The sol-gel method is a widely used technique in the preparation of materials with different morphologies. Thin films, powders, fibers, and other morphologies can be prepared by altering the processing conditions. The sol-gel method has been adopted widely and has seen rigorous development in the field of thin films. Sokolova et al. were the first to apply sol-gel coatings in the domain of high-power laser devices in 1967[1]. After that, sol-gel chemical coatings developed quickly and became an important feature of high-power laser devices. antireflective (AR) coatings prepared by the sol-gel method have good optical properties and high laser-induced damage thresholds. There are many optical elements that require AR coatings in large high-power laser devices around the world[2], such as the National Ignition Facility in the USA[3], the Laser MégaJoules in France[4,5], and the “Shenguang” systems in China[6–8].
Compared with films of high-refractive-index media made by physical vapor deposition, the refractive index of AR coatings made by the sol-gel method are not only low but also controllable[9,10]. According to the theory of optical film system design, double-layer, wide-bandwidth AR coatings can be achieved by depositing a high-refractive-index layer onto a substrate, followed by the deposition of a low-refractive-index thin film. It can effectively improve the light transmission efficiency of optical elements. In this Letter, AR coatings with low refractive indices were obtained by adjusting the molar ratios of ammonia and deionized water when the sols were prepared. The particle size distributions and viscosities of the sols were measured; sols with a narrow particle size distribution are stable and have a long lifetime. The lowest refractive index recorded was 1.16 at a 700 nm wavelength; the optical properties and hydrophobic performances of this coating are excellent. Thus, the results could be beneficial in the development of double-layer, wide-bandwidth AR coatings.
The sols were prepared by the Stöber method using base catalysis of ammonia[11]. The solutions, catalyzed with ammonia , were mixed with the reactants tetraethoxysilane (TEOS), deionized water , and ethanol . The molar ratios of TEOS, , , and in the solutions were , (, 3, 4, 5; , 1.0, 1.1) and the preparation process of the sols is shown in Fig. 1. The chemical reagents were stirred vigorously for more than 5 h at 5°C because the hydrolysis and condensation reaction associated with sol gels are slower at reduced temperatures. After stirring for 2 h at 20°C, all the solutions were placed into an oven to age for 7 days at 60°C. Finally, the solutions needed to be refluxed to remove ammonia to obtain the stable sols. The coatings were deposited on substrates of JGS1 silica glass and silica wafers by dip coating with a withdrawal speed of 8 cm/min and then were baked at 180°C for 24 h.
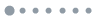
Figure 1. sol preparation process.
Twelve sol samples were prepared using different molar ratios of and , and the particle size distributions of the sols were measured by using a Malvern Nano ZS Mastersizer. It is important to judge the stability of sols from the particle size, which may influence the coating uniformity and transmittance. Figure 2 shows the particle size distributions of the sols. When the molar ratio of is fixed, the size of the particles within the colloidal silica suspension become larger as the water content is increased. Under these conditions, the mean particle sizes within the sols are approximately 7, 8, and 10 nm for corresponding molar ratios of 2, 3, and 4, respectively, and the particle size distributions show only a single peak. However, when the molar ratio of is 5, there are particles with a much larger size in the colloidal silica suspension; therefore, the particle size distributions display double peaks. These sols with large particles are unlikely to be stable over a long duration. This phenomenon is mainly determined by the content of : when the water content is relatively low, the water can fully react with tetraethoxysilane, and homogeneous sol particles can be formed. However, with the increasing water content, in particular as the molar ratio approaches 5, there will be excess water in the solution, resulting in further reactions that form larger particles.
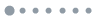
Figure 2.Particle size distributions of sols. (a) ; (b) ; (c) .
