1 Introduction
The explosive growth of the global commercial space industry has brought low-Earth orbit (LEO) satellite constellation programs, such as Starlink and Qianfan, to a pivotal stage in the evolution of space development toward commercialization.1 Traditional space missions have stringent requirements for mission risk and payload mass, while commercial satellite design emphasizes economic viability.2 This systemic transformation has not only redefined the operational framework of aerospace engineering but also opened critical pathways for the spatial application of emerging photovoltaic technologies. Perovskite solar cells (PSCs), endowed with high specific power and cost-effectiveness, have demonstrated competitive potential against silicon-based counterparts in terrestrial applications.3 Crucially, their application prospects are particularly promising in the space domain, where device mass, power density, and cost efficiency are critical design constraints.
However, the path to operationalizing PSCs in space is hampered by profound stability challenges.4 Ground-based studies reveal that synergistic environmental stressors—including ultraviolet/visible radiation, thermal cycling, and moisture exposure—accelerate material degradation via mechanisms such as ion migration, lattice contraction, and interfacial delamination.5 Current testing protocols, such as International Electrotechnical Commission (IEC) standards, while effective for conventional photovoltaics, fail to account for the complex parameter interdependencies inherent to PSCs.6 The absence of a unified understanding of these mechanisms has engendered fragmented experimental protocols and inconsistent data reporting, creating a critical bottleneck in harmonizing PSC stability assessments and accelerating their commercialization. Space environments impose unparalleled stressors—high-energy particle fluxes, extreme thermal gradients, and intense VUV irradiation—far exceeding terrestrial conditions. This necessitates an urgent, PSC-specific stability protocol, mirroring the global initiatives that harmonized efficiency measurement standards for this technology.
While established standards (e.g., AIAA S-111A-2014, ECSS-Q-ST-70-51C, GB/T 42633-2023) provide rigorous benchmarks for silicon and GaAs technologies, their applicability to PSCs is constrained by fundamental mismatches.7–9 PSCs exhibit distinct failure pathways—such as ion-driven interface instability and humidity-induced perovskite decomposition—that diverge from radiation-induced defect mechanisms in conventional cells. This divergence, compounded by the mismatch between PSCs current technological readiness and the short-mission lifespans of commercial satellites (5–10 years), creates a critical dilemma: overly stringent adoption of legacy standards risks excluding viable PSC innovations, while existing protocols like International Summit on Organic Photovoltaic Stability (ISOS) neglect the synergistic environmental stresses of space.10 Furthermore, unresolved challenges persist in PSC—specific encapsulation methodologies, radiation-tolerant substrate fabrication, and the absence of standardized qualification frameworks for modular systems. Directly following traditional aerospace “zero-failure” standards—formulated for mature technologies with decades-long lifespans—risks prematurely excluding promising PSC innovations.
Sign up for Advanced Photonics TOC Get the latest issue of Advanced Photonics delivered right to you!Sign up now
To address this, the development of a dedicated stability assessment framework that incorporates tiered thermal stress testing, radiation tolerance metrics, and quantification of self-healing behaviors is imperative. This framework not only optimizes resource allocation toward high-impact research domains but also establishes a fault-tolerant mechanism for iterative technological evolution, thereby catalyzing the transition of PSCs from laboratory validation to large-scale commercial satellite applications. Through this discourse, the work opens up a discussion on fostering synergistic collaboration between academia and industry to establish consensus on space-testing standards for PSCs. This could ultimately pave the way for their in-orbit validation and commercial deployment as a transformative energy technology.
