I. INTRODUCTION
Large-volume presses (LVPs) are widely used to investigate the effects of pressure on the structure and properties of materials.1 With LVPs, it is possible to synthesize and examine relatively large samples (millimeter size) at pressures of several GPa to over 30 GPa and at simultaneous high temperatures exceeding 2300 °C. Since the 1958 publication by Tracy Hall describing a multi-anvil high-pressure apparatus,2 there has been steady progress in the development of multi-anvil presses. With the development of high-pressure technology, various types of LVPs have been designed and constructed around the world, playing an essential role in a variety of fields. For example, the focus of LVPs with solid pressure-transmitting media is on material synthesis and planetary science research (especially in Earth sciences). Various types of apparatus for generating high pressures and high temperatures with liquid pressure-transmitting media have contributed, for example, to the synthesis of nanomaterials and gaseous materials and to investigations of hydration energy, the structure of liquid planets, and the origin of life. Nonequilibrium LVPs with rapid compression bridge the gap between static high pressure and dynamic high pressure in terms of time resolution and are therefore useful for the study of loading rate effects on properties and structure. In terms of spatial nonequilibrium, LVPs with the capability of deformation can simulate the stress environment in the deep Earth, as well as enabling the preparation of new materials under much lower pressures than would otherwise be needed. At present, to meet the increasing research demand for extreme conditions, many new types of large-volume press are at the design or construction stages.
Currently available LVPs with solid pressure-transmitting media can generally be divided into two types, depending on the shape of the chamber formed by the anvils, namely, cubic or octahedral. Cubic multi-anvil presses (6/6–6 mode) have enabled industrial production of superhard materials because of their low cost and high work efficiency. LVPs with octahedral pressure-transmitting medium (6–8 mode) usually achieve ultrahigh pressures through double-stage pressurization.3–6 By varying the truncation lengths of tungsten carbide anvils, various sample sizes and pressure ranges can be obtained. With higher pressure, the volume of the high-pressure chamber decreases. This places a severe constraint on size of bulk samples. Motivated by the desire to realize larger high-pressure chambers and thus samples, many LVPs with high loading forces of 60 MN (6000 t) or 50 MN (5000 t) have been constructed, such as those at Ehime University in Japan and the University of Bayreuth in Germany.7,8 However, the scope to increase the size of the high-pressure chambers is limited and is not such as to allow the synthesis of large samples.
In addition to LVPs providing hydrostatic pressure, LVPs for nonequilibrium environments are also under development. For example, a pressure jump from ambient pressure to 0.1 GPa was achieved within 100 ms by Barton and Stacey9 and a jump to 0.7 GPa was achieved in 5 ms by Woenckhaus et al.10 Rapid compression (5.2 GPa in 20 ms) was achieved in an LVP with piston–cylinder and Bridgman-type anvils by using a large-volume bladder-type power accumulator at Southwest Jiaotong University, China.11 However, the pressure limit and the pressure increase rate cannot bridge the gap between dynamic shock compression and static compression. Generally, a shear environment is achieved through a pressure-generating apparatus such as a D-DIA type press (SSRF, APS),12 a six ram press (DESY, BGI, ChiPs),13–15 a T-cup-type press (APS),16 or a rotating Paris–Edinburgh (PE) press, or through assembling parts with a 45° inclination.17,18 Despite their advantages, such presses typically produce relatively low loading forces, which are insufficient to accommodate larger samples.
Besides presses with solid pressure-transmitting media, a variety of LVPs with liquid pressure-transmitting media have been developed over the years because of their great scientific and industrial importance. Liquid high-pressure equipment was first developed for the synthesis of ammonia in the early nineteenth century. Currently, the pressures that can be generated are still of the order of 10 MPa, which is far below the requirements of scientific research. Achieving higher pressures and temperatures in a liquid environment can expand the scope of research into novel material, the structure of liquid planets, and the origin of life.
Although the past century has witnessed great developments both of LVPs and of the associated instrumentation and in situ measurement techniques, there are many problems remain to be solved, as mentioned above. In addition, owing to the distributions of LVPs at different research institutions, it is a challenge to achieve collaborative development of technologies and conduct interdisciplinary research. The aim of the Synergetic Extreme Condition User Facility (SECUF) at Jilin University, China is to accommodate the increasing demand for different types of LVPs with different capabilities.
In this paper, we describe the design and construction of three LVP subsystems at SECUF (Fig. 1): the Solid Environment High-Pressure and High-Temperature (SEHPHT) station, the Liquid Environment High-Pressure and High-Temperature (LEHPHT) station, and the Nonequilibrium High-Pressure (NHP) station. Their characteristics and capabilities are summarized in Table I. The advantages, design objectives, and research focuses are detailed in the following text. A number of reported results are also presented to illustrate the performance of the different LVP subsystems at SECUF in various areas of research. Users can choose the devices best suited for their experimental purposes, and the respective managers of the subsystems will help to train users and conduct experiments if required. This platform offers a series of dedicated sample machining, characterization, and data analysis laboratories with all the required infrastructure to ensure the progress of high-pressure and high-temperature (HPHT) experiments. Thus, SECUF’s HPHT platform is expected to be a powerful force for the development of high-pressure techniques in scientific research.
