1. Introduction
GaN-based nitride alloys, including InN, GaN, AlN, and their ternary alloy, have direct transition energy band and a tunable wide bandgap from 0.7 to 6.2 eV by controlling the AlN or InN mole fraction. Since the 1990s, GaN-based materials and devices have experienced rapid development, and have been regarded as the most promising materials for ultraviolet (UV) and visible light-emitting devices. UV laser diodes (LDs) have the advantage of a number of applications, such as material processing, bio-chemical analysis, excitation light source for phosphors and high photolithographic resolution. Thus, many studies have examined the fabrication of GaN based UV LDs. So far, GaN based UV LDs have been reported by many groups[1−17]. In 1997, the first InGaN UV LD in the world was fabricated by Nakamura et al. in Nichia Corporation. The lasing wavelength was 395 nm under continuous-wave (CW) operation at room temperature (RT)[9]. In 2003, Masui et al. shortened the emission wavelength of UV LD to 365 nm, its threshold current and voltage under CW operation was 50 mA and 4.8 V[6]. At the same time, they achieved a shorter UV LD with lasing wavelength of 354.7 nm under pulse current injection at 25 °C, but the threshold current increased significantly to 14.8 kA/cm2. Then, in 2008, Yoshida et al. in Hamamatsu Photonics K.K reduced the wavelength of UV LD to 342 and 336 nm by hetero-facet-controlled epitaxial lateral overgrowth (hetero-FACELO) method[10, 11], and they further achieved a 338 nm UV LD with output power over 1 W under pulsed operation[12]. This remained the highest power value of UV LDs until 2022. However, further reducing lasing wavelength and increasing output power faces many challenges because of the large lattice mismatch between high AlN mole fraction AlGaN cladding layer and the GaN substrate. To date, the highest CW optical output power of a 375–380 nm GaN-based commercially produced LD is approximately 400 mW, which was fabricated by Nichia Corporation. As to UVB (ultraviolet B) and UVC (ultraviolet C) LDs with electric-injection emission, AlN substrate or AlN template must be used to reducing the stress in AlGaN cladding layers with high AlN mole fraction. The high defect density of AlN and AlGaN material, and low hole concentration in p-type AlGaN cladding layer are the main limiting factors. In 2019, Amano’s group and Asahi Kasei Corporation cooperated to achieve the 271.8 nm UVC LD successfully by using distributed polarization doping (DPD) approach to achieve hole conductivity and injection[7]. This was the first UVC electrically injected LD in the world. Recently, they further reported a UVC LD under room temperature CW operation with largely reduced threshold voltage[13]. In general, in terms of UV LD, Japanese technology takes lead in the international research community. In China, our group realized UVA LDs with a lasing wavelength of 381.9 nm in 2016[14]. The lasing wavelength was further reduced to 357.9 nm in 2022[15, 16] and the RT CW output power of UVA LD increased to 3.8 W with a lasing wavelength of 386.5 nm[17, 18]. Although UV LDs have been investigated for many years, their performance is much lower than those of GaN based violet, blue, and green LDs. In this paper, the challenges of UV LDs, especially for lasing wavelengths from 320 to 400 nm, will be analyzed and approaches to improve their performance will be reviewed.
2. Challenges
The challenges for UV LDs are tremendous and depend strongly on the emission wavelength. As previously reported, the threshold current density increases with the reduction of lasing wavelength, especially when the wavelength is less than 380 nm[19]. This indicates that the difficulty for fabricating UV LDs increases largely with decreasing wavelength. In addition, UV LDs with high CW output power have rarely been reported. The typical epitaxial layer structure of GaN-based UV LDs includes n-AlGaN cladding layer (CL), lower AlGaN waveguide layer (LWG), active region, upper AlGaN waveguide layer (UWG), high AlN mole fraction AlGaN electron blocking layer (EBL), p-AlGaN CL, and p-GaN contact layer. To realize laser diodes in the UV region with shorter wavelength and higher output power, the following four major technological barriers need to be overcome:
ⅰ) A superior optical cavity that enables the confinement of as much light as possible therein with a low optical loss is highly required. To increase the optical confinement factor and decrease optical loss, lasers emitting at shorter wavelength require high AlN mole fraction of AlGaN or InAlGaN in active regions and confinement heterostructures. The optimized UV LD structure of AlN mole fraction of AlGaN CL and WG layers is higher than 20% and 10%, respectively. The tensile strain of the AlGaN layer increases with increasing AlN mole fraction when it grows on free standing GaN substrates with low defect density[20]. Special strain relief techniques are required to avoid the formation of cracks in the laser heterostructure.
