1. Introduction
Modern society heavily relies on various electronics, such as consumer electronics, vehicles, solid-state lighting, etc. And power electronic devices are at the core of power and energy systems. Since the invention of silicon based modern electronic devices in the 1950s[1], silicon has gradually become the choice of fundamental semiconductor material in power devices. However, with the skyrocketing demand for power consumption and conversion, silicon-based power devices have already reached their material limit[2]. Novel semiconductor materials are needed to support high-efficiency, high-power, high-voltage applications.

Table 1. Comparison of the physical properties of Si, GaN, SiC, and β-Ga2O3.
Table 1. Comparison of the physical properties of Si, GaN, SiC, and β-Ga2O3.
Semiconductor material | Si | GaN | 4H-SiC | β-Ga2O3 |
---|
Eg (eV) | 1.1 | 3.4 | 3.3 | 4.7-4.9 | μ (cm2/(V·s)) | 1400 | 1200 | 1000 | 300 | Ebr (MV/cm) | 0.3 | 3.3 | 2.5 | 8 | BFOM | 1 | 870 | 340 | 3444 | λ (W/(cm·K)) | 1.5 | 2.1 | 2.7 | 0.11 |
|
To solve this problem, third-generation wide/ultrawide bandgap semiconductors, such as SiC, GaN and Ga2O3, have been extensively explored for fabricating future power electronics. To date, some SiC and GaN power devices have already achieved commercialization. For example, the fast chargers based on SiC power devices have already been applied in the charging pile for some new energy automobiles[3,4]. However, the high cost of homogeneous bulk substrates has hindered the wide adoption of these devices, since the heteroepitaxy of semiconductors is unstable in epitaxy quality. Recently, beta-phase gallium oxide has drawn much interest due to its excellent properties. The ultra-wide bandgap of 4.9 eV and costless melt-grown substrates makeβ-phase Ga2O3 ideal for large-scale and high-power devices[5].Figs. 1(a) and1(b) show the bandgap dependences of the breakdown field and theoretical limits of on-resistances (Ron) as a function of breakdown voltage (BV) among various kinds of semiconductor material, respectively[6]. Hereβ-Ga2O3 exhibits excellent breakdown voltage and on-resistance compared with GaN and SiC. Such property ranks only second to the diamond material, while the diamond semiconductor is not affordable for most of the power device production. In fact, the relationship between breakdown voltage and the on-resistances follows an exponential relationship[1]:
![(Color online) (a) The dependences between the breakdown field and bandgap. (b) Theoretical limits of the relation between on-resistances and breakdown voltage for major semiconductors and β-Ga2O3. © 2012 American Institute of Physics. Reprinted with permission from Ref. [6].](/Images/icon/loading.gif)
Figure 1.(Color online) (a) The dependences between the breakdown field and bandgap. (b) Theoretical limits of the relation between on-resistances and breakdown voltage for major semiconductors and β-Ga2O3. © 2012 American Institute of Physics. Reprinted with permission from Ref. [6].
where
,
, and
are the relative dielectric constant, electron mobility and breakdown electric field, respectively. The
is defined as Baliga’s figure of merit (BFOM), which is usually used for comparing power electronic performance of different semiconductors. The comparison of BFOM along with other physical properties can be seen inTable 1.β-Ga2O3 here shows much higher BFOM than GaN and SiC for power electronics[6].
Recently, various studies on the design and fabrication of lateralβ-Ga2O3 field-effect transistors (FETs) have been established. The growth ofβ-Ga2O3 epitaxial layers have been achieved via various methods, including metalorganic chemical vapor deposition (MOCVD)[7-9], molecular beam epitaxy (MBE)[10,11], halide vapor phase epitaxy (HVPE)[12-14], etc. The n-typeβ-Ga2O3 FET channel can be easily achieved and controlled by doping with shallow donor elements like Sn[15-17], Si[18,19], Ge[17,20], Zr[21], and Hf[22]. Ohmic contacts in the source and drain region are usually defined using Si+ ion implantation. With all this preparation, the firstβ-Ga2O3 MOSFETs with gate-connected field plate (GFP) was developed by Wonget al. in 2016[23], and the source-connected field plate (SFP) MOSFETs were also demonstrated by Lvet al.[24]. The device fabricated by Sharmaet al.[25] in 2020 showed extremely high BV of 8.03 kV using composite GFP and polymer passivation, which is the highest breakdown voltage inβ-Ga2O3 MOSFETs as recorded. Besides, verticalβ-Ga2O3 FETs have been accomplished in recent years based on the former design of GaN[26] and SiC[27]. Even though these vertical devices are still facing some difficulties such as the lack of stability and the mismatch of the present electrical system, the potential of breakdown voltage and possibity of higher forward current make it another candidate for future applicableβ-Ga2O3 FETs.
However, fabricating enhancement-modeβ-Ga2O3 FET is still challenging due to some issues from the material properties ofβ-Ga2O3. The main problem is the lack of p-type doping. The high effective hole mass causing by the flat valence band ofβ-Ga2O3 severely restricts the hole mobility, and self-trapping of holes also prevents the formation of p-type dopingβ-Ga2O3[28]. It is worth noting that the lack of p-type doping is also the reason for designing unipolarβ-Ga2O3 MOSFETs. Hence, several novel structures of E-mode FETs have now been developed, such as trench MOSFETs[29], ferroelectric gate dielectric[30], optimized doping channel[31], etc. Besides, the NiO/β-Ga2O3 p–n diode has already been fabricated[32], which has been expected to solve the p-type doping problem ofβ-Ga2O3 devices.
This article focuses on reviewing the current advances of E-modeβ-Ga2O3 FETs. This review will first talk about the lateral E-modeβ-Ga2O3 FETs, including a brief introduction of theβ-Ga2O3 MOCVD growth at the beginning. The novel design and key parameters of recently reported E-mode lateralβ-Ga2O3 FET will be intensively discussed afterward as a main section. Next, the recent prograss of vertical E-modeβ-Ga2O3 FETs will also be reviewed. Other optimizations of breakdown voltage and on-resistance are also presented at the end in order to completely describe the development ofβ-Ga2O3 power devices.
2. Lateralβ-Ga2O3 FET
At present, achieving E-mode lateralβ-Ga2O3 MOSFETs is still challenging. The main problem is that the gate control of lateralβ-Ga2O3 MOSFETs is not strong enough to fully deplete the channel under the gate at zero gate voltage bias. In this section, the research to overcome such difficulty was classified into three main directions. Firstly, reducing the width of the channel can make it more easily to be depleted, hence realizing the E-mode. Secondly, an easily depleted channel can also be achieved by adjusting the doping distribution in the MOSFETs channel layer. Finally, several kinds of material that present strong gate control ability can also be chosen to replace the traditional gate material.
