1. Introduction
With the emergence of the Internet of Things (IoT), communication and interaction between objects have become smart, efficient, and convenient. Smart wearable devices possessing the ability to bend angle sensing and wireless communication play a key role in several IoT scenarios, including gesture recognition[1], remote healthcare[2], and human–machine interaction[3–5]. Optical sensors, especially fiber-optic sensors, have the advantages of anti-corrosion, anti-electromagnetic interference, and light weight. These merits effectively circumvent the disadvantages of electrical sensors and ensure stable acquisition and transmission of signals. Intensity modulation and phase modulation are two typical techniques for optical sensors. Phase modulation techniques mainly rely on the construction of fiber-optic interference structures[6,7], which sense the changes by monitoring the wavelength shift. However, the assembly of a broadband light source and spectrometer brings an expensive and complex system.
Intensity modulation techniques obtain the sensing information by directly monitoring the change of light intensity inside the fiber[8-10], resulting in a compact system, low-cost equipment, and flexible configuration. For instance, Zhou et al.[8] presented a wide joint angle detection based on plastic optical fiber (POF) using a laser source and an optical power meter. Aitkulov et al.[10] investigated the breathing rate measurement based on a smartphone-integrated fiber bending sensor. Similarly, using a flashlight and camera as a light source and detector, different sensors are demonstrated, including temperature[11], humidity[12], and refractive index[13]. Although smartphones provide a versatile platform for intensity-modulation-based sensing, the flashlight and camera are solidified inside a phone and cannot be flexibly configured. In addition, high-speed optical communication links are hardly realized from the hardware inside a smartphone.
Nowadays, optoelectronic devices based on III-nitride semiconductor material, especially GaN, have attracted much attention in high-speed ultraviolet light communication[14,15], visible light communication (VLC)[16,17], luminescence enhancement[18,19], optical sensing[20,21], and display[22-24] due to its advantages in fast response time, stable crystal structure, and wide bandgap width. In particular, the coexistence of light emission and detection of the GaN multiple quantum well (MQW) makes it possible to construct a monolithic optoelectronic platform and promotes the rapid development of GaN-based optoelectronic sensors and on-chip communication. For example, Li et al.[25] presented a monolithic integration of the light-emitting diode (LED), photodiode (PD), and waveguide on Si substrate, and a 250 Mb/s on-chip communication has been demonstrated. Wang et al.[26] investigated a two-way optical link using a single transmitter and receiver based on GaN MQW III-nitride diodes. Luo et al.[27] reported a chip-scale airflow sensor using a GaN-based optoelectronic device. Yu et al.[28] demonstrated a dual-functional p-i-n diode capable of light emission and detection in the deep ultraviolet band. Memon et al.[29] reported dual-wavelength wireless optical communication by integrating a micro-LED array with quantum dots, achieving the data rate of 586 and 55 Mbps at the emission wavelengths of 275 and 470 nm.
Sign up for Chinese Optics Letters TOC Get the latest issue of Advanced Photonics delivered right to you!Sign up now
In this work, a versatile optoelectronic platform with the monolithic integration of LED and PD has been developed to construct a fiber-optic bending angle sensing system as well as visible duplex communication links. On the one hand, the millimeter-sized optoelectronic device highly integrates a light emitter and a receiver, which enables the construction of a miniaturized chip-integrated fiber bending sensing system. In this case, fiber deformation changes the light amount coupled from the emitter to the detector, introducing an angle-dependent photocurrent response. On the other hand, such an optoelectronic device can be treated as a transceiver for duplex visible communication, and the corresponding uplink and downlink rates of 20 Mbps and 1 Mbps are obtained when pseudorandom binary sequence (PRBS) driven signals are applied.
