Vehicle radomes are important structural components located at the front end of a vehicle to reduce air resistance, maintain aerodynamic shape and protect the effective transmission of electromagnetic wave signals and efficient communication[1]. In flight, the radome endures intense aerodynamic heating and loads[2], as well as particle erosion[3]. Simultaneously, the radome is expected to exhibit excellent wave transparency to ensure normal radar operation during high-speed flight[4-5]. Therefore, vehicle radome materials must possess excellent comprehensive performance of heat protection-carrying-wave transmission-integration.
Hexagonal boron nitride (h-BN) possesses a crystal structure similar to that of graphite[6]. The special crystal structure endows h-BN with a series of unique comprehensive properties[7⇓⇓-10], such as low dielectric coefficient (3-5), low loss tangent ((2×10-4-8×10-4), extremely high sublimation temperature of about 3000 ℃ (in non-oxidative atmosphere), chemical inertness, excellent thermal shock resistance, tribological properties and good machining performance[11]. Consequently, it is an excellent material for preparing vehicle radome.
However, the strong covalent bond structure of h-BN hints its sintering and densification because of its minimal solid diffusion coefficient. Therefore, researchers have facilitated sintering by introducing a secondary phase that creates a liquid phase during sintering, such as SiO2-BN[12], BN-MAS[13-14], BN-Y2SiO5[15], BN-Y2O3-AlN[16], BN-La-Al-Si-O[17], BN-YAG[18], AlN-h-BN[19], and BN-SiC[20].
In this study, BN-SAS ceramic composites were fabricated by hot-press sintering. SrAl2Si2O8 (SAS) exhibits excellent mechanical properties, with high bending strength (134 MPa), low dielectric constant (~9.0), and low melting point (~1675 ℃)[21-22], which is expected to improve the comprehensive performance of BN ceramics. Effects of sintering pressure on the microstructure, mechanical properties, and thermal properties of BN-SAS ceramic composites were investigated. The thermal shock resistance and thermal shock damage mechanism of BN-SAS ceramic composites were also discussed.
1 Experimental procedures
1.1 Manufacturing process
The starting raw materials included h-BN powders (d50=1.31 μm, 99% purity, Dandong Chemical Research Institute Co., Ltd., China), SrCO3 powders (d50=3.12 μm, 99% purity, Tianjin Guangfu Fine Chemical Research Institute, China), Al2O3 powders (d50=0.72 μm, 99% purity, Taimei Chemicals Co., Ltd., Japan), and SiO2 powders (d50=3.39 μm, 98% purity, Lianyungang Guangyu Quartz Products Co., Ltd., China). SrCO3, Al2O3 and SiO2 were combined in the stoichiometric ratio required to yield SrAl2Si2O8. SAS was added with mass fraction of 30%, which was roughly equivalent to a volume fraction of 23%.
The starting powders were ball-milled in anhydrous ethanol for 24 h. Subsequently, the powder mixtures were hot-pressed in a 50 mm diameter mold, illustrated in Fig. 1, at 1800 ℃ for 60 min under a pressure range of 10~30 MPa in 1.013×105 Pa N2 atmosphere.
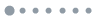
Figure 1.Flow chart for the preparation of BN-SAS ceramic composites by hot-press sintering
1.2 Thermal shock experiment
The water-quenching method was chosen to investigate the thermal shock resistance of the BN-SAS ceramic composites. The muffle furnace temperatures were set to target temperatures of 625, 825, 1025, 1225 and 1425 ℃. The samples were inserted into the furnace and held for 10 min to obtain a uniform temperature distribution, respectively. After heat preservation, the samples were promptly quenched in water against temperature difference ΔT of 600, 800, 1000, 1200 and 1400 ℃, respectively. The residual bending strength of the specimens was tested.
