0 Introduction
With the development of science and technology, optical crystals and semiconductors are widely used in optical system design, gem identification, medicine, chemical engineering and other fields, especially the typical optical crystal Sapphire Crystal and the typical semiconductor material GaAs. The Sapphire Crystal is usually used in intelligent instruments, laser window materials, infrared military equipment and other regions. The use of Sapphire Crystal in military photovoltaic equipment is very wide. For example, when it used as a window material of a military photovoltaic device, it is necessary to accurately calculate the refractive index and transmittance to effectively transmit radiation of ultraviolet to medium infrared bands. GaAs is used in infrared light emitting diode, lasers and many other optoelectronics. GaAs is usually used as the material of solar cells, and the refractive index is a key parameter to the film layer design to affect the photoelectric conversion rate. High-precision measurement of refractive index of Sapphire Crystal and GaAs is meaningful for optical design and metrological inspection. The gem refractometer is commonly used in the gem identification field to measure the refractive index of Sapphire Crystal, and its accuracy is 10−3[1]. The book (Optical Handbook[2]) for the refractive index accuracy of GaAs is 10−2. Therefore, further research is needed to improve measurement precision of refractive index. Currently, the most accurate method for measuring refractive index is the minimum deviation angle method (10−6)[3-5], but it requires prismatic sample material, high sample requirements and high cost. In addition, the measurement equipment is huge and has strict environmental conditions, so it cannot be universally applied. Abbé refractometer widely used in industrial and laboratory and precision is 10−4, but the measurement range is between 1.3-1.7. The ellipsometry can be measured refractive index in a wide wavelength, but the accuracy is 10−2. The m-lines method is used to measure refractive index of the film by a prism coupler[6], providing an accuracy of 10−3. In contrast, interferometry has the advantages of simple sample material processing, wide measurement range, low cost and high precision. At present, the commonly used methods include Michelson interferometer[7-8], Fabry-Perot interferometer[9-10], Mach-Zehnder interferometer[11-12], and self-mixing interferometer [13], etc. These methods are dependent on laser intensity fringes by the sample material optical path change. If the contrast of interference fringes is reduced, the measurement resolution will be lower. Further, the whole measurement optical path is the dead path, so there are environmental interference including air flow and vibration for these interferometers, making measurement accuracy and repeatability easily affected by environment and laser power fluctuations.
In order to improve the accuracy of GaAs and Sapphire Crystal, the article decides to avoid environmental disturbances and overcome interference contrast problems, so the paper proposes the microchip laser feedback interferometry (MLFI) at 1064 nm to measure refractive index and thickness. In this paper, MLFI combines the quasi-common path structure and the frequency shifted optical feedback to realize the compensation of dead-distance error and the heterodyne modulation of laser intensity, so the impact of environmental interference is eliminated and the measurement accuracy is improved. Compared with traditional methods, the measurement method can simultaneously measure refractive index and thickness and only the material needs to be processed into flake rather than prism shape. The measurement accuracy of refractive index of GaAs and Sapphire Crystal (under ordinary light) has been improved. The precision of refractive index of GaAs and Sapphire Crystal are better than 10−3 and 10−4 respectively and thickness is 10−4 mm. Therefore, it is very suitable and meaningful to use MLFI to simultaneously measure refractive index and thickness for improving the measurement accuracy of GaAs and Sapphire Crystal.
1 Experiment system
The schematic diagram of experimental system is shown in Fig. 1. ML is a microchip Nd:YVO4 laser light source pumped by two same LDs and ML outputs two parallel laser beams. Both laser beams are fundamental transverse modes and linearly polarized single longitudinal modes. The working wavelength of these two lasers is both 1064 nm. The measurement mirror ME is a light wedge covered with copper foil, and its front surface is the reflective surface. Acousto-optic modulators (AOM1 and AOM2 are YSGMN from SIPAT) are placed in the optical feedback path to realize the frequency shifting. The reference mirror MR is also a light wedge covered with copper foil. It is placed between the two acousto-optic modulators and ME to eliminate feedback environmental interference. L1 and L2 are two lenses used to focus the light beams (B1 and B2) on MR and ME respectively. The light beams (B1 and B2) are reference and measurement light. S is the solid material sample which is polished thin wafer. S is located between MR and ME, and it is controlled to rotate by an electric controlled rotation stage (MRS211 from Beijing Beiguang Century Instrument Co., Ltd.). The photodetector PD contains two PIN photodiodes.