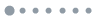
Figure 1.Experimental research hall of the synergetic extreme condition user facility (SECUF) at Changchun.

Table 1. Comparison of the subsystems and multi-anvil presses installed at SECUF.
Table 1. Comparison of the subsystems and multi-anvil presses installed at SECUF.
Subsystem | Capabilities and characteristics |
---|
SEHPHT | 20 000 t belt-type apparatus | P ≥ 20 GPa, V ≥ 1000 mm3, T ≥ 2500 K, | Solid condition | | cylindrical chamber | | 3000 t Kawai press | P ≥ 28 GPa, V ≥ 10 mm3, T ≥ 2500 K, | Solid condition | | octahedral chamber | 1000 t DIA press | P ≥ 23 GPa, V ≥ 10 mm3, T ≥ 2500 K, | | octahedral chamber | 1000 t Kawai press | P ≥ 28 GPa, V ≥ 10 mm3, T ≥ 2500 K, | | octahedral chamber | LEHPHT | Hundred milliliter volume press | P ≥ 0.5 GPa, V ≥ 100 ml, T ≥ 800 K, | Liquid condition | | cylindrical chamber | | Microliter volume press | P ≥ 1.8 GPa, V ≥ 10 µl, T ≥ 1000 K, | Liquid condition | | cylindrical chamber | | NHP | Rapid compression press | 10.2 GPa in 20 ms, V ≥ 10 mm3, T ≥ 1600 K, | Temporal nonequilibrium | | octahedral chamber | | D-DIA press | 8 GPa with shear deformation, V ≥ 10 mm3, | Spatial nonequilibrium | | T ≥ 1600 K, cubic chamber | |
|
II. SEHPHT STATION
SEHPHT is a system for large-volume HPHT experiments with a solid pressure-transmitting medium. The high pressures and temperatures are generated by a self-designed large-scale ultrahigh-pressure-generation apparatus with a cylindrical high-pressure chamber and a 2–6–8 configuration of high-pressure devices based on a piston–cylinder frame with octahedral high-pressure transmitting medium. A high-synchronicity Kawai and a DIA module are also installed to produce ultrahigh pressures and temperatures for three LVPs.
A. Belt-type high-pressure and high-temperature apparatus
Increasing the sample size has always been the goal of ultrahigh-pressure LVPs, since the large samples facilitate subsequent characterization through techniques such as nuclear magnetic resonance (NMR), neutron diffraction, and calorimetry. Therefore, achieving a larger sample volume under ultrahigh pressure is desirable but challenging for solid-state LVPs. Although many multi-anvil presses using the 6–8 mode have been developed, the chamber capacity is still not as large as that of a belt-type apparatus. Belt-type LVPs can provide larger sample volumes, but their pressures are limited to around 10 GPa. Smaller anvil truncations in an LVP can give higher pressures, but the size of the high-pressure cell decreases with increasing pressure. Increasing the maximum loading force is a prerequisite for generating ultrahigh pressures while maintaining a large chamber capacity. Higher pressure with larger sample volumes can be achieved by using larger hydraulic rams to generate a higher loading force.
Therefore, a new-generation 20 000 t (200 MN) large-scale belt-type apparatus was designed and constructed with the aim of providing a significantly large chamber volume (1000 mm3) while still operating above 20 GPa and 2500 K. Figure 2 shows its components, cell assembly, and structural parameters. With its large cylinder diameter of 2061 mm, the maximum oil pressure of 60 MPa corresponds to a loading force of 200 MN. The main obstacle faced in the construction of this press was the need for a particularly strong framework, owing to the fact that the stress in the high-pressure module exceeds the limit of traditional metal materials. In addition, although this unprecedentedly large press provides a high loading force, this leads to difficulty in aligning the hydraulic rams and anvils. These problems are solved in three innovative ways. First, the parallelism between the anvil blocks is ensured by aligning them through a special hydraulic system. Second, the strength of the high-pressure mold is greatly enhanced by splitting the mold and wrapping it with a steel strip. Third, the shear stress in the high-pressure cell assembly is reduced through the use of special pressure-gradient materials and sealing materials.
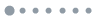
Figure 2.(a) Schematic of 20 000 t ultrahigh-pressure belt-type apparatus. (b) Main structural diagrams of this apparatus with dimensions (mm) from different aspects.
