Introduction
Aluminum nitride (AlN) exhibits extensive potential applications in electronic and optical devices[1−5], thus, substantial research efforts have been directed towards its high crystal quality growth[6−9]. AlN boasts a wide bandgap, minimal thermal and lattice mismatches when alloys with high Al compositions such as AlGaN, and exceptional transparency in the ultraviolet (UV) region. These characteristics position AlN as an advantageous material for the fabrication of deep ultraviolet (DUV) light-emitting diodes (LEDs), photodetectors (PDs), and laser diodes (LDs) based on AlGaN materials[10−13]. It is worth noting that AlN holds particular significance in laser devices, serving as a foundational material for ultraviolet laser diodes. Additionally, it is found to be utility as an optical waveguide and contributes to the manufacture of vibrating elements in micro-electro-mechanical systems (MEMS) laser devices. This versatile range of applications underscores the paramount importance of AlN in the realm of electronic and optical technology[14−16].
The commonly used methods for epitaxial AlN include metal−organic chemical vapor deposition (MOCVD), sputtering, pulsed laser deposition (PLD), and molecular beam epitaxy (MBE). In addition, there are also some high-end methods including atomic layer deposition (ALD) and electron beam evaporation (EBE)[17−21]. Due to the low mobility of aluminum (Al) atoms at low temperatures, it has been challenging for mainstream AlN growth equipment to exceed temperatures of 1400 °C. Consequently, the utilization of microwave plasma chemical vapor deposition (MPCVD) for AlN growth represents an innovative approach to achieving high-temperature epitaxy. This method also circumvents additional reactions induced by the use of ammonia gas. Since AlN epitaxy for MPCVD is still an evolving technology, various factors affecting epitaxy quality have been exposed. These factors include microwave power, chamber pressure, hydrogen flow rate, growth temperature, substrate material, molybdenum pedestal height, trimethyl-aluminum (TMAl) precursor deposition time, Al source flow rate, nitrogen-to-hydrogen ratio, and growth duration. Comprehending and fine-tuning the operational parameters are pivotal for the enhancement of AlN epitaxial film quality fabricated via MPCVD. Notably, the temperature control within the MPCVD apparatus does not operate on an autonomous basis; it necessitates a synergistic adjustment involving both microwave power and chamber pressure[22, 23]. Similar to MPCVD equipment, MOCVD systems are often used for the epitaxial growth of AlN, gallium nitride (GaN), and gallium oxide (Ga2O3). In MOCVD processes, various surfactants can be employed to assist in controlling the epitaxial growth process and enhancing the quality and performance of thin film growth. Ref. [24] by employing tellurium (Te) as a surfactant underscored the connection between the delayed plastic relaxation of strain and the alteration of growth mode achieved through the minimization of surface energy. Ref. [25] has reported that incremental flow growth of AlN was achieved by the addition of trimethy-lindium to the growth environment, and this enhancement resulted in increased surface mobility of adsorbed aluminum species. Ref. [26] reported a noteworthy improvement in the optical and structural properties of AlN/GaN multiple quantum wells (MQWs) grown via metal−organic vapor phase epitaxy (MOVPE) using indium as a surfactant. The study of Ref. [27] presented the impact of indium as a surfactant on strain and crack formation in AlN/GaN which distributed bragg reflectors (DBRs) grown via MOVPE. In Ref. [28], taking hydrogen (H), silicon (Si), and indium (In) as examples, the study explored whether and under what conditions these impurities would have influence on the growth morphology and potentially serve as surfactants or anti-surfactants.
In this work, the MPCVD method was employed to grow AlN films using Ga as a catalyst on 4° off-axis 4H-SiC substrates. We have found that with the increasing of precursor trimethyl-gallium (TMGa) flow, the growth rate of AlN can be greatly increased, and crystal quality was first improved and then deteriorated, while the surface roughness was first increased and then decreased. Finally, by employing a two-step growth approach, involving the initial growth of a 30-min nucleation layer followed by high temperature of AlN film growth with introduction of Ga surfactants, the high growth rate of AlN film with high crystal quality and low surface roughness was achieved.