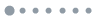
Figure 1.System for measuring based on laser feedback interferometry. ML: Nd:YVO4 microchip laser; BS: Beam splitter; PD: Photodetector; AOM1 and AOM2: Acousto-optic modulators; L1 and L2: Lens; W: Wollaston prism. MR: Reference mirror; S: Material; ME: Measurement mirror
Two beams of light emitted by the light source ML pass through AOM1 and AOM2 and are divided into eight beams. The optical path for differential frequency shift of two acousto-optic modulators is shown in Fig. 2. The output laser beam ② and ⑥ which underwent -1-order diffraction and +1-order diffraction are respectively used as reference light and measurement light, and the frequency shift amount is Ω (Ω2−Ω1). MR and ME can be adjusted so that the feedback light can return to the laser cavity passing through AOM1 and AOM2, so the total frequency shift amount of B1 and B2 are both 2Ω. Among them, the measurement light B2 through the Wollaston prism W is divided into two beams (ordinary ray and extraordinary ray), and it can be chosen which beam as the measurement light according to the anisotropy of materials. The two feedback optical signals B1 and B2 after heterodyne modulation are respectively received by the two PIN photodiodes and converted into electrical signals. According to the rate equation model, the power modulation of the frequency shift laser feedback after the light returning to the laser is given by[14]
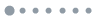
Figure 2.Schematic diagram of optical path for differential frequency shift of acousto-optic modulators. ①~⑧: Eight output laser beams
$ \Delta I(2\varOmega )=\kappa G(2\varOmega )\mathrm{cos}\left[2\pi (2\varOmega )t-\varphi +{\varphi }_{s}\right] $ (1)
where ΔI is the intensity of laser B1 and B2 respectively, κ is feedback light strength factor, G is the gain amplification factor, which is related to the value of frequency shifting, ϕ is the external cavity phase (ϕm or ϕr), and ϕs is fixed phase. For the material with large internal absorption and low transmittance, the system is based on the high sensitivity characteristics of frequency shifting light feedback, so the reduction of the interference fringe contrast will not cause the measurement resolution to decrease.
According to the equation, the wave of intensity modulation curve is cosine, and the modulation frequency is the frequency shift of feedback light (2Ω). As the material is rotated by an electric controlled rotation stage, the phase changed by the optical path change. Δϕr is reference signal between ML and MR, and Δϕm is measurement signal between ML and ME. Δϕm − Δϕr is compensation for impact of environmental disturbances. In the experiment, the driving frequency of AOM1 and AOM2 are 70 MHz and 70.4 MHz respectively, the power modulation frequency (2Ω) of the reference light and the measurement light are both 800 kHz. The transparent surface is coated by the antireflecting film to prevent the laser from being reflected by the edge surface of the acousto-optic medium to form feedback.