1.3 Characterization
The density of the BN-SAS composite was measured in distilled water by the Archimedes principle (DV314C) at room temperature. The phase composition was determined via X-ray diffractometry (XRD, D/max-γB, Japan). The microstructural features of the samples were observed by scanning electron microscope (SEM, HELIOS NanoLab 600i, FEI, America and AMBER, TESCAN, Czech Republic). Microstructure and energy spectrum elemental analyses of composite samples were performed by using transmission electron microscope (TEM, Talos F200x, FEI, USA).
Bending strength was measured on sample with dimension of 3 mm×4 mm×36 mm by the three-point bending method. The fracture toughness (KIC) was determined by the single-edge notched beam (SENB) method with specimen dimension of 2 mm×4 mm× 25 mm, using an outer span of 16 mm fixture and a crosshead speed of 0.05 mm/min. Bending strength and fracture toughness values were the average of four measurements tested under the same condition. The loading direction was parallel to the direction of hot pressing. The modulus of elasticity was measured by the pulsed excitation method (RFDA-HTVP-1750 ℃, IMCE, Belgium).
Thermal conductivity of the ceramic composites was tested using laser thermal conductivity meter (LFA467HT, NETZSCH, Germany), in the range from 200 ℃ to 1000 ℃, carrying out parallel to the direction of hot pressing. The coefficient of thermal expansion (CTE) was measured using a thermal expansion meter (DIL402C, NETZSCH, Germany) over the temperature range from room temperature (RT) to 1200 ℃, carrying out perpendicular to the direction of hot pressing.
2 Results and discussion
2.1 Density and mechanical properties
Table 1 displays density, bending strength and fracture toughness of BN-SAS ceramic composites. The density of BN-SAS ceramic composites increases from 1.90 to 2.33 g/cm3 with the sintering pressure increasing. This is primarily due to the low-melting SAS displaying a certain degree of mobility at the sintering temperature. Elevated sintering pressure enables the SAS liquid phase to spread more extensively and fill the pores more effectively.

Table 1.
Density, bending strength and fracture toughness of BN-SAS ceramic composites
Table 1.
Density, bending strength and fracture toughness of BN-SAS ceramic composites
Sintering pressure/MPa
| Density/(g·cm-3)
| Bendingstrength/MPa
| Fracture toughness/(MPa·m1/2)
|
---|
10 | 1.90 | 87±5 | 1.33±0.04 | 20 | 2.25 | 138±4 | 1.84±0.05 | 30 | 2.33 | 136±11 | 1.50±0.24 |
|
The bending strength gradually increased with the increase of sintering pressure. SAS is more effective in facilitating sintering during the sintering process. When the sintering pressure reaches 20 MPa, the densification of the ceramic composites increases, resulting in a notable enhancement in bending strength. The fracture toughness of ceramic composites increases and then decreases with the increase of sintering pressure.
2.2 Phase and microstructure
The main phases of the BN-SAS ceramic composites are h-BN and h-SrAl2Si2O8 (Fig. 2), showing that Al2O3, SrCO3 and SiO2 in the pristine powder reacted stoichiometrically to form SrAl2Si2O8. Additionally, under higher sintering pressure, SrAl2Si2O8 exhibits stronger diffraction peaks, indicating that increasing the sintering pressure can promote the crystallization of strontium feldspar.
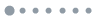
Figure 2.XRD patterns of BN-SAS ceramic composites sintered at different pressures
Fig. 3(a-c) present HRTEM images of BN-SAS ceramic composites sintered at 10 MPa. The h-BN grains show obvious lath-like features, and SAS is uniformly distributed within the pores of h-BN. The bond between the h-BN and SAS interfaces is tight and legible. The SAS comprises merely small crystalline grains that exhibit poor crystallinity, which is consistent with the XRD results. Adjacent to h-BN, the crystallinity of SAS surpasses that found in the interior regions. The interplanar spacing of BN crystal is measured at 0.33 nm, corresponding to the (002) crystal face of h-BN. The TEM image and elemental mappings are shown in Fig. 3(d-j). The interface between h-BN and SAS is also securely joined, without any obvious cracks or voids. The SAS phase is uniformly distributed within the pores of the “card room” structure formed by h-BN.
