1. INTRODUCTION
Optical trapping has emerged as a pivotal technology across the fields of biology, catalysis, spectroscopy, and medical science due to its non-invasive, contactless nature, high resolution, and ability to manipulate weak forces [1–8]. Conventionally, optical tweezers utilize the gradient force generated by the interaction of a focused laser beam with dielectric particles to trap and manipulate them in three dimensions [9–13]. While this technique has found widespread applications in various fields, its utility for manipulating metallic particles has been limited due to the high reflectivity of light by metallic particles. In particular, particles comparable to or greater than the free space optical wavelength, with conventional optical tweezers, encounter challenges because the scattering forces are stronger than the gradient forces [14,15]. However, manipulation of metallic particles holds immense significance in numerous fields, ranging from nanotechnology to biophysics, such as site-specific surface-enhanced Raman scattering (SERS) technology [16,17].
Plasmonic tweezers have emerged as a promising alternative for metallic particle manipulation [18–20]. The surface plasmon polariton (SPP) is formed through the cooperative coupling of photons and electrons within metallic nanostructures, enabling the confinement of light into deep subwavelength scale. Such confinement significantly amplifies field intensity and facilitates the enhancement of interactions between light and matter and optical forces. Through meticulous patterning of these nanostructures, including gaps [9,21–23], apertures [24,25], Archimedes spirals [26], bowtie structure [27,28], nano-rings [29,30], and plasmonic meta-surfaces [31], plasmonic fields can be focused, redirected, and precisely manipulated, so that they can exhibit sufficient attractive optical forces to trap both dielectric and metallic particles. However, dynamic plasmonic optical tweezers modulation for metal particles is typically achieved through the introduction of mechanical components for adjustment, such as a moving sample stage [15]. The mechanical adjustments not only increase the complexity and cost of the system but also introduce instability to the plasmonic tweezers system, affecting the trapping precision of metallic particles. Xie et al. [32] introduced and validated a method for trapping and manipulating particles in holographic optical surface-wave tweezers. This was achieved by modulating the incident laser beam into two parts: a trapping beam and an expulsing beam. The bulky high numerical aperture objective lens and stage movement are required. However, currently, dynamically manipulating metallic particles by plasmonic tweezers without mechanical adjustment remains a significant challenge.
To overcome the limitation, in this paper, we propose a new approach utilizing dynamic optical tweezers with tunable plasmonic fields for the manipulation of metallic particles. A modulated circularly polarized light beam is directed to a layer of gold film with nano-concentric-ring slits to excite surface plasmon waves, and the plasmonic fields are dynamically tailored by loading well-designed holograms onto a spatial light modulator (SLM). We employed a three-dimensional (3D) finite-difference time-domain (FDTD) approach for theoretical simulations and calculated the optical forces on a gold particle using the Maxwell stress tensor (MST) method. The holograms were generated by a custom-designed Gerchberg–Saxton (GS) phase retrieval algorithm. The metallic particles could be dynamically manipulated without any mechanical adjustments, only by changing the holograms loaded onto the SLM. Specifically, a gold particle can be dragged by the hotspot for more than 10 μm, indicating that the optical force is sufficient for most manipulation. Unlike traditional approaches, the hotspots of surface plasmons are not restricted to a predefined nanostructure locally but can be precisely relocated within a specified region of interest. The proposed plasmonic tweezers hold the advantages of simple structure without mechanical components. This technique of dynamic plasmonic tweezers may open wider applications for the metallic particle manipulation in SERS, biosensing, super-resolved detection, and nanoparticle assembly.
Sign up for Photonics Research TOC Get the latest issue of Advanced Photonics delivered right to you!Sign up now
2. RESULTS AND DISCUSSION
To dynamically control the hotspots of SPPs fields, a laser beam with a specially designed radial phase pattern was projected onto a gold film etched with a concentric ring coupler. As shown in Fig. 1, these concentric rings function as an in-plane coupler, efficiently converging SPP waves to create a targeted SPP field. A number of multiple excitation rings significantly enhance the intensity of SPP fields compared with a single ring coupler [33,34]. The thickness of gold film is 100 nm, the linewidth of ring slits is 240 nm, and the innermost radius of the ring slit is 10 μm. We employed a custom-designed GS algorithm [35] to generate various holograms (loaded onto an electronically addressed SLM), integrating a two-dimensional in-plane Fourier transform (FT) operator (concentric ring coupler) to determine the initial conditions for generating SPPs fields with different focal positions [36].
