1. Introduction
Laser welding finds extensive application in the manufacture of power batteries for electric vehicles, owing to its advantages of a reduced heat-affected zone and minimal targeted deformation[1]. Laser welding can be classified into heat-conduction welding and deep-penetration welding based on laser power density. Deep-penetration welding is distinguished by the occurrence of vaporization and the formation of a keyhole in the melt pool. The threshold for deep-penetration welding can be expressed as the ratio of the laser power to spot diameter (). Typical thresholds are 1.5 kW/mm for steel welding[2] and 4 kW/mm for aluminum (Al) welding[3].
Accurate measurement of keyhole depth is important for quality assurance and control in laser welding. Numerous approaches have been proposed and explored for measuring the keyhole depth using spectrometers, photodiodes, cameras, and optical coherence tomography (OCT)[4–7]. Among these techniques, OCT, utilizing low-coherence interferometry[8,9], offers a direct and precise measurement of keyhole depth through the coupling of the measuring and processing beams. Figure 1 depicts the schematic of the OCT measurement. Light from a superluminescent diode (SLD) is divided by a coupler into the measuring and reference beams, which are backreflected off the keyhole bottom and the mirror, respectively. The reflected beams are combined and analyzed by a spectrometer. The frequency of the interference spectrogram is determined by the length difference between the measuring and reference paths.
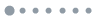
Figure 1.Schematic of the keyhole monitoring system.
The measuring beam is precisely aligned with the processing beams to hit the keyhole bottom. Nonetheless, in high-speed welding, the keyhole lags behind the processing beam, causing the measuring beam to hit the front keyhole wall[10], as shown in Fig. 1. Dorsch et al.[11] observed a reduction in the quantity of OCT data with increasing welding speed. Due to the impact of keyhole lag on OCT measurement accuracy, monitoring keyhole morphology and conducting a quantitative analysis of the keyhole lag have become crucial.
Sign up for Chinese Optics Letters TOC Get the latest issue of Advanced Photonics delivered right to you!Sign up now
Conventional methods for monitoring keyhole morphology include coaxial observation[12], the sandwich technique[13], and X-ray imaging[14–16]. Kim et al.[17] observed the keyhole surface by coaxial videography. Zhang et al.[18] captured the longitudinal keyhole wall by incorporating a transparent material into a sandwich specimen for imaging purposes. Miyagi et al.[19] captured the keyhole shape in the longitudinal view using X-ray imaging, although the images exhibited low resolution. Cunningham et al.[20] employed the synchrotron X-ray method to observe the keyhole shape with high spatiotemporal resolution. While these approaches may be successful in certain cases, they lack the capability for three-dimensional (3D) keyhole morphology monitoring. Utilizing a scanner to deflect the measuring beam, OCT allows for the capture of 3D keyhole morphology, as illustrated in Fig. 1. The measuring beam is deflected with a predefined width using a triangular wave, and OCT data are acquired along the welding length. Patterson et al.[21] employed a commercial OCT system to map the keyhole shape, revealing distinct differences between stainless steel and Ti-6Al-4 V.
The objective of this study was to explore the keyhole morphology monitoring in laser welding using OCT. A keyhole monitoring system was developed to capture the keyhole morphology of stainless steel and Al alloy at various welding speeds. The correlation between OCT data and seam surface quality, as well as weld cross section, was examined. Additionally, the quantification of keyhole lag was performed based on the longitudinal view of the keyhole morphology.
2. Experimental Setup
Figure 2 depicts the experimental setup of the keyhole monitoring system. The process laser employed was a 4 kW multimode fiber laser with a wavelength of 1070 nm and a fiber core diameter of 100 µm. In the welding head, the collimation lens and focusing lens had focal lengths of 100 and 200 mm, respectively, resulting in a focus diameter of 200 µm. The OCT light source utilized was a 40 mW SLD with a central wavelength of 850 nm and a bandwidth of 45 nm. The spectrometer possessed a maximum measuring range of 3 mm and was operated at a sampling rate of 80 kHz. The scanner employed was a galvanometer with a maximum scanning rate of 500 Hz. The OCT system utilized a fiber with a core diameter of 5 µm and a collimation lens with a focal length of 36 mm. With the 200 mm focal length focusing lens, the focus diameter of the OCT measuring beam was 27 µm.
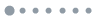
Figure 2.Experimental setup of the keyhole monitoring system.
