Metal halide perovskites are promising materials for solar cells because of high power conversion efficiency (PCE), tunable bandgap, high defect tolerance, long carrier diffusion length, and low-cost fabrication[1−7]. The PCE for perovskite solar cells (PSCs) reaches 26.14% for single-junction cells, 29.1% for perovskite/perovskite tandem cells and 33.9% for perovskite/silicon tandem cells, being comparable to that for silicon and other thin-film solar cells[8−10]. Perovskite solar cells have been made by solution methods including spin-coating, blade coating and printing[11, 12]. Alternatively, vapor depositions featuring “gas−gas” or “gas−solid” chemical reaction include co-evaporation, sequential evaporation, and chemical vapor deposition (CVD), needing less or no solvent for device fabrication[13−16]. The co-evaporation and sequential evaporation methods are usually performed under high vacuum for the deposition of perovskite films. By contrast, CVD method is normally operated under low vacuum[17, 18], which not only eliminates the influence of solvent and external environment, but also reduces the cost, offering an efficiency of 21.98% (Fig. 1).
Though promising for PSCs fabrication, the efficiency for CVD-made PSCs and PSMs still lags far behind solution-processed devices because of the residue PbI2, oxygen vacancy defects and high energy barrier from PbI2 to perovskite phase[30]. CVD technique can be regarded as a two-step deposition, in which the initial PbI2 layer is expected to react with organic halide vapor to form perovskite films. The volume expansion from lead halide to perovskite phase impedes organic halide vapor to penetrate into bottom lead halide layer, resulting in large amounts of unreacted lead halide[31]. The residue lead halide in devices will act as defects, which not only deteriorate device performance, but also accelerate the degradation of perovskite films and devices[32]. To address these issues, Tong et al. introduced NH4Cl into PbI2 layer at the first step to form PbI2 adduct, which can greatly low the phase transition energy barrier, promoting the complete phase conversion of PbI2 to MAPbI3 perovskite phase[33]. The oxygen defects originated from the oxygen loss in the process of CVD[34]. For conventional CVD-made PSCs, the device configuration is mainly n−i−p structure, in which TiO2 and SnO2 are used as electron-transport layer (ETL). The low pressure and continuous pumping during film formation will inevitably cause the oxygen loss, which creates more defects at ETL/perovskite interface, leading to more carrier recombination[21, 27, 35]. Qiu et al. used C60 as the buffer layer to modify SnO2 surface, mitigating the surface defects in PSCs and PSMs[27, 35]. Similarly, Tong et al. introduced potassium sulfamate (H2KNO3S) as the bridge between ETL and perovskite film, which can not only greatly reduce the defects at SnO2/perovskite interface, but also passivate the uncoordinated Pb2+ in perovskite, favoring carrier extraction and increasing photocurrent[21]. Tong and coworkers developed the intermediate phase and seed assisted growth strategy to control perovskite crystal growth and reduce the energy barrier, yielding a record efficiency of 21.98% for the cells, 16.16% for 5 × 5 cm2 module and 12.12% for 10 × 10 cm2 module, respectively[21]. The devices showed T80 lifetime over 4000 h for unencapsulated devices under one sun.
CVD fabrication includes lead halide deposition (PbX2, X = I, Br, Cl) and organic halide deposition (i.e., MAI, FAI) (Fig. 2)[19−22]. In 2014, Qi et al. used CVD to prepare MAPbI3−xClx films, in which PbCl2 layer was first deposited in vacuum chamber, followed by MAI evaporation in double-zone furnace with a low pressure of 100 Pa[23]. The devices delivered a PCE of 11.8% with long-term storage stability over 1100 h. Later, Luo et al. developed a low-pressure CVD method to make MAPbI3 films, in which spin-coated PbI2 films and MAI powders were placed in separated zones in furnace under low pressure[24]. The as-prepared MAPbI3 films were annealed in a humid environment (RH ~60%) and the resultant devices gave a PCE of 12.73%. CVD method not only greatly improves device stability, but also significantly eliminates humidity influence to deposition. Yin et al. proposed a vapor-assisted crystallization for making MAPbI3 films, and the devices gave an efficiency over 18%[20]. Tong et al. developed a vapor doping technique in combination with vacuum evaporation and CVD to make perovskite films with gradient bandgap, in which CsBr was introduced into perovskite films to obtain Cs0.15FA0.85PbI2.85Br0.15 films. The devices gave a PCE of 18.22% with long-term stability[25]. CVD technique also shows potential in making perovskite solar modules (PSMs). The fast chemical reaction of conventional solution methods and handling issues make its application more challenging in manufacturing PSMs. In contrast, CVD creates uniform pressures for organic halide (i.e., MAI and FAI) evaporation and mild molecular diffusion of organic halides vapor, enabling to achieve uniform large-area perovskite films and high reproducibility[26]. Qiu, Jiang, Qi, and coworkers developed hybrid CVD for scalable fabrication of Cs-FA based perovskite solar modules with sizes of 12, 22.8, and 91.8 cm2 (PCEs of 14.7%, 12.03%, and 9.34%), respectively (Figs. 3(a)−3(c))[27−29].
![(Color online) (a) 5 × 5 cm2 PSM made by CVD. Reproduced with permission[28], Copyright 2019, Wiley-VCH. (b) 10 × 10 cm2 PSM made by CVD. Reproduced with permission[27], Copyright 2019, the Royal Society of Chemistry. (c) 5 × 5 cm2 PSM made by rapid CVD. Reproduced with permission[22], Copyright 2020, the Royal Society of Chemistry.](/Images/icon/loading.gif)
Figure 3.(Color online) (a) 5 × 5 cm2 PSM made by CVD. Reproduced with permission[28], Copyright 2019, Wiley-VCH. (b) 10 × 10 cm2 PSM made by CVD. Reproduced with permission[27], Copyright 2019, the Royal Society of Chemistry. (c) 5 × 5 cm2 PSM made by rapid CVD. Reproduced with permission[22], Copyright 2020, the Royal Society of Chemistry.
In short, CVD method features uniform film, less solvent, low cost, and scalable fabrication. The efficiency for CVD-made devices needs improvement. More research on phase transition, film growth and interface defects are required.
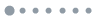
Figure 1.(Color online) Advances of CVD-made PSCs in lab scale.
![(Color online) (a) All vapor based CVD. Reproduced with permission[23], Copyright 2014, the Royal Society of Chemistry. (b) Hot air flow assisted CVD. Reproduced with permission[20], Copyright 2016, the Royal Society of Chemistry. (c) Seed-assisted CVD. Reproduced with permission[21], Copyright 2023, Wiley-VCH. (d) Rapid CVD. Reproduced with permission[22], Copyright 2020, the Royal Society of Chemistry.](/Images/icon/loading.gif)
Figure 2.(Color online) (a) All vapor based CVD. Reproduced with permission[23], Copyright 2014, the Royal Society of Chemistry. (b) Hot air flow assisted CVD. Reproduced with permission[20], Copyright 2016, the Royal Society of Chemistry. (c) Seed-assisted CVD. Reproduced with permission[21], Copyright 2023, Wiley-VCH. (d) Rapid CVD. Reproduced with permission[22], Copyright 2020, the Royal Society of Chemistry.