ⅱ) A semiconductor material with high optical gain is required. As for AlGaN-based semiconductors, if high-quality crystals are fabricated, very high optical gains in the several thousand should be obtained[21]. However, it has so far been difficult to obtain high-quality AlGaN crystals. Many kinds of defects, such as vacancy defect and dislocation, exist in AlGaN material. Meanwhile, the localization effect for carriers reported in InGaN material[22, 23] is weak in GaN or AlGaN materials. This results in serious nor-radiative recombination in waveguide layers and active region. Therefore, low carrier injection efficiency and radiative recombination efficiency often exist in UV LDs.
ⅲ) Because of the intrinsic requirement of stimulated emission in semiconductor lasers, the high-current-density operation, which enables population inversion of carriers in the active region, should be realized. This would result in serious leakage of carriers and a low wall plug efficiency (WPE). Furthermore, the characteristic temperature of UV LDs is often lower than blue-violet GaN based LDs, and thus the performance of UV LDs will degrade much faster due to increased Joule heating. This results in a thermal rollover phenomenon or catastrophic optical mirror damage (COMD), which further limits the increase of CW output power of UV LDs.
ⅳ) The high energy of ultraviolet photons with reduction of the lasing wavelength can easily destroy the cavity surface coating, increasing optical absorption loss. The selection of cavity coating material is more challenging, and the requirement for cleanliness of the cavity coating and hermetic tightness of packaging process of ultraviolet lasers is much stricter.
3. Progress
3.1. Mismatch stress relief of the AlGaN template
For the wavelength span of UVA (315−400 nm), especially for LDs with the lasing wavelength less than 370 nm, the optimized AlN mole fraction of AlGaN cladding layer is higher than 20%[1−6, 15−17]. Huge stress between AlGaN cladding layer and GaN underlayer may generate cracking in AlGaN epilayers. One solution to this problem is to use of epitaxially laterally overgrown (ELOG) and patterned GaN template to release the stress and suppress the generation of cracking in AlGaN cladding layers. A schematic diagram of the sample structure is shown in Fig. 1(a). This is an effective method, and many groups have been realized GaN based UVA LDs based on the ELOG AlGaN templates[1−4, 24]. In 2007, Yoshida[24] succeeded in fabricating GaN/AlGaN UV LDs without crack generation on whole 2-in sapphire substrate by using hetero-FACELO method. The UV laser diodes lased in the peak wavelength range from 355.4 to 361.6 nm under a pulsed current operation at room temperature. In 2015, Aoki et al.[4] have demonstrated the pulsed operation of a 350-nm-band UV LD using patterned GaN substrate and ELOG technology, The lasing wavelength was 356.6 nm and the peak output power reached to 10 mW from the one side of uncoated facets.
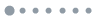
Figure 1.(Color online) Schematic diagram of the sample structures for two different growth methods: ELOG method (a) and the method grown on AlN strain modulation layer (b).
In addition to ELOG templates, AlN modulation layer is another method to release stress and obtain a cracking free AlGaN layer with low stress and low dislocation density, which has been reported in our previous literature[25]. For this method, AlN strain modulation layer was first grown on sapphire substrate. Then, AlGaN layer with AlN mole fraction of about 20% was grown on the AlN strain modulation layer. A schematic diagram of our AlGaN template growth method is shown in Fig. 1(b). This can be described by three stages: (ⅰ) nucleation; (ⅱ) coalescence; and (ⅲ) two-dimensional (2D) growth, which have been marked by the dashed line in Fig. 2. For the nucleation stage, deposited AlGaN will form a large number of small grains first due to the mismatch strain between AlGaN and AlN, in this case, the surface becomes rougher and rougher. The in-situ reflectance curve shows a drop at the nucleation stage. Then, at the coalescence stage, grains continue to grow and start to coalesce. The surface becomes smoother and the optical reflectance value rises. Finally, the reflectance stops to increase and 2D growth of the AlGaN begins. If the mismatch strain is released adequately at the nucleation and coalescence stages, then AlGaN will be relaxed in the beginning of 2D growth stage. Otherwise, the remaining stress will be released at the 2D growth stage by forming new dislocations, specifically, threading dislocations[26].
