1. Introduction
Light has energy and momentum, and, in modern optics, light is mainly studied as the essential attribute of light as electromagnetic waves, while, in contemporary optics, the mechanical effect of the photons with other micro/nano-level particles is the primary object of study. With the development of laser technology in the 1960s, researchers acquired a new tool with which to study the interaction between light and matter. After Ashkin[1] proposed the theory of optical levitation by using laser technology, optical levitation technology has gradually become a research field of interdisciplinary fusion on the cutting edge. Researchers use it as a new tool to study the interaction between micro–nano particles and light[2–4]. With the application of optical levitation technology in the fields of physiology and physics[5], quantum measurement[6–8], medical diagnosis[9], optical fiber levitation technology[10–12], and holographic optical levitation technology[13–15], near-field optical levitation technology[16,17] has gradually enriched the forms of optical levitation technology. However, as shown in Fig. 1[18], most of the optical levitation systems, the entire volume of which is , use traditional desktop lasers as the trapping optical sources with good beam shape and quality. Such systems are difficult to use in compact engineering devices, owing to their large volume and high cost. In addition, some on-chip optical trapping systems based on the waveguide structure can reduce the volume to a certain extent, but desktop lasers are always chosen, which still result in large volumes[19,20].
![Optical levitation system based on one traditional desktop laser from the group of Pesce[18] (M, 45° mirror; L, lens; F, filter; P, polarizer).](/Images/icon/loading.gif)
Figure 1.Optical levitation system based on one traditional desktop laser from the group of Pesce[18] (M, 45° mirror; L, lens; F, filter; P, polarizer).
To solve these aforementioned problems, herein, we propose a compact levitation system that integrates the light source with a pair of miniature lenses and a micro-electro-mechanical system (MEMS) cavity. The miniature optical levitation system can trap one particle, the diameter of which ranges from a few to dozens of microns. The overall volume of this system is just . The proposed system may be a solution for the miniaturization of the optical levitation system under low precision and stiffness requirements, which can make it a promising optical levitation platform in the future. Using this system will enable some miniature sensors such as accelerometers and gyroscopes to meet the requirements of mechanical measurement with higher accuracy and smaller volume.
In this study, the characteristics of the laser diode beam are firstly analyzed. Second, the cavity containing micro-particles is prepared by the MEMS process, and the laser diode with a maximum output power of 100 mW at a wavelength of 808 nm is used as the optical trapping source. After the compact optical levitation system is set up, one 10-µm-diameter particle is levitated in the gas environment. Finally, the stiffness of this system is evaluated by analyzing vibration signals of the trapped particle. Compared with other optical levitation systems, it may provide a new miniaturized platform for a variety of inertial and mechanical sensors.
Sign up for Chinese Optics Letters TOC Get the latest issue of Advanced Photonics delivered right to you!Sign up now
2. Analysis of Laser Diode Beam Characteristics
As shown in Fig. 2(b), the output spot characteristics of the laser diodes are different from those of the standard Gaussian beams, so it is necessary to analyze the spatial optical field. In this section, the transverse and axial optical field distribution characteristics of the laser diode output beams are analyzed first, and then the optical field distribution of the actual output spot is tested with a beam quality analyzer.
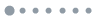
Figure 2.One edge emission laser (EEL) diode encapsulated in a transistor outline (TO). (a) Physical diagram of an EEL; (b) schematic diagram of optical field distribution.
2.1. Selection of laser diodes
Semiconductor laser diodes can be divided into edge emission laser (EEL) and vertical-cavity surface-emitting laser (VCSEL)[21] according to the structure of the chip. Although the VCSEL has a variety of performance advantages over the EEL, including low cost, high wavelength stability, and beam quality, it is not suitable for trapping one single dielectric particle in air due to its low output power and array arrangement. Therefore, we choose to use an EEL as the source in this system. The thermal effect of the high-power laser diode working for a long time will seriously affect the beam quality and stiffness of the optical trap; however, the addition of a heat sink will increase the volume of the system. Therefore it is necessary to comprehensively consider the influence of laser power, stiffness of the optical trap, and thermal effect. Based on the above considerations, an EEL with a wavelength of 808 nm and a maximum output power of 100 mW is selected.
2.2. Analysis of laser diode beam characteristics
The optical field emitted by the EEL is different from the scattering field of a standard Gaussian beam, which is divided into near- and far-fields according to the distance between the scattering field and the source. The distribution of near-field usually refers to the optical field distribution on the surface of the diode output cavity, and the distribution of the far-field usually refers to the optical field distribution after a distance from the surface of the output cavity. The near-field distribution of the single transverse-mode EEL is usually an elliptical spot with a long axis in the parallel direction and a short axis in the vertical direction.
