Structural coloration, the production of color with nanoscale structures, has steadily gained attention owing to numerous advantages such as environmental friendliness, long-term durability, and vivid coloration compared to conventional chemical pigments.1–3 In addition, recent developments in the field of nanofabrication have led to an increase in research on structural coloration with sophisticated artificial materials, known as metamaterials. Furthermore, various underlying physical mechanisms have been investigated such as Mie-scattering from high-index dielectric particles, localized surface plasmon resonances from metallic structures, and Fabry–Pérot (F-P) resonances through the use of metal-dielectric-metal multilayers. Consequently, structural coloration has attained an unprecedented pixel resolution of 10,000 pixels per inch (ppi) and full coverage of the standard RGB gamut.4–8
However, an inherent trade-off between high spatial resolution and fabrication cost prevents structural coloration from being commercially viable. For example, subwavelength dielectric structures require feature sizes in the order of 100s of nanometers,8 which inevitably requires time-consuming electron-beam lithography for fabrication. Similarly, other design approaches (i.e., localized surface plasmons and F-P resonances) suffer from a high production cost when high-density artificial structure arrays are used in the design. Nanoimprint lithography has been developed to ease such fabrication issues, and has recently been applied to manufacture 3D F-P structures by replicating molds prepared with grayscale electron-beam lithography. Nevertheless, their sample sizes remain limited to the submillimeter scale.9
Reporting in Advanced Photonics Nexus,10 a group led by Prof. Guixin Li of the Southern University of Science and Technology of China, solved this trade-off between size and resolution by using commercial direct laser writing to produce structural coloration using metamaterials made up of a semitransparent silver mirror and grayscale photoresist (PR) as the cavity of F-P structures. The thickness of the PR is controlled by grayscale exposure of direct laser writing at a recording speed of . Moreover, with this fabrication method, they achieved pixel sizes of with suppressed crosstalk between the colors. Furthermore, the maximum transmission efficiencies of the F-P structures approach 50%, which is comparable to those of conventional color filters. The authors finally presented centimeter-scale color printing with a 255-grayscale cavity thickness level demonstrating a resolution of 1200 ppi [Fig. 1(a)]. The 255-level height control enabled full coverage of the RGB gamut, which was verified using a light interferometer [Fig. 1(b)].
Sign up for Advanced Photonics TOC Get the latest issue of Advanced Photonics delivered right to you!Sign up now
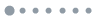
Figure 1.Demonstration of centimeter-scale structural coloration. (a) A captured image under a halogen lamp. Scale bar: 1 mm. (b) and (c) are the thickness scanning images of region 1 (R1) and region 2 (R2), respectively, using a light interferometer. Scale bars: .
The authors further claimed that the pixel resolution could be improved by increasing the numerical aperture of the objective lenses in the direct laser writing system. Clearly, considering their high transmission efficiencies and low production cost, the proposed F-P structures could have a significant impact as an alternative to commercial color filters. Furthermore, the results of this study can be applied to numerous applications using recently developed advanced materials for nanophotonic devices. For example, a humidity-sensitive photoresist was recently proposed for structural coloration11–13 that can be implanted into the cavity of F-P structures by modifying the chemical reactor of the resin to be compatible with direct laser writing. Consequently, this work not only suggests the possibility of structural coloration for diverse applications at visible frequencies but also highlights the importance of a novel approach to 3D fabrication methods using a direct laser writing process. We expect that their insightful large-area 3D fabrication approach will inspire other scholars involved in the commercialization of metalenses and metaholograms.14–17
Younghwan Yang received his BS in Mechanical Engineering at Ajou University (2018). He is currently pursuing a PhD in Mechanical Engineering at Pohang University of Science and Technology (POSTECH). He is a recipient of the Hyundai Motor Chung Mong-Koo fellowship and the NRF Ph.D. fellowship. His interests include nanofabrication of metasurfaces and metamaterials.
Trevon Badloe obtained his PhD in Mechanical Engineering at POSTECH (2023), and MPhys (hons) degree in Physics at the University of Sheffield (2012) with one year studying abroad at the National University of Singapore (2010). His interests include tunable metamaterials and metasurfaces, and machine learning for the design and optimization of nanophotonic applications.
Junsuk Rho is a Mu-Eun-Jae (无垠斋) Endowed Chair Professor and Young Distinguished Professor at POSTECH, Republic of Korea, with a double appointment in the Department of Mechanical Engineering and the Department of Chemical Engineering. He received his PhD at the University of California, Berkeley (2013), MS at the University of Illinois, Urbana-Champaign (2008), and BS at Seoul National University (2007), all in Mechanical Engineering. His research is currently focused on developing novel nanophotonic materials and their photonic applications employing advance fabrication methods.