As the critical component in low-voltage switching device, Ag-based electrical contacts are widely applied in contactors, breakers and relays, etc. The service life of these devices largely depends on the properties of the electrical contact material[1]. The conventional material “Ag/CdO” has long been preferred because of its outstanding contacting and arc extinction properties since the middle of last century. However, the toxicity of CdO causes serious pollution problems, restricting its applications[2]. In the past few decades, Cd-free electrical contact materials, such as Ag/SnO2, Ag/ZnO, Ag/C, Ag/Ni, have been studied extensively[3,4,5,6,7]. These substitutes cannot yet emulate Ag/CdO in terms of temperature rise, contact resistivity, machinability, arc erosion resistance, etc. Therefore, environment-friendly alternative with properties matching up CdO is in high demand.
Over the past decades, MAX phase[8,9,10], combining excellent properties of metal and ceramic, has been widely investigated in various fields[11,12,13,14,15,16]. As a representative member of MAX family, Ti3AlC2 has been used to reinforce Ag matrix as the electrical contact material[17,18,19,20,21]. However, the electrical resistivity of the Ag/Ti3AlC2 composite is not satisfactory, which is initially attributed to the inter-diffusion between Al layer and Ag matrix[22]. 2011, Gogotsi and Barsoum[23,24] jointly obtained a new kind of carbide material (Ti3C2Tx) with two-dimensional structure, coined as MXenes, were produced by selectively etching off Al atom planes from its parent Ti3AlC2. Up to date, Ti3C2Tx has received great attentions of many applications[25,26,27,28,29]. In addition to large specific surface area, Ti3C2Tx has good electrical conductivity, thermal-conducting property, and hydrophilicity[30], and thus it is promising reinforcement for electrical conductive composites. In particular, Ti3C2Tx has demonstrated its potential as an additive in composites with polymers (PVA, PAM, PEI, PAN, etc.), ceramics (MoS2, TiO2, etc.) and carbon materials (CNT, MWCNT, CNFs, etc.)[31]. Hence, the electric conductive Ti3C2Tx is expected to reinforce Ag matrix as a new electrical contact material.
In this study, the application of MXenes to electrical contact material is explored. Ti3C2Tx reinforced Ag-based composite was prepared by powder metallurgy, and its overall properties, such as electrical resistivity, hardness, machinability, tensile strength, and anti-arc erosion were investigated and compared with those of Ag-based composite reinforced by Ti3AlC2 ceramic. The mechanism of properties difference of these two kinds of samples were also analyzed and concluded. The research results would provide significant data for the design and preparation of the new generation of environment-friendly silver-ceramic composite electrical contact materials in the future.
1 Experimental
Base materials for composites were Ag (99.9%, ~10 μm, Xinshengfeng, China) and Ti3AlC2 (99.0%, ~10 μm, in-situ prepared with TiC (99%, ~5 μm, Aladdin, China), Ti (99.99%, ~50 μm, Aladdin, China), Al (99.7%, ~50 μm, Zhongnuo xincai, China). Ti3C2Tx was obtained by immersing Ti3AlC2 (5 g) into hydrofluoric acid (HF) solution (100 mL, 40% in mass) for 24 h under magnetic stirring (40 ℃)[23]. Ag/10% (in mass) Ti3C2Tx (Ag/Ti3C2Tx) and Ag/10% (in mass) Ti3AlC2 (Ag/Ti3AlC2) mixtures were individually homogenized by ball milling for 0.5 h with a medium of ethyl alcohol (99.7%, Shanghai Titan Scientific Co. Ltd., China). These two mixtures were subsequently cold-pressed into green bodies (15 mm in diameter, 2 mm in thickness) under 800 MPa, and then heat-treated at 700 ℃ for 2 h in argon atmosphere.