2.1. Metalorganic chemical vapor deposition of Ga2O3
The drift layer in lateralβ-Ga2O3 FETs is rather critical for device performance. Thanks to the relatively costless native substrates, the good quality drift layer can be grown via homoepitaxial methods such as MOCVD, MBE, HVPE, LPCVD, etc. Among all these technologies, MOCVD is considered as the suitable method for the industrial production ofβ-Ga2O3 devices because of its superiority in epitaxial growth, while there are still some unsolved problems in other methods. For example, the MBE method cannot control the n-type doping concentration at a low value, and the precise control of epitaxial thickness in the nanometer range is still difficult for HVPE and LPCVD[33]. In this section, we will introduce some details about the MOCVD epitaxial method and briefly review the research and development of homoepitaxial growingβ-Ga2O3.
MOCVD is a vapor phase growing method with Ar or N2 as the carrier gas transporting the precursors such as metalorganics and oxygen in the reaction chamber. In the epitaxy ofβ-Ga2O3, TMGa[34] (or TEGa[35]), and oxygen are usually selected as the metalorganic precursor and oxide precursor, respectively. After entering the chamber, the metalorganic and oxide precursors are absorbed on the substrate and start to react with each other. The epitaxial layer is formed in this process, as well as the by-products. The by-products are swept by the carrier gas and carried to the exhaust. The schematic diagram of theβ-Ga2O3 epitaxy via the close coupled showerhead MOCVD technique is shown inFig. 2(a)[36]. Such a technique is more suitable for industrial production, and the horizontal type is more commonly used in scientific research.
![(Color online) (a) The schematic of the showerhead MOCVD reaction chamber. © 2021 Elsevier B.V. Reprinted with permission from Ref. [34]. (b) The schematic diagram showing the mechanism of step-flow growth and two-dimensional nucleation growth. © 2019 American Institute of Physics. Reprinted with permission from Ref. [37].](/Images/icon/loading.gif)
Figure 2.(Color online) (a) The schematic of the showerhead MOCVD reaction chamber. © 2021 Elsevier B.V. Reprinted with permission from Ref. [34]. (b) The schematic diagram showing the mechanism of step-flow growth and two-dimensional nucleation growth. © 2019 American Institute of Physics. Reprinted with permission from Ref. [37].
The epitaxial rate and quality are affected by several parameters. Firstly, the selection of gallium sources should be considered carefully. Fikaduet al. studied the effects of different gallium precursors on epitaxial rate, including Ga(DPM)3, TMGa, and TEGa[37]. It is found that TMGa has the highest growth rate due to its high decomposition temperature. But the TMGa can introduce carbon that is considered as the donor-type impurities, possibly degrading device electronic performance. Hence, the high-qualityβ-Ga2O3 layers now are mainly fabricated via TEGa[9]. But Seryoginet al. later proved that high-qualityβ-Ga2O3 layers could also be obtained using TMGa[34]. In their study, a record low-temperature electron mobility exceeding 23 000 cm2/(V·s) at 32 K has been achieved. Seryoginet al. also mentioned that unexpected impurities can be diminished via growth condition modulation. By changing the O2/TMGa ratio from 230 to 530, the value of carbon concentration dropped below the instrument detection limit, and the RT Hall mobility of 113 cm2/(V·s) atn = 1 × 1017 cm−3 was recoveried from the resistive condition.
Secondly, for better epitaxial growth ofβ-Ga2O3, the native substrates usually have a small miscut angle for step flow growth mode. But to be honest, the step flow growth won’t be achieved without the careful optimization of growth parameters. Anoozet al. studied the transition between different growth modes and gave guidance about how to adjust the growth condition[38].Fig. 2(b) shows a schematic diagram of two growth modes[39]. The relation between the source diffusion length and terrace width determines the morphology of the layer. The step flow growth only occurs when the diffusion length is comparable to the terrace length, and a step-bunching growth will appear when the diffusion length is much larger than the terrace length. It is obvious that the terrace length is getting longer as the miscut angle increasing, and the diffusion length can be changed as the change of chamber pressure and gallium flux. By adjusting the growth condition, the balance between terrace length and diffusion length will finally be found, and then the growth ofβ-Ga2O3 will follow the step flow mode.
Thirdly, the n-type conductivity ofβ-Ga2O3 can be realized via Si+ doping. However, the tradeoff between doping concentration and carrier mobility still needs further study. The discrepancy between the carrier density and doping concentration indicates the existence of compensating defects and impurities. For precisely measuring theβ-Ga2O3 crystal quality, the low-temperature hall mobility can be applied, and the measurement result is shown inFig. 3(a)[33]. A peak mobility of 4984 cm2/(V·s) was achieved at a temperature of 45 K, indicating the low concentration of scattering centers. Meanwhile, three different donor energy levels can also be studied via the dependence of Hall charge density on the reciprocal of temperature (1000/T) obtained from this Hall measurement. The one with the lowest energy belongs to Si, while the origin of other donor levels has not been fully understood yet.Fig. 3(b) is a SIMS depth profile of impurities in MOCVD grown (010)β-Ga2O3 homoepitaxial thin film[33]. The carbon impurity comes from the TMGa, and the origin of Fe is the diffusion of Fe-doped substrate. The impurity concentration in the bulk area is below the detecting limit, proving the good quality of MOCVD growth layer even with Si+ doping.
![(Color online) (a) Temperature dependence of carrier mobility tested in low-temperature hall measurement. (b) SIMS depth distribution of impurities in MOCVD grown β-Ga2O3 epitaxial layer on (010) substrate. © 2019 American Institute of Physics. Reprinted with permission from Ref. [31].](/Images/icon/loading.gif)
Figure 3.(Color online) (a) Temperature dependence of carrier mobility tested in low-temperature hall measurement. (b) SIMS depth distribution of impurities in MOCVD grown β-Ga2O3 epitaxial layer on (010) substrate. © 2019 American Institute of Physics. Reprinted with permission from Ref. [31].
2.2. E-mode via channel reshaping
E-mode lateral Ga2O3 MOSFETs via channel reshaping was first achieved by Chabaket al.[40]. They fabricated a wrap-gate fin field-effect transistors on native (100)β-Ga2O3 substrate.Fig. 4(a) shows the fabrication process of the wrap-gate FinFETs. Firstly, a double layer Cr hard mask was deposited by electron beam lithography. The inductively coupled plasma (ICP) etching process was employed afterward[41]. In this process, the Cr hard mask and theβ-Ga2O3 layer were etched simultaneously in the ratio of 1 : 2, forming the fin gate structure and the bulk mesa contacts for source and drain electrodes. The triangle shape of the fin structure with a width of 300 nm at the bottom and a height of 200 nm was formed by over-etching, through which the Cr hard mask between fins was totally removed. Ohmic contacts were achieved by depositing Ti/Al/Ni/Au (20/100/50/50 nm) followed by rapid annealing process for 1 min at 470 °C in nitrogen. The 20 nm Al2O3 and the Ni/Au (20/480 nm) were used as the gate dielectric and gate metal, respectively.Fig. 4(c) shows the transfer characteristic of this device atVDS = 10 V. An obvious enhancement mode with a threshold voltage of 1 V can be extracted in this curve, proving that the thin fin-shaped channels are easily depleted. Besides the E-mode, the relatively high breakdown voltage of 600 V is also realized, as shown inFig. 4(d).
