I. INTRODUCTION
Dynamic fragmentation is a key phenomenon that occurs during high-velocity impacts and explosive events, in which a compression wave interacts with a free surface, resulting in tensile stress and then fracture in the target.1–14 By investigating the fragmentation behavior of materials, one can gain insights into energy dissipation, mass distribution, and the propagation of shock waves. This knowledge is invaluable for designing protective materials and structures that can withstand extreme conditions, such as ballistic impacts or explosive blasts. However, studying dynamic fragmentation presents significant challenges. The complex nature of fragmentation processes necessitates sophisticated experimental techniques and advanced computational models. Additionally, capturing the dynamic fragment distribution accurately and precisely characterizing the fragment properties pose inherent difficulties.13–18 Despite these challenges, the study of dynamic fragmentation in the realm of shock physics promises groundbreaking discoveries and applications in fields such as defense, aerospace, and materials science.19,20
Dynamic fragmentation involves the rapid formation and propagation of fragments under extreme forces, making it difficult to capture and analyze the process accurately. The high velocities, energies, and time scales involved pose significant challenges for experimental observation and measurement. To date, a variety of time-resolved techniques have been developed to probe dynamic fragmentations. For instance, high-speed imaging and X-ray radiography are frequently used to capture the fragmentation process, providing valuable information on fragment formation, propagation, and interaction.10,21–23 Laser velocimetry is widely employed to detect the speed of the moving fragments.24–26 It was a long-term debate on the phase nature (solid, liquid, or partially melted) of the fragments has long been a subject of debate.23,27 Most recently, in situ X-ray diffraction (XRD) based on synchrotron radiation has been utilized to characterize the lattice structure and demonstrate the potential to discriminate phase changes during fragmentation events.28,29 Experimental determination of the temperature, one of the basic thermodynamic properties of dynamic fragmentation, however, remains a challenge. Although pyrometry has recently been employed for in situ measurements of the temperature of high-speed moving fragments,24,30,31 this method is limited by difficulties in determining the emissivity and excluding the influence of the bulk material, resulting in possible confusion when extracting a reliable temperature of the fragments. Additionally, as the temperature decreases, thermal radiation is red-shifted, even toward the far-infrared region, accompanied by a decrease in radiation flux. Owing to the limitations of far-infrared detectors, this makes transient measurement of relatively low temperatures by fast optical pyrometry extremely challenging. Thus, there is an urgent need for the development of more reliable techniques to measure temperature during dynamic fragmentation.
To this end, we develop in this work an in situ XRD technique based on a high-power laser to probe the phase and temperature of laser-driven dynamic fragmentation in tin. Tin has been selected here for study owing to its well-known high-pressure properties, such as its equation of state.29,32–35 Experiments demonstrate the feasibility of simultaneously determining the phase and temperature of the fragments by analyzing their diffraction pattern. More interestingly, the results reveal that the measured temperature of the fragments may deviate from the widely accepted isentropic release assumption, leading to a 100–200 K higher temperature than expected, owing to the plastic work released during dynamic fragmentations. This finding is confirmed by large-scale molecular dynamics (MD) simulations.
II. EXPERIMENTAL DETAILS
The experiments were conducted on the SG-III Prototype laser facility using a laser driven X-ray source.36,37Figure 1(a) illustrates the setup featuring the modified TARDIS diffractometer.37 The interior of the diffractometer is displayed here after removal of the top cover and half-front lid. As depicted in Fig. 1(b), the target assembly was positioned within the concealed top lid, consisting of a 258 μm-thick Sn sample, a 20 μm-thick aluminum ablator, and a 20 μm-thick tantalum mask with a rectangular aperture measuring 2 × 0.6 mm2. The purpose of the mask was to isolate a specific region for laser shock driving and facilitate the X-ray probe. The Sn sample (with purity exceeding 99.9%), characterized by atomic force microscopy (AFM) as shown in Fig. 1(c), possessed an overall root mean square (RMS) surface roughness of less than 0.6 μm. This particular surface finish effectively prevented the generation of Richtmyer–Meshkov instability-induced ejecta,23 enabling controlled experiments to be performed. During the experimental procedure, a tunable energy driving laser (of wavelength 351 nm and square pulse duration 3 ns, and with a distributed phase plate of diameter 3 mm) was employed to induce shock waves within the target situated at the top cover, leading to dynamic fragmentation in the sample. At specified delay times Tdelay, an X-ray pulse (Fe-Heα emission with a wavelength of 1.85 Å) was generated by the interaction between four 800 J, 1 ns short-pulse lasers and 10 μm-thick iron foil. This X-ray pulse then passed through a 0.15 mm-diameter collimating aperture located in the front lid and was diffracted from the head part of the fragments, as shown in Fig. 1(d). The X-ray radiography of laser-driven dynamic fragmentation (in the form of a debris cloud) in tin was taken at a breakout pressure of 49 GPa and a delay time of 2 μs. Image plates (IPs) were used for recording the X-ray diffraction pattern.