Phase composition of the samples was characterized by X-ray diffraction (XRD, Bruker-AXS D8, Germany). The structure change of Ti3AlC2 and Ti3C2Tx powders were further characterized by Transmission Electron Microscope (TEM) (FEI, Nova Nano 450, America). Vickers hardness of samples was tested under 0.1 MPa by the micro-hardness tester (FM-700, Future-Tech Corp., Japan). Resistivity of samples was measured by the four probe method (Metra HIT 27 I, Gossen Metrawatt, Germany). Microstructure and chemical compositions were characterized by a scanning electron microscope (SEM, FEI/Philips Sirion 2000, Netherlands), equipped with an energy dispersive spectrometer (EDS, AZtes X-MAX 80). The Ag/Ti3C2Tx and Ag/Ti3AlC2 bulk materials were processed into the dumbbell-shaped samples with length of 40.0 mm, width of 7.5 mm, middle part width of 4 mm and thickness of 2.0 mm. The tensile strength of both samples was tested at a universal test machine (AGS- X5kN, SHIMADZU, Japan) at a speed of 1 mm·min-1. Finally, the Ti3AlC2 or Ti3C2Tx reinforced Ag-based composite electrical contact was installed in commercial contactors and tested under the harsh conditions (400V/100A/AC3, GB14048.4-2010) at Low Voltage Switch Testing Center of Shanghai Electrical Appliance Research Institute.
2 Results and discussion
Fig. 1 shows the phase compositions and microstructures of raw powders (Ti3AlC2 and Ti3C2Tx). Ti3AlC2 was characterized by granular morphology with smooth surfaces (Fig. 1(a)), and Ti3C2Tx exhibited a multilayered morphology with the layer thickness of 0.15-0.37 μm (Fig. 1(b)). Fig. 1(b) obviously shows that the (002) diffraction peak of Ti3C2Tx is tilted towards low angle, which also confirms the expansion of Ti3C2Tx layer space.
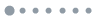
Figure 1.XRD patterns and morphologies of the raw powders(a) Ti3AlC2; (b) Ti3C2Tx
The microstructures and element distributions of Ag/Ti3AlC2 and Ag/Ti3C2Tx composites are displayed in Fig. 2. As shown in Fig. 2(a, c), both reinforcements (Ti3AlC2 and Ti3C2Tx) uniformly distribute in Ag matrices, Ti3AlC2 retains the granular morphology while Ti3C2Tx takes the stripe-shaped morphology. Fig. 2(b, d) display the element distributions of Ag, Ti and Al in composites, which further confirm that Ti3AlC2 and Ti3C2Tx take different shapes in Ag matrices. Moreover, slight diffusion of Al with Ag is observed in Ag/Ti3AlC2 (Fig. 2(b)), while a few Al elements detected in Ag/Ti3C2Tx (Fig. 2(d)), which is consistent with the XRD and TEM results.
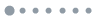
Figure 2.Microstructures with SEM images(a, c) and element distribution (b, d) of composites (a, b) Ag/Ti3AlC2; (c, d) Ag/Ti3C2Tx
Ag/Ti3C2Tx composite is further observed at higher magnification SEM image (Fig. 3(a)). It is obvious that the interface between Ti3C2Tx and Ag matrices is clear with no trace of cracks and holes, indicating a good physical bonding. However, Ti3C2Tx has large contact angle with Ag substrate in the high-temperature wetting experiment (Fig. 3(b)), which confirms the absence of reactive wetting (i.e. chemical bonding) between them.
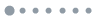
Figure 3.High-magnification SEM image of Ti3C2Tx in Ag matrix(a) and high-temperature wettability of Ti3C2Tx with Ag (b) The insets in (b) show optical images of contact angle at different temperatures
Contact materials are usually manufactured into various shapes, necessitating excellent machinability. A typical negative case is SnO2 with high hardness leading to the poor machinability of Ag/SnO2, which hinders its substitute for CdO[32]. Fig. 4 shows the Vickers hardness of Ag/Ti3C2Tx, Ag/Ti3AlC2, and pure Ag (for reference). Ag/Ti3C2Tx possesses intermediate hardness (64 HV), and can be cut into different shapes, including rod, rivet, disc and square (the insert in Fig. 4). The good machinability originates from the 2D structure of Ti3C2Tx, in which weak van der Waals interaction exists between layers. In addition, contacts usually carry high current density in service, thus a low resistivity is a prerequisite for potential electrical contact materials. As shown in Fig. 4, the Ag/Ti3C2Tx and Ag/Ti3AlC2 composites own low resistivity (16×10-3 μΩ·m of Ag for reference). In particular, the resistivity of Ag/Ti3C2Tx (30×10-3 μΩ·m) is 29% lower than that of Ag/Ti3AlC2 (42×10-3 μΩ·m), which is highly meaningful for the practice application.