2. Optoelectronic Chip Enabled Fiber-Optic Bending Sensing
2.1. Sketch diagram of the chip-integrated fiber sensing system
The sketch diagram of a chip-integrated angle-sensing system is shown in Fig. 1(a). Light emitted from an LED propagates along a leading-in fiber, passes through the sensing region, flows into a leading-out fiber, and is finally received by the on-chip PD. As force is applied over the sensitive region, the butt-coupling angle between the leading-in and out fibers changes, which causes variation in the transmission optical power inside the leading-out fiber. Weak fluctuation of the optical power is then captured by the on-chip PD. Figure 1(b) shows the microscope image of the chip under a biased voltage applied to the LED. It can be clearly seen that a bright light spot in the dark denotes the light-emitting region. The butt-to-butt coupling of chip and optical fiber is carried out with the assistance of a fiber coupling platform, and the bird-view image is displayed in Fig. 1(c). Here the light-emitting size is designed to be smaller than the diameter of the used fiber for a better butt coupling.
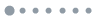
Figure 1.(a) Schematic diagram of a chip-integrated fiber sensing system. (b) Optical image of the chip with a driven voltage applied to the LED. (c) Microscope image of the butt-coupling between the optical fibers and chip.
2.2. Optoelectronic chip fabrication and characterization
The optoelectronic chip is fabricated on a sapphire substrate-based GaN wafer, as described in Fig. 2(a). The epitaxial structure is composed of undoped GaN, Si-doped GaN (n-GaN), MQW and Mg-doped GaN (p-GaN) from bottom to top. A 230-nm-thick transparent indium tin oxide (ITO) current spreading layer is deposited over p-GaN as a p-contact layer. Then two square regions with diameters of 0.1 and 1 mm are defined as the active areas for LED and PD units, respectively. Here, for micro-sized LED, inductively coupled plasma (ICP) is first used to etch the mesa with a footprint of and then the light-emitting region of the micro-sized LED is defined through patterning the ITO layer with a size of 100 µm rather than ICP etching of GaN. Deep etching is employed to remove all epilayers between the LED and PD regions for the device isolation. The metal stacks are further deposited on the n-GaN and ITO surfaces as the contact layer. After fabrication, the electrical and optical properties of the chip are characterized. As plotted in Fig. 2(b), current-voltage (I-V) curve is measured using a semiconductor device analyzer (Agilent B1500A). The inset plots the capacitance-voltage (C-V) curve of the chip. An alternating current (AC) signal of 1 MHz with applied voltage is used in the C-V measurement. The capacitance is approximately 50 pF before the driven voltage reaches the turn-on voltage. Figure 2(c) shows the emission and absorption spectra of LED and PD, respectively. As the driven current increases, the light amount of LED significantly improves, and a larger overlapped region occurs. The light emission is an irreversible process of light detection[30] that introduces a partially overlapped wavelength region, which is caused by the gravitational field[31]. The I-V characteristics of PD are measured under LED radiation with different driven currents, as presented in Fig. 2(d). Without LED radiation, the measured dark current is below . When the PD is radiated by the LED, the photocurrent significantly rises and reaches an order of at an injection current of 10 mA. The light emission power of the LED at a driven current of 10 mA is monitored over 8 h at room temperature, as recorded in Fig. 2(e). The peak-to-peak deviation is calculated to be 0.63%, which implies a good stability of the LED under a long-term operation.
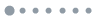
Figure 2.(a) Schematic diagram of the chip fabrication process, including (I) ITO deposition, (II) mesa definition and etching, (III) electrodes deposition, and (IV) meta pads deposition. (b) Current–voltage (I–V) curve of the LED. The inset shows its C–V curve. (c) Electroluminescence (EL) and response spectrum (RS) of the MQW-based structure. (d) Photocurrent response of the PD under LED radiation with different inject currents. (e) An 8 h stability test of the LED light-emitting intensity.
