1. Introduction
The mid-infrared (MIR) spectrum region from 3 to 50 µm[1] is interesting due to its wide possibilities for chemical analysis[2], thermal detection[3], object property study in infrared (IR) astronomy, and more[1–3]. The development of these areas is associated with the expansion of functional parameters and miniaturization, which implies the presence of MIR fiber optics. Promising MIR optical fibers are polycrystalline ones based on silver and thallium compounds. Silver halide fibers based on the at cover a wide transmission range of 2–20 µm and have low optical losses of up to 0.2 dB/m at a wavelength of 10.6 µm[4]. However, they are photosensitive, and the material itself is soft, which leads to scratches and a decrease in life cycle. Fibers based on thallium halides, for example, based on and , have higher strength characteristics, and their transmission range is 5–20 µm with losses of 0.5 dB/m at a wavelength of 10.6 µm[5]. Thallium halides are resistant to UV and ionizing radiation, so these properties are also characteristic of fibers[6]. However, due to the thallium halide single crystal lattice of the CsCl (Pm3m) type[6], fibers made of them are subject to grain recrystallization. It makes them extremely short-lived. In order to obtain single crystals with the advantages of both material groups, work was carried out on the synthesis of silver and thallium halide solid solutions[7]. As a result, the authors[7] obtained single crystals of the and systems, providing high photostability and resistance to -irradiation with doses of up to 800 kGy, increased hardness while maintaining flexibility sufficient for fiber production, and having a wide transmission range of 0.4–60.0 µm[7]. Current research is devoted to the development of polycrystalline fibers based on the silver and thallium halide single crystals, including the extrusion process modeling, experiments on testing extrusion modes, manufacturing fibers, and studying their properties.
2. Materials and Methods
2.1. Simulation of the Extrusion Process
The most efficient method for producing metal halide fibers is reverse extrusion[8]. To implement the process, it is necessary and sufficient to know the optimal preform heating temperature and extrusion speed, i.e., the plunger speed. Second, and also with controllable safety parameters, are the process pressure and mechanical loads on the tooling. Computer modeling was used to optimize the process of determining the extrusion modes for obtaining new fibers. It was carried out using the finite element method in Comsol Multiphysics 6.0 software[9]. The following single crystals were used as the materials: (only for the cladding), , ( system), , , and ( system).
2.2. Reverse fiber extrusion
For reverse extrusion, single crystals of the following composition were prepared: , , , , and . The technology of their synthesis is described in detail in Ref. [7]. Blanks with diameters of (for a 455 µm die), (for a 545 µm die), and a height of 7–11 mm were cut from them. They were loaded into a container together with a die, which set the fiber diameter on one side and a plug on the other side. The plunger and auxiliary elements were installed coaxially with the container and the blank. This entire construction was loaded into a tubular heater and installed in a hydraulic press. The blank was heated for 1 h to achieve its high flexibility. Then the extrusion speed was set on the press, which was maintained with an accuracy of 0.05 mm/min, and extrusion was performed. During the extrusion process, the fibers were placed in a fluoroplastic shell.
Sign up for Chinese Optics Letters TOC Get the latest issue of Advanced Photonics delivered right to you!Sign up now
2.3. Optical properties investigation
The transmission range was studied on an IR Fourier spectrometer (Prestige 21, Shimadzu) using a special attachment with off-axis parabolic mirrors for connecting IR fibers via SMA-905. The spectrum recording modes were as follows: the radiation source (globar, KBr beam splitter), the DLaTGS detector (1.46–30.0 µm, in the case of a KBr beam splitter), a resolution of , and the number of scans (). The spectra were recorded in the spectrometer background mode. The optical properties were investigated using the cut-back[11] method by comparing the energies in 1-m-long fibers and a 0.5-m-long section of the same fiber.
3. Results and Discussion
3.1. Extrusion modeling and results
The model in the Comsol Multiphysics 6.0 software[9] included three physics interfaces: laminar flow, heat transfer, and solid mechanics. The model geometry corresponded to the real tooling. The fiber at the output was specified as unclad or clad. This was necessary to confirm the possibility of obtaining IR fibers and experimental testing of modes that were primarily tested on unclad samples.
The model grid was combined: triangular for the fiber cross-section, distribution for the longitudinal section, and free tetrahedrons for the blank and tooling. The grid size was selected according to the recommendations of Comsol[9] and based on a preliminary analysis of the velocity parameter grid convergence. The velocity and temperature values were specified parametrically. The pressure and mechanical loads were calculated in the model based on the softening of the blank and the plunger speed. As a result, graphs of temperature and speed dependence along the axis “blank-fiber” were constructed, as shown in Fig. 1.
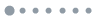
Figure 1.Modeling results for the unclad fiber based on the Ag0.97Tl0.03Cl0.26Br0.74 single crystal. Temperature distributions at (a) an extrusion speed of 0.1 mm/min and (b) an extrusion speed of 0.5 mm/min. (c) The change in speed in the cut “blank–die–fiber” at 170°C.