Despite its extremely large size, this press is highly automated. The main console is equipped with a programmable logic controller (PLC), which can perform all operations automatically and remotely. A hydraulic pumping system boosts the system oil pressure in the high-pressure oil vessel and pushes the hydraulic rams, which provide a high loading force of up to 200 MN. The oil pressure can be controlled to an accuracy of within 0.01 MPa. The sample chamber can be heated by a DC power supply. The temperature can reach 2500 K, with a pressure of 20 GPa in the extruded cylindrical chamber of 1000 mm3. This apparatus establishes a new model for LVPs with larger sample capacity, which will of benefit for HPHT research areas that demand larger samples.
B. Kawai and DIA-type high-pressure and high-temperature apparatus
Kawai-type or DIA-type multi-anvil presses are the most widely used type of laboratory apparatus for generating ultrahigh pressures and high temperatures with large sample volumes. They have sophisticated compression systems using double-staged multi-anvils in the 6–8 mode to produce quasi-hydrostatic pressure. However, the pressures available in the 6–8 mode have long been kept below 30 GPa owing to the deformability of the first-stage anvil and the hardness of the second-stage tungsten carbide anvils and to problems with synchronization and the stability of the pressure pumping system. Although reducing the truncation lengths of the anvils, and the use of third-stage anvils, harder sintered diamond anvils, or tapering anvils can effectively expand the pressure range available, improvements in stability and synchronization are essential to ensure the success of ultrahigh-pressure experiments. Presses using the 6–8 mode are now being widely used in many areas of research, with ultrahigh pressures (≥50 GPa) being realized.
This system at SECUF includes three HPHT presses: 3000 t Kawai, 1000 t Kawai, and 1000 t DIA-type presses, all from the C&T Factory, Japan, which are able to achieve high stability and synchronization. Figures 3(a) and 3(b) show the 3000 t Kawai-type LVP and the precise Kawai-type alignment module that enable it to generate ultrahigh pressures. The uniaxial loading force (limit of 30 MN) is loaded through a controllable oil pressure system. The oil pressure can be loaded up to a maximum value of 200 MPa through a visualization pressure control system. The improved control software can display the variation of oil pressure with time and the heating power as a function of temperature. The actual pressure is adjusted by a servo motor to reach the target pressure with an accuracy of ∼0.01 MPa. The oil pumping system is controlled using 13 segmented programs that provide real-time pressure and time parameters.
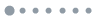
Figure 3.(a) 3000 t Kawai-type high-pressure apparatus (Kawai-type LVP). (b) Kawai-type module. (c) MgSiO3–Al2O3 mineral system phase relation at different pressures and 2000 K in a previous study.19 The red circular symbol corresponds to the solubility of Al2O3 in bridgmanite in the present study, which is calibrated at 29 GPa in the phase relationship represented by the blue curve with dot symbols. Brg, bridgmanite; Cor, corundum; Gar, garnet. (d) Pressure in the chamber vs oil pressure. The curve is constructed from several sets of conventional resistance pressure calibrations and a mineral pressure calibration. En50Cor50 (En = MgSiO3, Cor = Al2O3) is the starting material for the mineral pressure calibration. The sample was obtained at a set load and a temperature of 2000 K. The solubility of Al2O3 in bridgmanite was then determined to confirm the chamber pressure using the phase relationship shown in (c). Reprinted with permission from Ge et al., Chin. J. High Pressure Phys. 38, 030201 (2024). Copyright 2024 Chinese Journal of High Pressure Physics Editorial Office.20 (e) Temperature in the high-pressure assembly vs heating power curve in an HPHT experiment at 29 GPa.
There are six hard steel first-stage anvils on a guide block with a truncation length of 100 mm. 100 and 60 mm adapter pads can be used to match different sizes of second-stage WC anvils. The 60 mm adaptor is for WC anvils with a cube size of 32 mm and the 100 mm adaptor for a cube size of 52 mm. An AC heating system is available with 5 and 40 V options, which is adaptable to different heating materials (graphite, high-melting-point metals, lanthanum chromate, and boron-doped diamond). Generally, the low voltage is selected for metal heaters with low resistance, while the high voltage is used for lanthanum chromate heaters with high resistance. The heating power is set with automatic control software (maximum power 2000 W and control precision ∼0.1 W). The 1000 t Kawai and 1000 t DIA-type LVPs use the same pressure control module and heating system, except that they have a maximum oil pressure of 70 MPa for a loading force of 1000 t. These three devices can easily reach 28 GPa and 2600 K with a diameter range from 1 to 2 mm, depending on the loading force of the apparatus.