2.3. Optical fiber sensor fabrication
To sense the bending angle, a fiber sensor consisting of two opposite-aligned bare optical fibers (200 µm core diameter and ) sealed in a polydimethylsiloxane (PDMS) patch is presented. Fabrication stages are illustrated in Fig. 3. The first step involves the pouring of the underlying PDMS film, which is then heated at 80° for 40 min to obtain a flat PDMS patch with 300 µm thickness. Afterward, the underlying PDMS patch is transferred and attached to the bottom of a deeper model with a 1 mm thickness groove. Next, a piece of optical fiber is attached straight to the underlying PDMS patch, scratched with a diamond blade in the middle, and covered by a stack of PDMS liquid on the top layer. After heating again, a 1 mm thick PDMS patch is formed with the optical fiber firmly sealed in it. Finally, by slightly bending the middle part of the fiber, it is easily divided into two segments called the leading-in fiber and the leading-out fiber.
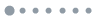
Figure 3.Schematic diagram of the fabrication process of a PDMS-packaged fiber sensor.
2.4. Experimental results for bending angle detection
The bending sensing performance is evaluated by measuring the photocurrent responses of the system under different bending angles. As force is applied to the sensitive region of the PDMS patch, the deformation of PDMS will bend the fiber inside, leading to a drop in the light coupling efficiency between the leading-in and leading-out fibers. In this case, the on-chip PD responds to the changed light intensity, and produces photocurrent to indicate the bending angles. As shown in Fig. 4(a), the photocurrent of PD decreases as the bending angle increases, and returns to the initial value (the pink baseline) once the bending is released. The measured photocurrent resembles a step-like trend, and a maximum photocurrent difference is about 410 nA when the bending angle changes from 0° to 40°. The symmetrical distribution of the steps indicates the good reducibility of the PDMS-encapsulated fiber sensor. As the bending angle exceeds 40°, the photocurrent value changes slowly. This is because that the amount of light received in the leading-out fiber is low at large misalignment coupling angles, resulting in little change in photocurrent. The corresponding photocurrent values at different bending angles are recorded and plotted in Fig. 4(b). As can be seen from the data (black and red dots), the system has a relatively low hysteresis when applying and withdrawing bending, and the slope efficiency of the linear ranges from 10° to 30° is calculated to be . Figure 4(c) shows the dynamic photocurrent response of the PD under repetitive cycles of fiber bending and release. The photocurrent response can consistently reach and return to the same baseline, suggesting the high repeatability of the sensing system. The minimally detectable bending angle of the system is also tested. As illustrated in Fig. 4(d), the system is capable of distinguishing bending angle of 2°, and the inset shows an enlarged view with distinguished steps.
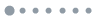
Figure 4.Bending sensing performances of the chip-integrated fiber system. (a) The system baseline (pink line) and step-like photocurrent response (blue line) when the bending angle continuously changes from 0° to 40°. (b) The extracted photocurrent values correspond to the bending angles. (c) Photocurrent response under instantaneous bending angle changes. (d) Photocurrent response of the sensing system under a bending angle step of 2°.
3. Optoelectronic Chip-Enabled Visible Light Communication
The integration of wireless communication and sensing modules broadens applications in IoT technology. Normally, the sensing system and communication modules are individually designed and accomplished, leading to high costs and complex configuration. Therefore, efficient utilization and mutual benefits between sensing and communication networks are demanded. Herein, apart from the ability of optical sensing, the proposed optoelectronic chip can also be applied for VLC. The schematic diagram of the VLC system is presented in Fig. 5(a). Duplex VLC links are established using the micro-LED as a transmitter and the on-chip PD as a receiver. The transmission and receiving performance of the chip are tested first. The pseudorandom binary sequence (PRBS) produced by the signal generator is used to drive the micro-LED. The emitted blue light is focused and directed to the external PD. Similarly, the on-chip PD is irradiated by a modulated 405 nm LD to verify the optical detection. Figure 5(b) shows the frequency response curve of the micro-LED transmitter under a biased voltage of 3.7 V. The device bandwidths at and are 12 and 42 MHz, respectively. Normally, micro-LEDs have a high modulation bandwidth and are widely employed for high-speed on-chip or free-space communication[28,29,32]. In our results, the frequency bandwidth is limited to tens of megahertz, which is possibly caused by the large resistance-capacitance (RC) time constant associated with our micro-fabrication process. As plotted in the inset in Fig. 2(b), the value of capacitance is around 50 pF before the applied voltage exceeds the turn-on voltage. The resistance of the LED is calculated to be approximately 48 Ω from the slope of the linear region of the I–V curve. The high resistance value may be caused by the poor contact characteristics of the metal and semiconductor. The relatively high RC constant limits the frequency bandwidth of the device. Based on PRBS modulation, the micro-LED is driven at a transmission rate of 20 Mbps, and a commercial PD is used to receive the signal. As recorded in Fig. 5(c), the received signal retains its original waveform profile at 20 Mbps. Figure 5(d) presents the waveform comparison before and after the on-chip PD reception when the LD is modulated with a data rate of 1 Mbps. The open eye diagram can be clearly seen corresponding to the transmitted rate of 20 Mbps, as illustrated in Fig. 5(e).