2 Experiments and results
When electric rotation stage is controlled to rotate, the optical path changes in the material with rotating. As shown in Figure 3, when the angle between the normal line of the material surface and the light is θ, the optical distance L in the material is
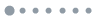
Figure 3.Schematic diagram of the sample material optical path
$L = \frac{{nd}}{{\cos i}} + {n_0}x - \frac{{{n_0}d}}{{\cos i}}\cos (q - i)$ (2)
where d is the thickness of material, n denotes the refractive index to be measured, i denotes the refraction angle in the material, n0 denotes the air refractive index, and x is geometric length from optical position incident on the material to the measurement mirror. According to Snell equation [15]
$ {n}_{0}\mathrm{sin}\theta =n\mathrm{sin}i $ (3)
derive as
$L{\kern 1pt} = {n_0}x - {n_0}d\cos \theta + d\sqrt {{n^2} - {n_0}^2{{\sin }^2}\theta } $ (4)
Assuming that the angle between the surface normal of material and the beam before rotation is θ0, and the angle after rotation is θ, the optical path change ΔL is
$ \begin{split} \Delta L =&\dfrac{\lambda }{{2\pi {n_{\rm{0}}}}}(\Delta {\phi _m} - \Delta {\phi _r}) =\Bigg[\sqrt {{n^{\rm{2}}} - {n_{\rm{0}}}^{\rm{2}}{{\sin }^{\rm{2}}}\theta } - {n_{\rm{0}}}\cos \theta - \\ & \sqrt {{n^{\rm{2}}} - {n_{\rm{0}}}^{\rm{2}}{{\sin }^{\rm{2}}}{\theta _{\rm{0}}}} + {n_{\rm{0}}}\cos {\theta _{\rm{0}}}\Bigg]{\kern 1pt} {\kern 1pt} \\ \end{split} $ (5)
where the optical path change Δϕr of reference signal comes from the air disturbance between ML and MR and the thermal effect of the acousto-optic modulators, and the optical path change Δϕm of the measurement signal comes from the air disturbance between ML and ME, thermal effect and the optical path change. When the material is rotated, θ and ΔL selected at multiple angles are substituted into equation (5) to solve this over-determined equation expressed by equation (6). It excludes the effect of thickness measurement uncertainty on refractive index accuracy.
$\left. \begin{gathered} \Delta {L_1} = d\left[\sqrt {{n^{\rm{2}}} - {n_{\rm{0}}}^{\rm{2}}{{\sin }^{\rm{2}}}{\theta _1}} - {n_{\rm{0}}}\cos {\theta _1} - \sqrt {{n^{\rm{2}}} - {n_{\rm{0}}}^{\rm{2}}{{\sin }^{\rm{2}}}{\theta _{\rm{0}}}} + {n_{\rm{0}}}\cos {\theta _{\rm{0}}}\right]{\kern 1pt} {\kern 1pt} \\ \Delta {L_2} = d\left[\sqrt {{n^{\rm{2}}} - {n_{\rm{0}}}^{\rm{2}}{{\sin }^{\rm{2}}}{\theta _2}} - {n_{\rm{0}}}\cos {\theta _2} - \sqrt {{n^{\rm{2}}} - {n_{\rm{0}}}^{\rm{2}}{{\sin }^{\rm{2}}}{\theta _{\rm{0}}}} + {n_{\rm{0}}}\cos {\theta _{\rm{0}}}\right]{\kern 1pt} {\kern 1pt} \\ \Delta {L_3} = d\left[\sqrt {{n^{\rm{2}}} - {n_{\rm{0}}}^{\rm{2}}{{\sin }^{\rm{2}}}{\theta _3}} - {n_{\rm{0}}}\cos {\theta _3} - \sqrt {{n^{\rm{2}}} - {n_{\rm{0}}}^{\rm{2}}{{\sin }^{\rm{2}}}{\theta _{\rm{0}}}} + {n_{\rm{0}}}\cos {\theta _{\rm{0}}}\right]{\kern 1pt} {\kern 1pt} \\ {\rm{ }} \vdots \\ \Delta {L_x} = d\left[\sqrt {{n^{\rm{2}}} - {n_{\rm{0}}}^{\rm{2}}{{\sin }^{\rm{2}}}{\theta _x}} - {n_{\rm{0}}}\cos {\theta _x} - \sqrt {{n^{\rm{2}}} - {n_{\rm{0}}}^{\rm{2}}{{\sin }^{\rm{2}}}{\theta _{\rm{0}}}} + {n_{\rm{0}}}\cos {\theta _{\rm{0}}}\right]{\kern 1pt} {\kern 1pt} \\ \end{gathered} \right\} \Rightarrow n,d$ (6)