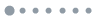
Figure 1.(a) Schematic of experimental setup. Dynamic fragmentation was induced by a 3 ns-long driving laser, and the X-ray probe pulse was generated by the interaction between four 1 ns-long laser pulses and iron foil. IPs were used to record the XRD pattern. (b) Diagram of assembled targets used in the experiments. (c) AFM image of the tin’s free surface to show its roughness. (d) X-ray radiography of dynamic fragmentation in tin at a breakout pressure of 49 GPa and a delay time of 2 μs.
Note that the breakout pressure Pbk was determined from a calibration experiment and the model of Phipps et al.,38 according to which , where I0 is the laser energy. Although this model is regarded as a somewhat rough, old, and highly empirical law, its validity for estimating shock pressure has been demonstrated on an aluminum ablator.39 Using the calibrated relationship between breakout pressure and laser driving energy, we could determine breakout pressures of 15 and 36 GPa corresponding to the laser energies of 381 and 959 J, respectively, used in the experiments.
III. RESULTS AND DISCUSSION
Figures 2(a) and 2(b) present the diffraction pattern and its azimuthal integration for dynamic fragmentation taken at a delay time of 1 µs and a breakout pressure of 15 GPa. It can be seen that in addition to the diffraction peak due to the Ta collimator, the diffraction peaks of the Sn fragments are evident, with their positions being consistent with the β-Sn (I41/amd) phase, which is stable at ambient pressure. This suggests that the pressure in the Sn fragments has been completely released. In addition to sharp peaks of crystalline Sn, two broad diffuse scatterings are also clearly visible at high and low azimuthal angles, indicating the possible presence of liquid Sn. Thus, the Sn fragments are partially melted when released from the breakout pressure of 15 GPa. Taking solid Sn, liquid Sn, and solid Ta into account, we fitted the diffraction curve using the PeakFit toolkit. The experimental result was perfectly reproduced by this fitting, in which the contribution of liquid Sn is in good agreement with the diffraction curve of molten Sn at (530 ± 50) K, which is close to the melting temperature.
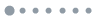
Figure 2.In situ XRD results for dynamic fragmentation in tin. (a) and (b) Diffraction pattern and its azimuthal integration at a delay time of 1 μs and a breakout pressure of 15 GPa. (c) and (d) Diffraction pattern and its azimuthal integration at a delay time of 0.58 μs and a breakout pressure of 36 GPa. The static X-ray diffraction profiles of liquid tin at 530 and 930 K are plotted as red curves for comparison.
Figures 2(c) and 2(d) present the diffraction pattern and its azimuthal integration for dynamic fragmentation taken at a delay time of 0.58 μs and a breakout pressure of 36 GPa. In remarkable contrast to the previous case, only two broad peaks can be clearly observed, which is a signature of complete melting. More interestingly, a peak shoulder appears at q = 2.8 Å−1, indicating the anomalous characteristics of molten Sn.40,41 On the basis of a direct comparison with the static diffraction profiles of liquid Sn,40 the temperature of molten fragments is determined to be (930 ± 50) K.
It is worth noting that the breakout pressure of 15 GPa, at which partially melting occurs, is much lower than the widely accepted initial melting pressure of 19 GPa at thermodynamic equilibrium. A calculation of multiphase equations of state based on an automated calibrated modeling method has been carried out to estimate the release temperature of shocked tin from Hugoniot states.33 As shown in Fig. 3, after isentropic release from the shocked states at 36 and 15–0 GPa, the temperature of shocked tin decreases monotonically to 750 and 502 K, respectively. Both of these values are lower than the experimental results. In particular, the latter is lower than the melting temperature of 505 K at ambient pressure, suggesting that the tin released from the breakout pressure of 15 GPa should remain in the solid state, which is in disagreement with experimental observations.28,29,35,42 Actually, melting at lower pressures has also been observed in other laser shock experiments, in which a velocity interferometer system for any reflector (VISAR) was used to measure the free-surface velocity of a sample target and a shock-recovery technique was used for post-mortem characterization.13,43,44 The results demonstrated that with a breakout pressure larger than 12 GPa, the recovered Sn samples showed clear evidence of melting, associated with a drop in the tensile strength. These observations were attributed to laser preheating, the influence of the polycarbonate used as shield plates, and unknown dynamic mechanisms. Here, we can safely exclude the first two factors because of the low ablation pressure45 and the in situ XRD technique used. Thus, we focus on the possible contribution of dynamic processes.
