory tract, and carries a risk of serious eye damage,
- The content of PbO is almost 4% in P3, knowing that it presents a risk during pregnancy, possible risk of impaired fertility. It is harmful by inhalation and ingestion with the danger of cumulative effects.
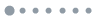
Figure 7.Fig. 7
4 Conclusions
The study aims to compare the environmental impacts of two bumpers manufactured with two different materials (steel and polyester) and two different processes (mechanical and contact molding) within the same company. The latter, decided to introduce more plastic material into its products to reduce the weight of its last and thereby reduce some environmental impacts including greenhouse gases that in order to meet a national and international regulation more and more demanding. Unfortunately, the choice of polyester as substitute materials has not been studied; the company already had a polyester workshop without asking the question about the possibility of creating new impacts. That’s why we use the “door-to-door” approach to life cycle analysis to compare just the manufacturing stage and help the company in its choice of materials.
The second part of the study, dust analysis, was carried out in order to detail the two impacts of polyester shock, namely the carcinogenic impact and the breathing impact of inorganic (mineral) products, which directly affects the health of workers.
In view of the results of the life cycle analysis of the two by shock, it may be noted that the choice of the “polyester” material could be at the origin of a pollution transfer; effectively, the use of polyester will reduce the weight of the truck but unfortunately it will increase the probability of exposure of workers to harmful dust.