As shown in Fig. 3(d), the calibration of the system oil pressure vs chamber pressure for the 8/3 assembly is performed at room temperature with the phase transition method. It is then verified by a mineral synthesis experiment [Fig. 3(c)]. Normally, this system can reach 29 GPa with a TF05 tungsten carbide anvil with a truncation length of 3 mm. Higher pressures can be achieved with harder tungsten carbide or smaller truncation length anvils. The highest chamber temperature of 2500 K has been achieved at 29 GP [Fig. 3(e)] with chamber volume greater than 10 mm3. Benefitting from their precise guiding blocks, these LVPs have high stability and synchronization, which is conducive to the generation of ultrahigh pressures. In the near future, it should be possible to reach 60–80 GPa or even 100 GPa with the use of smaller truncation edge length (TEL) and harder polycrystalline diamond (PCD) anvils.5,6,21 Similarly, ultrahigh temperatures of 3000–4000 K could be reached with boron-doped diamond (BDD) heaters.22
C. Synthetic materials and in situ measurement at SEHPHT station
Experimental research on high-pressure synthesis provides a basis for the performance optimization and applications of bulk materials. The development of larger high-pressure equipment facilitates such synthesis experiments, in which larger samples are highly desirable both for subsequent characterization and for industrial application. Single-crystal diamond and nanopolycrystalline diamond are of great importance for industrial applications and have received widespread attention from physicists and materials scientists. At present, diamond with a hardness far exceeding that of a single crystal can be prepared from onion carbon nanoparticles,23 and the toughness of the sample can be greatly improved by adjusting transgranular fracture and intergranular fracture [Fig. 4(a)].24 Amorphous diamond with excellent properties can be prepared from C60 [Fig. 4(b)],25 and the transformation path of carbon can be controlled under high pressure to obtain diamond derivatives with electrical conductivity. These results are realizable on the SEHPHT station. Nanodiamond particles with nitrogen vacancy centers can be obtained by transformation of organic matter under high pressure. The size of nanopolycrystalline diamonds is constrained by the volume of the high-pressure chamber. The possibility that metal hydrides exhibit near-room-temperature superconductivity has attracted intensive attention recently, but the associated experimental investigations require pressures of at least 50–100 GPa, which are far beyond those achievable with traditional laboratory presses. The preparation of new materials under high pressure necessitates a reduction in chamber size owing to the pressure increase, and this limits the potential applications of such materials. With the completion of the SEHPHT, ultrahigh pressures can be reached in a large chamber, which should enable the synthesis of bulk specimens with superior properties, thereby helping to promote the application of novel materials.
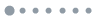
Figure 4.(a) Relation of Vickers hardness/toughness to grain size of PCD-1 to PCD-6. Reprinted with permission from Lian et al., Int. J. Refract. Met. Hard Mater. 118, 106490 (2024). Copyright 2023 Elsevier Ltd. (b) Pair distribution function g(r) of bulk amorphous carbon samples AC-1 (synthesized at 20 GPa and 1000 °C) and AC-3 (synthesized at 27 GPa and 1000 °C). Gra, graphite; Dia, diamond. Reprinted with permission from Shang et al., Nature 599(7886), 599–604 (2021). Copyright 2024 Springer Nature Limited. (c) Estimated ZT values of β-Ag2S as functions of temperature at different pressures. Reprinted with permission from Zhao et al., Appl. Phys. Lett. 123, 062202 (2023). Copyright 2023 AIP Publishing LLC.26 (d) Logarithm of acoustic emission hit rates, oil pressure, and displacement as a function of time during a typical acoustic emission experiment with boron–epoxy and pyrophyllite as pressure-transmitting medium. Reprinted with permission from Ma et al., Rev. Sci. Instrum. 94, 023901 (2023). Copyright 2023 Authors, licensed under a Creative Commons Attribution (CC BY) license.
Multi-anvil presses are essential tools for the Earth science community, owing to the need to replicate the HPHT conditions in the Earth’s interior in the laboratory. LVPs provide a window into the physical and chemical properties of planetary interiors, as a complement to seismology. Owing to previous limitations of LVP technology, geophysical research has usually been limited to the crust, the upper mantle, and the vicinity of the transition zone. It is difficult to conduct studies of the Earth’s deeper interior. However, thanks to the high stability and high synchronization of LVPs with tapered tungsten carbide anvils, sintered diamond anvils, and boron-doped diamond heaters, high pressures of 60–80 GPa and a high temperature about 4000 K can be reached, similar to the conditions of the Earth’s lower mantle. It is possible to study the circulation mechanisms of water, carbon, and other materials in the Earth’s interior, the maximum circulation depth, heat exchange and heat convection at the core–mantle boundary, the composition of materials in the Earth’s interior, the viscosity of molten minerals in the lower mantle, and other geophysical problems. At the same time, the larger chamber volume of an LVP can accommodate a greater number of grains. This enables a better understanding of grain-related problems in the Earth’s interior, and compensates for the small chambers of diamond anvil cells (DACs), which cannot satisfactorily simulate the effects caused by polycrystals and grains.
