In this work, a microfiber was applied to ultrasound sensing for the first time. Based on dual sensitization of microfiber evanescent field and PDMS package with high elastic coefficient, ultrahigh sensitivity ultrasound detection has been realized. Microfiber, as the sensing element, has the characteristics of small diameter and good flexibility, which provides the feasibility for the miniaturization of ultrasound sensor. Specifically, this linear lateral sensitive ultrasound sensor is very suitable for endoscopic photoacoustic imaging of abdominal blood vessels as shown in Fig. 2. Based on the phase detection technology and multiplexing technology, large-scale sensor arrays can be constructed to achieve real-time 2D and 3D photoacoustic imaging, which is of great promise for the study of animal brain activity and hemodynamics.
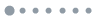
Figure 1.(a) The schematic diagram of highly sensitive ultrasound detection system based on the microfiber. The schematic diagram (b) and micrograph (c) of the microfiber ultrasound sensor. Sensitivity (d) and response bandwidth (e) of the sensor.7
As the key element of a photoacoustic imaging system, ultrasound sensors directly determine the imaging performance. The mainstream ultrasound sensors are based on the piezoelectric effect, which converts mechanical waves into electric charges2. The sensitivity of such sensors is related to the size of the piezoelectric elements. To achieve sufficient sensitivity, millimeter scale piezoelectric elements are required, which limits the miniaturization of the device.
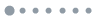
Figure 2.(a) Photoacoustic imaging system based on the microfiber ultrasound sensor. Reconstructed images (b, c). Axial (d) and lateral (e) resolutions.7
Photoacoustic imaging generates ultrasound waves by irradiating biological tissues with pulses or modulated continuous lasers. Ultrasound sensors are used to capture ultrasound signals in a distributed manner. Then, the light absorption distribution of biological tissues can be reconstructed with the help of image reconstruction algorithms. Compared with optical imaging, photoacoustic imaging provides higher spatial resolution, greater penetration depth and selective optical absorption contrast, thereby enabling detailed visualization of the distribution of hemoglobin, lipid, melanin, and other chromophores in biological tissues1.
Fiber optic sensors3, 4 provide a compelling alternative for ultrasound detection owing to the advantages of their small size, broad bandwidth and excellent immunity to electromagnetic interference. However, the sensitivity of a traditional optical fiber ultrasonic sensor is relatively low due to the large Young’s modulus of the silica fiber, thus limiting its application in weak photoacoustic signal detection. Although some new resonator structures5, 6, 8 can improve the sensitivity of fiber optic ultrasound sensors, their challenging machining characteristics and high demodulation cost impede their practical use. It is fair to say that the development of a new type of fiber optic ultrasound sensor with both high sensitivity and ease of processing would have significant application value in promoting and advancing the practical applications of photoacoustic imaging.
In the recent work published in Opto-Electronic Advances (OEA), Prof. Sun et al. have proposed a highly sensitive and miniature microfiber-based ultrasound sensor for photoacoustic tomography7. As a special optical fiber with a diameter of several microns or hundreds of nanometers, a microfiber has the characteristics of small size, large evanescent field, and sensitivity to environment, which provides a suitable platform for highly sensitive ultrasound detection. Researchers first optimized the diameter of microfiber to 7 μm in view of the larger evanescent field of microfibers. As shown in Fig. 1, the sensitivity of the sensor was further enhanced by using the Polydimethylsiloxane (PDMS) material with high elastic-optical coefficient to encapsulate the microfiber. When the ultrasound wave was applied on the sensor, the refractive index of PDMS changed correspondingly due to the elastic-optical effect, resulting in the modulated effective refractive index of the microfiber. Further, a Mach-Zehnder interferometer was constructed to demodulate the phase changes of the interrogation laser induced by the incident ultrasound waves. A feedback stabilizer based on the Proportion Integration Differentiation (PID) method was used to compensate the low frequency fluctuation caused by noise. Benefiting from this feedback stabilizer, the demodulation system can work steadily and precisely for a long time. The experimental results showed that the sensitivity of the linear microfiber ultrasound sensor was improved by an order of magnitude compared to the standard single mode fiber sensor. The sensor exhibited a low noise equivalent pressure of 0.15 kPa and a broad response bandwidth up to 14 MHz, reaching the leading levels in the reported fiber optic ultrasound sensors. As a future effort, the sensitivity and bandwidth of the sensor can be further improved by optimizing the microfiber size and detection system.
The research also demonstrated a photoacoustic imaging system based on the microfiber ultrasound sensor. The system achieved a signal-to-noise ratio (SNR) of 31 dB at the imaging depth of 12 mm, with a the lateral resolution of 250 μm and an axial resolution of 65 μm. This system exhibited the advantages of high resolution, large imaging depth and side photoacoustic/ultrasound imaging, demonstrating the great potential of applying the microfiber ultrasound sensor in medical and industrial applications.