![(Color online) (a) Fabrication process and (b) the geometry structure false-colored SEM image of FinFET with an LSD = 4. (c) The transfer characteristics in the form of log(ID)–VG with the forward and reverse sweeps. (d) The breakdown characteristics of β-Ga2O3 FinFETs with LGD of 16 and 21 μm measured at VGS = 0 V. © 2016 Chabak et al. Reprinted with permission from Ref. [40].](/Images/icon/loading.gif)
Figure 4.(Color online) (a) Fabrication process and (b) the geometry structure false-colored SEM image of FinFET with an LSD = 4. (c) The transfer characteristics in the form of log(ID)–VG with the forward and reverse sweeps. (d) The breakdown characteristics of β-Ga2O3 FinFETs with LGD of 16 and 21 μm measured at VGS = 0 V. © 2016 Chabak et al. Reprinted with permission from Ref. [40].
However, such wrap-gate FinFET is too complicated, which causes difficulties in repeatability and stability in the fabrication process. The absence of further study also verifies the lack of research value. Chabaket al. fabricated the first recessed-gate E-modeβ-Ga2O3 MOSFETs, which is much more simple in structure than the wrap-gate design[29].Fig. 5(a) shows the SEM false-colored cross-sectional view of this recessed-gate device. The initial channel with width of 200 nm was ICP etched to 60 nm at the gate region while the rest remained at 200 nm, minimizing the on-resistance. An evaporated Ti/Al/Ni/Au metal and Ti/Au metal were used as the ohmic contact and the gate metal, respectively. Obviously, the simplified etching process will lead to fewer defects and interface states, therefore reducing the threshold voltage offset and the sub-threshold swing.Figs. 5(b) and5(c) present the output and transfer characteristics of recessed-gate MOSFETs. The transfer characteristics measured atVDS = 15 V clearly shows the positive threshold voltage of around 4 V. From the curve of output characteristics, theRON = 215 Ω·mm can be extracted. Such relatively high on-resistance point out the shortcoming of decreased channel width. Donget al. also fabricated a similar E-mode recessed-gate MOSFETs, and the cross-section view is shown inFig. 6(a)[42]. The even higher on-resistance of 364 Ω·mm measured in this study increases the concern about the application prospect of recessed-gate structure. It has to be mentioned that the recessed-gate structure without E-mode was first reported by Greenet al.[43], and the power gain measurement of RF operation is the initial purpose of this device. With the thinner channel width, recessed-gateβ-Ga2O3 MOSFET can perform a high switching speed, which is suitable for RF operation. The on-resistance, as one of the crucial parameters of power devices, was not considered the key point at the beginning of the design. Recently, Huy-Binh Doet al. have offered a solution to this resistance problem in recessed-gate structure via TCAD simulation study[44]. The HfO2 gate dielectric and gate-connected field plate were used to optimize the device performance. A relatively low on-resistance of 92.1 Ω·mm was observed through the simulation process, while the device is still working in the E-mode. Such results benefited from the high permittivity of HfO2[45], resulting in more flexible control of the semiconductor Fermi-level. Besides, the breakdown voltage was increased to 1573 V after the fabrication of the field plate. However, this design is still in the simulation state yet. Further experiments of fabrication and testing are needed to prove the feasibility of the recessed-gateβ-Ga2O3 MOSFET.
![(Color online) (a) The false-colored SEM view of a recessed gate device with the LSD = 3 µm device. The HR-TEM picture below shows the facet morphology of sidewall and bottom in the gate-recess contact and gate metal interfaces. (b) The output characteristics for an LSD = 8 µm device at the gate bias of 8 V. (c) Linear transfer characteristics at VDS = 15 V. © 2017 IEEE. Reprinted with permission from Ref. [29].](/Images/icon/loading.gif)
Figure 5.(Color online) (a) The false-colored SEM view of a recessed gate device with the LSD = 3 µm device. The HR-TEM picture below shows the facet morphology of sidewall and bottom in the gate-recess contact and gate metal interfaces. (b) The output characteristics for an LSD = 8 µm device at the gate bias of 8 V. (c) Linear transfer characteristics at VDS = 15 V. © 2017 IEEE. Reprinted with permission from Ref. [29].
![(Color online) (a) Schematic diagram of the enhancement-mode MOSFET. (b) Linear transfer characteristics (IDS–VGS) of the fabricated trench gate MOSFET measured at VDS = 10 V. © 2019 IEEE. Reprinted with permission from Ref. [42].](/Images/icon/loading.gif)
Figure 6.(Color online) (a) Schematic diagram of the enhancement-mode MOSFET. (b) Linear transfer characteristics (IDS–VGS) of the fabricated trench gate MOSFET measured at VDS = 10 V. © 2019 IEEE. Reprinted with permission from Ref. [42].
2.3. E-mode via channel doping modulation
The doping process during epitaxial techniques is the critical step toward fabricating a conducting channel layer. By significantly increasing the carrier concentration, the on-state currents can be maintained at a proper value. However, high carrier concentration makes the gate control difficult to deplete the channel, which hinders the realization of E-mode lateralβ-Ga2O3 FETs. Hence, simply decreasing the carrier concentration in the channel might be helpful in achieving E-mode. Wonget al. fabricated unintentionally doped (UID) channel MOSFETs[46].Fig. 7(a) shows the cross-section view of this UID channel MOSFETs, and the device transfer characteristic is shown inFig. 7(b). Due to the low carrier concentration in the UID channel layer, the channel layer was easily depleted even with the relatively high thickness of 1.2μm. Another advantage of this design is the reduced process complexity compared to other E-mode structure. Kamimuraet al. also fabricated similar UID channel MOSFETs via MBE[31]. The channel layer that was unintentionally doped by N and Si impurities in the epitaxial process can act as a p-type material to form the E-mode MOSFETs, even if the source of these impurities remained unclear. However, the UID carrier concentration in these devices is far below the level that could provide acceptable threshold voltages and on-resistance. Therefore, the design of the channel doping needs to be further optimized to realize better performance.
![(Color online) (a) Cross section view of the E-mode MOSFETs with the UID channel layer and Si+-implanted source (drain) contacts. (b) Linear transfer characteristics at VDS = 15 V. © 2017 The Japan Society of Applied Physics. Reprinted with permission from Ref. [47].](/Images/icon/loading.gif)
Figure 7.(Color online) (a) Cross section view of the E-mode MOSFETs with the UID channel layer and Si+-implanted source (drain) contacts. (b) Linear transfer characteristics at VDS = 15 V. © 2017 The Japan Society of Applied Physics. Reprinted with permission from Ref. [47].