Bead-on-plate welds were performed on 304 stainless steel and 6061 Al alloy. The chemical compositions are presented in Table 1. To calibrate the processing beam center, a low-power spot weld was made on 304 stainless steel and scanned using OCT. The deepest point of the spot weld was set as the center of the processing beam. The calibration process was repeated twice more to enhance positioning accuracy.

Table 1. Compositions of 304 Stainless Steel and 6061 Al Alloy
Table 1. Compositions of 304 Stainless Steel and 6061 Al Alloy
Material | Chemical composition |
---|
304 | Cr | Ni | Mn | Si | B | S | C | P | Fe | Mass fraction (%) | 18.18 | 8.48 | 1.75 | 0.57 | 0.10 | 0.03 | 0.05 | 0.03 | Bal. | 6061 | Mg | Fe | Cu | Mn | Si | Zn | Cr | Ni | Al | Mass fraction (%) | 1.00 | 0.70 | 0.28 | 0.15 | 0.60 | 0.25 | 0.20 | 0.05 | Bal. |
|
Table 2 shows the process parameters. For 304 stainless steel and 6061 Al alloy, the values were 3 and 6 kW/mm, respectively, both surpassing the thresholds for deep-penetration welding. The welding speeds were 10, 25, 50, and 100 mm/s. The OCT measuring beam, smaller than the processing beam, was deflected by the scanner to scan the keyhole area. The scan size was with a scanning rate of 200 Hz in the -direction and 1 Hz in the -direction. Data collection was maximized to data points with an 80 kHz sampling rate, yielding 364 points/mm. OCT data were collected in real time and reconstructed to generate the keyhole morphology. It should be noted that the keyhole morphology represents a compilation of OCT measurement points throughout the entire welding process and does not correspond to a single measurement point.

Table 2. Process Parameters
Table 2. Process Parameters
Material | Power (W) | Defocus (mm) | P/d (kW/mm) | Speed (mm/s) | Scan size (μm × μm) | Data points |
---|
304 | 600 | 0 | 3 | 10, 25, 50, 100 | 550 × 550 | 200 × 200 | 6061 | 1200 | 0 | 6 | 10, 25, 50, 100 | 550 × 550 | 200 × 200 |
|
3. Results and Discussion
The keyhole morphology for 304 stainless steel and 6061 Al alloy at various welding speeds was analyzed. Figures 3(a)–3(d) show the keyhole morphology for 304 stainless steel at welding speeds of 10, 25, 50, and 100 mm/s. Figures 3(e)–3(h) display the keyhole morphology for 6061 Al alloy at welding speeds of 10, 25, 50, and 100 mm/s. The color scale indicates the keyhole depth. The keyhole morphology data comprises melt pool surface data, keyhole wall data, and keyhole bottom data. The melt pool surface data are around 0 mm in the -direction. The keyhole wall data and the keyhole bottom data are in the negative -direction. Clearly, at the investigated parameters, the OCT system identified a melt pool depression, signifying the vaporization and the formation of a keyhole in the melt pool. The keyhole depth was reduced with the increased welding speed for both materials because the laser energy absorbed by the materials was inversely proportional to the welding speed. It is evident that the keyhole morphology data of Al alloy is fluctuating compared to stainless steel. This phenomenon is attributed to keyhole instability during the welding process. The Al alloy suffers from high reflectivity, resulting in the generation of an unstable keyhole.
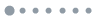
Figure 3.Keyhole morphology on (a)–(d) 304 stainless steel and (e)–(h) 6061 Al alloy. The welding speeds are (a), (e) 10, (b), (f) 25, (c), (g) 50, and (d), (h) 100 mm/s, respectively.
To investigate the relationship between the keyhole morphology and the weld properties, the seam surface macrograph and the weld cross section micrograph for 304 stainless steel and 6061 Al alloy are shown in Figs. 4(a) and 4(b). It can be seen that the seam surface quality is consistent with the melt pool surface data, as shown in Figs. 3(c) and 3(g). In comparison to stainless steel, the seam surface of Al alloy is irregular, and the melt pool surface data fluctuates. According to Ref. [22], employing an adjustable ring mode laser can enhance the keyhole stability of Al alloy, resulting in concentrated OCT data and improved surface quality. The weld depth-to-width ratio greater than 1 is used to distinguish the occurrence of vaporization and the formation of a keyhole in the melt pool[3]. This is confirmed by the keyhole morphology and the weld cross section for both materials.
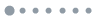
Figure 4.Seam surface macrograph and weld cross-section micrograph of (a) 304 stainless steel and (b) 6061 Al alloy.
