1. INTRODUCTION
Microlens arrays (MLAs) have become widely utilized in the fields of micro-optics and micro- and nanomanufacturing because of their exceptional optical performance and high level of integration [1,2]. The incorporation of MLAs with image sensors effectively enhances the field of view, increases light flux, and thereby improves imaging contrast [3]. This also leads to the miniaturization of optical systems [4]. By exploiting the beam-splitting and focusing characteristics of MLAs, the photolithography system enables parallel microlithography operations and achieves further convergence of the focused laser beams, thereby enhancing the processing efficiency and precision of the system [5,6]. The fabrication of MLAs with superior optical performance and high integration has consistently been a research focus in the field of micro-nano processing.
Currently, several methods are available for MLA manufacturing, including traditional photolithography, hot embossing, and two-photon direct-writing techniques [7–10]. For example, Bae et al. utilized a DNRL-4615 photoresist to fabricate MLAs using a combination of multilayer lithography and thermal-reflow techniques. Their approach enabled the creation of MLAs with variable heights ranging from 15 to 45 μm, while simultaneously achieving three distinct focal lengths. The MLAs were utilized in an imaging system, effectively expanding the depth of field from 8 to 49.2 mm [11]. Jürgensen et al. used a polymer material (cellulose diacetate) to fabricate an MLA using hot-embossing technology, which improved the efficiency of the light-emitting electrochemical cells by 1.45 times [12]. Marini et al. employed an SZ2080 photoresist to fabricate plano-convex MLAs with a high numerical aperture (NA) via the two-photon direct-writing technique. The biocompatible substrate of the MLAs enabled cell cultivation, resulting in a 2.3-fold enhancement in the magnification of fluorescence images when observed through a confocal microscope and two-photon microscope [13]. In summary, MLAs have exhibited potential applications in imaging, processing, and bio-micrographic observation. However, these methods typically utilize commercial photoresists and thermosensitive materials, limiting the transparency and refractive index of the fabricated MLAs.
In recent years, researchers have discovered the potential of dielectric microspheres as novel microlenses for near-field super-resolution imaging. When parallel light is incident on a microsphere, it produces a localized optical field enhancement effect on the side of the microsphere that is backward to the incident light, known as a photonic nanojet [14,15]. Photonic nanojets have a high-intensity main lobe, weak sub-diffracting waist, and very low divergence angles, and thus have a wide range of applications in fabrication and imaging [16–21]. Moreover, microspheres can be assembled to form a microsphere-lens array. For example, Zhang et al. employed an MLA comprising randomly dispersed barium titanate glass microspheres, each with a diameter of 53 μm, embedded within polydimethylsiloxane (PDMS) to successfully achieve super-resolution imaging of samples with a minimum feature size of 110 nm. This approach significantly expanded the area suitable for super-resolution imaging, reaching up to [22]. Wu et al. employed a self-assembled array of polystyrene (PS) microspheres ranging in diameter from 1.5 to 10 μm. A patterned array of structures with a minimum feature size of 450 nm was formed via a single exposure to the photoresist. This approach improved the resolution and efficiency of microlens projection lithography [23,24]. Microsphere lenses can be rapidly self-assembled into densely packed arrays using physicochemical regulation [25,26]. For example, O’Connell et al. employed a hexagonally close-packed monolayer of microspheres adhered to a substrate, enabling the focusing of UV light and enhancing the optical near-field intensity to create ablated holes with a diameter of approximately 1.8 μm [27]. Zhu and Kinzel used a hard-baked photoresist to adhere microspheres onto an optical flat, forming a reusable microsphere mask for the fabrication of infrared metasurfaces through microsphere photolithography [28]. However, this process presents challenges in fabricating patterns of varying designs. In our previous study, we utilized the electrohydrodynamic jet (E-jet) printing method to efficiently fabricate MLAs with diverse pattern structures [29–32]. Assembling the microsphere lenses with patterned MLAs fabricated using E-jet printing technology in a controlled manner enables pattern programmability and near-field super-resolution. However, the E-jet printing method encounters significant challenges in the programmable printing of extremely small droplets and in solidifying connections with a microsphere lens.