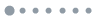
Figure 4.Machinability, electrical resistivity (blue bar) and Vickers hardness (red bar) of Ag/Ti3C2Tx and Ag/Ti3AlC2, compared with those of Ag The insert is pieces cut from Ag/Ti3C2Tx; colorful figure is available on website
The improved conductivity of Ag/Ti3C2Tx can be explained from three aspects: higher conductivity of Ti3C2Tx than that of Ti3AlC2, enhanced interface bonding between Ag and Ti3C2Tx, deformability of the stripe- shaped Ti3C2Tx in Ag matrices.
Firstly, based on the first-principle band structure calculations, in Ti3AlC2, Ti3d state contributes to the majority of the total densities of states (DOS) at Fermi level; removal of the Al layers from Ti3AlC2 results in the redistribution of Ti3d states from broken Ti-Al bonds into delocalized Ti-Ti metallic-like bonding states, leading to the increase of local DOS maximums at Fermi level[33]. Thus, in MXene (Ti3C2Tx), the electron density of states near Fermi level (N(Ef)) is 1.9-3.2 times higher than that in the corresponding MAX (Ti3AlC2)[34]. Secondly, EDS mapping indicates the existence of O and F elements, which may come from the functional groups (-F, -OH) of Ti3C2Tx surface[35] (Fig. 5). Generally, the hydrophilicity of -F/-OH functional groups is beneficial to the bonding between Ti3C2Tx and metal matrices[34], which avoids the similar phenomenon of poor interface bonding between carbon nanotubes, fibers and metal matrices [36]. In addition, the SEM observation also displays the tight bonding between Ti3C2Tx and Ag matrices without obvious cracks and holes, as shown in Fig. 2(c) and Fig. 3(a). Hence, the uniform microstructure and good bonding of Ag/Ti3C2Tx improved the conductivity. Thirdly, as shown in Fig. 2(b, d), the microstructure of stripe-shaped Ti3C2Tx is obviously different from that of granular Ti3AlC2 in Ag matrices. The 2D layered structure of Ti3C2Tx facilitates its deformability during preparation. The Ti3C2Tx was cold compacted into the stripe-like Ti3C2Tx (average thickness of ~3 μm), whereas Ti3AlC2 retains its original shape (average diameter of ~10 μm). In contrast with granular Ti3AlC2, the stripe-shaped Ti3C2Tx has smaller cross- sectional area perpendicular to the current direction, minimizing the scattering section for electrons and the resistance to the electron transmission. In summary, the excellent machinability and electrical conductivity makes Ag/Ti3C2Tx a promising substitute for Ag/CdO.
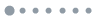
Figure 5.Micro-morphology and element distribution of Ag/Ti3C2Tx composite in high-magnification SEM image
However, as shown in Fig. 6, the maximum tensile strength of Ag/Ti3C2Tx composite (32.77 MPa) is far less than that of Ag/Ti3AlC2 composite (145.52 MPa). The superior tensile strength of Ag/Ti3AlC2 composite derives from the interdiffusion between the active Al atomic layer with Ag matrices. On the contrary, the absence of Al layer leads to the weaker interface bonding strength between Ti3C2Tx and Ag matrices, which finally deteriorates the mechanical property of the entire Ag/Ti3C2Tx composite.