![(Color online) Schematic diagram of in-situ reflectance curve in initial stage of AlGaN growth[25].](/Images/icon/loading.gif)
Figure 2.(Color online) Schematic diagram of in-situ reflectance curve in initial stage of AlGaN growth[25].
Based on this method, over 2 μm Al0.18Ga0.82N template layer without crack was successfully grown on AlN/sapphire substrate. Its relaxation is about 90% and the AlN mole fraction is about 18%, the reflectance curves of two samples are shown in Fig. 3. The growth process is similar to the one shown in Fig. 2. However, the process from 3D to 2D is related to their growth conditions. It is shown that a much longer time is needed to achieve 3D to 2D growth when the GR of AlGaN layer reduces. The full width of half maximum (FWHM) values of X-ray diffraction (XRD) (002) and (102) reflection measured by rocking curves are decreased to (206, 315) for the sample with small GR. Compared with the values for the sample with large GR (153, 549), the FWHM values of the (102) reflection obviously decrease. This indicates that the density of edge dislocations reduces during the process from 3D to 2D.
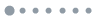
Figure 3.(Color online) The in-situ reflectance curves of AlGaN samples with different growth rate (GR). The GR controlled by TMGa flow rate, it is 34.7 sccm for the sample with small GR, 69.4 sccm for the sample with large GR.
3.2. Vacancy defect in AlGaN layers
Due to the large crystal mismatch and different atom mobility of Ga and Al atoms, the defect density in AlGaN material is as high as 108−1010 cm−3. For UV LDs, AlGaN material must be used as waveguide layers and the active region. In this case, carrier injection efficiency and radiative recombination efficiency of MQWs may decrease due to the loss of carriers resulted from serious non-radiative recombination. Therefore, defect states in AlGaN layer and their suppression methods must be investigated. Previously, the influence of defects on performance of UV LDs have been investigated by many groups. Tsuzuki[27] fabricated a 358 nm UVA LD by using a GaN/AlGaN MQW active layer grown on a low dislocation density grooved-AlGaN template, which dislocation density was as low as 1 × 108 cm–2. This UV LD exhibits a lower current density of 3.8 kA/cm2 at 7 °C. In 2015, Crawford[28] applied overgrowth of AlGaN templates patterned with submicron mesas for achieving reduced-through dislocation density (TDD) templates of (2–3) × 108 cm–2 for AlGaN LDs. He successfully demonstrated pulsed-current operation of 353 nm wavelength LDs at room temperature.
Except for dislocations and impurities, point defects are also critical defects in AlGaN layers. We have used positron annihilation experiments to investigate point defects in AlGaN layers, and used responsivity of AlGaN detectors to judge the transport ability of carriers. Figs. 4(a) and 4(b) show the low-momentum parameter S and the high-momentum parameter W as functions of positron incident energy for the five AlGaN samples, where the AlN mole fraction of AlGaN is 0%, 2.6%, 3.77%, 5.44%, and 6.47% for samples T0, T1, T2, T3, and T4, respectively. Fig. 4(c) shows the relationship between W and S parameter of these five samples. It is found that as the AlN mole fraction increases, the W parameter value decreases and the S parameter value increases, the parameter W varies linearly with S for these five samples. This indicates that the only type of point defect in the AlGaN layer is mainly negatively charged[29] and its concentration increases with the increase of AlN mole fraction. Because this kind of point defect is a negative center, it is most likely to be a Ga vacancy defect because formation energy of Ga vacancy defect is slightly lower than that of Al vacancy defect[30, 31]. Fig. 4(d) shows the peak responsivity of AlGaN detectors and S parameter versus AlN mole fraction in i-AlGaN. Peak responsivity decreases with the increase of AlN mole fraction of AlGaN, indicating that the transport ability of carriers reduces in AlGaN with higher AlN mole fraction. This is consistent with the variation of vacancy density in AlGaN. It is necessary to control the concentration of vacancy defects for the AlGaN material to enhance the injection efficiency of carriers[32]. The investigation of influence of vacancy defects on the performance of UV LDs is underway.