Recently, Guoet al. studied the muti-layer doping distribution in the MOSFETs channel via the TCAD simulation[47]. As shown inFig. 8, a surface layer was formed at the top of the Si-doped channel layer. On the one hand, the total carrier quantity has been reduced compared to the traditional channel layer, making it easier to be depleted. On the other hand, the carrier concentration in the channel beneath the surface layer remained at a high doping level. By adjusting the surface layer thickness, a trade-off between threshold voltage and device performance can be achieved. Besides, the electric field crowding at the corner of the gate could also be relaxed due to the introduction of the surface layer.
![(Color online) Schematic diagram of lateral Ga2O3 MOSFET structures (a) without and (b) with UID buffer layer. (c) The novel triple layer design of lateral MOSFET structure. © 2021 IEEE. Reprinted with permission from Ref. [47].](/Images/icon/loading.gif)
Figure 8.(Color online) Schematic diagram of lateral Ga2O3 MOSFET structures (a) without and (b) with UID buffer layer. (c) The novel triple layer design of lateral MOSFET structure. © 2021 IEEE. Reprinted with permission from Ref. [47].
Another doping optimization design was carried out by Zhouet al.[48]. The variation of lateral doping (VLD) technique was studied via TCAD simulation method. As shown inFig. 9(b), the doping concentration varies with four regions in the order of magnitudes from the gate to the drain. Such doping distribution meets both requirements of device reliability and performance. The low channel doping concentration of 1016 cm−3 near the gate not only formed an easily depleted region at zero gate voltage bias but also protected the device from early breakdown caused by the electric field crowding. As the distance to the gate region increased, the demand for device protection became less important, while the on-resistance needed to be limited in these regions. Therefore, the doping concentration becomes higher and higher to boost the carrier quantity. The result of the simulation is shown inFigs. 9(c) and9(d). The VLD lateral device and the one with a doping concentration of 1016 cm−3 were the only two that performed the E-mode among all these references. Considering the output characteristic, the device with the lowest doping concentration showed an extremely highRon, while the VLD lateral device had a moderateRon of 104.1 Ω·mm, which is close to the value of the uniform doping (UD) transistor with doping of 1017 cm−3. The breakdown voltage of UD and VLD transistors was simulated to be 1161 and 1832 V, respectively. Although all these excellent parameters above proved the success of the VLD design, such a complicated structure certainly will cause lots of problems in the fabrication process. Stenglet al. achieved this VLD via the implantation method in the silicon material[49]. A series of small holes with laterally decreasing diameter were used to realize the variation of carrier concentration. It is also pointed out that a VLD structure can also be realized via the diffusion of gas or liquid dopant source.
![(Color online) Cross section view of the FET with (a) UD layer and (b) VLD layer. The (c) linear and (d) semi-logarithmic scale of transfer characteristics extracted from the simulation. © 2021 IEEE. Reprinted with permission from Ref. [48].](/Images/icon/loading.gif)
Figure 9.(Color online) Cross section view of the FET with (a) UD layer and (b) VLD layer. The (c) linear and (d) semi-logarithmic scale of transfer characteristics extracted from the simulation. © 2021 IEEE. Reprinted with permission from Ref. [48].
Except for modulating the doping concentration, Lvet al. found another way to adjust the carrier concentration inβ-Ga2O3. The schematic cross section of the E-mode transistor fabricated by Lvet al. is presented inFig. 10(a)[50]. The channel region under the gate was treated via oxygen annealing (OA) process after the epitaxial growth. Before depositing the gate metal, the structure with only the source and drain contacts was tested to confirm the electrical mechanism of OA. The extremely high on-resistance of 739 Ω·mm was extracted at low drain bias with theLgd of 17μm. This phenomenon could be explained that the oxygen vacancies were filled or the donor impurities were oxidized in the OA process. After the test, the gate metal was deposited to form theMOSFET structure, and the SiN passivation layer was formed afterward to support two source-connected field plates. The transform characteristic presented inFig. 10(b) proves the E-mode of this OA lateral MOSFET, but also points out that the saturation current of this device is not high enough. Besides, excellent breakdown characteristics of this device were also realized on account of the field plate structure, as shown inFig. 10(c). On the whole, even though the OA treated MOSFET didn’t reach the ideal performance, finding the proper treatment method is still worth trying in the fabrication of lateral E-modeβ-Ga2O3 FETs.
![(Color online) (a) Schematic diagram of the OA β-Ga2O3 MOSFET with Lgd = 17 μm. (b) Log-scale transfer characteristics of the device. (c) The breakdown characteristics of the OA Ga2O3 MOSFET without source field plate, with single SFP and with double SFP. © 2019 WILEY-VCH Verlag GmbH & Co. KGaA, Weinheim. Reprinted with permission from Ref. [50].](/Images/icon/loading.gif)
Figure 10.(Color online) (a) Schematic diagram of the OA β-Ga2O3 MOSFET with Lgd = 17 μm. (b) Log-scale transfer characteristics of the device. (c) The breakdown characteristics of the OA Ga2O3 MOSFET without source field plate, with single SFP and with double SFP. © 2019 WILEY-VCH Verlag GmbH & Co. KGaA, Weinheim. Reprinted with permission from Ref. [50].