Experiment
Considering the substrate melting point and epitaxial growth temperature compatibility, along with the minimal lattice mismatch and similar lattice structures between SiC and AlN, more stable chemical properties and absence of oxygen element. Moreover, 4º 4H-SiC has a wider application prospect, and there are steps on the surface, which can promote Al atomic mobility[29], AlN films with varying TMGa flow rates were ultimately deposited on 4° 4H-SiC substrates using MPCVD. High-purity N2 was utilized as the nitrogen precursor and carrier gas, while TMAl and TMGa served as the precursors for aluminum and gallium respectively[30, 31]. The flow rates of N2, H2, and TMAl were set at 370, 135, and 35 sccm respectively. Microwave power and chamber pressure were maintained at 4800 W and 120 Torr respectively. Within this context, temperature measurements were conducted utilizing both a disappearing-filament pyrometer and an infrared thermometer.

Table 1. Experimental parameters of AlN thin films prepared at different TMGa flow rates.
Table 1. Experimental parameters of AlN thin films prepared at different TMGa flow rates.
Samples | Microwave power (W) | Pressure(Torr) | H2(sccm) | N2(sccm) | TMGa(sccm) | TMAl(sccm) | Temperature (°C) | Time (min) | X−(Al1−xGaxN) |
---|
S1 | 4800 | 120 | 135 | 370 | 0 | 35 | 1239 | 90 | W/O Ga | S2 | 4800 | 120 | 135 | 370 | 1 | 35 | 1240 | 90 | 12.5% Ga | S3 | 4800 | 120 | 135 | 370 | 5 | 35 | 1240 | 90 | 41.8% Ga | S4 | 4800 | 120 | 135 | 370 | 11 | 35 | 1150 | 90 | 61.2% Ga | S5 | 4800 | 120 | 135 | 370 | 12 | 35 | 1100 | 90 | 80% Ga |
|
Based on the differences in Ga flow rates, the deposited AlN films were categorized into five groups, denoted as S1, S2, S3, S4, and S5. Using a controlled variable approach, wherein all other parameters were kept constant, the Ga flow rate was varied as follows: S1: Direct deposition of AlN film for 90 min without the addition of any Ga source. S2: Building upon the S1 conditions, 1 sccm of TMGa was introduced. S3: Building upon the S1 conditions, 5 sccm of TMGa was introduced. S4: Building upon the S1 conditions, 11 sccm of TMGa was introduced. S5: Building upon the S1 conditions, 12 sccm of TMGa was introduced. The growth process is detailed as Table 1.
The characterization of Ga-assisted AlN films were conducted as follows: Crystalline quality of the AlN films was characterized by high-resolution X-ray diffraction (HR-XRD) on a PANalytical X’pert PRO. Surface morphology of the AlN layers was characterized by atomic force microscopy (AFM) in the tapping mode on a bruker icon in a scanning area of 5 × 5 μm2. Residual stress was estimated through raman spectroscopy at a wavelength of 532 nm. In addition, D8 advance's powder XRD, quanta FEG 250's energy dispersive X-ray spectroscopy (EDS) and scanning electron microscopy (SEM), FEI scios' focused ion beam (FIB) were used for structure and chemical composition of AlN characterization.
Results and discussion
Firstly, the crystal structure and elemental analysis of Ga-assisted AlN films were conducted to determine the presence of Ga in AlN film and its influence on the crystal structure of AlN. Fig. 1(a) showed XRD measurements of sample S1−S5, which provided more measurement angles and allowed for more detailed compound type and strength information about the AlN thin film. From XRD results, it was evident that apart from the SiC (0001) and AlN (0001) characteristic peaks, no additional crystal phase peaks were detected. Based on past experience, the higher the catalyst concentration, the easier it is to incorporate into thin film[32]. Therefore, sample S5 with the highest TMGa flow rate was measured using EDS element analysis. As shown in Fig. 1(b), EDS analysis detected the Ga content in AlN film of only 0.21%, which can be considered negligible. Therefore, it can be inferred that the introduction of Ga atoms was not incorporated into AlN films in the growth process and TMGa doping have no influence on crystalline quality and composition of AlN film.