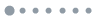
Figure 4.(Color online) Dependence of the low momentum parameter S (a) and high momentum parameter W (b) on positron incident energy in these five samples. (c) Relationship between S and W of the five samples. (d) S parameter and peak responsivity of AlGaN detector versus AlN mole fraction of AlGaN.
We have also found that Ga vacancy defects act as acceptors in n-AlGaN layer, which passivate donors in Si dopped AlGaN. This increases the resistivity of the n-AlGaN layer[33]. Increasing the GR and reducing the growth temperature is helpful for suppressing the formation of Ga vacancy, and therefore a AlGaN film with resistivity as low as 0.005 Ω∙cm can be obtained. The resistivity values as functions of AlN mole fraction of n-AlGaN layers reported by many groups are shown in Fig. 5, while our results are shown as red solid star symbols.
![(Color online) Previously reported resistivity value as a function of the AlN mole fraction of n-AlGaN layers. Our results are shown as red solid star symbols[33].](/Images/icon/loading.gif)
Figure 5.(Color online) Previously reported resistivity value as a function of the AlN mole fraction of n-AlGaN layers. Our results are shown as red solid star symbols[33].
3.3. Observation of localization effect in GaN/AlGaN ultraviolet quantum well
Due to the fluctuation of the InN mole fraction in InGaN, In-rich clusters will form in the InGaN layer, which act as localization states for carriers and hinder carriers to defect to regions and recombine there. Therefore, the emission efficiency is very high, even though the dislocation density is as high as 108−1010 cm−3[22, 23]. However, localization effects become weak when the InN mole fraction of InGaN decreases. The emission efficiency of UV quantum wells decreases rapidly and is more sensitive to dislocation density. This is harmful for UV LDs because the quantum well layers in UVA LDs usually are AlGaN, GaN, or InGaN with low InN mole fraction.
To increase the emission intensity of the UV quantum well, the emission mechanisms of GaN/AlGaN quantum well were studied by using temperature dependent photoluminescence (TDPL) and a 325 nm He−Cd continuous wave laser excitation. Two single GaN/AlGaN quantum well structures with different thicknesses of GaN quantum well of 3 and 6 nm were grown on the AlGaN template obtained by the method introduced in Section 3.1. They are named sample A and sample B, respectively. In these two samples, no other GaN layer is contained except for the GaN quantum well. Thus, the emission peak at about 360 nm comes from the GaN quantum well. The variations of peak energy with temperature are shown in Fig. 6. It is found that “V-shape” temperature dependence of photoluminescence (PL) peak energy exists in these two samples, which is similar to the phenomenon observed in InGaN multiple quantum wells[22, 23]. This indicates that localized states also exist in GaN quantum wells. In addition, we found that the blueshift of the peak increases with increasing thickness of GaN quantum well, which suggests that the localization effect is enhanced for a thicker GaN quantum well. It also results in a longer emission wavelength of thicker GaN quantum well at room temperature. We speculated that localized states are induced by the fluctuations of layer thickness of GaN QWs. Thus, the introduction of modified localization effect in GaN QWs may be a method to enhance the emission efficiency of GaN/AlGaN QW active region.
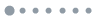
Figure 6.(Color online) PL peak energy each as a function of temperature for samples A (3 nm) and B (6 nm).
3.4. Suppression of the leakage of carrier by designing the structure of UV LDs
For UV LDs with a lasing wavelength less than 370 nm, the optimized Al mole fraction of AlGaN cladding layers should be higher than 20%[1−6, 14−16] to obtain good optical confinement. However, this is too high to grow on free standing GaN substrate directly due to the huge stress between AlGaN cladding layers and GaN substrate. Two methods to grow a high AlN mole fraction AlGaN template layer were introduced in Section 3.1. However, the crystal quality of AlGaN cladding layers is not as good as that of AlGaN with lower AlN mole fraction when grown on GaN substrate. This will lead to an increase of threshold voltage and threshold current density of UV LDs[10, 27]. In order to achieve short lasing wavelength of UV LDs, on the one hand, we need to optimize the growth condition to improve crystalline quality of AlGaN cladding layer; while on the other hand, we can design the structure of UV LDs based on high quality low AlN mole fraction of AlGaN cladding layers.
