On-chip optical interconnects based on silicon photonics technology have attracted significant attention in the past decade due to their compatibility with the mature complementary metal oxide semiconductor (CMOS) process, strong optical confinement, and the potential to realize the monolithic integration of optical and electronic components[1], which provide both cost and performance advantages. Several silicon photonic platforms have been demonstrated, and various optical interconnect devices have been developed[2–4]. The high level of integration also helps bring the design and production of systems into reality that otherwise would be too costly or complex to be developed in other material systems, such as wavelength division multiplexed passive optical network (WDM PON) solutions for fiber-to-the-home (FTTH)[5].
Coupling light from single-mode fibers to on-chip waveguides in silicon WDM PON systems requires large bandwidths and polarization insensitivity. Edge coupling of light from single-mode fibers to on-chip waveguides is typically utilized due to the narrow bandwidth drawback of grating couplers[6,7]. To further enable a polarization diversity operation, a broadband polarization splitter and rotator that cover the entire waveband from 1310 to 1550 nm are required[8]. An ultra-broadband polarization rotator splitter (PRS) operating from 1350 to 1750 nm was proposed in Ref. [9], in which they utilized a mode-sorting asymmetric Y-junction that requires high-resolution lithography and is difficult to precisely fabricate. Recently, a bi-wavelength PRS comprising an adiabatic conversion section and asymmetric directional coupler was proposed[8]; however, it is only suitable for FTTH applications at 1310 and 1550 nm wavebands and cannot satisfy the needs of triple wavebands in FTTH systems. A PRS with a bandwidth as large as 300 nm was proposed[10]. A layer of silicon nitride () was utilized as the top cladding material to break the vertical symmetry of the waveguides, which added complexity to the fabrication process.
In this Letter, we propose an ultra-broadband PRS based on a cascaded adiabatic bi-level taper and mode-evolution counter-tapered coupler. Benefitting from the broadband and low-loss characteristics of the adiabatic taper and counter-tapered coupler, the simulated insertion loss (IL) and crosstalk (CT) of the proposed PRS are less than 0.2 and with a bandwidth as large as 320 nm, covering all 1310, 1490, and 1550 nm wavebands. A standard silicon dioxide () cladding is used without the introduction of silicon nitride or air cladding due to the asymmetric cross section of the rib waveguide. The fabrication process sensitivity of the device is also analyzed, showing a large fabrication tolerance with a waveguide width variation of and top silicon thickness or slab height variation of for the entire operation waveband. Considering the manufacturing deviations in industrial silicon photonic foundries that have a top silicon thickness variation of and linewidth variations [11,12], this proposed device is quite fabrication tolerant. With such a broad operating bandwidth and a robust performance, this device offers great potential in silicon photonic systems, especially in applications requiring large bandwidths, such as WDM PONs for FTTH.
Figure 1 shows the schematic of the proposed device, where the dark blue regions represent the Si waveguides and light blue regions represent the partially etched slab waveguide. Table 1 lists the parameters and corresponding values of the proposed device. Silicon-on-insulator (SOI) wafers with a top silicon thickness of 220 nm are used, and a slab height of 90 nm is selected to be compatible with the standard fabrication process in a silicon photonic foundry[13]. The device is composed of an adiabatic bi-level taper and a mode-evolution counter-tapered coupler. A standard top cladding is used due to the asymmetric cross section of the rib waveguide. Both the and modes are launched into the left port of the bus waveguide, as shown in Fig. 1. The mode directly passes through the device and outputs from the through port. The mode will be converted to the mode first by the bi-level taper and then coupled to the mode in the cross port after passing through the counter-tapered coupler. In this way, the and polarizations are separated and output as modes at two ports. To obtain a broad operation bandwidth, both the bi-level taper and mode-evolution counter-tapered coupler are carefully optimized.

Table 1. Parameters and Corresponding Values of the Proposed Device
Table 1. Parameters and Corresponding Values of the Proposed Device
Parameters | Values (μm) | Parameters | Values (μm) |
---|
W0 | 0.45 | Ws | 0.5 | W1 | 0.55 | Wg | 0.16 | W2 | 0.75 | Ltp1 | 28.5 | W3 | 0.72 | Ltp2 | 25 | W4 | 0.5 | Ltp3 | 200 | W5 | 0.18 | Ltp4 | 10 | W6 | 0.4 | R | 20 | W7 | 0.45 |
|
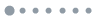
Figure 1.Schematic of the proposed device based on a cascaded adiabatic bi-level taper and mode-evolution counter-tapered coupler.