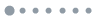
Figure 1.(Color online) (a) XRD spectra of Ga-assisted AlN films under varying TMGa flow rates respectively, (b) EDS spectra of Ga-assisted AlN sample S5.
Then FIB was used to more accurately determine the shape of the layer sidewalls and film thickness which AlN samples was performed small-scale micro cutting, for better observation of AlN surface morphology, AFM images was also measured and inserted in FIB images as shown in Fig. 2. Firstly, as increasing TMGa flow rates, AlN film thicknesses of samples S1 to S5 was respective 102, 286, 435, 487, and 546 nm, growth rate of AlN was showed a linear increase as function of TMGa proportion and five times increased from S1 to S5 as shown in Fig. 2(f), indicating the obvious catalysis of TMGa in MPCVD AlN growth. However, AFM results showed that the roughness of AlN from S1 to S5 is 30.1, 49.2, 66.5, 17.8, and 6.42 nm respectively. The morphology of Ga-assisted AlN thin films had undergone significant changes, from S1 to S3, along with the increased thickness, surface roughness of Ga-assisted AlN film was increased obviously. While as TMGa flow rate was increased further, surface roughness was decreased and AlN film was presented a two-dimensional growth mode, Sample S5 demonstrates the flattest surface when TMGa proportion increased to 80%. We speculate that the possible mechanism is that when the input of TMGa is small, the auxiliary growth effect of Ga on AlN is not significant, leading to an increased growth rate which favors the vertical growth of nucleation islands. This makes it difficult for them to merge, thus forming larger AlN islands[33]. However, when a large amount of TMGa is input, it produces more AlN nucleation sites, making the islands denser and increasing the likelihood of horizontal merging, thus reducing the roughness[34].
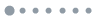
Figure 2.(Color online) (a)−(e) The cross-sectional SEM images of Ga-assisted AlN films grown under different TMGa flow rates and corresponding 5 × 5 μm2 AFM images, (f) Ga-assisted AlN growth rates as a function of Ga proportion.
For further observing Ga-assisted AlN film morphology and analyzing the change of growth mode, SEM measurement was performed. As shown in Figs. 3(a)−3(f), the surface roughness of AlN was firstly increased and then decreased along with increased TMGa flow rate which was consistent with Fig. 2, when Ga proportion further up to 80%, the surface morphology of AlN become flatter obviously, but the distinct cracking was also observed whether the center or edge of sample S5 indicating large tensile stress was induced in AlN growth process. The lattice constant of 4H-SiC (0001) plane is 3.073 Å, while this of AlN (0001) plane is 3.110 Å. Compressive stress would be expected considering the lattice constant mismatch, which was contradicted by the observed phenomenon, ruling out the influence of lattice mismatch. Furthermore, both AlN and 4H-SiC possessed identical thermal expansion coefficients of 4.5 × 10−6 K−1, thus eliminating the impact of thermal mismatch. Therefore, it is speculated that another factor, possibly introducing tensile stress, might be at play.
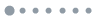
Figure 3.(a)−(f) SEM images of Ga-assisted AlN films grown with different Ga flow rates.
To investigate further, Raman spectroscopy with a wavelength of 532 nm was conducted for a more specific stress analysis, as shown in Fig. 4. The value of AlN E2 (high) characteristic peak for S1−S5 was 658.5, 658.5, 657.1, 651.4, and 647.2 cm−1 as Raman measurement shown and the theoretical value of AlN E2 (high) characteristic peak was 657 cm−1. Compared with the theoretical value, it presented a left shift trend along with TMGa flow rate increased. Sample S5 was deviated to the left by 10.2 cm−1 indicating that AlN film was experienced large tensile stress, which was consistent with the observed cracking phenomenon. Previous researches have shown that lateral coalescence of crystalline grains can introduced tensile stress in the growth process, with higher nucleation densities leading to greater tensile stress[35, 36]. Therefore, we speculate that the doping of TMGa may increase the nucleation sites of AlN in the growth process, prompting lateral coalescence and resulting in large tensile stress. Therefore, the nucleation morphology of AlN at 30 min of growth was observed to analysis the nucleation process. The SEM image of AlN nucleation layers grown without and with 80% TMGa doping are shown in Figs. 5(a) and 5(b).