Large sample volume is also critical for various in situ measurements of physical properties under HPHT, such as thermal diffusivity, electrical conductivity, elastic modulus, and viscosity. The feasibility and experimental accuracy of many in situ measurements depend greatly on the chamber size of an LVP. For example, measurements of the viscosity coefficient of melted minerals under HPHT27 may be affected by a small chamber size, which leads to errors in the timing of the falling ball in the capture process. Small chamber size also causes difficulties for in situ electrical measurements, owing to the ease with which multi-measurement wire arrangements can be broken. Similarly, measurements of the electrical conductivity and thermoelectric coefficient of functional materials require a certain temperature gradient, which is difficult to control in a small chamber. In situ thermoelectric measurements [Fig. 4(c)] can be easily realized with the SEHPHT station because of its large chamber. For HPHT in situ measurements of thermal diffusivity, ultrasound transmission, and acoustic emission, a large sample size is necessary to avoid errors in the obtained thermal conductivity coefficient, elastic modulus, and location of acoustic emission. The SEHPHT station will enable such investigations to be performed successfully [Fig. 4(d)]. Larger sample volumes also benefit chemical diffusion experiments, especially for rapid diffusion processes, which cannot be effectively investigated when the sample size is too small. Thanks to the large volume and stable operation of the LVP at the SEHPHT station, the above in situ measurement problems can all be solved.8
In summary, the implementation of solid-state systems for the synthesis of bulk materials and for innovative in situ measurement techniques will benefit a variety of research areas, accelerate the industrial production of new materials, and solve long-standing questions in Earth sciences.
III. LEHPHT STATION
The LEHPHT station comprises an ultrahigh-temperature and static high-pressure apparatus (100 ml volume at 0.5 GPa) and a piston–cylinder liquid high-pressure apparatus (microliter volume at 1.8 GPa). These are designed and installed to meet the needs of higher pressure and a larger chamber under liquid conditions. They provide a liquid chamber and temperature and pressure monitoring based on in situ spectroscopic measurements. The fundamental obstacle to studies of the structures and chemical reactions of the samples at high pressure and temperature is the inability to perform direct in situ spectral measurements of materials in liquid high-pressure devices. To solve this problem, this station is equipped with an in situ spectroscopic measurement system for use under HPHT conditions, including a fluorescence microscope and a Raman spectrometer. This station serves for studies of synthetic materials, property regulation, and high-pressure liquid aspects of research into planetary science and life under extreme conditions. It represents a class of experimental apparatus intermediate between high-pressure reactors and DACs, being able to achieve a higher pressure than a high-pressure reactor and with a chamber capacity 1000 times larger than that of a DAC.
A. Hundred milliliter ultrahigh-temperature and static high-pressure apparatus
This apparatus can achieve liquid pressures of the order of 102 MPa. As shown in Fig. 5(a), it consists of a high-pressure vessel, a booster cabinet, and a control module. The pressurization module uses a double-stage gas-driven pressurization technique. The first-stage booster is used for pressurization up to 130 MPa, and the second-stage booster for pressurization beyond 130 MPa. To measure the pressure, a 700 MPa piezoresistive pressure sensor is integrated into the booster cabinet. The chamber pressure can be displayed in real time through an ultrahigh-pressure spring tube pressure gauge and imported into remotely control software.
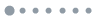
Figure 5.(a) Ultrahigh temperature and static high-pressure apparatus. (b) Nested heater chamber. The heater is placed in the high-pressure vessel. (c) High-pressure vessel with connected fiber optic couplers.
High-pressure liquid conditions can be achieved in the sample chamber with a volume of 100 ml [Fig. 5(b)]. The heating components are nested on the high-pressure vessel. Three sapphire alumina optical windows are set in the wall of the high-pressure vessel to facilitate monitoring of the state of samples in a liquid environment and dynamic analysis of reaction processes by in situ spectroscopy. As shown in Fig. 5(c), these optical windows are connected to the fluorescence spectrometer through optical fibers. In a routine high-pressure procedure, the high-pressure vessel needs to be pre-pressurized at room temperature to seal the liquid and ensure safe operation. Subsequently, it is heated to the target temperature, and the pressure is then increased to its target value. Currently, this apparatus can achieve a pressure of 500 MPa and a temperature of 800 K with 100 ml of 0.1 wt. % rhodamine 6G aqueous solution. The pressure and temperature displayed on the control panel can be directly manipulated using the control software.