Sign up for Photonics Research TOC Get the latest issue of Advanced Photonics delivered right to you!Sign up now
This study proposes a method that utilizes E-jet printing to assemble microsphere lenses. The assembly of arrayed microsphere lenses is facilitated by the encoding of dot patterns of an ultraviolet (UV)-curable adhesive with high precision and ultra-small volume using E-jet printing. The experimental results demonstrate the ability of the E-jet-printing-assisted assembly method to assemble microspheres with various patterns, spacings, sizes, materials, and scales. The simulation results indicate that assembling microsphere lenses on a UV-curable adhesive has little influence on the optical characteristics of the microsphere lenses. Microsphere lenses with the same diameter exhibit a higher imaging resolution than microlenses under identical conditions. A projection-lithography system is developed to align the focal plane of the microsphere lenses with the photoresist plane, enabling the direct projection-lithography patterning of micro-nanostructures onto the photoresist. A new method that combines the simplicity of assembling microsphere patterns and precision of projection lithography is introduced for the rapid prototyping of patterned micro-nanostructures. The precision of microsphere-lens projection lithography is unaffected by the UV-curable adhesive, and the minimum feature size of the nanostructures is 850 nm. This method of assembling microspheres enables the cost-effective fabrication of arbitrarily patterned templates, providing a simple and economical approach for producing microstructure arrays with submicrometer feature sizes. These patterned micro- and nanostructures have potential applications in functional devices, such as planar meta-lenses, photonic crystals, and plasma sensors.
2. EXPERIMENTAL SECTION
A. Pattern-Encoded Assembly of Microsphere Arrays
The pattern is determined by a matrix of UV-curable adhesive droplets on a glass slide (width 2 cm and thickness 160 μm); the position of each adhesive droplet aligns with the ideal position of its corresponding microsphere. The patterns were created by printing a UV-curable adhesive (NOA 63, Edmund Optics, USA) using an E-jet printing system. The detailed steps for this process are available in previous works [29,30]. Next, the dried microspheres (BaseLine ChromTech, China) were assembled on the substrate with the pattern of the UV-curable adhesive. During the assembly process, microspheres in quantities several times that of the UV-curable adhesive droplets are drawn into a syringe through negative pressure adsorption and then released onto the patterns of UV-curable adhesive. Depending on the size of the pattern, the microspheres can be transferred to the target area multiple times until all the droplets are fully assembled with microspheres. Due to the adhesive, the microspheres will assemble point-to-point onto the adhesive droplets; hence, they were positioned and adhered to the glass. Subsequently, the glass substrate assembled with microspheres was placed in a petri dish and gently blown with nitrogen to remove the unadhered microspheres. The blown-off microspheres were retained in the petri dish for recycling. Finally, the microsphere-lens arrays were exposed to UV light with an intensity of 1000 mJ/cm2 at a wavelength of 355 nm for 30 min to ensure the complete cross-linking of the UV-curable adhesive.
B. Preparation of the Photoresist Layer
The first step in preparing the photoresist substrate for microsphere-lens projection lithography involved the ultrasonic cleaning of the glass substrates with acetone and anhydrous ethanol at a frequency of 40 kHz for 30 min. The substrates were rinsed with deionized water and dried using nitrogen gas. The AZ1500 photoresist solution (Suzhou Research Materials Microtech Co., Ltd., China) was then dispensed onto the treated glass using an EZ4-S spin-coater (Lebo Science, Jiangsu, China). A two-step spin-coating process was employed, initially at 800 r/min for 30 s, followed by 5000 r/min for 60 s. The photoresist-coated glass was then heated in an oven at 100°C for 60 s, ultimately resulting in the formation of 400-nm-thick photoresist films on the glass substrate.
C. Exposure and Development
We developed a self-built projection-lithography system to perform the exposure. The system comprised three main components: an illumination component, an imaging component, and a focusing component.
The illumination component comprised two light sources and a diffuser plate. Their purpose was to provide adequate light intensity. A UV lamp with a center wavelength of 365 nm and power of was selected as the exposure light source for the lithography system. A white light source (C-HGFI, Nikon, Japan) was used for imaging illumination. Opal glass was utilized as the diffusion plate (Edmonds Optics, USA), providing uniform diffuse illumination for the imaging object as light passed through it.
The imaging component consisted of a mask, two objective lenses (Nikon, Japan), and a charge-coupled device (CCD) camera (Point Gray, Canada). To create the photomask, a commercially available black-and-white printer was used to print a pattern on a transparent film paper with a millimeter-to-centimeter scale. The image of the photomask was then scaled down by an objective lens. In addition, real-time observation of the imaging plane was achieved using another objective lens in conjunction with the CCD camera.