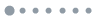
Figure 4.(Color online) The results of the Raman spectroscopy measurement.
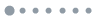
Figure 5.SEM images of AlN nucleation morphology (a) without TMGa and (b) with 80% TMGa.
As we can see, it was presented that the large but sparse nucleation islands for AlN growth without TMGa doping, while, for Ga-assisted AlN nucleation growth, the more densely distributed and more small size nucleation sites were observed. Thus, we speculate that the addition of TMGa can effective increased the nucleation sites of AlN. According to previous reports in Refs. [23, 37], the decomposition temperature of GaN is about 1050 °C, and during the MPCVD epitaxial process, hydrogen gas exhibits significant etching effects on both AlN and GaN[38]. Furthermore, in conjunction with the observed increase of AlN epitaxial nucleation sites promoting by TMGa, the probable mechanism of TMGa assisted AlN growth as catalyst in MPCVD was proposed as shown in Fig. 6.
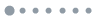
Figure 6.(Color online) (a−c) Schematic diagram of Ga-assisted AlN growth, (d−f) W/O Ga-assisted AlN growth.
The growth process of AlN assisted by TMGa in MPCVD mainly includes the following steps: Similar to the conventional epitaxial methods employed in chemical vapor deposition (CVD), gas-phase reactions lead to the accumulation of N atoms, Al atoms, Ga atoms, H atoms, TMAl oligomers, and other species above the 4H-SiC surface. Molecular and atomic species undergo physical adsorption, some oligomers are directly formed islands along with adsorbing unstable precursors and diffused along low-energy paths to stable adsorption sites, then formed bonds with H atoms, Ga atoms, Al atoms, N atoms, etc. Notably, compared with AlN nucleation process as shown in Figs. 6(d)−6(f), unlike the AlN growth process without gallium (Ga) assistance, in the AlN films with Ga, Ga atoms was introduced into gas phase reactions, the incorporated Ga nucleation sites can further fixed N atoms adhering to substrate surface and forming GaN, meanwhile more Al atoms can be fixed by nitrogen atoms, creating new AlN nucleation sites. However, the decomposition temperature of gallium nitride is approximately 1050 °C, and since our experimental temperatures exceeded this value, it is speculated that some GaN grown in the experiments decomposes at high temperatures[37]. Additionally, it is assumed that GaN is easily etched by hydrogen plasma, producing gaseous byproducts such as GaH3, which are expelled from the chamber[39, 40]. The catalytic effect of Ga atoms in this chemical reaction process promotes the formation of more nucleation sites for AlN.
The influence of different amounts of TMGa catalyst on crystal quality of AlN was evaluated simultaneously. Figs. 7(a) and 7(b) present the X-ray rocking curves for (002) and (102) planes of AlN samples S1−S5. By comparing the values of full width at half maximum (FWHM) of rocking curves for AlN films, it can provide a clearer assessment of the crystal quality of AlN films. The FWHM values of AlN (002) plane of samples S1−S5 were 677, 461.7, 393, 489.8, and 656 arcsec, and FWHM values of AlN (102) plane of samples S1−S4 were 735, 600, 582.8, and 790 arcsec, respectively, due to the peak of AlN (102) plane overlapped by the peak of SiC (104) plane, sample S5 was made accurate fitting unfeasible. Figs. 7(c) and 7(d) summarize the variation curves of AlN crystal quality, growth rate, and growth temperature as a function of Ga proportion. It is observed that as TMGa flow increased, the crystal quality of AlN presented a significant alteration. The crystal quality of AlN was improved from sample S1 to sample S3 along with AlN growth rate increased under a steady high temperature, however, when TMGa flow was further added as shown in sample S4 to sample S5, growth temperature was obviously decreased and the crystal quality of AlN was deteriorated, indicating that excessive TMGa may adversely affect the growth temperature. We speculate that the significant decrease in temperature after adding a large amount of Ga may be related to the gas environment[41]. MPCVD uses microwave energy to excite gases into plasmas that heat and promote chemical reactions. The absorption of microwave and the formation of plasma both depend on the physical and chemical properties of gas, so the characteristics of plasma make it very sensitive to changes in gas composition, and the introduction of new chemical gases (such as TMAl, TMGa) may directly affect the absorption efficiency of microwave and the stability of plasma. As the Ga flow rate increases, the quality of AlN crystals first improves and then deteriorates. From S1 to S3, as the TMGa flow rate increased, the quality of the AlN crystals improved, possibly because the incorporation of a small amount of gallium led to the merging and annihilation of dislocations during the AlN grain boundary merging process, thereby reducing the number of dislocations[42]. We speculate that the mechanism for the worsening of crystal quality in S4 and S5 could be due to a decrease in temperature, leading to a reduction in the migration rates of Al and N atoms, thereby degrading the crystal quality[43]. Moreover, after incorporating a large amount of gallium, the excessive number of nucleation sites and the large number of interfaces during nucleation island merging lead to the predominant formation of edge dislocations at these interfaces, significantly reducing the quality of the epitaxial crystals[42]. The specific mechanism needs to be further studied.