A schematic diagram of LD structure is shown in Fig. 7, where the Al content of AlGaN CL is about 7% and the Al content of AlGaN waveguide (WG) layer is about 3%. The optical confinement factor is higher than 4%[15], which is large enough for UV LDs[34, 35]. However, in this case, due to the small potential barrier energy between QW region, WG layers, and CL layers, the confinement effect for carriers is relatively weak, the carrier concentration in AlGaN upper WG layer will be relatively large, and more carriers stay and recombine in the UWG layer, as shown in Fig. 8. This leads to a reduction of the accumulation rate of carriers in QW region. The carriers in WG layers do not contribute to stimulated emission. Thus, a higher threshold current should result. In order to suppress the carrier loss in UWG layers, thinner AlGaN WG layers and an n-AlGaN hole block layer were used in UV LDs. A comparison of LD1 of Fig. 8(a) with LD2 of Fig. 8(b) shows that the accumulation rate of injected carriers in QW layer of LD1 increases and 366 nm UVA LD lasing was achieved[15]. Based on this modified structure, another UVA LD with lasing wavelength of 357.9 nm was also fabricated by using an increased AlN mole fraction of AlGaN WG layer[16]. The electroluminescence spectrum of the latter UV LD under room temperature (RT) pulsed operation condition at an injection current of 1550 mA is shown in Fig. 8(c), and its output power as a function of injected current measured at RT is shown in Fig. 8(d). The inset is a photo of the laser beam image formed on the white paper screen.
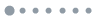
Figure 7.(Color online) The schematic diagram of LD structure.
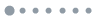
Figure 8.(Color online) Spatial distribution of electron concentration around WG layers and active region under different injection current values from 20 to 300 mA for samples LD1 with 50 nm-thick WG layer (a), LD2 with 150 nm-thick WG layer (b). (c) Shows lasing wavelength of 357.9 nm in the electroluminescence spectrum of another UV LD under RT pulsed operation condition at an injection current of 1550 mA. (d) Shows the RT output power of the 357.9 nm LD as a function of injected current. The inset shows a photo of the laser with the blue far field pattern of the laser beam image formed on the white paper screen.
3.5. Suppression of thermal effect in UV LDs
UV LDs are potential light sources of various applications, such as ultraviolet curing and materials processing. For these applications, high output power is required to obtain, for example, high UV curing speed and quick cuttings of thick metal. In addition to the slope efficiency (SE) and threshold current of LDs, thermal rollover phenomenon at high injection current and the catastrophic optical mirror degradation (COMD) at facets are also limiting factors for their output power[1, 16]. Therefore, improving the characteristic temperature T0 and reducing the junction temperature of UV LDs may be solutions for high power LDs. The thermal properties of GaN UV LDs have been reported by some research groups, Taketomi[12] and Crawford[28]et al. measured characteristic temperature T0 of their UV LDs, it is 119 and 140 K in the temperature range of 20−60 °C, respectively. Tsuzuki et al.[27] fabricated a 358 nm UV LD with a high characteristic temperature T0 of 174 K in the temperature range of 7−27 °C, they attribute higher T0 to low density of dislocation or nonradiative recombination centers. Yoshida et al.[36] of Hamamatsu Corporation investigated the temperature characteristic of a GaN/AlGaN MQW LD with lasing wavelength of about 360 nm in detail. They have found that the characteristic temperature in the low temperature range is 130 K. Meanwhile, in the high temperature range, it drops down to a value of 90 K. They believe that the decrease of T0 may be due to the increase of nonradiative recombination, as well as the increase of electron current overflow from the active region to the p-cladding layer at higher temperature.