In the experiment, the material S is polished thin wafer which is Sapphire Crystal or GaAs. Because sapphire is an anisotropic uniaxial crystal, it has two refractive indices. Choose ordinary ray of W as the measurement light B2. The thickness of Sapphire Crystal and GaAs are 0.302 mm and 0.686 mm respectively measured by a micrometer. The air sensor is used to detect the air in the experiment. The indoor temperature of Sapphire Crystal is 23.34 ℃, the air pressure is 101.93 kPa, the relative humidity is 18.5%, and the air refractive index n0 is calculated as 1.0002678 by the modified Edlén equation[16]. For GaAs, they are 23.60 ℃, 101.89 kPa, 16.5%, and 1.0002675. Considering the transmittance of the materials and reducing the measurement uncertainty requirement, decide that Sapphire Crystal is rotated from 0° to 30° with pausing every two degrees, and GaAs from 0° to 20° with pausing every angle. The optical path difference of rotating material at each angle is measured 20 times within 20 seconds. The average optical path difference is shown in Table 1 and Table 2.

Table 1. The average optical path difference in Sapphire Crystal with angle
Table 1. The average optical path difference in Sapphire Crystal with angle
Rotation angle/(°) | Optical path change/nm | Rotation angle/(°) | Optical path change/nm | 1 | 145 | 11 | 8924 | 2 | 354 | 12 | 10693 | 3 | 689 | 13 | 12594 | 4 | 1186 | 14 | 14502 | 5 | 1827 | 15 | 16679 | 6 | 2598 | 16 | 19042 | 7 | 3558 | 17 | 21524 | 8 | 4674 | 18 | 24134 | 9 | 6015 | 19 | 26870 | 10 | 7482 | 20 | 30037 |
|

Table 2. The average optical path difference in GaAs with angle
Table 2. The average optical path difference in GaAs with angle
Rotation angle/(°) | Optical path change/nm | Rotation angle/(°) | Optical path change/nm | 2 | 69 | 18 | 6550 | 4 | 270 | 20 | 8047 | 6 | 700 | 22 | 9811 | 8 | 1275 | 24 | 11703 | 10 | 2036 | 26 | 13771 | 12 | 2896 | 28 | 16006 | 14 | 3937 | 30 | 18365 | 16 | 5158 | | |
|
Substitute the experiment data in Table 1 and Table 2 and n0 into equation (5) by fitting refractive index and thickness. The theoretical curve and experimental data points are drawn in Fig. 4(a). It is shown that, consistent with the experimental data, the solution of the Sapphire Crystal n is 1.7551, d is 0.3017 mm, the GaAs n is 3.4653, and d is 0.6862 mm. The difference between theoretical fit data and experimental data of optical path change at every angle is presented in Fig. 4(b), and the difference range is from −80-80 nm.
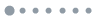
Figure 4.(a) Theoretical and experimental data of optical path change of two materials with angle of rotation; (b) Difference between theoretical fit data and experimental data
There are five times of the measurement of Sapphire Crystal and GaAs, and the measurement results are presented in Table 3. Calculate the measurement average value (refractive index and thickness) and type A evaluation of uncertainty[17](that is, the standard deviation calculated by the Bessel equation[18]). From Table 3, the refractive index of Sapphire Crystal is 1.7550±0.0005. The reference value is based on the value calculated by Sellmeier equation[2], which is 1.7545, so the deviation of the experimental data with the reference data is 0.0005. The measurement accuracy of Sapphire Crystal reaches 10−4 and the material does not need to be processed into prismatic shape. However, the accuracy of ellipsometry method and m-lines method are 10−2 and 10−3 respectively, and the common reflective gem refractometer is 10−3. The refractive index of GaAs is 3.4719±0.0039. The reference refractive index value is 3.4727 which is calculated by Sellmeier equation[19], so the deviation of the experimental data with the reference data is 0.0008. The measurement accuracy range of GaAs is between 10−3-10−4. However, the ellipsometry method accuracy is 10−2 and GaAs is beyond the measurement range of Abbé refractometer. From Table 3, the thickness of Sapphire Crystal is (0.3022±0.0004) mm, and the thickness measured by micrometer is (0.302±0.001) mm. The thickness of GaAs is (0.6861±0.0001) mm, and the thickness measured by micrometer is (0.686±0.001) mm. Therefore, the results are satisfactory and the accuracy has been improved.