2.4. E-mode via novel gate material
Due to the lack of p-type doping inβ-Ga2O3, using alternative p-type materials to form heterojunctions might be a possible solution to form E-mode. Recently, the heterojunction of p-type NiOx andβ-Ga2O3 has drawn lots of interest due to its successful realization of p–n junction. The NiOx forming by sputtering and thermal oxidation of Ni owns intrinsic p-type conductivity due to the nickel defects and impurities naturally forming in the amorphous structure[51]. Luet al. fabricated the first kilovolt-class NiO/β-Ga2O3 heterojunction diodes (HJD)[52], and several remarkable achievements were achieved later[53]. The firstβ-Ga2O3 HJ-FET using NiO as the gate dielectric was fabricated by Wanget al.[54]. The structure in this study was designed to meet the requirement of testing the MOSFET and diode performance at a single device. In this research, two different channel widths of 200 and 600 nm were applied in the fabrication of HJ-FETs structure, but neither of them performed the E-mode as expected. Obviously, the gate control is not strong enough at this channel width even with HJ structure. Later, Leiet al. also studied the E-modeβ-Ga2O3 FETs on the combination of NiO/β-Ga2O3 heterojunction via TCAD simulation[55]. The device with a channel width of 600 nm was first tested to be depletion mode (D-mode) as expected. The channel width of 100 nm was then simulated, and the E-mode was almost achieved. However, a severe leakage current at low drain voltage bias was shown in the output characteristic (Fig. 11 (b)). The condition comes from the parasitic HJD between the gate and drain. When the gate voltage exceeds the drain voltage, the HJD will be turned on and will cause the severe leakage current. Hence, a Al2O3 layer with the thickness of 20 nm was then added between the gate metal and dielectric for blocking the leakage current, as shown inFig. 11(c). The absence of reverse leakage current in the output characteristic (Fig. 11(d)) demonstrates the successful control of parasitic HJD. Moreover, a more significant E-mode was achieved in this structure compared to the previous one without the blocking layer. This parasitic HJD was not considered in the previous study of heterojunction FETs, and it has to be taken into account in the future design. Recently, the real fabrication of E-modeβ-Ga2O3 HJ-FETs was achieved by Zhouet al.[32]. As shown inFig. 12(a), this E-mode was realized via the combination of p-type NiO and recessed-gate structure. It seems that the E-mode lateral Ga2O3 FETs can't be realized only by the NiO gate dielectric without sacrificing the on-resistance of the device. After the epitaxially growing 200 nm thickβ-Ga2O3 channel layer, the low RF power ICP etching method was used to form the 120 nm gate trench. Therefore, the channel width under the gate was only 80 nm. The heavily doped source and drain regions were formed by MOCVD selectively regrown using SiO2 as a hard mask. The positive threshold voltage of 0.9 V can be extracted from the transfer characteristic shown inFig. 12(b). An on-resistance of 151.5 Ω·mm and a saturation current of 10.8 mA/mm can be extracted from the linear region and saturation region of output characteristic, respectively. Even though the ideal device performance was not achieved, further study of the combination among various design of E-modeβ-Ga2O3 FETs is worthwhile.
![(Color online) Cross-sectional view of the E-mode HJ-FET (a) without the Al2O3 layer and (b) with the Al2O3 layer. The linear-scale transfer characteristics for the E-mode HJ-FET (c) without the Al2O3 layer and (d) with the Al2O3 layer. © 2022 IEEE. Reprinted with permission from Ref. [55].](/Images/icon/loading.gif)
Figure 11.(Color online) Cross-sectional view of the E-mode HJ-FET (a) without the Al2O3 layer and (b) with the Al2O3 layer. The linear-scale transfer characteristics for the E-mode HJ-FET (c) without the Al2O3 layer and (d) with the Al2O3 layer. © 2022 IEEE. Reprinted with permission from Ref. [55].
![(Color online) (a) Cross-section view of the gate-recessed HJ-FET. (b) Log-scale IDS–VGS curves of the gate-recessed HJ-FET at VDS of 0.1, 5, and 8 V. © 2022 IEEE. Reprinted with permission from Ref. [30].](/Images/icon/loading.gif)
Figure 12.(Color online) (a) Cross-section view of the gate-recessed HJ-FET. (b) Log-scale IDS–VGS curves of the gate-recessed HJ-FET at VDS of 0.1, 5, and 8 V. © 2022 IEEE. Reprinted with permission from Ref. [30].
Except for the p-type NiO, Fenget al. fabricated the E-modeβ-Ga2O3 via the laminated-ferroelectric (L-FeG) charge storage gate[30].Fig. 13(a) depicts the schematic diagram of the L-FeG E-mode FETs. The 200 nm Sn-dopedβ-Ga2O3 channel layer was deposited on the Fe-doped (010) homogeneous substrate. The source and drain region were etched for about 20 nm via the ICP method to achieve a lower Ohmic contact resistance. The laminated-ferroelectric was then formed by plasma-enhanced atomic layer deposition (PEALD), which specific layered structure can be seen in the inset ofFig. 13(a). The Al2O3 here served as a charge tunneling layer and interlayer, covering the HfO2 as the charge storage layer. The key unit of this muti-layer structure was the ferroelectric HZO. This L-FeG actually acted as the D-mode when it was first fabricated. Then, a 1 ms pulse bias of 18 V was given to the gate electrode. This gate pulse forced the HZO to build a strong polarization, hence drawing electrons through the charge tunneling layer and trapping them in the charge storage layer. These trapping electrons together with the gate electrode could offer the gate control ability strong enough to fully deplete the channel layer below.Fig. 13(c) shows the comparison of transfer characteristics between E-mode and D-mode. The threshold voltage changed from –9.85 to 1.34 V, proving the transformation from D-mode to E-mode. The low on-resistance of 23.84 Ω·mm can be extracted fromFig. 13(b), further affirming the superiority of the device. The only problem might be the complicated fabrication process and the instability of device performance. Even though Fenget al. have proved that the threshold voltage shifting was negligible, the structure complexity still calls out the concern about the real application.
![(Color online) (a) Schematic diagram of L-FeG Ga2O3 MOSFET. (b) Linear-scale IDS–VDS and (c) IDS–VGS curves of the D- and E-mode L-FeG Ga2O3 MOSFET with an LSD = 11.4 μm © 2020 Feng et al. Reprinted with permission from Ref. [30].](/Images/icon/loading.gif)
Figure 13.(Color online) (a) Schematic diagram of L-FeG Ga2O3 MOSFET. (b) Linear-scale IDS–VDS and (c) IDS–VGS curves of the D- and E-mode L-FeG Ga2O3 MOSFET with an LSD = 11.4 μm © 2020 Feng et al. Reprinted with permission from Ref. [30].
3. Verticalβ-Ga2O3 FET
3.1. Hydride vapor phase epitaxy ofβ-Ga2O3
Before the review of verticalβ-Ga2O3 devices, it is also necessary to give a brief introduction about the epitaxial method. Being different from the lateral devices, vertical FETs were usually fabricated via the HVPE technique because of their less requirement for the thickness control[2]. The pure metal Ga was first reacted with HCl at the temperature of 850 °C to form GaCl in the upstream region. In the epitaxial growth ofβ-Ga2O3, the GaCl was then transported to the downstream region along with O2 by the carrier gas. These Ga source and oxygen were finally started to react with each other on theβ-Ga2O3 native substrate which has been heated to a temperature between 800 and 1050 °C[56]. The main advantage of the HVPE method is its high growth rate over 10μm/h in theβ-Ga2O3 epitaxial growth, which makes it the common choice for the commercial production ofβ-Ga2O3 material. However, defects such as surface pits are formed in this fast growth process. Hence, extra procedures like chemical mechanical polishing (CMP) are particularly important for the HVPE technique to form a pristine surface. Besides, compared to other method, using the HVPE method can significantly decrease the background electron density in theβ-Ga2O3 epitaxial layer to the level below 1013 cm−3, further guaranteeing the subsequent device performance.