2 Critical Test
2.1 Thermal Cycling
LEO, the primary operational domain for the international space station and commercial satellites, presents a severe thermodynamic environment for spacecraft.11 Due to their constant traversal of Earth’s shadow zones, these spacecraft experience extreme thermal shocks every 90 minutes: the sun-facing side can soar to temperatures exceeding 150°C, while the shadowed side plummets below –150°C, resulting in a temperature differential exceeding 300°C. These intense temperature shifts stress the materials in solar cells, especially perovskite-based ones. In high-temperature environments, ion migration intensifies within the perovskite absorber layer, accelerating chemical decomposition reactions that induce irreversible defects and efficiency degradation.12 Conversely, low temperatures trigger lattice contraction in perovskite crystals, elevating interfacial resistances and hindering charge carrier mobility.13 Furthermore, the synergistic effects of thermal stress and illumination exacerbate material fatigue, thereby shortening the operational lifespan of the devices.
Current testing methodologies, such as thermal cycling and damp-heat assessments, are inadequately aligned with the characteristics of perovskites. These methods predominantly emphasize a binary “pass/fail” result, neglecting the materials’ inherent self-repair capabilities. The crystal structure of perovskites permits defect migration to more stable locations, such as edges or surfaces, thereby preventing permanent entrapment during temperature fluctuations. This self-healing mechanism occurs through phenomena such as light-triggered repair, heat-induced reorganization, or ionic movement. By solely measuring initial and final efficiency, the dynamic recovery potential of perovskites is overlooked. To accurately assess their capabilities, testing protocols must quantify this recovery process and refrain from underestimating their stability.
We suggest introducing a tiered thermal stress testing framework to enhance existing standards. It uses three temperature ranges: ±100°C (baseline), ±120°C (enhanced), and ±150°C (extreme), matching the temperature extremes of LEO at different altitudes and mission lengths. Each test cycle includes a one-hour recovery period to measure material self-healing. Baseline validation uses 20 cycles (simulating 10 days in orbit), while extended testing scales to 1000 cycles (equivalent to one year of operation).6 Consistent encapsulation processes are critical for reliable results. We believe this framework may offer a more comprehensive approach to thermal testing, supporting reliable device validation while also potentially encouraging innovation in new materials and techniques through a structured, tiered process. We hope it can serve as a step toward developing a common and measurable standard for evaluating perovskite solar cell materials, optimizing device performance, and assessing engineering reliability—with the long-term goal of facilitating their potential use in space-related applications (Fig. 1).
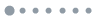
Figure 1.Illustration of suggested performance checklist for space PSC.
2.2 Proton Radiation Effects
In space irradiation environments, perovskite materials demonstrate considerable advantages over conventional photovoltaic materials. First, their exceptional defect tolerance enables carrier diffusion lengths on the micrometer scale, thereby maintaining efficient charge transport even in the presence of numerous crystalline defects.14 Moreover, these materials exhibit remarkable resilience to proton irradiation, as evidenced by their ability to withstand 2 MeV protons at a fluence of without a significant decline in device efficiency, while silicon-based and III-V solar cells experience efficiency reductions that exceed 20%.15 Furthermore, the soft lattice structure of perovskites enables partial defect self-healing, creating a fundamental difference from the irreversible radiation damage in traditional rigid-lattice materials.16
Despite their promise, perovskites face space application challenges due to mismatches between ground tests and orbital radiation environments. Conventional methods—using isotopes or mono-energetic accelerators—fail to replicate LEO’s broad proton (0.1–20 MeV) and electron spectra, especially missing sub-1 MeV protons that cause internal device damage. High costs further impede large-scale characterization. Emerging technologies such as laser-driven acceleration (LDA) and multi-energy composite field irradiators are becoming complementary solutions.17 By means of the interaction between an ultra-strong laser and a solid target, LDA generates 0.1 MeV–50 MeV continuous-spectrum proton/electron beams, cutting single-test costs by while achieving spectral matching to LEO environments. Recently, preliminary performance evaluations of PSCs have been conducted (Fig. 2), thereby paving the way for the development of low-cost and high-fidelity standards for space irradiation testing (Table 1).