Since the thickness of the active region is thin, the divergence angle of the far-field in the vertical direction () is larger, which is usually approximately 30°. It is approximately 10° in the parallel direction ().
Figure 3 shows the near- and far-field distributions of the simulated elliptical Gaussian beam.
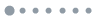
Figure 3.Distributions of light intensity across the cross section of the elliptical Gaussian beam along the direction of propagation.
The waist radius of the long axis on the output cavity surface is set as 3 µm, and the waist radius of the short axis is set as 1 µm. The elliptical beam gradually diverges with increasing propagation distance, but the divergence angles of the long and short axes are not consistent. This is the reason why the beam along the short axis diverges faster than that along the long axis. When the propagation distance reaches 5.2 µm, the length of the beam along the short axis is equal to that along the long axis. Figure 4 shows the variation of transverse light intensity of the elliptical Gaussian beam along the direction of propagation.
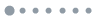
Figure 4.Variation of transverse light intensity of the elliptical Gaussian beam along the direction of propagation.
2.3. Test of output spot
The beam quality of the actual laser diode before beams are focused is evaluated intuitively by using the beam quality analyzer, and the distribution of the optical field is shown in Fig. 5. The entire picture of the spot cannot be analyzed, which is due to the large divergence angle of the diode when it is not focused. Consequently, the beam of the laser diode cannot directly trap one particle without focusing.
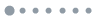
Figure 5.Optical field distribution of the laser diode in the experiment before focusing.
3. Design of Miniature Optical Levitation System Based on Laser Diode
3.1. Design and construction of a miniature optical system
As mentioned above, the beam of light must be focused so as to form an optical field with a strong gradient. Hence, one laser diode and a pair of lenses placed in opposite directions are adopted to comprise the miniature optical system, the schematic diagram of which is shown in Fig. 6. To decrease the packaging volume as much as possible, the diameter of the lenses is considered first. We finally choose a pair of lenses with a diameter of 6 mm, a focal length of 7 mm, and an equivalent numerical aperture (NA) of 0.28.
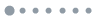
Figure 6.Schematic of the optical system.
The assembly drawing of the optical system including the source and a pair of lenses is presented in Fig. 7(a); its packaging volume is .
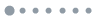
Figure 7.Optical system. (a) Assembly drawing; (b) photograph of the optical system.
As shown in Fig. 8, after being focused, the spot is roughly between the elliptical and rectangular light spots, and the distribution of the optical field is basically strong in the middle and weak on the outside. Judging from the results, the optical system has an ability to trap one particle.
3.2. Design and construction of the particle cavity
One vacuum chamber with a large volume is used in almost all of the optical levitation systems at present. Not only it is beneficial to achieve more accurate measurements of displacement and velocity information, but it can also reduce the impact of gas collisions on particles. This, however, is not suitable for micro-sized optical levitation systems with low vacuum degree and measurement accuracy requirements. Therefore, a cavity including micro-particles based on the MEMS process is designed in this system, and the main manufacturing process is shown in Fig. 9.
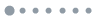
Figure 8.Optical field distribution of the laser diode in the experiment after beams are focused.
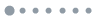
Figure 9.Manufacturing process of the MEMS particles cavity.
The physical diagram of the particles cavity is shown in Fig. 10. The volume of this cavity is .
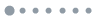
Figure 10.Photograph of the MEMS particles cavity.
The particles cavity adopts a “glass-silicon wafer–glass” structure, in which the silicon wafer is polished on both sides as the substrate. Owing to the thick silicon wafer, it is necessary to use an ultraviolet nanosecond laser to scribe both sides of the wafer to form a through cavity. One piece of heat-resistant glass and the lower surface of the silicon wafer are bonded by a one-sided anodic bonding process. After adding micro-particles, another piece of glass is tightly bonded with the upper surface of the silicon wafer to form a seal in the same way.
The optical levitation system is shown in Fig. 11.
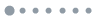
Figure 11.Optical levitation system. (a) Schematic diagram; (b) photograph of the miniature optical levitation system.
3.3. Experimental test setup of the optical levitation system
The experimental test setup of the miniaturized optical levitation system is shown in Fig. 12, which includes a particle trapping system, an observation system, and an optical detecting system with a four-quadrant photoelectric detector (QPD).
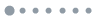
Figure 12.Experimental test setup of the optical levitation system. (a) Diagram of the optical path; (b) photograph of the experimental system.