A bi-level taper with an asymmetrical waveguide cross section is utilized to realize a highly efficient mode conversion. Due to the mode hybridization in the asymmetric waveguide cross section, mode conversion between the TM fundamental mode and higher-order TE modes is observed[14]. To obtain a broad bandwidth covering the entire waveband from 1310 to 1550 nm, the device is optimized at two wavelengths of 1310 and 1550 nm. Effective indices of the first three modes (, , and ) in the cross section along the proposed bi-level taper are calculated with a commercial simulation software package (FIMMWAVE) and shown in Fig. 2(a). The brown dashed circles in Fig. 2(a) show the mode hybridizations between the and modes at the rib/slab waveguide widths around at the two wavelengths. A bi-level taper with rib widths/slab widths increased from to is designed. are selected to avoid the back conversion from the mode to the mode. The taper length is also a factor determining and . Figure 2(b) shows the electric field profiles of the first two modes in the cross section along this taper at the wavelength of 1310 nm. The first mode, which is identified as a mode, directly passes the bi-level taper. The second mode is a mode at the beginning of the taper and converted into a mode after passing through the taper, which is also shown by straight and dashed arrows in Fig. 2(a). In the mode hybridization region, the minor component ( or ) is comparable to the corresponding major component ( or ), which leads to the mode conversion between the and modes[14], as shown in Fig. 2(b).
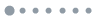
Figure 2.(a) The calculated effective refractive indices of the first three modes in the waveguide cross section along the bi-level taper at wavelengths of 1310 nm (dashed) and 1550 nm (straight). (b) The electric field profiles of the first two modes in the cross section along this taper at the wavelength of 1310 nm.
To obtain an efficient mode conversion, the taper lengths and need careful optimizations. The second taper with a length of is designed after the conversion section to transform the rib waveguide to a channel one; this is shown in Fig. 1. The of 0.75 μm is selected such that the effective mode indices of the and modes are separated wide enough so that the mode will not convert back to the mode. Meanwhile, a larger requires a longer taper to reduce the transition loss. The three-dimensional simulation software FIMMPROP based on the eigen-mode expansion (EME) method is used to find and . Figure 3(a) shows the simulated conversion efficiencies as a function of with of 15, 20, and 25 μm at both 1310 and 1550 nm wavelengths. The conversion efficiencies increase with increasing for all three and reach nearly 100% when is large enough. One can also note that there are some notable ripples with a shorter (), which are likely caused by undesired modes interferences or reflections in the taper and could be eliminated with the increase of and . An of 28.5 μm and an of 25 μm are selected to achieve high efficiency mode conversions for the two wavelengths of 1310 and 1550 nm. The relation between conversion efficiency and wavelength is finally simulated with FIMMPROP and shown in Fig. 3(b). A conversion efficiency larger than 99% is obtained from the wavelength of 1.27 to 1.59 μm, which verified our design method using two wavelengths of 1310 and 1550 nm. The inset of Fig. 3(b) clearly shows the simulated electric field intensity distributions in this bi-level taper with the mode launched at 1310 and 1550 nm wavelengths.
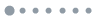
Figure 3.(a) The mode conversion efficiency from the mode to mode in the bi-level taper as the varies with the second taper length , 20, and 25 μm at the wavelength of 1310 nm (dashed) and 1550 nm (straight). (b) Wavelength dependence of the mode conversion efficiency when and . Inset: simulated electric field intensity distributions in the bi-level taper as the mode launched at 1310 and 1550 nm wavelengths.
A counter-tapered coupler that has two waveguides with the cores counter tapered is designed after the bi-level taper to couple the obtained mode in the bus waveguide to the mode in the cross port. An adiabatic taper with a length of is designed to connect the bi-level taper and counter-tapered coupler. The operation principle is based on mode evolution. Unlike the directional coupler based on interference theory, the counter-tapered couplers are approximate adiabatic devices and do not rely on precise phase conditions to be satisfied over an extended length, which permits ultra-wideband mode division operations. A more detailed discussion of the counter-tapered coupler can be found in Refs. [15,16]. An S-type bend with a radius of is utilized to alleviate the coupling between the through and cross waveguides.
FIMMWAVE is used to calculate the effective indices of the mode and mode in the through waveguide and the mode in the cross waveguide at the two wavelengths of 1310 and 1550 nm, as shown in Fig. 4(a). The width of the through waveguide decreases from 0.72 μm () to 0.5 μm (), whereas the width of the cross waveguide increases from 0.18 μm () to 0.4 μm (). Effective index cross points or phase-matching points between the mode in the through waveguide and the mode in the cross one can be found in Fig. 4(a) for both wavelengths of 1310 and 1550 nm; these are circled by brown dashed lines. This indicates the mode in the through waveguide would convert to the mode in the cross one with a properly designed coupler length . The end widths of the two tapers are carefully selected to ensure not only the existence of index cross points, but also that no converted modes couple back. Unexpected coupling between the two modes in through and cross WGs is eliminated with a larger through WG width .
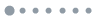
Figure 4.(a) The calculated effective refractive indices of the modes ( and ) in the cross/through waveguide of the counter-tapered coupler with width tapering from 0.18/0.72 to 0.4/0.5 μm at wavelengths of 1310 nm (dashed) and 1550 nm (straight). (b) Mode conversion loss from the launched mode to the mode at the wavelengths of 1310 and 1550 nm. Inset: wavelength dependence of the mode conversion loss at and . (c) and (d) Simulated electric field intensity distributions in the counter-tapered coupler as the mode launched at the wavelengths of 1310 and 1550 nm, respectively. .