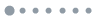
Figure 1.Schematic diagram of plasmonic tweezers. The phase of circularly polarized light is modulated by the hologram loaded onto the SLM. A 2D Fourier relationship can be delineated between the complex amplitude along an annular-rings coupler of a converging surface wave and the out-of-plane component of the SPP field. The red arrow indicates the movement of the hotspot, and the gold particles move accordingly.
To illustrate the dynamic control capabilities of our method over the optical field, target patterns with hotspots of SPPs fields in different positions are shown in Figs. 2(a1)–2(a3). The phase distributions in the excitation rings coupler and the generated SPP fields are related to each other with Fourier transform [36]. Figure 2(b) shows the analytical intensity distribution information for various target patterns [shown in Figs. 2(a1)–2(a3)] calculated directly by the custom-designed FT algorithm. In this section, a modified GS algorithm was employed, which iteratively modulates the amplitude and phase of the incident light to closely match the target pattern. As shown in Figs. 2(c) and 2(d), the 3D FDTD method was employed to simulate the amplitude and phase distribution of SPPs fields for different targets, respectively. Figures 2(e1)–2(e3) depict the modulated phase distributions of different incident beams, which generate SPP hotspots corresponding to different targets [shown in Figs. 2(a1)–2(a3)]. In the FDTD simulations, the wavelength of incident circularly-polarized light is 1064 nm, the thickness of gold film is set as 100 nm, and the diameter of the innermost ring is 20 μm. SPP waves can be excited by transverse-magnetic (TM) polarized light at a dielectric/metal interface. A radially polarized beam (RPB) is particularly effective for exciting SPP waves due to its axially symmetric TM polarization, but it suffers drawbacks in the requirement of additional optical components and the difficulty for alignment with holograms. In our experiments, we use a left-handed circularly (LHC) polarized beam and a circularly symmetric coupler to excite SPP waves. The LHC polarized beam can be decomposed into radially polarized and azimuthally polarized components, both exhibiting a spiral phase wavefront. The azimuthally polarized component, characterized as a TE mode concerning the ring groove, can be ignored. The spiral phase () inherent in the radially polarized component can be canceled out by introducing an additional spiral phase. Conversely, a circularly polarized beam with opposite chirality will inherit a spiral phase of . Hence, the supplementary spiral phase integrated into the SLM must also possess the opposite chirality. The refractive indices were set to 1.515 and 1.32 for glass and water, respectively, and the refractive index of gold was at 1064 nm [37]. The results of these theoretical simulations align well with the anticipated distributions of the SPPs fields.
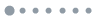
Figure 2.Analytical and numerical simulation results for various target patterns. (a) Target patterns with hotspots in different positions. (b) Normalized two-dimensional field intensity distributions corresponding to the different target patterns calculated directly by the custom-refined FT algorithm; (b1)–(b3) are the corresponding two-dimensional field distributions of (a1)–(a3), accordingly. (c), (d) Full-wave 3D-FDTD simulation results of normalized intensity and phase distributions of numerical simulation results for the different target patterns; (c1)–(c3) are the intensity distributions of numerical simulation results matched with target patterns (a1)–(a3), accordingly. (d1)–(d3) correspond to the phase distributions of numerical simulation matched with target patterns (a1)–(a3), accordingly. (e1)–(e3) Phase distributions of the incident beam tailored with different target patterns (a1)–(a3), accordingly. The scale bar is 4 μm.
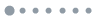
Figure 3.(a) Intensity distribution of electric field of a single dot hotspot (background). The blue arrows denote the energy flow distributions (Poynting vector) at each position. (b) Optical force (represented by the blue curve) exerted on a gold particle (diameter of 1 μm, located 50 nm above the surface of gold film) and optical potential well (represented by the red curve) along the axis. The black dot represents the experimental results. The horizontal axis measures the distance from the center of the gold particle to the central peak of the SPP field. The data for both the optical force and the potential well were smoothed using the piecewise cubic Hermite interpolating polynomial (PCHIP) method. (c) The lower part of the figure shows the magnitude of the optical force exerted on the gold particle at various locations, while the upper part of the figure displays the distribution profile of the corresponding potential well in the plane. The scale bar is 2 μm. The incident power is 10 mW.