The focusing component comprised mounts for the marked photoresist substrate and microsphere-lens array substrate as well as a precision displacement stage. Its primary purpose was to align the imaging plane with the photoresist plane, which was accomplished through a two-step process. (1) The illumination light source was activated, and the microsphere-lens array was brought close to the photoresist. The microsphere-lens array was gradually moved along the optical axis until a clear image of the photomask was obtained using the CCD camera. Once the desired image was obtained, the microsphere-lens array substrate mount was secured. (2) The position of the photoresist substrate was adjusted along the optical axis to enable the simultaneous observation of the photomask image and mark on the photoresist using a CCD camera. Once the imaging planes of the microsphere lens and photoresist were aligned, the photoresist substrate was secured. This signified the completion of the focusing process.
Subsequently, the illumination light source was turned off, and an intense source of non-collimated UV light was switched on. The image of the photomask was projected onto the photoresist, exposing the substrate for a duration of 60 s. Following exposure, the substrate was once again subjected to baking at 120°C for 120 s. The exposed photoresist was then immersed in a bath that contained a commercial developer solution (NMD-32, Microchem, USA) for 45 s. Finally, the samples were rinsed with deionized water and dried using a stream of nitrogen.
D. Characterization and Measurements
The surface morphologies of the fabricated UV-curable adhesive dots, microsphere-lens arrays, and photolithographed structures were characterized using scanning electron microscopy (SEM; Quattro , Thermo Fisher Scientific, USA). The geometry and surface roughness of the microstructures were assessed using atomic force microscopy (AFM; Dimension Icon, Bruker Nano, Inc., USA). Fluorescence images were obtained using a titanium microscope (Eclipse TIE, Nikon, Japan).
An optical characterization system was employed to assess the optical properties of the microsphere lenses. The system comprised four components: a light source, a three-dimensional moving platform, a CCD camera (Point Gray, Canada), and two objective lenses (, Nikon, Japan). A transparent plastic sheet with a “+” pattern was chosen as the imaging target. The focusing capabilities of the microsphere lenses were tested using a plastic sheet with a circular aperture.
3. RESULTS AND DISCUSSION
A. E-jet-Printing-Assisted Assembled Patterned Microsphere-Lens Array and Microsphere Projection-Lithography Process
The process flow of the E-jet-printing-assisted assembly of the patterned microsphere-lens array and microsphere projection lithography is shown in Fig. 1. This process was divided into two parts. The first part involves the assisted assembly of microsphere-lens arrays using an E-jet printing system. The trajectory of the printed droplets was controlled using a program that encoded the desired position of the microspheres. Based on prior research, we opted to utilize the stable cone-jet mode to produce UV-curable adhesive patterns [29,30,32]. The printed droplets of the UV-curable adhesive assisted in the assembly of the microspheres, effectively templating their positions, as depicted in Figs. 1(a) and 1(b). This method enabled the production of high-precision microsphere templates at low cost. Moreover, the microspheres firmly adhered to the substrate using a UV-curable adhesive, enhancing the durability of the templates and providing a higher level of damage resistance, thereby enabling their prolonged use. Furthermore, the microsphere templates could be quickly and easily adjusted at low cost to validate experiments or create small-scale custom designs. To the best of our knowledge, this method provides a unique and innovative demonstration of the templated direct assembly of intricate patterned microsphere arrays on transparent substrates.
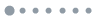
Figure 1.Schematics of the microsphere-lens template assembly and lithography process. (a) UV-curable adhesive patterned template fabricated using an E-jet printing system. (b) Process of using the UV-curable-adhesive-assisted assembly of microsphere-lens arrays for projection lithography. (c) Magnified microsphere-lens lithography.