The refractive indices of AR coatings were measured using a Sopra GES-5 E Spectroscopic Ellipsometer at a wavelength of 700 nm. The film with the lowest refractive index, 1.16, originated from a sol with the following molar ratio of chemical reagents: . The results in Fig. 3 show that when the molar ratios of are identical, the refractive indices of coatings first increase and then decrease as the molar ratios of rise from 2 to 5. If Figs. 2 and 3 are analyzed together, the change in refractive indices is consistent with the change in particle sizes. This is because the refractive index of a coating is related to its porosity, and the size of the particles within the sol affects the porosity of the coating. For the sols with a mean distribution of particles, relatively small particles will occupy the pores that were shaped from the large-particle deposition during the film dip-coating process. The porosity of the coating will be reduced, and the refractive index will rise[12]. Conversely, for the sol with an molar ratio of 5, most of the particles are large, so the small particles cannot completely occupy the pores, resulting in a decrease in the film refractive index.
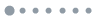
Figure 3.Refractive indices of AR coatings.
The AR coatings prepared by the sol-gel method possess a porous structure; many polar OH groups exist on the surface of the films. The water contact angles of the AR coatings were measured using a DataPhysics OCA40 instrument in order to assess the hydrophobic properties of the films. This information can be used to determine the environment for which the films could be suitable. Figure 4 shows that films deposited from sols prepared using an molar ratio of 2 exhibited contact angles about 120°, regardless of content, and therefore had excellent hydrophobic properties compared to the films of other molar ratios. As the molar ratio increased, the contact angles of the films diminished significantly down to a minimum value about 20°. This could have a deleterious effect on the quality of films when it is used in a humid environment. It can be explained that non-polar Si-O-Si groups were more prevalent than polar OH groups on the surface of films deposited using sols with an molar ratio of 2 after heating at 180°C. By contrast, sols with molar ratios of 3, 4, or 5 resulted in films with many polar OH groups in existence, even after the films were heated.
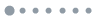
Figure 4.Contact angles of the AR coatings deposited on JGS1 substrates.
The optical spectra of AR coatings were acquired using a PerkinElmer Lambda 900 spectrophotometer, and the data are presented in Table 1. The transmittances of all the AR coatings are higher than 99.5% at the peak wavelengths except for the film deposited using a sol prepared by the molar ratios , due to some absorption in the ultraviolet range. Whereas the peak wavelengths of coatings are different with the changing of the molar ratios of water, it can show the physical thickness of coatings estimated by optical thickness. It is for this reason that the physical thickness of films deposited by sol-gel dip coating can be predicted by the Landau-Levich-Derjaguin equation[13]. The viscosity of the sol becomes the main factor determining the thickness of the coating when other parameters, including withdrawal speed and density, are similar. The viscosities of sols measured by a TA Ares-G2 rheometer are listed in Fig. 5 and are consistent with the physical thickness of film equation; the thickness of the film is proportional to the viscosity.
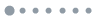
Figure 5.Viscosities of the different sols.

Table 1. Transmittance Peaks of Different SiO2 AR Coatings
Table 1. Transmittance Peaks of Different SiO2 AR Coatings
| n(NH3)=0.9 | n(NH3)=1.0 | n(NH3)=1.1 |
---|
n(H2O) | Tmax | λmax | Tmax | λmax | Tmax | λmax |
---|
2 | 99.95 | 908 | 99.98 | 900 | 99.97 | 890 | 3 | 99.93 | 506 | 99.95 | 526 | 99.97 | 502 | 4 | 99.75 | 410 | 99.89 | 414 | 99.90 | 416 | 5 | 99.79 | 450 | 97.35 | 322 | 99.56 | 434 |
|
In conclusion, this study aims to prepare sol-gel AR coatings with low refractive indices, which can be used in high-power laser devices as well as to make double-layer, wide-bandwidth AR coatings. The experimental results clearly show that the ammonia catalyst content does not affect the properties of the sols and the corresponding coatings. Conversely, the water content has an important influence on the reaction processes and the properties of the resultant sols and coatings. The sol prepared using the molar ratios result in films of the highest quality, in terms of the parameters tested (i.e., particle size, viscosity, refractive index, water contact angle, and transmittance), and thus, excellent low-refractive-index coatings can be realized.