The white LED (WLED) has become the fourth-generation lighting source. Compared with fluorescent lamps and incandescent lamps, it has many advantages of energy saving, long life, green environmental protection, short switching time, and so on and is widely used in the indicator, backlight, car headlights, and daily lighting[1–10]. The commercial white LED combines a blue GaN LED chip with a (YAG) yellow phosphor, and Ce: YAG is packed on the chip surface using traditional silicone or epoxy resin[1,11–13]. This package brings about the deterioration and yellowing of traditional silicone (epoxy resin) and finally leads to some problems of white LEDs, including lumen–power loss, chromaticity shift, and the reduction of long-term reliability[14–18]. In order to solve these questions, the transparent solid luminescent material with good chemistry stability is one of the new directions for the development of white LED, and a large number of works of phosphor-in-glass (PiG) converters for white LEDs have been done[19–23]. In 2005, Fujita et al.[24–26] reported the first glass–ceramic (GC) phosphor; however, the maximum quantum yield (QY) for the Ce: YAG GC was only 30%, and the optimal luminous efficiency (LE) of GC-WLEDs reached merely . In 2012, a study on the preparation of PiG by the low-temperature co-sintering method was carried out by Lee et al.[27,28]. At present, the glass material used in the PiG research mainly includes: borosilicate glass material[29], tellurate glass material[30], and boro-bismuthate glass material[31]. Compared to the other two glass materials, the boro-bismuthate glass material has two main advantages: (1) lower sintering temperature could be achieved, reducing the attenuation of luminous efficacy caused by high temperature co-sintering of phosphor powder during preparation of PiG; (2) the boro-bismuthate glass material is relatively stable, which can realize PiG with multi-wavelength phosphor doping and good thermal stability[32].
In this Letter, we report boro-bismuthate-based PiG material that can be used to replace the conventional silicon-based phosphor converter in WLEDs. The mixture of boro-bismuthate glass powder and Ce: YAG phosphor was co-sintered at 700°C for different times under the reducing atmosphere of CO; all of the samples have compared and analyzed the photoluminescence (PL) properties. Moreover, we analyzed the content and variation in the crystal structure of of the PiG by an X-ray photoelectron spectrum analyzer and the X-ray diffraction (XRD) method.
In this Letter, the precursor glass with the following nominal composition (mole fraction) of 25% , 70% , and 5% ZnO was prepared by the conventional melting quenching method. Figure 1 is a schematic illustration of the synthesis of the PiG sample. , , and ZnO were used as starting materials without further purification that were mixed thoroughly in porcelain crucibles for 0.5 h and melted at 800–1000°C for 2 h in ambient atmosphere. The melt was quickly poured into a stainless steel mold and then cooled to room temperature. The original glass was milled to powders employing an agate mortar and sieved through 500 mesh screens, Ce: YAG (YAP4454-L, RayPower, China) phosphor powders were used without additional treatments to produce homogeneous particles, and the content of phosphor powder was 5% (mass fraction) in the final mixture. The mixture of glass powders and Ce: YAG phosphors was co-sintered at times ranging from 20 min to 60 min for 700°C under reducing atmosphere and air atmosphere, respectively, subsequently annealed at 100°C/h to relieve intrinsic stress, and then naturally cooled to room temperature. Finally, the obtained co-sintered disks were ground and polished to a thickness of 1 mm.
Sign up for Chinese Optics Letters TOC Get the latest issue of Advanced Photonics delivered right to you!Sign up now
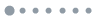
Figure 1.Schematic illustration of the synthesis of the PiG sample.
The crystal structure of the obtained sample was confirmed by the XRD method (Rigaku, Ultima IV, Japan) with Cu Kα radiation () at a scanning rate of 0.02(°)/step and 4(°)/min over a 10°–70° range. The PL and PL excitation (PLE) spectra were measured by Edinburgh Instruments using a xenon lamp as the light source. The concentrations of and were tested using an X-ray photoelectron spectrum analyzer (Escalab 250Xi, Thermo Fisher), of which the minimum resolution was 0.1 eV.
Figures 2(a)–2(d) display the PLE and PL spectra of the PiG co-sintered at times ranging from 20 min to 60 min at 700°C in reducing atmosphere and air atmosphere. The PLE spectra [Figs. 2(a) and 2(c)] show a broad excitation band ranging from 400 to 550 nm monitored at maximum emission wavelength of 558 nm, which is attributed to the transition of the ions. The PL spectra [Figs. 2(b) and 2(d)] show a broad emission band ranging from 500 to 650 nm excited at 460 nm originating from the transition of the ions. In Figs. 2(a) and 2(b), with the increase of sintering time, the PLE and PL intensity decreased in air atmosphere, which indicates that long-term sintering has a negative effect on luminescence properties of Ce: YAG. As shown in the Figs. 2(c) and 2(d), PiG was obtained by co-sintering under reducing atmosphere, and the excitation and emission intensity was decreased with the increase of time; however, compared to Figs. 2(a) and 2(b), the relative PL intensity of samples showed significant enhancement. With the common appearance in Figs. 2(a), 2(b) and 2(c), 2(d), the excitation and emission intensity of the PiG with a co-sintering time of 60 min was significantly weakened.