We also study the thermal characteristics of two UV LDs with different WG structures LD A and LD B under pulsed and CW operation[17], as shown in Fig. 9. The lasing wavelength is 384 nm under CW operation. The WG layer thickness of LD B (120 nm) is larger than LD A (80 nm), the absorption loss of LD A is larger than that of LD B. The threshold current (Ith) increases and slope efficiency (SE) slightly decreases when the temperature increases from 30 to 70 °C. The relationship of ln(Ith) with the temperature (T) has been derived and is fitted by using linear relation for both LDs, as shown in the insets of Figs. 9 (a) and 9(b). The calculated characteristic temperature T0 of LD A and LD B is 139 and 138 K, respectively. These values are comparable to those of previously reported UV-LDs in the literature[12, 27, 28, 36], and the temperature stability of LD B is close to that of LD A. However, under CW operation, the dependence of output power on temperature is very different for LD A and LD B. For LD A, its Ith increases and SE decreases quickly with increasing temperature, and it does not lase, even though the injection current increases to 1.4 A at temperature of 70 °C. For LD B, the Ith increases and SE decreases much slower than those of LD A, and Ith increases only 150 mA when the measured temperature increases from 25 to 70 °C. The output power of LD A deteriorates larger than that of LD B with increasing temperature. This indicates that the junction temperature of LD A is higher than LD B under CW operation. This is attributed to the stronger self-heating effect of LD A due to larger optical absorption loss. Controlling junction temperature is more important for UV LDs operated under CW mode because they usually have lower characteristic temperature (T0) compared with GaN based blue and violet LDs. Fig. 10 shows P−I−V curves of LD A and LD B measured from zero current to a large injection current of 3 A. The I−V curves of two LDs are quite similar to each other. However, the output power decreases when the injection current increases to higher than 1.9 A for LD A due to thermal rollover phenomenon, and such a phenomenon is not observed for LD B until 3 A. This indicates that the suppression of the self-heating effect to decrease the junction temperature is very important for high power CW UV LDs.
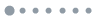
Figure 9.(Color online) Pulsed light output power versus injection current of LD A (a) and LD B (b) as a function of temperature. Temperature dependences of CW P−I−V characteristics of LD A (c) and LD B (d). The insets of (a) and (b) show ln(Ith) as a function of temperature for LD A (a) and LD B (b).
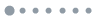
Figure 10.(Color online) P−I and I−V curves of LD A (empty symbols) and LD B (full symbols) under CW operation for LD A and LD B.
Another method to decrease the junction temperature is to use flip chip package (p-side down on sub-mount) to accelerate heat dissipation[18]. The chips were packaged with n-side down on sub-mount (named LD B’) or p-side down on sub-mount (named LD B’’), respectively. Fig. 11 shows I−V and P−I curves of LDs under CW operation. The red date points are the output power and voltage date of LD B’ and the black points are the ones of LD B’’. It can be seen that the output power increases with increasing injection current for both LD B’ and LD B’’ at first, then it decreases when the injection current increases to higher than 2.4 A for LD B’ due to thermal rollover phenomenon, and such a phenomenon is not observed for LD B’’ until 4 A. This indicates that the flip chip package (p-side down on sub-mount) is an effective method to accelerate heat dissipation and increase the maximum output power of UV LDs.
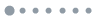
Figure 11.(Color online) I−V curves (square points) and P−I curves (circle points) of LD B’ (red) and LD B’’(black) under CW operation.
3.6. Mechanisms of cavity facet degradation for GaN-based laser diodes
Degradation mechanisms are a key factor to improve the reliability of GaN-based LDs. Many researchers have studied the degradation mechanisms of GaN based LDs previously. Some groups found that the degradation of active region is one reason for the degradation of GaN LDs[37−39], which can be attributed to the increase in nonradiative recombination due to the deep-level states induced by vacancy defects. Another reason is the variation of junction temperature, which is caused by the increase of the series resistance because of the degradation of the Ohmic contact. A higher junction temperature also leads to an increased leakage current[40] and a high non-radiative recombination rate. Catastrophic optical mirror damage (COMD) related to high power optical densities is also a common degradation mode occurring on the facet of LDs. The COMD in GaN-based LDs shows a thermal procedure for material decomposition, melting of (Al, In) GaN, and even a partial vaporization in active region and waveguide layers. A typical effect of the consequences of COMD in GaN-based LDs is the void cavities or gallium droplets on the facets[41−43].
