1. Introduction
With the development of modern communication, integrated photonics has strongly promoted the development of optical communication[1–3]. As the key component of integrated photonics, waveguide beam splitters[4], which allow the guiding and splitting of light in small volumes, play a significant role in getting faster information transmission in optical communication[5,6]. For example, beam splitters have been designed and fabricated in various integrated platforms, such as directional couplers[7–11], polarization beam splitters[12–14], multi-mode interferometers[15–17], and Y-branches[18,19].
In recent years, the fabrications of waveguide beam splitters in crystalline materials have been deeply investigated[20–22]. The conventional waveguide channel fabrication techniques, such as ion exchange, ion implantation, and chemical vapor deposition[23–26], suffer from complicated processing steps and high costs. In contrast, waveguide beam splitters fabricated by femtosecond laser direct writing (FLDW) have emerged as a cost-effective, fast, and mature strategy. FLDW has been proven to be a powerful and unique technique to fabricate waveguides in a wide range of transparent materials owing to its advantages of non-contact and maskless fabrication, high resolution, and high efficiency[27–32]. In general, the modifications of waveguide regions processed by FLDW can be divided into two types[33] when the pulse energy of the laser is higher than the modification threshold: (1) the lattice and the bond-lengths are contractive due to the contractive stress of the lattice strain-field along the filaments, resulting in the refractive index increase at processed regions, which is referred to as type I modification[4,20,34], and (2) the lattice defects/damages and the elongation of bond-lengths are observed due to expansive stress resulting in the refractive index decrease at processed regions, which is referred to as type II modification[35]. In contrast with type I modification, type II modification requires a more complex configuration design and fabrication process and a longer fabrication time in transparent optical crystals. The fabrication of waveguide beam splitters with type I modifications has been reported, but the previous studies are mainly focused on achieving a uniform splitting ratio.
In this Letter, waveguide beam splitters () with type I modifications are fabricated in a crystal by FLDW. The influence of the relative positions of the sub-waveguides on the splitting ratio of the beam splitter is observed in the numerical simulation during the design procedure. Three waveguide beam splitters with different relative positions of the branch segments are selected for laser processing and experimental investigation in our work. The results of the numerical simulation are confirmed with the experimental findings as expected. There are significant differences in the splitting ratios among the three beam splitters. By adjusting the relative width of the three sub-waveguides, the waveguide beam splitter with a splitting ratio of 1:1:1 is successfully designed and fabricated. In general, we demonstrate that beam splitters with different splitting ratios can be made by simply adjusting the relative positions and relative widths among the branch segments, which provides the possibility for further improvement and practical application of the straightforward-designed beam splitter in integrated photonics circuits.
Sign up for Chinese Optics Letters TOC Get the latest issue of Advanced Photonics delivered right to you!Sign up now
2. Design and Simulation
Figure 1(a) shows the schematic description of the beam splitter. The waveguide beam splitter studied in this work possesses three branch waveguides or sub-waveguides: the left waveguide, the right waveguide, and the middle waveguide. The lengths of the incident waveguide and the output waveguide are all 3 mm, which are labeled and , respectively. The lengths of the two S-bend waveguides and the middle straight waveguide are 4 mm [all labeled in Fig. 1(a)].
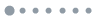
Figure 1.(a) Schematic description of the beam splitter. The output powers of (b) the left waveguide, (c) the middle waveguide, and (d) the right waveguide as functions of W1 and W2 of the splitters, and the incident power is normalized. The triangle, the circle, and the diamond marks in each image correspond to splitters BS1, BS2, and BS3 respectively.
During the numerical simulation, the background materials are set to the crystal[36]. Since the polarization direction of the incident laser is along the optical axis and the coupling system is based on a 532 nm laser, the refractive index is set to . The change of the refractive index by FLDW can be estimated by measuring the maximum efficient incident angle of the straight type I waveguide[37]. According to the coupling experiment results, the double laser direct writing processing will cause a slightly larger refractive index change, which is about , compared to the single laser direct writing processing. In order to increase the cross-sectional area of the waveguide and reduce the coupling loss, double laser direct writing processing is selected. The change of the refractive index is set up to 0.0014 in numerical simulation. Based on these parameters, the effect of the distances between the left waveguide and the middle waveguide and between the right waveguide and the middle waveguide [labeled and in Fig. 1(a), respectively] on the splitting ratio is investigated by beam propagation method (BPM). The output powers of the left waveguide, the right waveguide, and the middle waveguide as functions of and are plotted in Fig. 1.