The taper length is also an important factor in selecting the taper end width. Figure 4(b) shows the simulated mode conversion loss as the function of coupler length at the wavelengths of 1310 and 1550 nm. The mode conversion loss decreases as increases, and a very low loss of less than 0.1 dB can be achieved when at both wavelengths of 1310 and 1550 nm. An of 200 μm is selected considering the device loss and footprint. Conversion losses are finally simulated with FIMMPROP and shown in the inset of Fig. 4(b). Losses less than 0.2 dB can be obtained in the wavelength range from 1.29 to 1.63 μm. A larger coupler length would further reduce the conversion loss of modes with wavelengths smaller than 1310 nm. Figures 4(c) and 4(d) show the simulated electric field intensity distribution in this counter-tapered coupler with the mode launched at wavelengths 1310 and 1550 nm, respectively. One can note that the mode conversions from the mode to mode in this coupler are achieved as expected. For mode input, it will pass through the coupler directly, as no index cross points and mode coupling occur between the two waveguides.
FIMMPROP is used to verify the performance of the complete device. The PRS device performances are usually characterized by IL and CT for each input polarization. Figure 5(a) shows the wavelength dependence of the IL and CT for the mode and mode. CT and IL of less than and are obtained from the wavelength of 1290 to 1610 nm for both input modes, respectively. With such a broad operating bandwidth, this device offers great potential in silicon photonic systems, especially in applications requiring a large operation waveband, such as WDM PONs for FTTH. Figures 5(b)–5(g) show the simulated electric field intensity distribution in the designed PRS at the wavelengths of 1310, 1490, and 1550 nm. For all three wavelengths, the launched modes output from the cross port of the PRS after conversion to the modes. Meanwhile, the input modes output from the through port directly, which confirms our previous design.
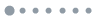
Figure 5.(a) Wavelength dependence of the PRS performance in terms of the IL and CT for different launched modes. (b)–(g) Simulated electric field intensity distributions in our proposed PRS as the mode and mode launched at the wavelengths of 1310, 1490, and 1550 nm.
The IL and CT gradually degrade for the mode input when the wavelength falls short of 1310 nm, as shown in Fig. 5(a), but this can be improved by increasing the coupler length of the counter-tapered coupler. Meanwhile, the CT of the mode has some ripples that can be improved by increasing the lengths and of the bi-level taper. The CT gradually increases with the increasing wavelength for both two modes, which is caused by the coupling between the S-type output waveguide and straight output that can be further improved by design optimization.
The fabrication tolerance is investigated for the proposed PRS. Performance degradations for the and mode inputs are simulated. Figures 6(a)–6(c) show the wavelength dependence of the IL and CT with a top silicon thickness variation of , a slab height variation of , and a waveguide width variation of , which includes the bi-level taper and counter-tapered coupler as the mode input. The performance metrics remain stable with a width variation of and top silicon thickness or slab height variation of in the whole operation waveband. As no mode conversion and coupling occur in the PRS for the mode input, the performance metrics remain stable with the above variation for the mode input through our simulation. Manufacturing deviations with a top silicon thickness variation of and linewidth variations are demonstrated in silicon photonic platforms[11,12], which are smaller than the fabrication tolerances of the design. Due to the adiabatic conversion and coupling of modes in the bi-level taper and counter-tapered coupler, the width, thickness, or wavelength variation only lead to the position shift of the mode hybridizations and phase-matching points and will not affect the PRS performance seriously. Compared to the previously reported PSGC[17] and PRS[8], this device has an ultra-broad operating bandwidth and large fabrication tolerance, which offers potentials in applications requiring a large operation bandwidth such as WDM PONs for FTTH.
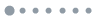
Figure 6.Fabrication tolerance analysis for the wavelength dependence of IL and CT with (a) the top silicon thickness variation , (b) the slab height variation , and (c) the waveguide width variation of the whole device as the mode launched.
In addition, only the mode conversion loss is considered in this work. The scattering loss due to the side-wall roughness of the waveguide is extremely detrimental to the total loss of this PRS in practice. This kind of loss could be significantly reduced by optimizing the fabrication process, such as photolithography and etching processes[18]. To further reduce the size, a narrower gap of could be selected to enhance the coupling strength, and thus, a smaller coupler length can be obtained. On the other hand, the bi-level tapers could be optimized by adopting some other shapes (e.g., parabolic or sinusoidal) with multi-variable optimization[19] to reduce the device length.
In conclusion, an ultra-broadband and fabrication-tolerant silicon PRS based on a cascaded adiabatic taper and mode-evolution counter-tapered coupler is proposed in this Letter. IL and CT of less than 0.2 and are obtained, respectively, with a bandwidth as large as 320 nm. Due to the asymmetric cross section of the rib waveguide, a standard top cladding is used, eliminating the need for silicon nitride or air cladding. The performance degradation due to fabrication errors is also analyzed, showing that the device is quite robust, with tolerances greater than the manufacturing deviations of mature silicon photonic platforms. With such a broad operating bandwidth and robust performance, this device offers great potential in silicon photonic systems, especially in applications requiring large bandwidths such as WDM PONs for FTTH.