B. Microliter liquid piston–cylinder liquid high-pressure apparatus
It is a great challenge to achieve an HPHT liquid environment (GPa and 1000 K scale) in a sample chamber while simultaneously performing in situ spectral measurements. In the LEPHT station, the microliter piston–cylinder liquid high-pressure apparatus is combined with a 1000 t high-pressure press (from the Max Voggenreiter Company, Germany) and a piston–cylinder high-pressure module. The 1000 t hydraulic rams are designed to apply a loading force to the piston–cylinder module. A larger piston–cylinder device was designed to achieve high-pressure liquid conditions [Figs. 6(a) and 6(b)]. The piston–cylinder module has a sample chamber volume of 10 µl. It is able to achieve pressure and temperature conditions of 1.8 GPa and 1000 K in a liquid environment. The piston–cylinder module consists of a tungsten carbide piston–cylinder assembly, a heating furnace, and an external water cooling system. The piston–cylinder assembly is equipped with diamond optical windows to enable in situ spectroscopy. The sealing of the internal sample chamber is illustrated schematically in Fig. 6(c). A pressure of 1.8 GPa and a temperature of 1000 K can be achieved in this liquid LVP.
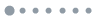
Figure 6.(a) High-pressure generation apparatus. (b) The piston–cylinder device is surrounded by a water cooling system (golden-colored). (c) Schematic of cell assembly to seal samples.
Determination of liquid chamber pressures of up to 1.8 GPa poses a challenge. Pressure calibration can be performed through in situ spectroscopy. Zircon was selected as a pressure marker material because its ν3(SiO4) Raman peak exhibits a regular shift with temperature and pressure.28,29 To calibrate the liquid pressure, the ν3(SiO4) Raman peak position was obtained by an in situ Raman system. The pressure at the corresponding temperature was then obtained by fitting this peak position. A pressure of 1.8 GPa and a temperature of 1000 K have been validated in the liquid chamber. In a typical experiment, the sample can be sealed into the liquid chamber together with zircon. The pressure and temperature of the sample can then be determined with this standard P–T marker.
C. Synthesis of materials, property regulation, and investigations into planetary science and life under extreme conditions at LEHPHT
Many kinds of materials with special structures can be synthesized under HPHT liquid conditions at lower temperatures than those required for solid state reactions. Increasing pressure effectively shortens synthetic cycles. To date, many nanoscale materials have been synthesized under high-pressure liquid conditions, such as fluorite,30 perovskite,31,32 scheelite,33 spinel,34 and pyrochlore.35,36 In addition, the application of high pressures can be used to alter the crystal structures and properties of materials. For example, high-quality metal–organic frameworks (MOFs) and covalent organic frameworks (COFs) are crystalline porous polymers, the properties of which can be tuned by the application of pressure.37–39 The normally non-emissive MOF-2 exhibits blue emission at 455 nm under pressure because of the synergetic effect of hydrogen bonding at high pressures.40 After decompression, the bright blue photoluminescence with a quantum yield up to 70.4% is retained. The availability of a wide pressure range and in situ observation methods are beneficial for adjusting the directions of MOF and COF syntheses and in the search for growth mechanisms. It is likely that the use of high-pressure liquid presses will lead to the discovery of further novel phenomena and pressure-induced smart materials.
The study of high-pressure liquid environments helps to provide an understanding of the behavior of groundwater and minerals, which is beneficial for analyzing the structure, composition, and history of planets and their satellites. For example, water–rock exchange under high pressure has significant effects on the chemical evolution of subsurface liquid water oceans on icy satellites in the Solar System.41 Extrapolation of the properties of water at high density and its high-pressure phase evolution to the conditions expected to be present in the interiors of these moons [Fig. 7(b)] is important for understanding their diversity and even their possible habitability.42–45 Furthermore, studying the individual and combined effects of high hydrostatic pressure on micro-organisms in the deep ocean [Fig. 7(c)] is relevant to understanding the origin of life on Earth and the possible existence of extraterrestrial life.46 The high-pressure liquid system at SECUF provides a leading platform for research in these directions.
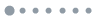
Figure 7.Material synthesis, planetary research, and biological research in HPHT liquid environments. (a) A large-molecule pressure transmitting medium (DAPHNE 7575) is used as a structure-fortifying guest species to stabilize the prototypical MOF-5 at high pressures (>9 GPa) and enable the recovery of crystalline material upon decompression. Reprinted with permission from Baxter et al., Chem. Mater. 34(2), 768–776 (2022). Copyright 2022 American Chemical Society. (b) Temperature and pressure phase diagram of water ice. Different high-pressure ice phases corresponding to different icy satellites in the solar system.47 (c) Cartoon showing organisms known to exist in the ocean under extreme conditions.48
In summary, liquid environment LVPs can overcome the limitations of studies of solid-state materials and open the way to interdisciplinary research in areas such as Earth and planetary sciences and biology, including exobiology. A variety of in situ measurement techniques are now available for liquid environments, although further developments will be necessary to meet the demanding requirements of research into HPHT liquid conditions.