3.2. Unclad fiber manufacture
The selected extrusion modes were tested experimentally on unclad fibers. The extrusion modes obtained as a result of modeling and refined experimentally are shown in Table 1. A detailed scheme of the fiber production is shown in Fig. 2.
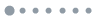
Figure 2.Block diagram of the infrared polycrystalline fiber production based on the single crystals of the metal halides.

Table 1. Fiber Extrusion Modes
Table 1. Fiber Extrusion Modes
Composition | Temperature modeling (°C) | Temperature experiment (°C) | Extrusion speed (m/s) |
---|
Ag0.97Tl0.03Cl0.26Br0.74 | 175 | 175 | 0.35 ± 0.05 | | 170 | 170 | 0.30 ± 0.05 | Ag0.07Tl0.93Cl0.71Br0.29 | 200 | 200 | 0.40 ± 0.05 | | 200 | 200 | 0.35 ± 0.05 | Ag0.97Tl0.03Cl0.24Br0.74I0.02 | 185 | 180 | 0.30 ± 0.05 | | 180 | 180 | 0.25 ± 0.05 | Ag0.94Tl0.06Cl0.24Br0.73I0.03 | 180 | 170 | 0.40 ± 0.05 | | 180 | 180 | 0.30 ± 0.05 | Ag0.91Tl0.09Cl0.23Br0.72I0.05 | 180 | 180 | 0.40 ± 0.05 | | 180 | 180 | 0.30 ± 0.05 |
|
As a result, fibers up to 3.5 m long with diameters of 455 and 525 µm were obtained. The fibers were terminated with SMA-905 connectors. Also, short sections (20 cm) were cut from each fiber to analyze the susceptibility to recrystallization by observing the side surface structure stability using an Olympus BX 51 microscope at magnification. Among the obtained samples, grain recrystallization was observed only for the fiber based on the single crystal. The grain coarsening process occurred rapidly and was visually observed for several hours after fabrication, which led to the destruction of the fiber and the impossibility of assessing its functional properties. Due to grain recrystallization, the fibers had high losses. This is reflected in the energy level, which does not reach 0.05 energy units (Fig. 3). The reason for the recrystallization occurrence in this composition of fibers is that the CsCl (Pm3m) crystal lattice is most stable at temperatures above 150°C–175°C. At lower temperatures, it gradually recrystallizes to Cmcm, and this process is accelerated due to mechanical action (extrusion)[7]. For recrystallization, grain coarsening occurs, which, in the case of the fibers, leads to increased brittleness and its destruction. As a result of monitoring the other fibers' surface for 12 to 18 months, their structural stability was found. Thus, for other fibers, recrystallization was not observed, which is due to their material lattice type, NaCl (Fm3m)[7]. Nevertheless, according to the experimental results, some samples need to change extrusion modes. Single crystals of and showed the need to reduce the temperature to 180°C and 170°C, respectively, owing to the high blank flexibility, which leads to an increase in the rate and unevenness of material flow. This, in turn, disrupts the fiber structure and reduces its optical characteristics. The process pressure with decreasing temperature was maintained in the range of 2.9–3.9 MPa, which is significantly lower than the critical value of 70 MPa. For the other fibers, the extrusion modes corresponded to the modeling results. All fibers were placed in a fluoroplastic shell, and the ends were cut with a special glass cutter and fixed up in SMA-905 connectors.
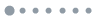
Figure 3.Transmission spectra of the 1-m-long optical fibers.
3.3. Optical properties of unclad fibers
The spectra obtained for the 1-m-long samples are shown in Fig. 3. The transmission spectra were estimated using the two-tangent method[10], when the extreme wavelength value was taken as the transmission limit. Thus, the fiber spectra cover the range of 4–25 µm in the case of the composition and 3.5–28 µm in the case of the samples based on the single crystals of the system. At the same time, with an increase in the content of thallium iodide, the spectrum shifts to the longer wavelengths from 3.5 to 26.5 µm for the composition to 4–28 µm in the case of the composition. These values are the maximum for fiber optics to date. It should be noted that all spectra do not have their own absorption windows, thus, the fibers operate effectively in their entire transmission range.
For all fibers, the intrinsic optical losses were estimated. The loss spectra of the manufactured fibers are shown in Fig. 4. The minimum losses in the fibers reach at a wavelength range of 11–17 µm. These values are comparable with known fibers based on silver halides of the AgCl-AgBr (up to )[4] and AgCl-AgBr-AgI ()[5,8] systems. The results obtained confirm the adequacy of the selected extrusion modes. This follows from both the absence of recrystallization and the presence of a wide transmission range and relatively low optical losses.
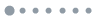
Figure 4.Fibers' intrinsic optical losses.