There exist significant changes among the powers of the three output waveguides when and of the beam splitter change. Considering the interaction among the three output waveguides due to the close distance, the cases when and are discussed. When , the influence of the branch angles on the symmetric beam splitters () can be studied. With the increase of the branch angle of the beam splitter, the power of the middle waveguide gradually increases, and the powers of the left waveguide and right waveguide gradually decrease. When , the splitting ratio of the asymmetric beam splitter () can be studied. With the increase of , the output power of the left waveguide decreases, and the output power of the right waveguide increases when is constant. When is constant, the case is reversed. Here, several specific situations are selected, and the triangle, the circle, and the diamond marks correspond to splitters (, ), (, ), and (, ) in each image, as shown in Fig. 1. A waveguide beam splitter (, ) with a 1:1:1 splitting ratio is designed by doubling the widths of the left and right waveguides based on splitter . The specific design parameters of these four splitters are listed in Table 1.

Table 1. Comparison of the Dimension Parameters of the Beam Splitters
Table 1. Comparison of the Dimension Parameters of the Beam Splitters
Type | End-face | Distance | Number |
---|
BS1 |  | W1 = 30, W2 = 30 | NLeft = 2, NMid = 2, NRight = 2 | BS2 |  | W1 = 50, W2 = 50 | NLeft = 2, NMid = 2, NRight = 2 | BS3 |  | W1 = 50, W2 = 30 | NLeft = 2, NMid = 2, NRight = 2 | BS4 |  | W1 = 50, W2 = 50 | NLeft = 4, NMid = 2, NRight = 4 |
|
3. Fabrication and Measurement
In this work, the beam splitters are fabricated in an optical-polished pure -cut crystal [] by FLDW. The -cut sample is placed on a 6-axis precision motorized stage during the fabrication process. An amplified Ti:sapphire laser system (Astrella, Coherent Inc., United States) is used as the laser source, which delivers linearly polarized pulses with a pulse duration of 100 fs, a central wavelength of 800 nm, and a repetition rate of 1 kHz. The laser beam is focused by a microscope objective lens () into the crystal, and the focusing depth is about 100 µm beneath the sample’s upper surface. The single pulse energy is set to 75 nJ.
Figure 2 shows a schematic description of the beam splitter in the crystal. The structure is formed by moving the focal point with a velocity of 0.1 mm/s along the -axis of the crystal. The input waveguides of the four beam splitters are all formed by six tracks with an interval of 1 µm by FLDW. Each branch waveguide of splitters , , and is processed twice with an interval of 1 µm. In this way, a double-line structure can be formed, as shown in the inset red square in Fig. 2. The left and right branch waveguides of splitter are processed four times with an interval of 1 µm, forming a quadruple-line structure, as illustrated in the inset black square in Fig. 2. In the splitter , the left branch waveguide and the right branch waveguide correspond to four tracks from the left and four tracks from the right of the input waveguide, respectively.
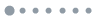
Figure 2.Schematic description of the beam splitter in the LiNbO3 crystal. W1 and W2 are the distances between the left waveguide and the middle waveguide and between the right waveguide and the middle waveguide, respectively. The inset is the transmission microscopic image of the beam splitter BS1.
The Raman properties of the waveguide beam splitter are measured using a confocal micro-Raman spectroscopy system (XperRam200, Nanobase Inc., Republic of Korea). An end-face coupling system is utilized to test the guiding properties of the waveguide beam splitters. During this experiment, a continuous laser at 532 nm (Verdi G, Coherent Inc., United States) is coupled into the input end-face of the waveguide beam splitter through an objective lens (, ). A half-wave plate is used to control the polarization direction of the laser beam. Another microscope objective (, ) is used to collect the light from the output end-face and deliver the focused light to the CCD camera (WCD-UCD 12-1310, DataRay, United States). The output optical intensities are measured by a power meter.
4. Results and Discussion
The inset in Fig. 2 shows the microscopic image of the output end-face of the waveguide beam splitter (). It can be clearly found that the modified regions are brighter than the non-processed bulk region, which indicates that the modified regions have suffered type I modification by FLDW. In this way, the input energy can be divided into three parts.