The second part focuses on microsphere-lens projection lithography. In this process, microstructure arrays were created by employing the assembled microsphere arrays to project the image of a distant macroscopic mask onto a photoresist substrate, as illustrated in Fig. 1(c). The mask determined the shapes of the micro- and nanostructures, whereas the spatial arrangement of the structures was determined by the arrangement of the microsphere-lens arrays. Importantly, the mask enabled cost-effective and efficient iteration, thereby addressing a key challenge associated with fabricating arrayed micro- and nanostructures: the rapid evolution of the structure per unit cell [33]. The structure of each unit was essentially the same because of consistent microsphere-lens projection imaging. By exploiting the high-NA property () of silica microspheres, a spatial resolution of 0.28 μm could be attained in the UV band with a wavelength of 365 nm. Microsphere lenses possess the ability to project patterns from the centimeter or millimeter scale directly onto the micrometer or submicrometer scale without intricate procedures. The size of the projected image was reduced by a factor of approximately compared to the size of the photomask. Consequently, this resulted in reduced requirements for the mask, which could be easily produced using traditional commercial printers or laser cutting, thereby eliminating the need for electron beam or laser direct writing. E-jet-printing-assisted assembled microsphere-lens projection lithography combines the ease of assembled microsphere patterning with the precision of projection lithography, offering a novel approach for the rapid patterned fabrication of repetitive micro- and nanostructures.
B. Simulation and Numerical Analysis of Optical Properties of Assembled Microspheres
According to prior research, the projected imaging properties of microsphere lenses are closely related to their focusing characteristics [34]. The intensity and geometry of the photonic nanojet (PNJ) focused by the microspheres primarily depended on two factors: the shape of the microspheres and the refractive index contrast between the microspheres and their surrounding medium. The shape and intensity of the light field focused by the microspheres must remain unaffected by the UV-curable adhesive to maximize the optical performance. Therefore, we conducted a numerical analysis using the finite element simulation software COMSOL (COMSOL Inc., Sweden) to investigate the effect of the shape of the UV-curable adhesive on the focusing performance of the microsphere lens. In the simulation, a silica microsphere lens with a diameter of 10 μm (refractive index: [35]) was assembled on the UV-curable adhesive NOA 63 (refractive index: [29]), and the surrounding medium was air (refractive index: [34]). The incident light was a plane wave with a peak wavelength of . The light was incident from above, along the -axis, onto the microsphere lens, and it generated a PNJ [Fig. 2(a)]. To achieve the precise point-to-point assembly of the UV-curable adhesive with microspheres, the size of the adhesive was designed to be 20%, 30%, and 40% of the microsphere diameter. If the diameter of the UV-curable adhesive is too large, microspheres may adhere to the edge of the adhesive or two microspheres may stick to the same adhesive, whereas a diameter that is too small may result in poor adhesion of the microspheres to the substrate. Consequently, the sizes of the UV-curable adhesives shown in Figs. 2(b)–2(d) were selected. Considering that the a/b value (i.e., the ratio of the diameter of the adhesive droplet to its height) of the adhesive is solely related to the contact angle of the substrate and remained constant throughout this experiment [29–31], the experimentally measured a/b value of four was applied to all simulation models. Figure 2(e) shows an optical simulation of a standalone silica microsphere lens without a UV-curable adhesive, which was used for comparing and analyzing the impact of microspheres assembled on various sizes of UV-curable adhesive on the field-strength distribution. Figures 2(f)–2(h) present the simulation results of the light-intensity distribution in the plane for the respective microsphere lenses depicted in Figs. 2(b)–2(d). The figures show that the presence of the UV-curable adhesive affected the field-strength amplitude of the microsphere focusing. Figure 2(i) summarizes the distribution of the light-field intensity along the -direction for silica microspheres assembled on different shapes of the UV-curable adhesive in Figs. 2(e)–2(h). The figure provides information on the maximum intensity position (MIP) and focal length () of the light field. The smaller the size of the UV-curable adhesive, the smaller its effect on the MIP and . Figure 2(j) illustrates the profile of the nanojet at the maximum field distribution along the -direction, demonstrating the intensity and full width at half maximum (FWHM) of the PNJ. When the diameter of the UV-curable adhesive was smaller, the PNJ intensity and FWHM of the microsphere-lens focus were observed to be more similar to those without the UV-curable adhesive. Statistical data indicated that assembling microsphere lenses onto smaller-sized UV-curable adhesives resulted in minimal variation in the light field, , PNJ intensity, and FWHM compared with microsphere lenses that were not assembled on the UV-curable adhesive. Therefore, the optical properties of the microsphere lens were only minimally affected by the UV-curable adhesive. Moreover, a smaller diameter of the UV-curable adhesive resulted in a lower impact on the optical properties of the microsphere lenses.