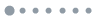
Figure 6.Tensile properties of Ag-based composites reinforced by different reinforced phase materials
In order to further investigate the property of Ag/Ti3C2Tx, electrical arc discharging experiments were carried out on this contact surface under a harsh condition (AC-3, 100 A, 400 V, GB14048.4-2010). The Ag/Ti3C2Tx contact failed to make and break after 1233 times arc discharging. The optical image shows that the shape of contact remains well with some dents and protuberances (Fig. 7(a, b)). The surface morphologies of Ag/Ti3C2Tx contact after arc erosion are subsequently exhibited in Fig. 7(c), complete edge and flat surface were further confirmed by SEM. Some Ag spheres, solidified Ag blocks, and small cracks were observed at high-magnification SEM image (Fig. 7(d)). Fig. 7(e-h) exhibit the microstructure and chemical composition of Ag/Ti3C2Tx contact surface. There are many irregular dark blocks surrounded by little bright particles (Fig. 7(e)). As shown in Fig. 7(f), area 1 (white block) contains large amount of Ti, O, F with trace of Ag and Al, which may be attributed to the Ti-O-F mixture produced by electrical arc erosion to Ti3C2Tx. Area 2 (bright particles) is mainly composed of Ag, F, and O. It is deduced that the Ag-O-F mixture was produced by the absorption of O2 in liquid Ag and reaction with -F function group of Ti3C2Tx. Fig. 7(h) displays two types of spheroid particles at magnified SEM image. EDS analysis results showed that both the particles contained vast N element, showing that these two particles were composed of Ag-O-F-N.
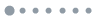
Figure 7.Surface morphology, microstructure and chemical composition of Ag/Ti3C2Tx contact after arc erosion(a, b) Optical image and magnified image; (c, d) Surface morphology; (e-h) Microstructures and chemical composition
The relative mass loss of Ag/Ti3C2Tx (54% after 1233 times arc discharging) is considerably more than that of Ag/Ti3AlC2 (0.82% after 3000 times arc discharging), which is also attributed to the absence of Al layer in Ti3AlC2. As analyzed previously, the lack of Al-Ag interdiffusion leads to the weak bonding strength of Ti3C2Tx with Ag, and thus decrease the mechanical property of composite, which accordingly impairs the resistance to electrical arc impact damage. In addition, the absence of Al-Ag interdiffusion also results in the poor wettability of Ti3C2Tx with Ag during the electrical arc discharging and consequently decreased viscosity of molten pool, finally deteriorating the resistance to the material transfer of Ti3C2Tx and Ag under electrical arc high-temperature. Nonetheless, there is still space for further improvement of the arc erosion resistance of Ag/Ti3C2Tx with superior electrical conductivity by the composition design, structure optimization, technique promotion in the following work.
3 Conclusions
In this work, Ag-based electrical contact materials, reinforced by Ti3AlC2 ceramic and its derivative (Ti3C2Tx), were successfully prepared by powder metallurgy. The microstructure, chemical composition, hardness, conductivity, machinability, mechanical property and erosion resistance of Ag/Ti3AlC2 and Ag/Ti3C2Tx composites were investigated and compared. The main conclusions are as follows:
1) Stripe-like Ti3C2Tx uniformly distributes in Ag/Ti3C2Tx composite.
2) In contrast with Ag/Ti3AlC2, Ag/Ti3C2Tx has lower resistivity (30×10-3 μΩ·m), 29% lower than that of Ag/Ti3AlC2. The superior conductivity of Ag/Ti3C2Tx results from the stronger metallicity of Ti3C2Tx, uniform microstructure, and smaller cross-sectional area of Ti3C2Tx in the composite.
3) The moderate hardness and excellent machinability of Ag/Ti3C2Tx are also satisfactory for electrical contact materials.
4) The tensile strength (32.77 MPa) of Ag/Ti3C2Tx composite is inferior to that of Ag/Ti3AlC2 (145.52 MPa) due to the lack of Al-Ag interdiffusion.
5) Ag/Ti3C2Tx shows moderate arc erosion resistance with production of Ti-O-F, Ag-O-F, and Ag-O-F-N mixture, which is inferior to that of Ag/Ti3AlC2, and needs to be further improved.