I. INTRODUCTION
Laser-driven inertial fusion is a highly promising approach to the practical achievement of fusion power generation, which has been a quest of humanity for well over half a century. The National Ignition Facility (NIF) at Lawrence Livermore National Laboratory achieved a target gain G > 1 at the end of 20221 and set a new fusion yield record of 5.2 MJ in February 2024,2 thus successfully demonstrating the feasibility of laboratory laser fusion. However, this gain is still far below the target value of 30–100 required for inertial fusion energy (IFE).3 In fact, limited by its configuration,4 energy,5 and the technical route identified in the 1980s,6,7 it is hard for the NIF to reach such a high gain. Hence, the development of a driver based on novel laser technology is a mandatory step in the path toward IFE. In this paper, we will present a conceptual design for an efficient and low-cost laser driver capable of one shot per 30 min, aiming for G > 30. A schematic is shown in Fig. 1, and the main technical specifications are shown in Table I. In the following, we will address the novel technological developments required to improve the energy storage efficiency, extraction efficiency, flux, volume, etc. for this driver.
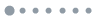
Figure 1.Schematic of the general layout of the laser driver with its target chamber. (a) Arrangement of laser beam, which is injected at the front end (FE) with an initial energy of 5 J, reflected at the Pockels cell (PC) with an amplified energy of 1.5 kJ, amplified in the main amplifier and filtered by the laser filters (LAF), and finally delivered at the spatial filter (SF) with an energy of 20 kJ and a beam size expansion from 260 mm to 530 mm. (b) Beamlet of four beams at 3ω. (c) Octahedral spherical Hohlraum and its ideal laser arrangement with 16 beamlets per end. The human figure to the left of (b) shows the scale of the laser driver.

Table 1. Main technical specifications.
Table 1. Main technical specifications.
Laser energy | 10 MJ | Laser power | 2–3 PW | Laser wavelength | Beam color selectable | | from 2ω/3ω/4ω | Waist diameter | 1000 μm | Main pulse width | 3–5 ns | Repetition rate | 1 shot/30 min | F number | 10–15 | End number | 6 | Beamlet number per end | NQ = 16 | Beam number per beamlet | 4 | Driving mode | Octahedral configuration | Shooting angle | All beamlets have the same | (for details, see Refs. 4 and 8) | incidence angle θL | ranging from 50° to 60° | and the same initial azimuthal | angle ϕL0 ranging | from 0° to 360°/4NQ | Cost | ≤20 × 109 RMB |
|
II. KEY TECHNOLOGICAL DEVELOPMENTS
A. Multi-front-end technology
Laser–plasma instabilities (LPIs) are among the main obstacles to achieving high gain at the NIF. In our novel design, each laser beam has an independent front-end, i.e., one distributed feedback (DFB) oscillator per beamline. Improved freedom of regulation can then be achieved, because each laser beam has no fixed phase relationship, and therefore incoherent superposition can be realized at the target point. This is conducive to beam smoothing and can effectively suppress LPIs. Moreover, a super light spring of incoherence in all dimensions of time, space, and angle can be used to further suppress LPIs.9 Thus, it is possible for the driver to work also at a frequency lower than 3ω, for a higher energy conversion efficiency and a higher damage threshold for the optical components in the final optical assembly.
B. Near-field spatial separation amplification of pre-pulse and main pulse
In ignition target designs, the laser pulse consists of a pre-pulse and a main pulse, with the power of the pre-pulse usually being much lower than that of the main pulse. This makes the conversion efficiency of the pre-pulse very low during the frequency conversion process, as a consequence of which the overall frequency conversion efficiency of the ignition pulse is about 30% lower than that of a square-wave pulse.7 In our novel design, the pre-pulse and main pulse are spatially separated in the amplifier through the use of spatiotemporal shaping. Furthermore, the pre-pulse corresponds to a smaller part of the aperture, with the main pulse corresponding to the rest. This can be used to adjust the power densities of the pre-pulse and the main pulse so that they are equivalent, thereby improving the overall conversion efficiency. The superposed effect of the pre-pulse and main pulse at the target point can be the same as that of the traditional amplification method.
C. High-fluence amplification employing laser material with low emission cross section, long fluorescence lifetime, and high energy storage
The gain medium in most existing laser drivers is neodymium glass, which has a large radiative transition probability and a high gain, owing to its short fluorescence lifetime and large emission cross section. However, it provides relatively small energy storage. As the main amplifier gain medium in our novel driver design, we employ a new sensitizing-doped laser material that has a long fluorescence lifetime of ∼650 µs, a low emission cross section of cm2, and a high stored energy of 0.5 J/cm3. In addition, a high-flux and multipass amplification is used to effectively extract the stored energy. This type of amplifier is expected to achieve a high flux output of 30 J/cm2.
D. Water-cooled xenon lamp with annular section and fluorescent conversion separator material
The operational efficiency of high-power laser devices is relatively low, only about three to four shots per day. In our novel design, we use a xenon lamp with an annular section as the pump, the fluorescence of which can be converted into an absorption band and absorbed by the laser medium using a fluorescence conversion baffle material. Hence, the pumping light–laser conversion efficiency can be remarkably improved. In addition, the xenon lamp is water-cooled to enable prompt removal of heat and prevent the laser medium from continually heating up. As a result, the emission interval can be effectively shortened, and a shooting capability of 30 min per emission can be expected. This aspect of the novel design improves the radiation efficiency of the large-diameter xenon lamp and the absorption efficiency of the gain medium, leading to a much higher energy storage efficiency of the disk amplifier and a much shorter emission interval.