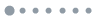
Figure 2.PLE and PL spectra of the PIG co-sintered for 20–60 min: (a) PLE spectra in air atmosphere; (b) PL spectra in air atmosphere; (c) PLE spectra under reducing atmosphere; (d) PL spectra under reducing atmosphere.
Figures 3(a) and 3(b) exhibit the increasing ratio of the maximum intensity of the PLE and PL spectra of PiG co-sintered and of the reducing atmosphere relative to the air atmosphere at different times, respectively. In Fig. 3(a), the relative PLE spectral peak intensity of PiG co-sintered for 20–60 min under a reducing atmosphere is significantly improved by about 6–13 times that under air atmosphere sintering. In Fig. 3(b), the relative PL spectral peak intensity of PiG co-sintered for 20–60 min under a reducing atmosphere is significantly enhanced about 2–14 times that under air atmosphere sintering. As shown in Figs. 3(a) and 3(b), the PLE and PL spectra of PiG co-sintered for 20–60 min are enhanced apparently under reducing atmosphere; the effect of the reduction co-sintering on the PL properties reduces when the co-sintering time is 60 min.
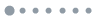
Figure 3.Increasing ratio of the luminescence intensity of the reducing atmosphere relative to the air atmosphere: (a) intensity ratio of PLE spectral peak intensity; (b) intensity ratio of PL spectral peak intensity.
The Ce: YAG phosphor and several phosphors use as an active ion, owing to its intense parity allowing electronic transitions[33,34], and the Ce ion has two valence states ( and ). As shown in Fig. 4, with the partial energy level schematic diagram and configuration coordinate of in YAG, we can find that the characteristic luminescence of Ce: YAG belongs to the transition of electrons, which has an obvious Stoke’s shift. The electronic transitions can be expressed with detail, and the electron in ground state A (the equilibrium position in the ground state) is promoted to excited state B. The electron relaxes from excited state B to minimum position C (the equilibrium position of the excited state); this relaxation is a nonradiative relaxation process accompanied by phonon emissions.
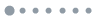
Figure 4.Partial energy level schematic diagram and configuration coordinate of in YAG.
Fluorescence is produced by electronic transition from minimum position C to ground state D. The electron relaxes from ground state position D to the minimum ground state position A; this relaxation is a nonradiative relaxation process accompanied by phonon emissions[35]. However, does not produce electron transition, so no electrons remain in the layer to achieve Stoke’s shift.
The X-ray photoelectron spectroscopy (XPS) profiles of glasses sintering for 20 min and 60 min in a reducing atmosphere and air atmosphere in the Fig. 5 were tested experimentally. There are two valence states ( and ) of rare earth cerium ions, in which ions are effective ions, and the characteristic luminescence of , which can be realized by Stoke’s shift, such as Ce: YAG phosphor, can emit yellow light under the excitation of blue chips. The 884, 902, 881.6, and 899.9 eV binding energies correspond to the , , , and components by querying the standard database of the XPS spectra[36]. The atomic system is slightly disturbed, and the binding energy of the inner layer may be shifted when the chemical environment around the Ce atom changes. According to relevant literature[36], the maximum binding energy of the Ce ion is 17.9 eV. Co-sintering atmosphere, FWHM, peak area, and the relative percentage of and [ratio of peak area of () or area of ()] of PiG co-sintered at different times are presented in Tables 1 and 2. As shown in Table 1, the content of the PiG increased from 46.2% to 68.7% because of the co-sintering atmosphere. According to the luminescence principle of Ce: YAG[37], only one electron in the layer of can achieve excitation and emission. If is oxidized to , then no electrons of can transit between the and levels to gain luminescence. It is found that the increase of content was the reason why the PiG co-sintered for 20 min exhibited the best luminescence performance. As shown in Table 2, the content of PiG increased from 45.1% to 49% for 60 min after reduction co-sintering, because a part of ions were reduced to ions. As the reduction co-sintering time goes on, the effect of reduction co-sintering is weak (Fig. 2). Thus, the concentration would directly affect the PL properties of the PiG. Therefore, PiGs were prepared by co-sintering under reducing atmosphere, which is beneficial for increasing the PL properties of the PiG.
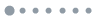
Figure 5.XPS spectra and fitting curves of Ce in the PiGs: (a) co-sintered for 20 min in air atmosphere; (b) co-sintered for 20 min under reducing atmosphere; (c) co-sintered for 60 min in air atmosphere; (d) co-sintered for 60 min under reducing atmosphere.