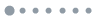
Figure 2.Simulation and numerical analysis of the optical-field distribution of microsphere lenses assembled with the assistance of a UV-curable adhesive. (a) Schematic of the focused optical field of the microsphere lens. (b)–(d) Schematic of the microsphere lens assembled with three different sizes of UV-curable adhesive. (e) Simulation of the focused optical field of a single microsphere lens that was not assembled on a UV-curable adhesive. (f)–(h) Simulation of the focused optical field of the microsphere lens assembled with three different sizes of UV-curable adhesive corresponding to (b)–(d). (i) Intensity distribution along the -axis, which is the central axis of the microsphere lens in (e)–(h). Here, is the bottom of the microsphere. (j) Intensity distribution along the -axis, which is located at the field maximum in (e)–(h).
C. Printing of UV-Curable Adhesives and in situ Assembly of Microspheres
Figure 3 illustrates the process of creating a template with a UV-curable adhesive through an E-jet printing system, as well as the in situ assembly of microspheres onto the template. Figure 3(a) shows a schematic of the process for fabricating a UV-curable adhesive template using E-jet printing. A direct current (DC) was applied between the nozzle and substrate to enable the UV-curable adhesive solution at the nozzle tip to overcome multiple coupling forces, resulting in its ejection and the formation of a UV-curable adhesive template on the substrate. The size of the UV-curable adhesive could be regulated by manipulating the E-jet printing parameters. These included the inner diameter of the nozzle, distance between the nozzle and substrate, and amplitude and duration of the applied voltage. Using the programmed path control of a precision displacement stage, UV-curable adhesive droplets of accurate sizes could be deposited exactly at designated positions on the substrate. The printing process was similar to that described in our previous study. The quality of UV-curable adhesive templates, particularly the dimensions of the UV-curable adhesive and uniformity of the array, is crucial for the accurate arrangement of microsphere projection-lithography structures. During the experiments, the use of smaller UV-curable adhesive droplets improved the precision of the assembly of the microspheres into their intended positions (Fig. 6 in Appendix A). However, the size of the UV-curable adhesive droplets should not be too small to ensure the strong adhesion of the microspheres. The experiments showed that a UV-curable adhesive droplet with a size of approximately 30% of the diameter of the microspheres provided an optimal balance between the accuracy and firmness of the microsphere assembly while minimizing the impact on the optical properties of the microsphere lenses. The SEM images in Figs. 3(b) and 3(c) display the UV-curable adhesive templates produced using E-jet printing, including templates consisting of numbers, letters, and a large range of spiral-array templates [Fig. 7(a) in Appendix B]. The AFM images in Fig. 8 of Appendix C demonstrate the ultra-microvolume, high precision, and homogeneity of the printed UV-curable adhesive droplets. The average diameter of the UV-curable adhesive droplets was , and the homogeneity of the droplets also ensured the consistent focusing of microspheres.
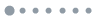
Figure 3.Fabrication and characterization of UV-curable-adhesive-printed microsphere lenses assembled in situ. (a) Schematic of the UV-curable adhesive templates printed using the E-jet system. (b), (c) SEM images of UV-curable-adhesive-patterned templates printed using the E-jet system. (d) Schematic of the in situ assembly of patterned microsphere lenses on UV-curable adhesive. (e), (f) SEM images of patterned microsphere arrays assembled on UV-curable adhesive templates corresponding to (b), (c), respectively. (g) SEM images of the assembled arrayed microspheres. (h) SEM images of the assembly of microspheres of three different sizes and materials, with a scale bar of 10 μm shown in the inset. (i) Optical image of patterned fluorescent microsphere arrays assembled over a large area.