3.2. CAVETs and CBL structure
To be honest, the inspiration of verticalβ-Ga2O3 FETs is another imitation of previous successful design realized by other semi-conductor material. Wonget al. built the first verticalβ-Ga2O3 FETs using a current blocking layer (CBL) structure[57] which directly followed the similar design of GaN current aperture vertical electron transistors (CAVETs)[26] and SiC double-implanted MOSFETs[27].Fig. 14 shows the cross-sectional schematic of theβ-Ga2O3 CAVETs. The fabrication process began with the HVPE growth of the 10µm thick Si-dopedβ-Ga2O3 drift layer on the (001) native Sn-doped substrate. Both sides of this chip were then planarized by CMP to further improve the subsequent contact quality. After that, the Mg++ was implanted to the layer at the energy around 560 keV to form the CBL with an aperture at the central of it, and the defects caused by this process was partially recovered through 30 min N2 thermal annealing at 1000 °C. Subsequently, the channel region of 150 nm thick was defined by Si ion implantation. The gate dielectric and several electrodes were finally deposited after activating the dopants. Even the peak transconductance of 1.25 mS/mm and the minus threshold voltage of –34 V measured at a drain bias of 8 V showed the immaturity of this design, it was still a good start for the verticalβ-Ga2O3 FETs. The further optimization of this design was also achieved by Wonget al. in 2018. They used N++ instead of Mg++ to form the CBL because the better blocking ability of N++ was proved by the experiment, and the peak transconductance was successfully increased to 4.7 mS/mm.
![(Color online) Cross-sectional view of the current aperture vertical Ga2O3. © 2018 IEEE. Reprinted with permission from Ref. [57].](/Images/icon/loading.gif)
Figure 14.(Color online) Cross-sectional view of the current aperture vertical Ga2O3. © 2018 IEEE. Reprinted with permission from Ref. [57].
The first attempt of E-mode CAVET was still studied by Wonget al.[58].Figs. 15(a) and15(b) here show a comparison between the E-mode and D-mode CAVET. It is obvious that the key point of this E-mode design is the decrease of channel doping concentration (nch). But even the highly doped access region was enlarged in this E-mode CAVET to improve the conducting characteristic, theID of this E-mode CAVET could only reach the 1/10 of the D-mode one (nch = 1 × 1018 cm−3). Considering the complexity of this structure, it is pretty doubtful for this design to become applicable.
![(Color online) Schematics of (a) E-mode and (b) D-mode current aperture vertical Ga2O3 MOSFETs. © 2019 IEEE. Reprinted with permission from Ref. [58].](/Images/icon/loading.gif)
Figure 15.(Color online) Schematics of (a) E-mode and (b) D-mode current aperture vertical Ga2O3 MOSFETs. © 2019 IEEE. Reprinted with permission from Ref. [58].
However, researchers have already come up with kinds of ideas using CBL to realize E-modeβ-Ga2O3 FET. In 2022, Zenget al. developed the diffusion doping process to form the CBL[59]. The Mg was deposited on the surface by the spin-on-glass technique, followed by furnace thermal to accomplish the diffusion. Such a doping method won’t produce much crystal damage like ion implantation, which means the needlessness of the annealing process. Based on this technique, Zenget al. fabricated the firstβ-Ga2O3 vertical diffused barrier field-effect-transistor (VDBFET), and its schematic is shown inFig. 16. Since the source regions were totally covered by the Mg-diffused region, the VDBFET would stay at off-state without voltage bias. When applying the positive gate voltage bias, a near-box profile will be accumulated at the interface between Mg-diffused region and Al2O3, forcing the device to turn on. Thus, a natural normally-off FET was achieved with the help of CBL.
![(Color online) Cross-section schematic of the fabricated VDBFET. © 2022 IEEE. Reprinted with permission from Ref. [59].](/Images/icon/loading.gif)
Figure 16.(Color online) Cross-section schematic of the fabricated VDBFET. © 2022 IEEE. Reprinted with permission from Ref. [59].
Following similar principles as Zenget al., Maet al. and Zhouet al. constructed the E-modeβ-Ga2O3 U-Shape trench gate MOSFET (U-MOSFET). The schematic view of the UMOSFET fabricated by Zhouet al. is shown inFig. 17(a)[60]. The CBL here was realized via oxygen annealing at 1200 °C for 6 h. The top access region with the thickness of 100 nm was then defined by the Si ion implantation. After activating the dopants, they used the ICP etching process to accomplish the trench shape along with the mesa isolation. The gate dielectric and electrode were finally deposited and patterned in the trench region. The charge accumulation layer would form at the side interface between CBL and gate dielectric when the positive gate voltage was applied. The E-mode was proved through measurement with the threshold voltage of 11.5 V, and theRon,sp of 1.48 Ω·cm2 was also extracted, as shown inFigs. 17(c) and17(d). However, the breakdown characteristic was dissatisfactory, which might come from the immaturity of the oxygen annealing technique. In the study by Maet al., the similar device was fabricated but via a different method[61]. The layers here were formed by high dose of N+ implantation at the energy of 380 keV. Two types of devices with different N+ concentration level of 5 × 1018 and 1 × 1019 cm−3 were tested in this experiment, denoted as UMOS-LN and UMOS-HN, respectively. The testing results showed inFigs. 18(c) and18(d) present a higherRon,sp, but the obvious promotion of high voltage tolerance still proves the feasibility of this design. In short, further study on the fabrication of CBL is needed to find the proper method.
![(Color online) (a) Cross sections view and (b) optical micrograph of a Ga2O3 UMOSFET with CBL realized by oxygen annealing. (c) Transfer and (d) output characteristics of Ga2O3 UMOSFET © 2022 Zhou et al. Reprinted with permission from Ref. [60].](/Images/icon/loading.gif)
Figure 17.(Color online) (a) Cross sections view and (b) optical micrograph of a Ga2O3 UMOSFET with CBL realized by oxygen annealing. (c) Transfer and (d) output characteristics of Ga2O3 UMOSFET © 2022 Zhou et al. Reprinted with permission from Ref. [60].
![(Color online) (a) Schematic view of Ga2O3 UMOSFET with CBL realized by N+ implantation. Output characteristics of (b) UMOS-LN and (c) UMOS-HN. Three terminal breakdown characteristics of (d) UMOS-LN and (e) UMOS-HN. © 2023 IEEE. Reprinted with permission from Ref. [61].](/Images/icon/loading.gif)
Figure 18.(Color online) (a) Schematic view of Ga2O3 UMOSFET with CBL realized by N+ implantation. Output characteristics of (b) UMOS-LN and (c) UMOS-HN. Three terminal breakdown characteristics of (d) UMOS-LN and (e) UMOS-HN. © 2023 IEEE. Reprinted with permission from Ref. [61].