E. Near-field multipass split-plate amplifier based on angle-sensitive film
The energy extraction efficiency is crucially important for a driver. To improve the extraction efficiency, we have designed a near-field multipass amplifier. The constituent amplifiers have a certain splitting angle, and the film layers of their surfaces are designed to be angle-sensitive. In this way, the pulse has a high reflectivity on the surfaces in the first two transmission paths, and the angle corresponding to the third path provides a high transmissivity.10 Thus, the actual transmission distance of the pulse passing through the amplification medium is three times the thickness of the medium. In other words, this is a three-pass amplification scheme, in which the pulse has nearly equal fluence in each amplifier medium, while the integral fluence is enhanced by a factor of three. This amplification mode has a simple system structure but a high extraction efficiency.
F. Two-pass amplification configuration combined with near-field three-pass amplification
Together with the near-field three-pass amplification, the main amplifier is equipped with a two-pass amplification configuration, and the amplification of 48 equivalent pieces can be realized by adopting eight pieces of gain medium. This system has a compact structure (with a length of about 20 m), a large integral flux, a balanced flux of each piece of gain medium, and a high extraction efficiency, which can provide the required image transmission of the system when combined with a traditional spatial filter.
G. Spatial filtering based on angular spectrum-sensitive nonlinear crystal
Current laser technology employs low-gain high-fluence amplification. Therefore, the B integral of the system is high, and spatial filtering is required to prevent it from increasing to unacceptable values.6 However, traditional spatial filters are generally long and require a vacuum assembly, making them expensive. In our design, we use a nonlinear near-field filtering method with specially designed single or cascaded nonlinear crystals. This enables the high-spatial-frequency components of pulses to be converted to second-harmonic waves and filtered during the subsequent amplification processes. Meanwhile, the low-frequency components of pulses have a low conversion efficiency. As a result, the spatial filtering can be realized. In particular, a nonlinear spatial filter can be conveniently inserted into the amplifier, resulting in a more compact structure of the laser driver, with significant space and cost savings.
H. Beam combination system based on noncollinear nonlinear frequency conversion
The number of beams of a laser driver is restricted because the solid angle of the target chamber is fixed. In our design, the two fundamental-frequency beams of light are combined into one beam at third-harmonic frequency (3ω) through noncollinear second-harmonic and sum-frequency conversion. Furthermore, the beam number can be doubled by using the noncollinear beam combination scheme, and sufficient brightness of the output pulse can be ensured with a small F number under the condition that the load capacity of the device is constant.
I. New measurement and control techniques
Compared with the advanced control techniques that are now available, the control systems used in laser drivers lags far behind. Our design will employ a centralized control system based on the global wireless Internet of Things (IoT), together with a high-resolution and high-stability time-synchronization system based on high-speed communication technology, together with full-system control based on artificial intelligence (AI) and miniaturized measurement packages.
J. General layout: Semi-underground layout centered on the target chamber
With the approaches described above, the space occupied by the driver can be greatly reduced, and also an underground layout becomes possible. The proposed general layout is semi-underground, centered on the target chamber, which has six laser shooting ends,8 with 16 beamlets per end and four beams per beamlet, guided into the target chamber, as shown in Fig. 1. This can reduce the cost of construction, as well as the environmental impact.
III. SUMMARY
As a step on the path to achieving IFE, we have presented a conceptual design for a next-generation laser driver that provides 10 MJ, 2–3 PW, and one shot per 30 min. It is applicable to multiple schemes that adopt the ideal laser arrangement with an octahedral spherical Hohlraum.8,11,12 The highly symmetric radiation drive at all times and for all spectra naturally generated inside an octahedral spherical hohlraum is mandatory in achieving a fusion of high gain with the delicate capsule designs.13–15 With a 10 MJ drive, it should be possible to achieve G ≈ 30 in the case of a burn depletion3 of Φ ≈ 45% of 2 mg DT fuel by indirect drive, and G ≈ 100 in the case of Φ ≈ 30% of 10 mg DT fuel by direct drive. Here, we consider a lower Φ for direct drive owing to the worse asymmetry caused by laser imprinting and beam crossing. We shall present detailed designs for such targets in the future publications. As shown in Table I, the beam colors of the novel driver are selectable from 2ω/3ω/4ω, which means that each laser beam can simultaneously and independently work at 2ω, 3ω, or 4ω for various applications.16,17 This can be realized via a nonlinear frequency conversion process by removing or changing the crystals. Compared with previous designs, our novel laser driver can provide remarkable improvements in energy storage efficiency, extraction efficiency, flux, and repetition, at great reductions in size, metal components, and cost.
ACKNOWLEDGMENTS
Acknowledgment. The authors are grateful to Dr. Xiaohui Zhao of Shanghai Institute of Laser Plasma, Dr. Yongsheng Li, Dr. Hui Cao, Dr. Yaohua Chen, and Dr. Xiumei Qiao of Institute of Applied Physics and Computational Mathematics in Beijing for their help. This work is supported by the National Natural Science Foundation of China (Grant No. 12035002).