Figure 3(d) shows a schematic of the UV-curable-adhesive-assisted assembly of the monodisperse microspheres. The microspheres were dry and assembled on a UV-curable adhesive. After the complete crosslinking of the UV-curable adhesive, the microspheres firmly adhered to the glass substrate. The SEM images in Figs. 3(e) and 3(f) illustrate the precise point-to-point assembly of 10-μm-diameter microspheres using UV-curable adhesive templates shown in Figs. 3(b) and 3(c). The microsphere-lens array is arranged in a pattern of numbers, letters, and spirals [Fig. 7(b) in Appendix B]; it demonstrated a superior quality and aligned perfectly with the intended UV-curable adhesive template. To showcase the flexibility of this methodology, we constructed microsphere patterns with pitches ranging from 20 to 35 μm [Fig. 3(g) and Fig. 9 in Appendix D]. The period of UV-curable adhesive templates is contingent upon the size of the microspheres, allowing for adjustment based on their dimensions. As shown in Fig. 10 of Appendix E, a range of template periods was successfully achieved through the E-jet printing. Additionally, arrays of silica microspheres with an average diameter of 10.1 μm, PS microspheres of 18.9 μm, and silica microspheres of 33.5 μm were assembled, as shown in Fig. 3(h). This small-scale assembly exemplified high-precision microsphere assembly. Figure 3(i) displays a large-scale assembly (approximately ) of patterned arrays containing PS fluorescent microspheres, which have a diameter of 10 μm, demonstrating the capability to assemble microspheres with diverse materials and optical properties on a large scale. The fluorescent images in Fig. 3(i) and Figs. 11(a)–11(c) of Appendix F clearly exhibit the “Butterfly,” “Puppy,” “Rose,” and “Beach” designs. Notably, the “Puppy” design was assembled using more than 3000 fluorescent microspheres. Figures 11(d)–11(f) in Appendix F show optical images of UV-curable adhesive templates for “Puppy,” “Rose,” and “Beach,” consistent with the fluorescent images in Figs. 11(a)–11(c) of Appendix F. Moreover, Figs. 11(g)–11(l) in Appendix F present various fluorescence images of the microsphere patterns. This also demonstrates the potential application of this approach in the field of light-emitting diodes and display devices [36–38]. The experimental findings demonstrate that the E-jet-printing-assisted assembly method can assemble microspheres with various patterns, spacings, sizes, materials, and scales.
D. Characterization of the Projection-Imaging Properties of Microsphere Lenses
We built an optical system to investigate the performance of microsphere-lens projection imaging, as shown in Fig. 4(a). A array of microsphere lenses was arranged on a carrier table, which could be adjusted along the optical axis. The illumination light was directed onto the “+” pattern mask and then reduced in size using a objective lens to generate a smaller image of the “+” within the optical path. By adjusting the microsphere lenses to an appropriate position along the optical axis, the CCD camera could effectively capture the projected image within each lens. Figure 4(b) presents an image depicting the “+” array that was projected by the microsphere lenses. The image of the “+” array is clear and bright and demonstrates good uniformity, indicating the excellent imaging performance of the microsphere-lens arrays assembled on the UV-curable adhesive. To accurately determine the size of the projected “+,” we extracted and normalized the light intensity values of the “+” in Fig. 4(b) to obtain the mapping image depicting the light-intensity distribution [Fig. 4(c)]. The overall size of the “+” was approximately , and the smallest feature size was 0.82 μm. The lack of clarity of the “+” image edges may be attributed to aberrations in the imaging of the microsphere lens, which is an inherent characteristic of convex lenses. These aberrations can be eliminated by optimizing the optical system; however, this falls outside the scope of this study and is not discussed here. In addition to evaluating the imaging performance, we investigated the focusing capabilities of the microsphere lens [Fig. 4(d)]. The sharp light spots indicated the excellent focusing ability of the microspheres. The normalized light-intensity distribution of the spots marked in Fig. 4(d) also demonstrated the homogeneity of the microsphere lenses. Each focal spot exhibits a Gaussian distribution with an average FWHM of 1.04 μm and a remarkably low standard deviation of only 0.13 μm. After investigating the imaging performance of microsphere-lens arrays with a diameter of 10 μm, we also examined the imaging performance of convex lenses with the same diameter for comparison [Figs. 4(f)–4(i)]. The fabrication process of the plano-convex microlenses can be found in previous studies. Under identical imaging conditions, the “+” image size observed from the microlens array was , exhibiting a minimum feature size of 1.45 μm [Figs. 4(f) and 4(g)]. This size was approximately 1.77 times larger than the microsphere imaging feature size. In addition, the focal spot imaging and extracted light-intensity distribution demonstrated that the 10-μm microsphere lens produced a smaller focal spot compared to the microlens. Overall, the assembly of microsphere lenses using UV-curable adhesives still demonstrated good imaging performance. In addition, microspheres of the same size offered better imaging resolution than microlenses.