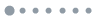
Figure 3.Isentropic release temperature of shocked tin from Hugoniot states calculated using multiphase equations of state based on an automated calibrated modeling method.
To understand the discrepancy between experiments and theoretical calculations, it is important to recall the basic assumption used in the calculations, namely, that the release process is isentropic and thus the contribution of plastic work is ignored. However, as a matter of fact, the conversion of plastic work into heat could significantly increases the temperature, resulting in a deviation from the isentropic release path. In particular, owing to the ultrahigh strain rate ( > 107 s−1) induced by laser loading, plastic work could be several times larger than that in plate-impact experiments,13,46–48 leading to an even higher temperature in the fragments.49,50 This may explain why lower shock pressures for release melting have been observed in laser-shock experiments than in plate-impact experiments.
We can roughly estimate how much plastic work is converted into heat (ΔT · CV) to accelerate the melting process at the breakout pressure of 15 GPa by51where λ is the melting fraction, Tm is the melting temperature, CV is the specific heat at constant volume, and ΔS is the entropy change at the melting temperature. As shown in Fig. 2(b), the coherent scattering intensity (integrated area) ratio between the liquid and crystal parts is about 0.72(±0.05):0.28(±0.05). Considering the smaller coherent scattering cross-section of the liquid phase, it is inferred that λ should be larger than 0.5. Thus, the estimated ΔT is at least 100 K, which turns into the latent heat of melting. The contribution of plastic work during dynamic processes therefore cannot be ignored, and this can raise the release temperature by more than 100 K in the single-phase region.
To further clarify this dynamical mechanism, we conducted MD simulations using the Large-scale Atomic/Molecular Massively Parallel Simulator (LAMMPS) code.52 In our simulations, we employed the embedded-atom-method (EAM) potential developed by Sapozhnikov et al.53 for tin. Figure 4 shows the simulation results. When shock compression is induced by plate impact, the shock wave can be seen as a square wave. The shock release follows an isentropic path, where the pressure decreases nearly monotonically from its maximum to zero, as illustrated by the dashed lines in Figs. 4(b) and 4(d). Concurrently, the sample temperature decreases from its maximum to 350 and 575 K. However, in these experiments, shock compression is driven by a laser shock. As the unsupported pressure pulse traverses the target, the compression front steepens and the release wave spreads, resulting in an approximately triangular shape. When the shock wave reaches the free surface, its reflection from that surface immediately produces a rarefaction front. The interaction of this reflected wave with the incident unloading wave gives rise to tensile stresses over a layer beyond the free surface. When the tensile forces generated by the reflected wave are strong enough, the tensile damage starts to nucleate, and small voids will grow. When nucleation of tensile damage occurs, the temperature decreases to its lowest value. Subsequently, the kinetic and strain energies are transferred into interfacial and thermal energies during the nucleation and growth of voids, leading to an increase in the temperature. This phenomenon is depicted by the black lines in Figs. 4(b) and 4(d). According to the MD simulation, the temperature of the tensile region will be about 100–250 K higher than that released along the isentropic line, as indicated by the red lines in Figs. 4(b) and 4(d), aligning with our experimental findings.
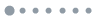
Figure 4.MD simulation results for tin under dynamic compression with square and triangular stress profiles. (a) and (b) Results at a breakout pressure of 15 GPa. (c) and (d) Results at a breakout pressure of 36 GPa. Dashed and solid lines represent the cases of square-wave and triangular-wave loading, respectively.
IV. CONCLUSION
In summary, we have developed a novel method for diagnosing the phase and temperature of high-speed moving particles using in situ XRD. By applying this method to tin fragments generated by laser shock loading, we have been able to gain valuable insights into impact-driven dynamic fragmentation. In comparison with traditional approaches (such as the use of pyrometers), our temperature diagnostic method provides more reliable and accurate data, allowing us to obtain the body temperature of a specified area. By targeting the head of the fragments, we have discovered a temperature increase of more than 100 K compared with isentropic release. These findings indicate that plastic work, released by tensile damage, can have a significant impact on material response during shock release. These results have profound implications for understanding material behavior under high pressures and strain rates, underscoring the necessity for further investigation in this domain. Enhancing our understanding of the effects of plastic deformation on the thermodynamic behavior of materials may enable the development of more precise models for predicting material responses under extreme conditions.
ACKNOWLEDGMENTS
Acknowledgment. We acknowledge Sai Jin and Zhijun Li for experimental support and thank Fengchao Wu for helpful discussions. This work was financially supported by the National Natural Science Foundation of China (Grant Nos. 12072331, 11902308, and 12274383) and the CEAP Foundation (Grant Nos. CX20210012 and CX2019002).