3.3. FinFETs
Even though the CAVETs were the first fabricated verticalβ-Ga2O3 FET, the first achievement of vertical E-mode Ga2O3 FET was the FinFET structure fabricated by Huet al.[62]. This study was just next to their first success of fabricatingβ-Ga2O3 FinFET.Fig. 19(a) here presents the schematic structure of this device. The top 50 nm ofβ-Ga2O3 FinFET was doped with Si for the convenience of Ohmic contact. In the procedure of forming the fin shaped structure, Pt metal was patterned serving as the hard etching mask, and the chips was then etched to fin-channels with the height/width of 1.0/0.3μm. The Al2O3 and Cr was deposited as the gate dielectric and electrode in the trench, respectively, while the part on the top of the fin was etched away. A 200 nm SiO2 was deposited and patterned before the final depositing of source electrode in order to isolate the gate metal and source metal. The clear E-mode with the threshold voltage of 2.2 V can be seen in the testing results shown inFig. 19(b). TheRon,sp of 18 mΩ∙cm2 and the breakdown voltage of 1057 V also exhibit some advantages of this design. In 2019, Huet al. optimized this design via adding the source connected field plate[63]. The breakdown voltage was further increased to over 1.6 kV, and the lowerRon,sp of 5.5 mΩ∙cm2 can be extracted with the help of a wider fin shape. Right in the same year, Liet al. developed a post-deposition annealing technique that could boost the channel mobility in theβ-Ga2O3 FinFET[64]. The multi-finβ-Ga2O3 FET fabricated by them performed the record high breakdown voltage of 2.6 kV and relatively lowRon,sp of 23.2 mΩ·cm2, further showing the potential ofβ-Ga2O3 FinFET and vertical devices.
![(Color online) (a) Cross sections view and (b) output characteristics of a Ga2O3 FinFET. © 2018 IEEE. Reprinted with permission from Ref. [62].](/Images/icon/loading.gif)
Figure 19.(Color online) (a) Cross sections view and (b) output characteristics of a Ga2O3 FinFET. © 2018 IEEE. Reprinted with permission from Ref. [62].
4. Other optimizations ofβ-Ga2O3 FETs
Besides realizing the E-mode, there are still some other parameters needed to be optimized in the fabrication of lateralβ-Ga2O3 FETs. As the direct indicator of device reliability, breakdown voltage has already been considered as the key point for a long time. Recently, the field plate structure has been commonly used to increase the device breakdown voltage.Fig. 20 here shows some representative field plate structure. The employment of the field plate started from the first successful fabrication ofβ-Ga2O3 MOSFETs. Wonget al. achieved the first stableβ-Ga2O3 MOSFET via the gate-connected field plate (GFP) structure[23]. The on/off ratio over 109 andVbr of 755 V was obtained through this GFP structure. Later then, Lvet al. fabricated the source-connected field plate (SFP) with theVbr of 480/680 V,Ron,sp of 4.57/11.7 mΩ·cm2, theIDS,sat of 267/222 mA/mm and the BFOM of 50.4 MW/cm2 [24]. In 2018, Zenget al. achieved excellent performanceβ-Ga2O3
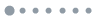
Figure 20.(Color online) Cross section view of (a) gate-connected Ga2O3 FP-MOSFET. © 2015 IEEE. (b) SFP-MOSFET © 2018 IEEE. (c) Composite gate-connected Ga2O3 FP-MOSFET © 2018 IEEE. (d) Ga2O3 composite field plate MOSFET © Mun et al. 2019. (e) Composite gate-connected Ga2O3 FP-MOSFET with polymer passivation. © 2020 IEEE.
MOSFET measured aVbr of 1850 V for aLgd = 20µm[65]. The gate-connected field plate was supported by composite atomic layer deposited (ALD) and plasma-enhanced CVD (PECVD) SiO2 layer, as shown inFig. 20(c). A similar improvement was also achieved in the SFPβ-Ga2O3 MOSFETs by Munet al.[66]. Via fabricating SFPβ-Ga2O3 MOSFETs withLgd of 25µm and composite PECVD SiO2 and Si3N4 layers, theVbr = 2.32 kV was got, and the increase of breakdown voltages followed a linear trend with theLgd. The highest breakdown voltage of lateralβ-Ga2O3 MOSFETs was observed by Sharmaet al. in their GFPβ-Ga2O3 MOSFETs[25]. The self-aligned RIE method was used on the high-dopingβ-Ga2O3 layer to form the source and drain contacts. After the formation of composite oxide layer and the gate-connected field plate, the SU-8 passivation was spin coated on the surface and patterned to open the area of metal pads. The extremely high breakdown voltage of 6.72, 8.03 kV was achieved in theLgd of 40, 70µm, respectively. Besides, some novel composite FP structures have also been proven to own some excellent properties. For example, the OA treatedβ-Ga2O3 MOSFETs fabricated by Lvet al. as mentioned above achieved both the high breakdown voltage and E-mode[50].
Fig. 21 shows another lateralβ-Ga2O3 MOSFETs structure designed by Wanget al. to enhance the device reliability[67]. A super junction (SJ) structure was fabricated in the channel region between the gate and drain. With the help of these p–n junctions, the channel can be easily depleted even with relatively high carrier concentration, resulting in a uniform distribution of the electric field. The breakdown voltage of the device can be increased without the electric field crowding, and the serious sacrifice of on-resistance through decreasing carrier concentration can be avoided. The super junction design has been commonly used in commercialized silicon power devices in order to break the theoretical limit[68]. Some devices based on ultra-wide bandgap materials like SiC[69] and GaN[70], have also adopted the super junction structure to improve their performance. Such a design was not considered in theβ-Ga2O3 device fabrication at the beginning because of the lack of p-type doping. But the development of p-type NiO offers the possibility to demonstrateβ-Ga2O3 SJs.Fig. 21 shows the fabrication process of the SJ lateralβ-Ga2O3 MOSFETs. After the deposition of source and drain metal, the trenches in the drift region were etched in the BCl3/Cl2 mixed ambient, followed by a wet treatment to smooth the etched surface. The p-NiO was then epitaxially grown in the trench by radio frequency (RF) reactive magnetron sputtering and lift-off processes. The breakdown voltage of 1326 V can be observed in the trench width of 2μm. However, the charge balance in the p–n junction is of great importance for the performance of SJ, but the control of hole carrier concentration in p-NiO is not mature enough to stably reach that balance. A big deviation of breakdown voltage among SJ devices could be observed in the study, calling for further development on the p-NiO epitaxial technique.
![(Color online) (a–e) Schematic of the fabricating steps for β-Ga2O3 SJ-equivalent MOSFETs. (f) The Photographs of SJ formed by parallel arranged p-NiO/n-Ga2O3 strips in the region between gate and drain. (g) 3-D schematic diagram of the β-Ga2O3 SJ-equivalent MOSFETs. © 2022 IEEE. Reprinted with permission from Ref. [67].](/Images/icon/loading.gif)
Figure 21.(Color online) (a–e) Schematic of the fabricating steps for β-Ga2O3 SJ-equivalent MOSFETs. (f) The Photographs of SJ formed by parallel arranged p-NiO/n-Ga2O3 strips in the region between gate and drain. (g) 3-D schematic diagram of the β-Ga2O3 SJ-equivalent MOSFETs. © 2022 IEEE. Reprinted with permission from Ref. [67].