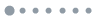
Figure 2.(a) Typical schematic diagram of temperature settings for one cycle in the thermal cycling test. TC-1 refers to a thermal shock of ±100°C (Basic Grade), TC-2 refers to a thermal shock of ±120°C (Enhanced Grade), and TC-3 refers to a thermal shock of ±150°C (Extreme Grade). The dwell time at both the highest and lowest temperatures is set at 0.2 hours (12 minutes), with the total duration of a single thermal cycle being 2 hours. The initiation of each thermal cycle is indicated by the J-V test time point, and an efficiency test is conducted once per cycle. (b) The device structure of the PSC is: . The J-V test is conducted every 10 thermal cycles. To ensure accuracy, 10 samples are measured, and the mean value along with the standard deviation is subsequently calculated. (c) Schematic representation of the LDA setup, in which the performance of the PSC was measured in situ under 1-sun conditions during proton irradiation. (d) Normalized PCE decay curves are presented at equivalent proton radiation doses for varying duration of LEO orbits.

Table 1. Suggested checklist for stability assessment of space PSCs.
Table 1. Suggested checklist for stability assessment of space PSCs.
Key aspects | Characteristic details to be reported | Thermal Shocka | Thermal Cycling Test Specifications | Basic Grade (TC-1) | ±100°C (temperature ramp rate ≥1.67°C/min) | Enhanced Grade (TC-2) | ±120°C (temperature ramp rate ≥2°C/min) | Extreme Grade (TC-3) | ±150°C (temperature ramp rate ≥2.5°C/min) | Test Period Specifications | Basic Grade | 1000 cycles | (3 months mission simulation) | Enhanced Grade | 20,000–30,000 cycles | (3–5 year mission simulation) | Evaluation Criteria | Structural Integrity | No interlayer delamination or electrode detachment observed | Photovoltaic Performance | PCE degradation ≤15% from the initial value | (measured under AM1.5G, 1-sun illumination) | High-Energy Particle Radiation Resistanceb | Proton Irradiation Test Specifications | Basic Grade (PI-1) | 0.1 MeV, | 2 MeV, | (3-year mission simulation) | Enhanced Grade (PI-2) | 0.1 MeV, | 2 MeV, | (10-year mission simulation) | Evaluation Criteria | Photovoltaic Performance | PCE degradation ≤15% (Basic Grade) | PCE degradation ≤20% (Enhanced Grade) | Dark current increase ≤30% | Vibration Endurance | Vibration Resistance Test | Launch Phase Simulation | Broadband random vibration 5–2000 Hz | Acceleration spectral density 10–20 g²/Hz | Duration ≥3 minutes | Triaxial loading | On-orbit phase simulation | High-frequency micro-vibration 10–1000 Hz | Acceleration spectral density 0.1–5 g²/Hz | Simulating deployment mechanism dynamic loads | Duration ≥10 hours. | Bending Test Specifications | Bending radius 1 mm | Cycle count 105 | Evaluation Criteria | Post-bending PCE degradation ≤8% | No substrate cracking or electrode fracture | Atomic Oxygen Erosion Resistance | Test Specification | Flux 3 × 1020 atoms/cm² | AO energy 5–8 eV | Beam uniformity ≥95% | Fully encapsulated devices | (3-year mission simulation) | Evaluation Criteria | Mass loss rate ≤5% | Transmittance attenuation at 850 nm wavelength ≤10% | Short-circuit current (ISC) degradation ≤15% | Moisture Resistancec | Humidity Test Specifications | 3 months storage under constant conditions of 45°C/95% RH in an environmental chamber | Evaluation Criteria | Water absorption rate of encapsulation layer ≤3% | Increase in device series resistance ≤20% | No visible mold spots or electrolyte leakage observed | Specific Powerd | Definition | The ratio of device output power to total mass (including encapsulation, substrate, and electrodes), used for product performance grading. | Production Classification | Grade A | >2.5 W/g (efficiency: >25%) | Grade B | 1.8–2.2 W/g (efficiency: 22%–24%) | Grade C | 1.2–1.5 W/g (efficiency: 18%–20%) | Outgassing Test | Outgassing Test Specifications | The device was placed under a vacuum of 1 × 10−4 Pa at a temperature of 125°C (257°F) and operated for 24 hours. Afterwards, its total mass loss (TML) and collected volatile condensable materials (CVCMs) were tested. | Evaluation Criteria | TML ≤1% | CVCM ≤0.1% |
|
3 Comprehensive Testing Items
When exploring the potential of perovskite solar cells for space applications, it is crucial not only to rely on thermal cycling and proton irradiation tests but also to give equal importance to other key testing factors. These additional tests play a vital role in assessing the durability of perovskite solar cell modules in real orbital environments. Although research in these areas is gaining attention, current investments are still insufficient, especially concerning atomic oxygen testing and vibration resistance.