One new mode of facet degradation was found during our experiment with unsealed blue-violet LDs with lasing wavelength of 434 nm[44]. The aging curve of the optical power and the corresponding voltage curve for the unsealed LD is shown in Fig. 12. The optical output power of the unsealed LD remains at a constant value within the initial 30 h and then decreases accompanied by an irregular undulation of the output power. The voltage remained unchanged during the testing process. This indicates that neither deterioration of the electrode quality nor leakage currents occurs during testing. Fig. 13 presents the images of the front facet for the initial and aged LDs. A biforked deposit was observed on the facet after 1000 h of aging. Deposit growth is believed to be responsible for the undulation of the optical power during the degradation of the unsealed LD. With an increase in the sediment thickness, the reflectance of the facet changes, and thus the resonance property of the cavity is partially damaged. Energy dispersive X-ray spectrometer (EDS) mapping was employed to analyze the chemical composition of the sediment. This reveals that the sediment is composed of the elements of silicon (Si), oxygen (O), aluminum (Al), and gallium (Ga) with different atomic percentages, respectively. According to the analysis, Al and Ga elements are from Al2O3 front facet coating and GaN epilayer. The biforked deposit should be SiO2. It is proposed that the splitting of water molecules induced by high-energy photons triggers the deposition of SiO2[44]. The deposits on the facet should be responsible for the reduction of the LDs’ output power.
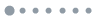
Figure 12.(Color online) Optical output power curve (red) and the corresponding voltage curve (blue) as a function of the aging time for the unsealed LD under a CW operation with an injection current of 800 mA.
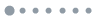
Figure 13.(Color online) Optical micrographs of the top view of LD front cavity facet for virgin (a) and aged (b) LD, respectively, where the waveguide ridge region can be seen by two green parallel lines. The deposits at front facet are marked by a red ellipsoidal circle in (b). SEM images (c) of the front cavity facet for aged LD. A biforked deposit is clearly observed in the side view.
For UV LDs with higher energy of photons, the facet degradation should be more serious. White spot deposits were observed only in the front cavity facet around MQW region below ridge in UV LDs after 48 h of aging and is not observed outside the ridge, as shown in Figs. 14(a) and 14(c), where MQW region is between two blue dotted line. This indicates that the formation of the white spot deposits in cavity is related to laser action. Figs. 14(b) and 14(d) are the EDS images for the regions in Fig. 14(a) marked with red ellipsoidal circle and thick red crosshair, respectively. It is found that the location of white spot deposits contains higher concentration of Si and O elements. There should be SiO2. The mechanism should be similar to the facet degradation mechanism observed in the blue-violet LDs[44] but the GR of deposits is much faster. Thus, improving the tightness of device package is necessary to avoid the fast degradation of GaN-based LDs, especially for UV LDs. In addition, an increase of nonradiative recombination in active region was observed in UV LDs. The related experimental data are being sorted out and will be published later.
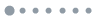
Figure 14.(Color online) (a) SEM images of the front cavity facet for aged flip chip packaged LD with lasing wavelength of 384 nm, where the QW region is located between two parallel dashed blue lines; (c) is the enlarged image of (a) under ridge region; (b) and (d) are the EDS images for the regions in (a) marked with red ellipsoidal circle and thick red crosshair, respectively.
4. Summary
In this paper, we outline major challenges in the realization of UV LDs and the technologies required to respond to them. In order to improve the performance of UV LDs, a thick layer of high crystal quality AlGaN film without cracking, a high emission efficiency active region, a good optical waveguide structure, and a relatively low junction working temperature are important. In order to relieve the mismatch stress of the AlGaN template, we used a AlN modulation layer to change the growth mode of AlGaN layer, a high crystal quality AlGaN film without cracking was obtained. The emission mechanism, cavity facet degradation mechanisms, and the optimized design of device structure for UV LDs were studied. With these techniques, RT pulsed oscillation of AlGaN UVA LD has been realized, whose lasing wavelength is 357.9 nm. Combined with the suppression of thermal effect, the high output power of 3.8 W UV LD with lasing wavelength of 386.5 nm was also fabricated.