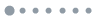
Figure 4.Characterization of the imaging performance of microspheres assembled on the UV-curable adhesive. (a) Schematic of the microsphere-lens imaging system. (b) Optical image of the “+” pattern projected by an array of microsphere lenses assembled on the UV-curable adhesive. The inset in the upper-right corner shows the magnified projected image of a single microsphere lens. (c) Normalized light-intensity mapping image corresponding to the imaging of a single microsphere lens. (d) Images of the focal spots focused by the microsphere-lens array. (e) Distribution of the normalized light intensity corresponding to the five focal spot images circled in (d). (f) Optical image of the “+” pattern projected by a microlens array. The inset in the upper-right corner shows the magnified projected image of a single microlens. (g) Normalized light-intensity mapping image corresponding to the imaging of a single microlens. (h) Images of the focal spots focused by the microlens array. (i) Distribution of the normalized light intensity corresponding to the five focal spot images circled in (h).
E. Characterization of Microsphere-Lens Projection Lithography
A microsphere projection-lithography system was constructed to demonstrate the effectiveness of microsphere-lens projection lithography, as depicted in Fig. 5(a). This system was used to align the image plane of the microsphere-lens projection with that of the photoresist. The system was equipped with two light sources: an illumination light source utilized for system modulation and calibration and a UV light source employed for exposure. The microsphere-lens array, substrate carrying the photoresist layer, and microscope could be modulated along the optical axis. The UV light was activated to initiate the exposure process when both the mark on the photoresist and image of the microsphere projection were observed simultaneously in the CCD camera using an illumination light source. During exposure, UV light was projected through the mask, creating an image of the mask on the photoresist using microsphere-focused imaging [Fig. 5(b)]. We fabricated the “+” structure utilizing the patterned microsphere array in Fig. 3. The SEM images in Figs. 5(c)–5(f) depict the nanopatterned array that was etched into the photoresist. These structural images were mirrored to facilitate a comparison with the assembled microsphere patterns. The insets in the upper-right corners provide detailed views of the structure, illustrating the quality of the high-resolution nanopatterns achieved by projection lithography using each microsphere. The corresponding AFM images of each structure are shown in Figs. 5(g)–5(i). These images reveal the morphology of structures that were photolithographed, with critical dimensions down to . The area of the pattern is constrained by the projection photolithography system. Critical parameters within this system, such as the illumination range of the ultraviolet light source, determine the effective exposure area. After measurement, it was found that the maximum area that the system can photolithograph is about . Despite the requirement of optimizing the exposure time of each mask, this process can be efficiently completed whenever necessary because of the short exposure duration, typically lasting a few tens of seconds. In the experiment, the microsphere lens array functioned similarly to a photolithography mask and could be reused. After using the same microsphere lens array for 10 projection lithography operations, there were no significant changes in the microsphere lens array. Currently, the projection photolithography system is only designed for transparent substrates. Adjusting the imaging component of the system from a projection mode to a reflection mode holds promise for extending its application to photolithography on translucent or opaque substrates.
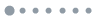
Figure 5.Characterization of microsphere-lens projection lithography. (a) Optical image of the microsphere-lens projection-lithography system. (b) Schematic of microsphere-lens array projection lithography. (c)–(f) SEM images of structures fabricated by the microsphere-lens array projection lithography, which have been mirrored. The insets in the upper-right corners show the results of a magnified individual structure. (g)–(j) AFM images corresponding to the structures in (c)–(f), respectively.
4. CONCLUSION
In this study, we proposed a method for the E-jet-printing-assisted assembly of microsphere lenses. The experimental results indicate that the E-jet-printing-assisted assembly method can be used to assemble microspheres with various patterns, spacings, sizes, materials, and scales. By combining the ease of assembling microsphere patterns with the precision of projection lithography, rapid prototyping of patterned micro- and nanostructures can be achieved. The assembly of arrayed microsphere lenses is facilitated by encoding dot patterns of a UV-curable adhesive with high precision and ultra-small volume using E-jet printing. These microsphere-lens arrays can project photolithographically patterned micro- and nanostructures with high resolution. A projection-lithography system was constructed to achieve precise alignment between the focal plane of the microsphere lens and the photoresist plane. The results indicated that the accuracy of microsphere-lens projection lithography remained unaffected by the UV-curable adhesive, and the smallest feature size of the nanostructures was 850 nm. In future studies, the projection-lithography system can be further optimized. We will optimize the illumination system by adopting a collimated light source to reduce the impact of non-ideal light propagation and enhance resolution. We will refine the exposure dose experiments to determine the optimal conditions for achieving the highest resolution and pattern quality. This method of assembling microsphere templates enables the cost-effective fabrication of arbitrarily patterned templates, offering a straightforward and economical approach for generating microstructure arrays with submicrometer feature sizes. These patterned micro- and nanostructures may potentially be used in various functional devices, including planar meta-lenses, photonic crystals, and plasma sensors.