Table 1. Relative Percentage of Ce3+ in the PiGs Co-sintered for 20 min in Air Atmosphere and under Reducing Atmosphere
Table 1. Relative Percentage of Ce3+ in the PiGs Co-sintered for 20 min in Air Atmosphere and under Reducing Atmosphere
| Co-sintering Atmosphere | Peak (eV) | FWHM/eV | Area (a.u.) | Sum (a.u.) | Relative Percentage (%) |
---|
Ce4+ 3d5/2 | Air atmosphere | 884.595 | 4.19 | 2267.87 | 133417.20 | 53.80 | Ce4+ 3d3/2 | 901.438 | 8.20 | 131149.33 | Ce3+ 3d5/2 | Air atmosphere | 889.147 | 7.27 | 83165.05 | 114381.10 | 46.20 | Ce3+ 3d3/2 | 906.278 | 4.44 | 31216.05 | Ce4+ 3d5/2 | Reducing atmosphere | 884.535 | 4.86 | 53586.47 | 130628.82 | 31.30 | Ce4+ 3d3/2 | 900.830 | 4.27 | 77042.35 | Ce3+ 3d5/2 | Reducing atmosphere | 889.880 | 5.87 | 122283.08 | 287279.04 | 68.70 | Ce3+ 3d3/2 | 904.545 | 5.97 | 164995.96 |
|

Table 2. Relative Percentage of Ce3+ in the PiGs Co-sintered for 60 min in Air Atmosphere and under Reducing Atmosphere
Table 2. Relative Percentage of Ce3+ in the PiGs Co-sintered for 60 min in Air Atmosphere and under Reducing Atmosphere
| Co-sintering Atmosphere | Peak (eV) | FWHM (eV) | Area (a.u) | Sum (a.u.) | Relative Percentage (%) |
---|
Ce4+ 3d5/2 | Air atmosphere | 885.782 | 5.40 | 14141.38 | 125147.56 | 54.90 | Ce4+ 3d3/2 | 901.210 | 8.44 | 111006.18 | Ce3+ 3d5/2 | Air atmosphere | 889.540 | 6.35 | 65515.70 | 102626.73 | 45.10 | Ce3+ 3d3/2 | 906.210 | 4.40 | 37111.03 | Ce4+ 3d5/2 | Reducing atmosphere | 884.755 | 4.52 | 3616.25 | 124691.85 | 51.00 | Ce4+ 3d3/2 | 901.220 | 8.28 | 121075.96 | Ce3+ 3d5/2 | Reducing atmosphere | 889.184 | 7.12 | 81335.89 | 119671.41 | 49.00 | Ce3+ 3d3/2 | 906.070 | 4.73 | 38335.52 |
|
Figure 6 shows the XRD patterns of phosphor sintered for 20–60 min and PiG co-sintered in air atmosphere and under reducing atmosphere. As shown in the Fig. 6(a), the diffraction pattern of the samples showed all of the peaks of the YAG phase, which is in good agreement with the Joint Committee on Powder Diffraction Standards (JCPDS) card (No. 33-0040). This result indicates that the characteristic peak of YAG has no obvious change with the increase of the sintering time. The XRD also showed that the -doped YAG has a crystal structure with the space group Ia−3d (230) and lattice parameter [38,39]. As displayed in Fig. 6(b), the XRD peaks of the as-prepared PiGs sintered at 700°C are also similar to those of the standard YAG crystal (JCPDS No. 33-0040), where no impurity peak is observed. However, the XRD peak number decreases, and the main characteristic peak (420) is reduced with the increasing co-sintering time, so we can find that the excitation intensity and the emission intensity were decreased because of the damage of the lattice structure of YAG in the PiG. Further, we can conclude that co-sintering under reducing atmosphere can effectively slow down the corrosion of glass material on YAG lattice, protecting the lattice structure around ion. Thus, the luminescence performance can be significantly improved when co-sintered under reducing atmosphere.
In summary, we have successfully fabricated Ce: YAG PiG by the low-temperature co-sintering method. The PL properties of Ce: YAG PiG co-sintered at times ranging from 20 min to 60 min at 700°C under reducing atmosphere and air atmosphere were analyzed and studied. PL spectra and the ratio of the PL spectral peak intensity revealed that the luminescence properties of co-sintered PiG under reducing atmosphere were significantly enhanced about 7–10 times that under air atmosphere sintering. XPS investigation demonstrates that the and ions exist in the crystal lattice, and the ratio of the decrease was detected. XRD measurements showed that the lattice structure of YAG became damaged with the increase of co-sintering time [Fig. 6(b)]. The results show that the luminescence properties of co-sintered PiG under reducing atmosphere were significantly enhanced. The main reason was that (1) was less oxidized, and (2) co-sintering under reducing atmosphere can effectively slow down the corrosion of glass material on the YAG lattice.
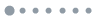
Figure 6.XRD patterns of Ce: YAG phosphors and PiG: (a) XRD of phosphors sintered at 700°C for different times; (b) XRD of PiG co-sintered at 700°C in air atmosphere and under reducing atmosphere.