Table 3. Measurement results
Table 3. Measurement results
Number
| Sapphire Crystal | | GaAs | n | d/mm
| n | d/mm
| 1 | 1.7553 | 0.3028 | | 3.4653 | 0.6862 | 2 | 1.7551 | 0.3026 | 3.4759 | 0.6861 | 3 | 1.7539 | 0.3019 | 3.4739 | 0.6860 | 4 | 1.7554 | 0.3018 | 3.4696 | 0.6859 | 5 | 1.7551 | 0.3017 | 3.4749 | 0.6861 |
|
There are several reasons for refractive index measurement error Δn. First of all, the material composition, processing technology and surface morphology are the main reasons for the measurement error Δn. Among them, the main component of Sapphire Crystal is Al2O3, which contains the trace elements titanium (Ti4+) or iron (Fe2+), and different doping concentrations lead to different refraction effects. Due to the different crystal growth process, the melting temperature, the number of pulling times and other steps are also different. However, the temperature, pulling number and other steps will affect refraction results. Secondly, both materials are polished wafers, so the parallelism, roughness and uniformity of their surfaces will affect the measurement accuracy and the corresponding Δn cannot be accurately calculated. In addition, the air refractive index and the laser wavelength will vary with the ambient temperature. In a normal laboratory environment, the refractive index of air changes less than 10−5, and Δn is less than 7×10−6. The frequency-stabilized microchip laser has the wavelength drift Δλ less than 2.6×10−4 nm, and Δn is only 1.94×10−7. Finally, GaAs is a semiconductor material, and refractive index of semiconductor material is complex number because its conductivity is not zero. This article is measuring the real part of the complex refractive index. However, when light is incident on the GaAs sheet obliquely at a certain angle, the extinction coefficient of the semiconductor material (that is, the imaginary part of the complex refractive index) will affect the real part, thereby affecting the measurement data of refractive index.
3 Summary
In conclusion, in order to improve the measurement accuracy of refractive index of GaAs and Sapphire Crystal, the paper use LD-pumped microchip Nd:YVO4 laser feedback interferometry at 1064 nm to simultaneously measure refractive index and thickness. The experimental results are satisfactory. The experimental measurement uncertainty of refractive index of two materials less than (or equal to) 0.0005 and 0.0039 respectively and the deviation from reference value is lower than 0.0008. The thickness measurement uncertainty is less than 0.0004 mm. The precision of refractive index of GaAs and Sapphire Crystal are 10−3 and 10−4 respectively and thickness is 10−4, so the measurement accuracy has been improved. The measurement method is high sensitivity, high precision and high stability. In particular, the measurement is simultaneous and only the material needs to be processed into flake rather than prism shape. Therefore, it is very suitable and meaningful to use the measurement system to measure for improving the accuracy of refractive index measurement. The Sapphire Crystal is usually used in intelligent instruments, laser window materials, infrared military equipment and other regions. GaAs is used in infrared light emitting diode, lasers and many other optoelectronics. High-precision measurement of refractive index and thickness of Sapphire Crystal and GaAs is of great significance to infrared region, optical design and metrological inspection. In the future, it is our duty to optimize this system to other wavelengths and other materials. Moreover, further improving refractive index measurement accuracy of Sapphire Crystal and GaAs is necessary.