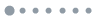
Figure 3.HRTEM and TEM characterization of BN-SAS ceramic composites sintered at 10 MPa(a) HRTEM image; (b) Inverse FFT image of area A in figure (a); (c) SAED pattern of h-BN; (d) TEM image of BN-SAS ceramic composites; (e-j) Elemental analysis of the figure (d); (e) B; (f) N; (g) O; (h) Sr; (i) Al; (j) Si
Fracture morphology is shown in Fig. 4. Fracture surface of the ceramic composites is uneven, featuring numerous lamellar particles resulting from the extraction of the plate-like h-BN particles from the matrix. The uneven fracture suggests a zigzag crack extension path, which absorbs fracture energy and enhances the bending strength. As the sintering pressure further increases, the fracture of the composites exhibits more denser morphology, with lamellar h-BN particles embedded within the secondary phase SAS.
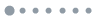
Figure 4.Fracture microstructures of BN-SAS ceramic composites sintered at different pressures(a) 10 MPa; (b) 20 MPa; (c) 30 MPa
2.3 Thermal properties and thermal shock resistance
Fig. 5(a) presents the temperature dependence of dL/L0 of BN-SAS ceramic composites. The ratio dL/L0 increases monotonically with the increase of temperature, maintaining a relatively uniform rate in the range of RT-600 ℃. At 1200 ℃, the value dL/L0 peaks at 5.2×10-3. These ceramic composites demonstrate positive coefficients of thermal expansion. The ceramic composites sintered at 20 MPa show the least dL/L0 values, indicating minimal thermal expansion.
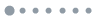
Figure 5.Thermal properties of BN-SAS ceramic composites sintered at different pressures(a) Thermal expansion rate with inset showing the average CTE (α); (b) Thermal conductivity
The inset in Fig. 5(a) displays the average CTE of BN-SAS ceramic composites over the temperature interval from 200 to 1200 ℃. The average CTE increases from 2.96×10-6 K-1 to 5.04×10-6 K-1 with the increase of sintering pressure. This is primarily because lowering the sintering pressure leads to higher porosity within the composites, which effectively accommodates the increased atomic spacing caused by atomic thermal vibrations, consequently reducing the CTE. In addition, the lowering sintering pressures remain the SAS primarily in an amorphous form, which further reduces the CTE.
Fig. 5(b) illustrates the thermal conductivity as a function of temperature. Thermal conductivity of ceramic composites increases slightly with sintering pressure rising in the range of RT-600 ℃, although the differences are minimal. In the range of 600-800 ℃, the thermal conductivity decreases with increased sintering pressure of 20 MPa and 30 MPa, and it is obviously lower than that of 10 MPa at 1000 ℃.
The mechanical and thermal properties of the ceramic composites were utilized to determine the thermal shock fracture resistance factor R and thermal shock damage factor RIV[23-24], the outcomes are summarized in Table 2.

Table 2.
Properties of the BN-SAS ceramic composites
Table 2.
Properties of the BN-SAS ceramic composites
Sintering pressure/MPa | Bending strength/MPa
| Fracture toughness/ (MPa·m1/2)
| Young's modulus/GPa
| Average CTE/ (×10−6, K−1)
| λ/( W·m-1·K-1, 1000 ℃)
| R/℃
| RⅣ/μm
|
---|
10 | 87±5 | 1.33±0.04 | 48.47 | 2.96 | 14.70 | $609(1-\nu )$ | $230/(1-\nu )$ | 20 | 138±4 | 1.84±0.05 | 67.83 | 3.33 | 12.42 | $613(1-\nu )$ | $177/(1-\nu )$ | 30 | 136±11 | 1.50±0.24 | 66.94 | 5.04 | 5.72 | $404(1-\nu )$ | $122/(1-\nu )$ |
|
At a sintering pressure of 20 MPa, the R reaches its maximum value, indicating that the ceramic composites exhibit the greatest critical thermal shock temperature difference and superior thermal shock resistance. Furthermore, the BN-SAS ceramic composites sintered at 20 MPa displayed the highest bending strength at room temperature. Consequently, the ceramic samples sintered at 20 MPa were selected for subsequent thermal shock resistance experiments.