APPENDIX A: POSITION OF MICROSPHERE LENS ASSEMBLY ON UV-CURABLE ADHESIVE
As demonstrated in Fig. 6, using microspheres with a diameter of 10 μm as an example, the assembly behaviors of microspheres under four distinct conditions are observed. When the diameter of the UV-curable adhesive droplet exceeds the diameter of the microspheres (Case 1), a phenomenon occurs where two or more microspheres adhere to the same droplet. If the adhesive diameter is less than 10 μm but greater than 3 μm (Case 2), microspheres are likely to be adhered to the edge of the droplet, resulting in significant positional deviation. At 3 μm in diameter (Case 3), microspheres can be adhered to the designated location with smaller deviation. However, when the adhesive diameter is less than 3 μm (Case 4), although the microspheres can assemble at the preset position, they struggle to firmly adhere to the substrate due to lack of adhesive. To ensure the firmness and neatness of the microsphere arrays, subsequent experiments used UV-curable adhesives with a diameter of 30% of the microsphere diameter for the arrayed assembly process.
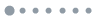
Figure 6.An example of microspheres with a diameter of 10 μm is used to illustrate the effect of different sizes of UV-curable adhesives on the assembled microspheres.
APPENDIX B: UV-CURABLE ADHESIVE SPIRAL ARRAYS AND ASSEMBLED MICROSPHERES
Figure 7 shows the scanning electron microscopy (SEM) image of the patterned spiral array template of UV-curable adhesive, as well as the corresponding SEM image of the patterned microsphere array assembled on the template.
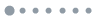
Figure 7.(a) Scanning electron microscopy (SEM) image of UV-curable-adhesive-patterned spiral array template. (b) SEM image of patterned microsphere arrays assembled on UV-curable adhesive spiral array template, corresponding to (a).
APPENDIX C: CHARACTERIZATION OF UV-CURABLE ADHESIVE PATTERNED ARRAY TEMPLATES
Figure 8 shows the optical images and local atomic force microscopy (AFM) images of the droplet arrays of UV-curable adhesive forming numerals, letters, and spiral patterns, along with the corresponding droplet profile curves.
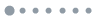
Figure 8.(a) Optical image of UV-curable-adhesive-patterned number array template. (b), (c) Atomic force microscopy (AFM) image of the UV-curable adhesive in (a) and the corresponding profile curves. (d) Optical image of UV-curable-adhesive-patterned letter array template. (e), (f) AFM image of the UV-curable adhesive in (d) and the corresponding profile curves. (g) Optical image of UV-curable-adhesive-patterned spiral array template. (h), (i) AFM image of the UV-curable adhesive in (g) and the corresponding profile curves.
APPENDIX D: CHARACTERIZATION OF ARRAYED MICROSPHERES WITH DIFFERENT SPACINGS
Figure 9 shows the SEM images of the arrayed microspheres with different spacings.
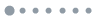
Figure 9.(a)–(c) SEM images of the assembled arrayed microspheres with different spacings.
APPENDIX E: CHARACTERIZATION OF UV-CURABLE ADHESIVE PATTERNED ARRAY TEMPLATES WITH DIFFERENT SPACINGS
Figure 10 shows UV-curable adhesive templates with different periods successfully achieved through the E-jet printing.
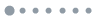
Figure 10.(a)–(c) SEM images of different periods of UV-curable adhesive templates printed by E-jet.
APPENDIX F: PATTERNED FLUORESCENT MICROSPHERE ARRAYS ASSEMBLED OVER A LARGE AREA
Figure 11 displays the optical images of “Puppy,” “Rose,” and “Beach” patterns composed of UV-curable adhesive droplet arrays, as well as the corresponding fluorescence images of green, blue, and red polystyrene (PS) fluorescent microspheres assembled into the respective patterns.
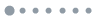
Figure 11.(a)–(c) Optical fluorescent images of patterned fluorescent microsphere arrays assembled over a large area. (d)–(f) Optical images of UV-curable adhesive templates for “Puppy,” “Rose,” and “Beach,” corresponding to the fluorescent images in (a)–(c). (g)–(l) Blue and red fluorescent images of fluorescent microsphere patterns.