The poor thermal conductivity is another main drawback ofβ-Ga2O3. Lots of research has been established to overcome this obstacle. Kimet al. systematically studied the thermal conducting mechanism on the dependence of two main parameters: the orientation of the channel width and the geometrical design of the metallization structures[71]. The impact of channel orientation on the thermal conducting was first studied through the real structure shown inFig. 22(b) and the simulation method. Four orientations of 0°/30°/60°/90° were compared in the real device measurement. The 30° device with the channel direction perpendicular to (−201) exhibits the lowest channel temperature rise in the measurement. Besides, the impact of metallization structures on thermal conductivity was tested to exclude the possible influence. Results showed that the metallization structures had little effect on the device thermal conductivity. However, only rotating the channel direction cannot afford enough heat dissipation that exceeds the limit ofβ-Ga2O3. The specific design to systematically improve the device thermal conductivity is needed in the fabrication ofβ-Ga2O3 MOSFETs. Recently, Songet al. have achieved the lateralβ-Ga2O3 MOSFETs on theβ-Ga2O3/4H-SiC composite wafer. By bonding the Ga2O3 substrate with other material with relatively high thermal conductivity, the self-heating problem of the Ga2O3 device can be somehow relieved to a certain extent. It is believed that diamond might be another material that can assist the device heat dissipation. The study of device-level transient cooling via diamond was also established by Kimet al.[72]. As shown inFig. 23, three structures were fabricated to compare the heat dissipation performance under steady-state and high frequency power switching conditions. The result shows that the steady-state channel temperature can be reduced by 65% through the backside bonding on the substrate. However, the second option didn’t exhibit the expectative heat dissipation ability during the high frequency power switching condition, proving that the composite substrate did not improve the transient thermal response of the device. The third option with the diamond heat spreader on both sides of the device exhibited the best performance during the high frequency power switching condition, indicating that the double-side cooling schemes might be a common choice for device-level transient cooling in the near future.
![(Color online) (a) Schematic diagram of the β-Ga2O3 MOSFET. (b) CCD images of β-Ga2O3 MOSFETs with four different channel orientations. (c) Simulation and experimental results of Gate temperatures and IR images for MOSFETs with different orientations. (d) Simulated results of relation between MOSFET channel temperatures and channel orientation at VGS = 4 V. Two devices with different channel widths of 50 and 100 μm were used in this simulation. © 2022 IEEE. Reprinted with permission from Ref. [71].](/Images/icon/loading.gif)
Figure 22.(Color online) (a) Schematic diagram of the β-Ga2O3 MOSFET. (b) CCD images of β-Ga2O3 MOSFETs with four different channel orientations. (c) Simulation and experimental results of Gate temperatures and IR images for MOSFETs with different orientations. (d) Simulated results of relation between MOSFET channel temperatures and channel orientation at VGS = 4 V. Two devices with different channel widths of 50 and 100 μm were used in this simulation. © 2022 IEEE. Reprinted with permission from Ref. [71].
![(Color online) (a) Option 1: Cross section view of a lateral β-Ga2O3 MOSFETs. (b) Option 2: A simulated structure with the β-Ga2O3 substrate bonded by the diamond at the bottom. (c) Option 3: A simulated structure based on the option 2 in (b) optimized by depositing the polycrystalline diamond over the exposed part of β-Ga2O3 channel layer. © 2022 IEEE. Reprinted with permission from Ref. [72].](/Images/icon/loading.gif)
Figure 23.(Color online) (a) Option 1: Cross section view of a lateral β-Ga2O3 MOSFETs. (b) Option 2: A simulated structure with the β-Ga2O3 substrate bonded by the diamond at the bottom. (c) Option 3: A simulated structure based on the option 2 in (b) optimized by depositing the polycrystalline diamond over the exposed part of β-Ga2O3 channel layer. © 2022 IEEE. Reprinted with permission from Ref. [72].
5. Conclusion and outlook
In conclusion, there have been considerable improvements in the design of E-modeβ-Ga2O3 FETs. Three main fabrication schemes proposed for lateral E-mode design in recent years are channel reshaping, channel doping modulation, and the selection of proper gate material. Starting from the wrap-gate design, the E-mode lateralβ-Ga2O3 FETs has been proven feasible through the channel reshaping scheme, and the invention of recessed-gate structure paved a simple way to fabricate E-mode Ga2O3 FETs. The UID channel MOSFETs is another feasible attempt, but the high on-resistance and threshold voltage call for the proper modulation of channel doping. Some E-mode devices with novel channel doping distribution have been achieved in simulation, and other methods like OA treatment can also effectively change the device’s doping concentration. As for the choice of gate material, theβ-Ga2O3 HJ-FETs using p-NiO to form the HJ gate structure has been considered as a possible solution for achieving the E-mode. Besides, there are still some novel materials like L-FeG that deserve to be carefully studied to enhance the gate control ability. Besides, there are still some novel materials like L-FeG that deserve to be carefully studied to enhance the gate control ability. Besides, the E-mode vertical Ga2O3 FET has been accomplished via the CBL structure, FinFETs and so on. Even though these attempts are still at a preliminary stage, the potential of these vertical devices is still worth exploring.
However, few of these E-mode fabrication schemes have reached the application standard due to their intrinsic drawbacks and the immaturity ofβ-Ga2O3 device fabrication technology. The high subthreshold swing of recessed-gate structure and FinFETs indicates the existence of interface states caused by the etching process. These harmful defects can be removed via some wet-etching processes like hot concentrated phosphoric acid (H3PO4) treatment. But even if the defects can be effectively eliminated, the inevitable sacrificing of on-resistance is still a big problem for recessed-gate lateral MOSFET, while the stability is still a big problem for the FinFET structures. As for the channel doping modulation, the experimental realization of these doping distribution was still absent except for the OA treatment due to some technical difficulties. A similar problem also occured in the study ofβ-Ga2O3 HJ-FETs. The E-mode can be observed in the simulation process, but this E-mode can be achieved without the help of recessed-gate in the real fabrication. Except for realizing the E-mode, theβ-Ga2O3 devices are still facing some basic problems. The device reliability needs to be further optimized through structures like field plates to approach the material limit ofβ-Ga2O3, and the bonding of high thermal conductivity material can probably solve the thermal conductivity problem. Fortunately, these difficulties mentioned above have their own solutions, which require further understanding of the material property.
In summary, considerable improvement has been achieved in the realization of E-modeβ-Ga2O3 FETs. The gap between experiments and applications will exist for a long time since theβ-Ga2O3 device fabrication is not mature enough now. Still, breakthroughs in the p-type doping ofβ-Ga2O3 or the further optimization of p–n HJ are needed to achieve the applicableβ-Ga2O3 FETs.