The residual strength and residual strength rate of BN-SAS ceramic composites sintered at 20 MPa after thermal shock experiments with temperature differences ranging from 600 ℃ to 1400 ℃ are depicted in Fig. 6. The thermal shock residual strength of BN-SAS ceramic composites shows an initial increase followed by a decline with the increase of thermal shock temperature difference. The residual strength of the composite peaks is (140±15) MPa after the 800 ℃ thermal shock experiment, higher than that of unquenched samples. Subsequently, it decreases progressively with further increase in thermal shock temperature difference. This phenomenon is primarily due to the microstructure transformation of the composite.
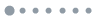
Figure 6.Residual bending strength and residual strength rate of BN-SAS composites sintered at 20 MPa as a function of thermal shock temperature difference
The surface morphology of BN-SAS ceramic composites after thermal shock is shown in Fig. 7. With the thermal shock temperature difference gradually increasing, droplets and microcracks emerge on the surface of the ceramic composites. With the thermal shock temperature difference ranging from 600 ℃ to 800 ℃, a thin oxide layer forms on the surface of ceramic composites. The surface becomes smoother and denser, with a reduction in the number of pores. At this thermal shock temperature difference, the h-BN on the surface of the ceramic composite undergoes oxidation to form a mobile B2O3 liquid phase that encapsulates the surface and mends defects such as microcracks, enhancing the surface density of the samples.
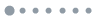
Figure 7.Micrographs of surfaces and fracture edges of BN-SAS ceramic composites sintered at 20 MPa after thermal shock with different temperature differences(a) 600 ℃; (b) 800 ℃; (c) 1000 ℃; (d) 1200 ℃; (e) 1400 ℃; (f) Fracture edge morphology under thermal shock temperature difference of 1400 ℃
When the thermal shock temperature difference reaches 1000 ℃, tiny glassy droplets appear on the surface of the ceramic composites. h-BN oxidizes to yield B2O3, that subsequently merges with SAS, resulting in formation of a stable and viscous SrO-Al2O3-SiO2-B2O3 glass that adheres to the surface of the composite. Further increase in temperature difference exacerbates the oxidation process of h-BN, leading to a progressive enlargement of glassy droplets.
At a thermal shock temperature difference of 1400 ℃, larger cracks appear on the surface of the ceramic composites. Numerous pores are evident, contributing to rough and uneven material surface. This indicates that the significant thermal stress inside the ceramic composites at this temperature difference causes material cracking, seriously diminishing the residual bending strength. Moreover, the enlargement of glassy droplets suggests a severe oxidation of the composites.
3 Conclusions
In this study, BN-SAS ceramic composites were prepared by hot-press sintering. Drawn from the experimental results and detailed microstructural analyses, conclusions are listed as follows.
1) The BN-SAS ceramic composites, fabricated by hot-press sintering, exhibit optimal mechanical properties at a sintering pressure of 20 MPa, with bending strength and fracture toughness of (138±4) MPa and (1.84±0.05) MPa·m1/2, respectively.
2) The residual strength rate of BN-SAS ceramic composites after thermal shock at 800 ℃ was 101%. During thermal shock, the ceramic composites undergo oxidation, leading to the formation of a SrO-Al2O3-SiO2-B2O3 glass film that encompasses on the surface of the composites, mending the surface defects and enhancing the mechanical properties of the BN-SAS composites.