Keyhole morphology analysis was extended by projecting the OCT data into different orientations. Figures 5(a) and 5(b) show the surface views of the keyhole morphology for 304 stainless steel at welding speeds of 10 and 100 mm/s. Figures 5(c) and 5(d) display the surface views of the keyhole morphology for 6061 Al alloy at welding speeds of 10 and 100 mm/s. The processing beam center is indicated by crosshairs, and its diameter is denoted by a red circle. Regions with lost signal, due to the absence of keyhole data in some OCT measurements, are depicted in white. This signal loss is caused by the measurement sensitivity of the OCT technique. An increase in welding speed resulted in the keyhole center shifting behind the processing beam center for both materials.
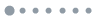
Figure 5.Surface views of keyhole morphology on 304 stainless steel at (a) 10 and (b) 100 mm/s; 6061 Al alloy at (c) 10 and (d) 100 mm/s. The processing beam center is marked by the crosshairs, and the processing beam diameter is represented by the red circle. The white regions represent no signal.
Figures 6(a)–6(d) illustrate the longitudinal views of the keyhole morphology for 304 stainless steel at welding speeds of 10, 25, 50, and 100 mm/s. Figures 6(e)–6(h) depict the longitudinal views of the keyhole morphology for 6061 Al alloy at welding speeds of 10, 25, 50, and 100 mm/s. The welding was in the positive -direction. The processing beam center is indicated by a black line, and its diameter is denoted by red dotted lines. It can be seen that a high aspect ratio weld occurs at a welding speed of 10 mm/s. Further increasing the welding speed to 100 mm/s becomes a low aspect ratio weld, but a keyhole remains detectable. There was a reduction in the detected keyhole depth and a lag in the keyhole center as the welding speed increased from 10 to 100 mm/s. The keyhole lag is more apparent in the longitudinal view compared to the surface view. The longitudinal view of the keyhole morphology for stainless steel is adequately matched with the weld cross section, as shown in Fig. 4. For Al alloy, the similarity between the keyhole morphology and the weld cross section is weak due to the excessive noise in the OCT data. The noise points lying around the keyhole have either to be attributed to invalid measurement caused by keyhole fluctuation or various sources of OCT noise, including autocorrelation, speckle, and detector noise[23–25].
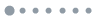
Figure 6.Longitudinal views of keyhole morphology on (a)–(d) 304 stainless steel and (e)–(h) 6061 Al alloy. The welding speeds are (a), (e) 10, (b), (f) 25, (c), (g) 50, and (d), (h) 100 mm/s, respectively. The processing beam center is marked by the black lines, and the processing beam diameter is represented by the red dotted lines. The welding direction is from left to right.
The keyhole lag was quantified as the difference between the central location of the keyhole and the center of the processing beam. Figure 7 illustrates the keyhole lag for 304 stainless steel and 6061 Al alloy at varying welding speeds. The keyhole lag exhibited an increase in welding speeds for both materials. At welding speeds below 25 mm/s, the keyhole center preceded the processing beam center, and the keyhole lag in stainless steel was lower than that in Al alloy. At welding speeds exceeding 25 mm/s, the keyhole center lagged behind the processing beam center, and the keyhole lag in stainless steel was higher than that in Al alloy. The material-dependent keyhole lag occurs during high aspect ratio welding at low welding speeds. Once the welding speed is high enough to become a low aspect ratio weld, the keyhole lag is material-independent. It should be noted that a minor amount of keyhole lag deviation can result from the fact that the OCT data of Al alloy are more scattered than those of stainless steel, as shown in Fig. 6.
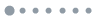
Figure 7.Keyhole lag for 304 stainless steel and 6061 Al alloy with different welding speeds.
4. Conclusion
This work investigated the keyhole morphology monitoring using OCT. The examination revealed a melt pool depression at the investigated parameters, signifying the occurrence of vaporization and the formation of a keyhole in the melt pool. Subsequently, the correlation between OCT data and seam surface quality, as well as weld cross section, was investigated. The results indicated that Al alloy exhibited irregular seam surface and fluctuating keyhole morphology. Furthermore, the keyhole lag was quantitatively analyzed based on the longitudinal views of the keyhole morphology. The keyhole lagged behind the processing beam at high welding speeds. The keyhole lag demonstrated an increase in welding speed and was consistent for both stainless steel and Al alloy.
Future research will focus on compensating for the keyhole lag to enhance OCT measurement accuracy and revealing the relationship between keyhole changes and weld properties.