The optical path of the particle trapping mainly includes one EEL and one particle cavity, on which the laser diode is focused after shaping by one pair of micro-aspherical lenses. In the observation path, the illuminating light is reflected to the micro-cavity through the spectroscope, and the particles are received by a charge-coupled device (CCD) after imaging through the high-NA objective lens. The signal test optical path is used to focus the laser scattered by the particle on the QPD center through one lens to realize the photoelectric signal test of the particle.
4. Experiment Results
4.1. Trapping performance test
To trap one particle in air, the focal plane of the objective lens, laser, and bottom of the MEMS cavity must first be adjusted at the same height. The vibration frequency of the ceramic piezoelectric sheet is then set to 100 kHz, and the excitation effect will force the particles to overcome their own gravity and van der Waals force. One particle will be trapped by the optical force until there is a blurred image of the trapped particle in the field of vision. Whether the particle is levitated can also be judged by adjusting the focal plane of the objective lens or the three-dimensional movement of the particle cavity.
Figure 13 shows the trapping and passive movement of one silica particle with a diameter of 10 µm in air.
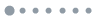
Figure 13.Trapping process of one SiO2 particle. (a) Silica is stably trapped; (b), (c) processes of moving the micro-particles cavity to the lower right.
4.2. Vibration performance test
To evaluate the optical trap stiffness of the system, the vibration signals of the particle must be tested. At present, the most common methods of particle position calibration include the CCD imaging method[22,23] and interferometry[24,25]. In this study, one QPD is used as the sensitive unit, and the interference spot is detected through back-focal-plane interferometry to realize the displacement measurement of the levitated particle. In order to avoid coupling of the displacement of the particle along the long and short axes of the elliptical beam, it is necessary to strictly align the optical spot axes with the X and Y axes of the detector. The sampling frequency of the QPD is 25.6 kHz, and the sampling time is 5 s. The displacement signal of the dielectric particle is shown in Fig. 14.
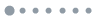
Figure 14.Measurement results of the dielectric particle displacement by the QPD. Displacement along (a) long axis and (b) short axis of the elliptical beam.
By analyzing the frequency spectrum of the displacement signal (Fig. 15), obvious environmental noise and electrical noise are observed at 24.1 and 50 Hz, respectively. After the dielectric particle is trapped, there are obvious vibration signals at 1136 Hz in the frequency spectrum of the X axis and 1275 Hz in the frequency spectrum of the Y axis.
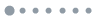
Figure 15.Frequency spectrum distributions of the X and Y axes of the QPD (a),(b) when no dielectric particle is trapped and (c), (d) when one dielectric particle is trapped.
5. Discussion
By using this optical levitation system, we can trap different-diameter particles by adjusting the power of the light source, which ranges from a few to dozens of microns. Owing to the smaller particles being subjected to a larger van der Waals force, the minimum diameter of the particles that can be trapped is 8 µm when the power of the laser is 115 mW. As the diameter of the particle increases, the gravity increases with a cubic index. So, the maximum diameter of the particle is 13 µm that can be trapped when the power of the laser is 140 mW.
Due to the instability of the diode power and the inhomogeneity of different media spheres, the observed signal covers 300–1400 Hz. According to the relationship between the stiffness and frequency, it can be estimated that the stiffness of the system for trapping one particle with a diameter of 10 µm is 1.47 and along the long and short axes, respectively. As expected, the stiffness of the long axis is lower than that of the short axis because of the smaller gradient. The experimental result shows that the optical levitation system based on a laser diode has a certain particle trapping ability. Besides, it can be tried to trap a nano-level particle by using this system in the future. Under this demand, it is necessary to increase the vacuum of chamber and use another way to excite the particles.
In a word, it will be a good choice for trapping a micron particle with low vacuum and measurement accuracy requirements.
6. Conclusions
The compact optical levitation system based on a laser diode described in this study has the advantages of small size and low cost that the traditional space optical levitation system lacks. Experimental results show that the proposed system can stably trap one micro-particle and obtains good test signals. Its optical system and MEMS cavity are packaged in the volume of , and it is also the smallest optical levitation system reported, to the best of our knowledge. To further improve its performance without increasing the overall volume of the system, the bonding process in a high vacuum or the addition of a laser cooling optical path can be used to further reduce the air damping and environmental noise. Hence, the optical levitation system based on a micro light source provides a new technological tool for additional research fields in the future, such as biological targeting therapy, micro molecular directional capture, and micro-mechanical and inertial sensing.