Figure 3(a) depicts the electric field distribution (background) of a single dot pattern located 50 nm above the gold film, revealing a highly intense hotspot at the center. The blue arrows indicate the direction of energy flow (Poynting vector) at each location, converging towards the center, which clearly indicates that the energy flow is directed towards the hotspot capable of trapping particles. Given that the incident light is circularly polarized, the energy flow is annularly uniformly distributed in all directions. In Fig. 3(b), the blue curve represents the attractive force (, vertical force) with injected optical power of 10 mW exerted on a gold particle with diameter of 1 μm along the x axis. Additionally, the optical potential well generated by the optical force is represented by the red curve in Fig. 3(b). This data was interpolated using the piecewise cubic Hermite interpolating polynomial (PCHIP) method. The potential well is calculated as [38] with all values being negative, signifying a trapping potential with an attractive force. The depth of the trapping potential well is estimated to be approximately (where is the Boltzmann constant and is the ambient temperature of about 300 K), which was sufficient to overcome the Brownian motion and meet the criteria for stable optical trapping. In the vertical plane, there is indeed an attractive force that pulls particles towards the gold film. However, this force weakens quickly as the gap size increases, due to a rapid decline in the intensity of the SPP field along the vertical direction from the interface [39].
To delve deeper into the study of optical force and potential wells, the lower pattern of Fig. 3(c) displays the 2D optical force, while the upper one shows the corresponding 3D profile of the potential well. The 2D optical force pattern indicates that the magnitude of the attractive (negative) optical force peaks at the center of the optical field. This distribution pattern of 3D potential distribution indicates a deep optical potential well at the center of the optical field, providing an efficient mechanism for particle trapping.
Figure 4(a) depicts the experimental setup of our plasmonic tweezering system. The incident laser beam with a wavelength of 1064 nm (FL-1064-CW, 5 W, Changchun New Industry Optoelectronics Technology Co., Ltd.) was expanded via a telescopic system (comprising L1 and L2) to cover the effective area of the spatial light modulator (SN6086, E19X12-500-1200, Meadowlark Optics). A polarizer (P) transformed the polarization state of the incident light into linearly polarized (LP), and a half-wave plate (HP) adjusted the polarization angle to align with the liquid crystals’ long axis in the SLM, prior to its interaction with the SLM. As shown in the inset of Fig. 4(a), the holograms imprinted on the SLM were generated through iterative application of a custom-designed phase map using the GS phase retrieval algorithm. This phase map was subsequently integrated with a diffractive blazed grating featuring a ring-shaped aperture, designed to diffract the light into different diffraction orders. The ring-shaped aperture is assigned to significantly reduce the influence of both transmitted light and diffracted zeroth-order speckles (direct current component of the incident beam). After blocking the undesired diffraction orders, the first order of the diffractive light imprinted with the tailored information is employed for further processing. Subsequently, a quarter-wave plate (QP) was employed to convert the polarization state of light to circular polarization (CP). The laser beam was then focused onto the sample using a optical objective lens (OBJ1) with numerical aperture (NA) of 0.8. Given that the gold film was situated beneath the focal plane of the objective lens, the stimulated SPPs advanced towards the designated area, engaging in constructive interference, which culminated in a homogeneous intensity pattern across the Au film’s surface. A fraction of the incident light, reflected by the film into OBJ1, facilitated the observation of the laser-sample alignment using a charge coupled device (CCD1). To align the incident beam and the excitation ring coupler, we load a hologram of a fork grating onto the SLM to generate a vortex beam and then align the vortex beam center with the coupler center through observation with CCD1. To achieve dynamic manipulation without any mechanical movement, after the alignment, we replace the hologram with tailored holograms to generate different desired hotspots. This allows us to manipulate particles without adjusting the stage, ensuring that the phase hologram ring aligns well with the excitation coupler on the gold film.
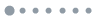
Figure 4.Schematic diagram of the experimental setup. (a) Experimental configuration of the plasmonic tweezers system. Inset: the hologram loaded on the spatial light modulator (SLM) consists of a modulated phase pattern and a blazed grating with a ring-shaped aperture pattern. Abbreviations: L1 and L2, lens; P, polarizer; HP, half-wave plate; SLM, spatial light modulator; QP, quarter-wave plate; OBJ, objective lens; BS, beam splitter; CCD, charge coupled device. (b) Scanning electron microscopy image of the nanostructure. The innermost ring has a radius of 10 μm, the linewidth of each ring is 240 nm, and the spacing between the two adjacent ring slits is 786 nm (). The scale bar is 4 μm.