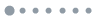
Figure 5.Experimental results of VLC when the monolithic optoelectronic chip serves as a transceiver. (a) Experimental setup of the VLC links for audio and video transmission. (b) Bandwidth of the micro-LED. Comparisons between transmitted and received PRBS signals when the system works in the (c) uplink and (d) downlink states, respectively. (e) Eye diagram at 20 Mbps.
Afterward, real-time audio and video signal transmissions are demonstrated with the VLC system. As displayed in Fig. 5(a), the surrounding image is collected by a camera, and the voltage of the generated data streams is amplified first by an operational amplifier. Then the amplified signal mixed with the DC signal through a bias-T is employed to drive the micro-LED. At the receiving part, an external PD converts the optical signal into the electrical signal. The electrical signal is captured via a video capture card, transformed into a video signal, and displayed on the screen of a terminal monitor in real time (see Visualization 1). For audio signal demonstration, a clip of music “Sky City” is transformed into data format and loaded into the signal generator to drive an external LD. The driven voltage and amplitude applied to the LD are set to be 3.6 V and 800 mVpp, respectively. The on-chip PD responds to the laser radiation and generates the photocurrent carrying the audio information. The detected audio signal is amplified by a trans-impedance amplifier (TIA) and replayed through a speaker (see Visualization 2). The original signal and the recovered audio signal are compared and analyzed in the time domain and frequency domain, respectively. As displayed in Figs. 6(a) and 6(c), the detected waveform (marked with blue curve) is consistent with the original signal (marked with red curve). The recovered signal nearly retains most of the amplitude information without distortion. Since the audio signal is composed of multiple frequency components, the quality of the received signal depends on the accurate reception of each single frequency. The corresponding spectrograms are analyzed by fast Fourier transform (FFT) to evaluate the signal reconstruction performances. As can be seen in Figs. 6(b) and 6(d), the frequency distributions of the selected music are below 4 kHz, mainly in the range from 1 to 2 kHz. In addition, a series of vertical stripes in the spectrogram are clearly observed, which denote the amplitude of the audio signal over time. In terms of intensity visibility, the recovered signal is weaker than the original signal owing to the reduced amplitude values. But the main frequency components are able to be maintained. As a result, there is no distortion in the sound quality of the recovery signal played through the speaker.
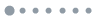
Figure 6.Comparisons between original and recovered audio signals in the time domain and the frequency domain. (a) Waveform and (b) spectrogram of the original signal. (c) Waveform and (d) spectrogram of the recovered signal.
4. Conclusion
In conclusion, we demonstrate a versatile monolithic optoelectronic platform, which can be used for fiber sensing as well as VLC. The monolithic integration of the LED and PD efficiently replaces the bulky external light source and detector, which is small in size and low in cost. By configuring this optoelectronic platform, bending angle measurement and audio-video transmission are performed. These proof-of-concept experiments validate the multi-function of the optoelectronic platform, which is expected to build a miniaturized and low-cost integrated optical sensing and communication (IOSAC) systems.