3.1 Atomic Oxygen
In commercial space applications, the competitive advantage of perovskite materials is predicated upon their flexibility, lightweight characteristics, and tolerance to extreme environments. This necessitates the utilization of flexible polyimide substrates with controllable thicknesses ranging from 5 to 10 μm, along with lightweight, flexible encapsulation films, such as polyethylene terephthalate (PET)-modified membranes with thicknesses of , achieving an overall device areal density of less than , in comparison to – for GaAs and – for silicon-based materials.18 However, these organic flexible materials encounter significant challenges in LEO atomic oxygen (AO) environments, where AO flux can reach values in the range of . The highly oxidizing nature of AO induces surface ablation of films such as polyimide, with an erosion rate of approximately , resulting in diminished encapsulation transparency and structural failure.
To mitigate these challenges, the AO tolerance of packaging modules must be evaluated under conditions that accurately simulate orbital environments. This involves conducting accelerated testing using low-energy AO beam facilities (5–10 eV energy, beam uniformity ≥ 95%) at a flux of , which is equivalent to three years of cumulative LEO exposure, encompassing typical commercial satellite lifetimes. Key evaluation metrics include a mass loss rate of , transmittance decay at 850 nm of , and short-circuit current decay of , thereby ensuring the long-term reliability of flexible encapsulation systems in extreme oxidizing environments.
3.2 Vibration Testing
In space applications, PSCs confront critical challenges due to launch system dynamics. Broadband vibrations (5–2000 Hz, 10–20 g) during launch, alongside high-frequency micro-vibrations (10–1000 Hz, 0.1–5 g) during deployment, jeopardize film integrity and interface reliability.19 Brittle lattice structures (20–30 GPa modulus, toughness) are susceptible to microcracks and grain slippage under cyclic stress, while interface delamination (e.g., SiOX debonding energy ) accelerates water and oxygen ingress.20 Current testing methodologies, such as static irradiation and thermal cycling, neglect vibration-specific aging. Unlike titanium alloy models ( error), the failure mechanisms of PSCs remain unquantified, and the impact of thermo-vibrational stresses (150°C–300°C expansion mismatches) on crack propagation is underexplored.
To address these issues, a vibration reliability framework is required. Initial steps should involve creating ISOS-like tools for screening vibration thresholds of films and modules, followed by applying modal analysis and Steinberg’s criterion to establish standards for broadband, high-frequency, and thermo-vibrational testing. This framework must connect failure mechanisms to material and structural design, providing a roadmap for the deployment of flexible PSCs in space applications.
3.3 Specific Energy-to-Mass Ratio in Space Photovoltaics
Flexible PSC modules can facilitate ultra-light designs with a total thickness of less than 100 μm (inclusive of substrate and encapsulation) and an area density maintained below , resulting in a weight reduction exceeding 70% compared to traditional solutions. Consequently, specific energy emerges as a critical metric for assessing competitiveness. Although the efficiency of single-junction cells () is temporarily lower than that of GaAs (30%), their specific energy is 3 to 5 times greater, leading to a reduction in payload launch costs by over 30%.21 Furthermore, the high defect tolerance of perovskite materials obviates the need for complex purification processes, thereby lowering the cost per watt to less than 50% of that of traditional modules. This lifecycle economy possesses irreplaceable strategic value for the large-scale deployment of low-orbit constellations.