3.4. Unclad fiber manufacture and its properties
Since it was possible to obtain optical fibers with competitive properties from single crystals of the composition , , , and , some of these materials were used to obtain clad fibers. To ensure the required difference in the refractive indices “core-cladding” () when fulfilling the relation , and single crystals with refractive indices (n) of 2.134 [7] and 2.167[7] at a wavelength of 10.6 µm were used as the fibers’ core. A single crystal of with was used for the cladding[7]. The blanks for the cladding were machined from a single crystal in the form of a hollow cylinder and subjected to chemical treatment in hydrochloric and hydrobromic acids in order to remove contaminants without destroying the surface (e.g., due to chemical etching).
The blanks for the cladding had an external diameter of and an internal one of . The blanks for the core were made in the form of a cylinder with a diameter of in a similar way. Then, the core was placed in the cladding blank by interference fit. The height of both cylinders was 12 mm. A thin disk with a thickness of and a diameter corresponding to the cladding cylinder [] was additionally placed at one end of the blank. The disk is designed to increase the viscous friction between the core and the cladding, which ensures a higher quality of the core-cladding boundary and the preservation of their diameter ratios. The resulting construction was loaded into a container together with a die on one side and a plug on the other side. All other hydraulic press tooling elements were installed similarly to the case of the uncladded fibers. Since the dimension of the blanks exceeded the usual parameters for the uncladded fibers blank, a larger die was used in order to reduce the constriction coefficient (its internal diameter was 1120 µm). The positive effect of using such a die also consists of reducing the press and, consequently, reducing the load on the tooling.
The extrusion modes for obtaining the cladding fiber structures were refined. The blank was heated for 1.5 h, with the temperature increased to 200°C, and the extrusion speed was . Such modes ensured uniform heating of the entire blank and high flexibility of both the core and the cladding. Reduced speed values are necessary to obtain a high-quality, core-cladding interface. Taking into account the above-described features, reverse extrusion[4,8] was implemented. The process parameters are shown in Table 2. The speed in Table 2 is the parameter when the fiber flows out of the die. However, the dependence of the speed on time is similar to the case of the unclad fiber extrusion, where this parameter is higher in the first process minutes. This is due to the pressing of both the blank to the size of the container and the core to the size of the hollow cylinder-cladding. The pressure parameter throughout the entire process did not exceed 3.9 MPa, which ensured extrusion safety and uniformity. Table 2 shows the average pressure value during extrusion.

Table 2. Cladding Fiber Extrusion Modes
Table 2. Cladding Fiber Extrusion Modes
Core composition | Temperature experiment (°C) | Extrusion speed (m/s) | Average pressure (MPa) |
---|
Ag0.97Tl0.03Cl0.26Br0.74 | 200 | 0.22 ± 0.04 | 3.2 | Ag0.94Tl0.06Cl0.24Br0.73I0.03 | 200 | 0.20 ± 0.04 | 3.2 |
|
As the extrusion result shows, fibers of 1.7–2.0 m in length were obtained, the cladding diameter was , and the core one was . The part of the fiber that extruded from the disc was cut off. The fibers were placed in a fluoroplastic shell and terminated with SMA 905 connectors. The end preparation was carried out similarly to the unclad fibers.
The spectra were recorded using similar modes of the IR Prestige 21 spectrometer. The losses were estimated using the cut-back[11] method by comparing the energies at the outputs of 1 and 0.5 m long optical fibers. As shown in Fig. 5, the transmission ranges covered 3.5–25 µm for the fiber with the core and 4–27 µm in the case of the core. The minimum optical losses were at and at , respectively. The obtained optical transmittance values significantly exceed the transparency range of the only commercially available polycrystalline cladding fibers based on AgCl-AgBr single crystals[12] (3.5–27 µm compared to 2–20 µm)[4,12]. Optical losses also showed similar or lower values (0.2–0.3 dB/m at for fibers based on AgCl-AgBr)[12]. The low level of losses and the wide range of spectral transmittance confirm the high quality of the core-cladding interface and the adequacy of the extrusion modes.
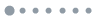
Figure 5.Transmission and optical loss spectra for clad optical fibers.
5. Conclusion
The unclad and clad fiber extrusion modes obtained by modeling and experimental research made it possible to form a set of temperature-speed parameters for obtaining new optical fibers based on the single crystals of the and systems. The fibers' optical properties showed impressive characteristics. Thus, the transmission range covered 3.5–28.0 µm (depending on the composition) without absorption windows, which significantly exceeds the transparency of all existing fiber types. Optical losses were 0.2–0.5 dB/m in the MIR, which is comparable to existing commercially available fibers. The fiber materials are photo- and radiation-resistant. This ensures the fibers' durability and the possibility of using them without protective cladding and in conditions of high-intense ionizing radiation. Thus, the technologies we proposed for producing fibers based on silver and thallium halide single crystals made it possible to manufacture new fiber-optic elements of various structures with competitive optical characteristics.