IV. NHP STATION
The NHP station can realize nonequilibrium conditions both in time and in space. Spatial nonequilibrium conditions including uniaxial and shear/rotation can be realized by the 3000 t uniaxial high-pressure apparatus [Fig. 8(a)] and 3000 t rotational press [Fig. 8(b)]. A DIA-type guide-block system is used, based on that developed by Jiro Osugi’s laboratory. It incorporates upper/lower guide blocks with four 45° slopes, four more first-stage anvils with sliding wedges and a pressure intensifier main ram,49 and a pressure intensifier D-Ram. The six first-stage anvils are loaded by an electric chain hoist [Fig. 8(a)], and the cubic space is synchronously compressed in the [100] directions [Fig. 8(d)]. The first-stage anvils all have truncation lengths of 37 mm in both the 6–6 cubic mode and the 6–8 mode [Fig. 8(d)]. The AC heating system has 8, 20, and 50 V options, with a maximum power of 12 kW, and it provides a stable heating power supply.
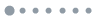
Figure 8.NHP station. (a) 30 MN (630 bars) downstroke press with (d) D-DIA-type module. (b) 30 MN (3000 t) rotational apparatus with (e) two PE-type WC anvils. (c) 10 MN (690 bars) laboratory rapid compression press with (f) double-stage PE-type module (f).
Rotation in space is realized by a 3000 t rotational press [Fig. 8(b)] which can preselect a continuous pressing force from 0 to 30 MN (corresponding to 0–630 bars). The compression and decompression rates can be continuously controlled via software at 0–100 bars/min with an accuracy of ±0.5 bars. The maximum load capacity is 2000 t and the maximum torque is 90 kN m. The main switch heater is 8 V/1500 A, 20 V/600 A, and 50 V/240 A for providing sufficient heating power. A double-toroidal first-stage anvil made of tungsten carbide (WC) is adopted for rotation [Fig. 8(e)]. An additional laser distance sensor and temperature sensor are used for detecting the pre-pressing position and the temperature of the anvils.
The RCMA-1000 t rapid compression press [Fig. 8(c)], with a maximum load of 10 MN, is based on a commercial LVP. However, to enable rapid compression, in addition to the conventional oil system, two bladder-type power accumulators (EHV 12-760/90, with gas pressure ranging from 0 to 760 bars) are added. These use compressed nitrogen and oil and include a pump, 12 electromagnetic valves and pipes, a pressure sensor (working voltage 10–30 V at 4–20 mA, corresponding to 0–1600 bars), a resistance (300 Ω), two batteries (18 V), an oscillograph (Tektronix MSO54), and a control system. Jumps in oil pressure are recorded by the oscillograph as changes in current values. The initial voltage is 1.2 V and pressures of 0–1600 bars correspond to 4–20 mA for an external resistance value of 300 Ω. Voltage values are converted to oil pressure values according to the formula (voltage signal −1.2 V)/4.8 × 1600. A single toroidal first-stage WC anvil is adopted for static and rapid compression processes.
Deformation under uniaxial high pressure is achieved using the 5/3 cell assembly shown in Fig. 9(a), where the cubic MgO assembly is located in the second-stage anvils forming the 6–6 mode. The second-stage anvils are made of WC and the anvil guide frame is made of resin or aluminum [Fig. 9(b)]. The uniaxial pressure is recorded by the software as shown in Fig. 9(c). Pressure calibration is performed through electrical measurements of the phase transition of ZnTe in the 6–6 mode with the 5/3 cell assembly as shown in Fig. 9(d).
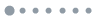
Figure 9.D-DIA press. (a) Schematic of 5/3 assembly with alumina pistons. (b) 6–6 compression mode with high-pressure shear assembly. (c) Difference compression positions of D-DIA upper and lower guide blocks. (d) Pressure calibration of conventional 5/3 assembly and shear assembly. (e) Typical signal recorded by the oscillograph during rapid compression. (f) Oil pressure jump curve obtained from this signal.
PE-type assemblies are used for rapid compression. Typical assemblies consist of pyrophyllite, with an Mo piston. A typical rapid compression process as recorded by the oscillograph is shown in Fig. 9(e). According to the equation relating the current signal and oil pressure value given above, the time/oil pressure dependence is shown in Fig. 9(f). It is found that a high oil pressure jump of 65.98 bars occurs within 15.9 ms. By modifying the assemblies, a higher pressure jump above 10 GPa within 20 ms could be achieved. The rapid compression procedure is as follows. The loading oil pressure jump value is initially set in the bladder-type power accumulator. Then, the assemblies and anvils are pre-compressed to a low pressure to eliminate gaps and cavities. Finally, the main valve is abruptly opened, and the pressure in the main cylinder is increased to the target pressure.