The current industrialization process can be expedited through a tiered technology system: basic-level modules (efficiency 18%–20%, specific energy –) cater to conventional energy requirements; optimized-level products (efficiency 22%–24%, specific energy –) have successfully undergone pilot-scale validation, exhibiting over 3000 hours of radiation stability in LEO, achieving a 40% weight reduction in 500 kg-class satellite power systems, and yielding savings of over one million US dollars in launch costs per satellite; advanced-level modules (efficiency , specific energy ) are tailored for high-orbit and deep space exploration scenarios. This gradient structure not only mitigates the risk of technical verification through basic-level products but also ensures cost competitiveness in the commercial aerospace sector with optimized-level products. Ultimately, advancements in cutting-edge technologies broaden application boundaries, establishing a transformative pathway that aligns demand, mitigates risks, and enhances value. This progression paves the way for the engineering transition of perovskite photovoltaics from laboratory innovations to aerospace-grade products.
4 Outlook
PSCs hold great promise for space applications, but their successful integration into orbital systems depends on the establishment of a robust and standardized certification framework. As technology transitions from laboratory advancements to industrial-scale implementation amid a surge in commercial space exploration, developing a tailored testing and evaluation framework becomes imperative. This framework should be built upon established aerospace photovoltaic standards while incorporating the unique properties of perovskite materials and the specific environmental stresses of orbital missions. Initial evaluations must focus on core metrics such as radiation tolerance, thermal cycling stability, and flexible encapsulation reliability. By adopting a tiered testing approach that addresses critical failure risks, this framework can provide clear engineering validation guidelines without stifling innovation, thereby facilitating the scalable integration of perovskite photovoltaics in the commercial aerospace sector.
Yifan Zheng is an associate professor in the Shanghai Institute of Optics and Fine Mechanics (SIOM), Chinese Academy of Sciences (CAS). He received his PhD in optical engineering from the University of Electronic Science and Technology of China, and then served as a postdoc in the State Key Laboratory of Artificial Microstructure and Mesoscopic Physics, Department of Physics, Peking University. His research interests are focused on space photovoltaics, and laser wireless energy transmission technology.
Guodong Zhang is the founder and CEO of Hangzhou Shangyi Optoelectronics Technology Co., Ltd (China). He obtained his PhD from SIOM, specializing in high-efficiency perovskite solar cells with an emphasis on their commercialization. He has authored over ten peer-reviewed articles in leading journals, including Joule, Advanced Materials, and Small. His current research focuses on space photovoltaics and related technologies.
Deying Luo is a full professor at the International Institute for Interdisciplinary and Frontiers, Beihang University (China). He received his PhD in atomic and molecular physics from Peking University in the area of inverted perovskite solar cells. He got his postdoctoral trainings under supervision of Professor Zheng-Hong Lu at the University of Toronto and Professor Sheng Xu at the University of California, San Diego (UCSD), working on device physics of organic and perovskite optoelectronic devices. He has published 70 peer-reviewed papers in tier 1 journals including Science, Nature, Nature Reviews Materials, Nature Materials, and Nature Reviews Chemistry.
Yuchuan Shao is a full professor at SIOM, CAS. He received his BS degree from University of Science and Technology of China (USTC) in 2009. He completed his master’s degree at SIOM in 2012 and his PhD from University of Nebraska–Lincoln. After a postdoc period at Yale University and the University of North Carolina at Chapel Hill, in 2019, he joined SIOM as a professor of photoelectronics. His current research interest focuses on perovskite optoelectronic devices.
Biographies of the authors are not available.