To monitor the manipulation process, a white-light source illuminated the samples from above over BS2. The laser and the image of manipulation progress were reflected by the gold film and then collected by the second objective lens (OBJ2, 60) with an NA of 0.9. The laser was filtered through a band-pass filter to avoid the influence on observation before the manipulation progress was imaged by a second CCD camera (CCD2). Figure 4(b) shows the scanning electron microscopy (SEM) pattern of our sample. A 100 nm gold film was sputtered onto a quartz substrate by magnetron sputtering (NANO 36, Kurt J. Lesker Company), and the ring-slit structures were fabricated using focused ion beam (FIB) milling (Helios 5 UC Dual Beam FIB-SEM system, Thermo Fisher Scientific) featuring a linewidth of 240 nm, a spacing of 786 nm (equal to the wavelength of excited SPPs, ) between the two ring-silt, and an innermost radius of 10 μm.
In the experiment, circularly polarized light with the phase distribution determined by the SLM was directed perpendicularly onto five concentric circles formed by etching into a 100 nm gold film to excite surface plasmons, with each excitation ring spaced at 0.786 μm (equal to the wavelength of excited SPPs) to enhance the hotspot intensity. Alterations in the SPP field hotspots within the concentric rings are accomplished by changing holograms generated by the GS algorithm, which are designed for specific target patterns. The dynamic behavior of gold particles (ranging in diameter from 0.8 to 1.5 μm) was investigated. The sample is prepared as follows: a small quantity of gold particle (0.8–1.5 μm, Alfa Aesar, Inc.) powder is first transferred to a test tube using a pipette, then 5 mL of pure water is added, and the sample is sonicated for 15 min in an ultrasonic cleaner. Figure 5 presents the sequential images extracted from charge-coupled device (CCD) video (see Visualization 1, Visualization 2, and Visualization 3), illustrating the plasmonic tweezer’s ability to attract nearby Au particles. As the hotspot relocated in response to hologram adjustments, the particles move accordingly, dynamically creating specific trajectories, such as “S”, “Z”, and “U” shapes. Specifically, the gold particle moved according to the displacement of the hotspot over a large distance (more than 10 μm), indicating that the optical force generated by SPPs is sufficient for any manipulation. These observations are in strong agreement with simulations (as depicted in Fig. 2) and confirm the significant role of the attractive (negative) force in particle trapping. Therefore, this technique holds promise for applications in micro–nano fabrication and for the enhancement of Raman signals at precise locations.
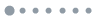
Figure 5.Experimental demonstration of plasmonic tweezers. (a) Sequential images show the capture and manipulation of gold particles (diameter of 0.8–1.5 μm) forming an “S” shape. (b) Sequential images depict the capture and manipulation of gold particles resulting in a “Z” shape. (c) Sequential images illustrate the capture and manipulation of gold particles achieving a “U” shape. The blue dashed line represents the trajectory of the particle motion. The sequence of images progresses from left to right, with a time interval of 1 s between images. The incident laser power is 10 mW. The scale bar is 4 μm.
3. CONCLUSION
In summary, this paper proposed and demonstrated a novel plasmonic tweezers system for the dynamic manipulation of gold particles by tailoring tunable plasmonic fields. Our system employed microscale concentric circular structures as SPP excitation rings; the employment of multiple excitation rings significantly enhances the intensity of SPP fields. Through the modulation of plasmonic single hotspots by holographic patterns produced by a custom-designed Gerchberg–Saxton algorithm, this study achieves considerable improvement in the precision and flexibility of gold particle manipulation. Unlike traditional approaches, the hotspots of surface plasmons are not restricted to a predefined nanostructure locally but can be precisely relocated within a specified region of interest. Another significant advantage of our tweezers system is its capacity for dynamic manipulation of metal particles without the need for mechanical adjustments. Theoretical simulations and MST mechanical simulations have confirmed that our proposed plasmonic optical tweezers system can generate sufficiently strong SPP hotspots to stably capture gold particles. Experimental results have validated the feasibility of dynamically controlling the positions of gold particles by altering the customized holographic images on the SLM, thereby creating specific trajectories such as “S”, “Z”, and “U” in response to the changes in SPP field hotspots. Specifically, the gold particles were moved by more than 10 μm, which illustrated that the optical force generated by SPPs is sufficiently strong over a wide spatial range. Through meticulous theoretical and experimental analysis, the proposed plasmonic tweezer underscores the potential of complex optical field manipulation in advancing the capabilities of dynamical plasmonic tweezers, driving future innovations in this rapidly evolving field. This method of manipulating dynamic SPP fields based on GS algorithm shows promise in forming multiple SPP hotspots and generating SPP fields with arbitrary intensity patterns. These advancements are expected to enable the trapping of multiple particles in different positions independently and simultaneously, as well as the arrangement of multiple particles along complex patterns. This research holds great promise for widespread applications in surface-enhanced Raman scattering, imaging, biosensing, and other related fields.