The Raman spectra collected from the output cross section of are shown in Fig. 3. Raman spectra are accurately measured at the bulk and waveguide regions, respectively, by a 785 nm continuous laser. For the type I modified waveguide, there is no obvious difference between the processed waveguide region (red solid line), as the guiding region and the non-processed bulk region (black solid line) indicate that the lattice structure in the irradiation region is well preserved during FLDW. The Raman intensity mapping image of the middle waveguide end-face with the channel of the central wavenumber at is displayed in the inset in Fig. 3. It has been calculated that the intensity of the modified regions reduces by just 2% compared with the bulk region. In order to further investigate the formation mechanism of the refractive index modulation, the redshift (wavenumber increase) is observed in the processed region from the Raman frequency shift mapping at , which corresponds to the molecular phonon mode . The redshift indicates the increase of the vibration frequency and the contraction of the bond-length which is caused by the contractive stress of the lattice strain-field along the filaments, resulting in the refractive index increase at processed regions. The change of the refractive index has been calculated by measuring the maximum efficient incident angle of the straight type I waveguide. According to our investigation, the refractive index change induced by the laser direct writing once is only , and the refractive index change will be enhanced to when the laser scans twice to form the branch waveguides.
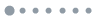
Figure 3.Raman spectra collected from the non-processed bulk area (black solid line) and the waveguide area (red solid line) excited by a 785 nm laser. Corresponding molecular phonon modes are marked out on every peaks.
The corresponding splitting ratios measured by the power meter are presented in Table 2. Through the comparison of the experimental results with the numerical simulation results, the maximum error among them is less than 3.5%. The maximum insertion loss is about 17.90 dB, which is mainly caused by the higher coupling loss. The propagation loss is 4.03 dB/cm according to our investigation. Comparing the beam splitters of , , and , we can find that the output power ratio of the output waveguide with the shorter distance from the middle output waveguide is higher, but it cannot exceed the output power of the middle output waveguide when and . Thus, it means that we can have access to regulate the splitting ratio of the splitters by just changing the parameters and . Furthermore, the splitter has been successfully fabricated with the performance of the 1:1:1 splitting ratio. Different from the design of , the left branch and the right branch of have been processed four times with an interval of 1 µm in , which increases the width of these two output waveguides. Comparing splitters (1:3:1) and (1:1:1), we find that the power ratio of the middle output waveguides can be reduced from 60% to 30% by increasing the width of the side waveguides. Therefore, it can be concluded that the width of the waveguides can affect the splitting ratio easily.
The 2D (bottom) and 3D (top) mode profiles of the output light field collected from , , , and are presented in Fig. 4. The mode profiles prove that these beam splitters support the propagation of fundamental modes with high beam quality at TM polarization. The sample that has been processed is a -cut lithium niobate crystal, which is a birefringent crystal. The coupling loss of the beam splitter is very large at TE polarization, so that we do not discuss the performances of the beam splitters at TE polarization here.
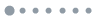
Figure 4.Near-field mode intensity distribution results at 532 nm are exhibited as 2D (bottom) and 3D (top) images. (a), (b), (c), and (d) correspond to splitters BS1, BS2, BS3, and BS4, respectively. The x-axis is located at the height of the centers of the three sub-waveguides at the output end.
Considering the accuracy of the optical power measurement, the beam powers are gained from the near-field mode intensity distribution along the -axis (in 2D images in Fig. 4), which is located at the height of the centers of the three sub-waveguides, and the normalized results are shown in Fig. 5. After normalization, the power splitting ratios are 22.1%:55.2%:22.7%, 19.4%:60.6%:20.0%, 15.1%:47.2%:37.7%, and 33.9%:33.2%:32.9%, corresponding to splitters , , , and , respectively. Compared with the numerical simulation results, the maximum error has been controlled to be less than 2.5%. According to our simulation and experimental results, beam splitters with any output power ratios can be realized by choosing appropriate structural configurations. Thanks to the input and output waveguides, which have a proportionable cross section compared with single-mode optical fibers and support single-mode laser propagation, the proposed beam splitters can be compatible with optical fibers and can promote their applications in the field of fiber-to-chip devices.
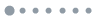
Figure 5.Normalized power ratios obtained from the coupling results. (a), (b), (c), and (d) correspond to splitters BS1, BS2, BS3, and BS4, respectively.
5. Conclusion
In summary, the design, simulation, and fabrication of the waveguide beam splitters () with type I modifications have been presented. The modal profiles of the splitters exhibit good fundamental modes at TM polarization. The experimentally measured power splitting ratios of the waveguide beam splitter are good and consistent with the simulation results. These performances also indicate that the beam splitting ratio of the waveguide beam splitter can be precisely regulated by adjusting the position and the width of the sub-waveguide, which provides more possibilities for the application of waveguide beam splitters in integrated optics.