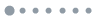
Figure 7.(Color online) (a, b) X-ray rocking curves of AlN (002) and (102) planes of samples S1−S5, (c) the variation curves of the full width at FWHM of AlN (002) and (102) planes of samples S1−S5, (d) AlN growth rate and growth temperature as function of Ga proportion.
One challenge with the aforementioned growth mode is the inability to simultaneously enhance crystal quality and reduce roughness. To address this issue, a new two-step growth method in MPCVD was proposed. Initially, a Ga-free AlN nucleation layer was grown for 30 min using only 25 sccm of TMAl and 370 sccm N2, followed by the addition of 80% TMGa as a catalyst for further AlN growth for 1 h, resulting in sample S6. It should be noted that 35 sccm TMAl is used as the precursor of the nucleation layer growth, 35 sccm TMAl and 12 sccm TMGa are used as the precursor of the upper layer growth for S6. The crystal quality, surface morphology and growth thickness of sample S6 were measured as presented in Figs. 8(a)−8(d), respectively. FWHM values of AlN (002) and (102) planes of sample S6 are 465 and 597 arcsec respectively. These values represented a significant improvement compared to S1 and S5. It is evident that the approach of growing a 30-min Ga-free AlN nucleation layer followed by Ga-assisted AlN growth resulted in a substantial enhancement of AlN crystal quality. The roughness average (Ra) value of surface roughness of sample S6 was measured at 6.6 nm, which represented a five-fold reduction compared to Sample S1. FIB observations revealed that Ga-assisted AlN epitaxy with a nucleation layer exhibits a smoother surface compared to Ga-assisted AlN epitaxy without a nucleation layer. We hypothesize that the reason behind this phenomenon lies in the high temperature of 1240 °C which was beneficial for obtaining the high single crystalline gains for the nucleation layer growth. Subsequently, after introducing 80% Ga, the catalytic effect can effectively increase growth rate and obtain more flatten surface of AlN, thereby resulting in better crystal quality compared to samples without a nucleation layer.
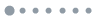
Figure 8.(Color online) FWHM values of AlN (002) (a) and (102) (b) planes, surface morphology (c) and growth thickness (d) of Sample S6.
Conclusions
In summary, the MPCVD method was employed to grow AlN films using Ga as a catalyst on 4° off-axis 4H-SiC substrates. Various measurements, including powder XRD, EDS, SEM, HR-XRD, AFM were used to investigate the crystal structure, chemical composition and surface morphology of the films. We have found that with the increase of the flow rate of precursor TMGa, the growth rate of AlN can be greatly increased. When TMGa flow was high, the two-dimensional growth mode of AlN was presented, with the increase of Ga source results in the deterioration of AlN crystal quality. When TMGa flow was low, the quality of AlN crystals could be improved and three-dimensional island growth mode of AlN was enhanced with the increase of Ga source. Furthermore, employing a two-step growth approach, involving the initial growth of a 30-min Ga-free AlN nucleation layer followed by Ga-assisted AlN growth, results in AlN films with the best crystalline quality and surface morphology.