A. Synthesis with rapid compression and compression coupled with shear deformation
The study of materials under nonequilibrium HPHT conditions is of great importance in the context of synthesis and property modulation.50–52 Rapid compression can lead to changes in crystal structure, as well as to the formation of materials that cannot be synthesized under static high pressure. Among the valuable results obtained from rapid compression experiments are those on the changes in the phase transition path of Bi that occur under such conditions [Fig. 10(b)].53–55 The Bi-II and Bi-III phases expected from previous static measurements are not observed during pressure release following rapid compression, and instead Bi-II appears at longer delays. Rapid compression produces a highly disordered structure and leads to amorphization. With rapid compression, it is possible to produces amorphous sulfur, which has extraordinary high thermal stability. The apparatus at the NHP station can be used to prepare bulk samples of amorphous material and enables study of the Grüneisen parameter. Although dynamic shock wave compression can achieve more rapid compression, the loading rate is then too fast and is not controllable. The press at the NHP station is able to couple pressure, temperature, and loading rate (P–T – ΔP/ΔT), which will provides greater opportunities to synthesize and study the physical properties of materials at different loading rates.
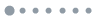
Figure 10.(a) X-ray diffraction patterns of amorphous sulfur, showing rapid compression amorphization. Reprinted with permission from Shao et al., Macromolecules 40, 9475–9481 (2007). Copyright 2007 American Chemical Society.56 (b) Compression and release path in the phase diagram of Bi under HPHT. Reprinted with permission from Pépin et al., Phys. Rev. B 100(6), 060101 (2019). Copyright 2019 American Physical Society. (c) Transition from graphite to hexagonal diamond and cubic diamond under low pressure, and to the fullerene phase under moderate pressure and shear conditions. Reprinted with permission from Gao et al., Carbon 146, 364–368 (2019). Copyright 2019 Elsevier Ltd. (d) Moment magnitudes of acoustic emission events, pressure, strain, and stress vs time. Reprinted with permission from Wang et al., Sci. Adv. 3(7), e1601896 (2017). 2024 American Association for the Advancement of Science.
The application of uniaxial ultrahigh pressures under nonequilibrium conditions can regulate phase transitions and simulate geological stress, enabling the exploration of mineral composition and geodynamics.57–60 Shear may lead to much lower pressures for phase transition points such as those of graphite and boron nitride.61,62 Deformation can induce a large number of dislocations within a metal to improve its mechanical performance. It can also create high stress inside a material to synthesize nanocrystals. In the uniaxial compression of Ni–Mn–Ga alloy, the shrinkage behavior of single crystals under strain affects the magnetic properties of the material.50 The application of high-pressure deformation and torsion has been shown to be an effective method for the synthesis of solid-state hydrogen storage materials.63,64 High pressures and high temperatures coupled with high stress can replicate the conditions in the Earth’s interior, especially the subduction zone. For example, shear-induced phase transitions and dehydration under HPHT conditions may cause embrittlement of minerals, which affects their rheological behavior and could explain the origin of deep earthquakes.65,66 Wang et al.60 conducted experiments on the preferred orientation of the olivine lattice under high pressure and high shear stress. Their results demonstrate that water has a limited effect on the dynamics of the asthenosphere, and the observed changes in lateral seismic anisotropy in the asthenosphere may affect the geometry of mantle flow. The D-DIA-type module in the NHP station can achieve controlled deformation in the vertical direction, which can be used to study the influence of the P–T–stress environment on phase transitions, for property modulation, and to simulate the conditions in the Earth’s interior.
Overall, nonequilibrium high-pressure systems expand the scope of research on static pressure in both the time and space dimensions. They provide new methods to create and study crystal structure and microstructure that are not available with static high-pressure apparatus, and they also facilitate investigations of geodynamics under high-stress conditions.
V. SUMMARY AND OUTLOOK
Different types of LVPs have been designed and constructed at SECUF to realize a variety of functions for use in a range of research areas. The solid-state subsystem provides a large chamber to meet the requirements for larger samples under ultrahigh pressures and temperatures. The liquid subsystem is able to realize the high-pressure liquid conditions in an LVP and widens the scope of research into materials in the liquid state. The nonequilibrium system enables rapid compression and deformation of materials under HPHT conditions. Furthermore, a range of in situ high-pressure techniques for use with LVPs, such as in situ high-pressure mechanical measurements, have been developed to meet the increasing demands of various disciplines of high-pressure research. More sophisticated LVP devices and in situ measurement techniques will be developed for this platform. It is anticipated that the upgrading of equipment and techniques at SECUF will provide a basis for deepening and expanding the research scope of high-pressure science.
ACKNOWLEDGMENTS
Acknowledgment. This work is supported by the Major National Science and Technology Infrastructure, the National Natural Science Foundation of China (Grant No. 12204254), and the National Major Science Facility Synergetic Extreme Condition User Facility Achievement Transformation Platform Construction (Grant No. 2021FGWCXNLJSKJ01).