0 Introduction
As an inertial instrument, the IFOG is an all-solid-state instrument that utilizes the Sagnac effect, and it has several advantages such as good stability, low power consumption, high reliability, etc. IFOG becomes one of the mainstream instruments in inertial navigation and strategic applications[1], which is widely used in aviation, aerospace, weapons systems and many industrial areas[2-4]. With the long-haul navigation and guidance requirements of the strategic-grade weapon launching platforms, submarines, large-scale surface ships and submarines, the requirements of precision are getting higher and higher[5-10], such as some applications require that the precision of the IFOG should be better than 0.001 (°)/h in the geomagnetic field of 0.5 Gs.
Magnetic non-reciprocity is one of the main non-reciprocal error sources of IFOGs[11-12]. Methods for suppressing magnetic non-reciprocity include software compensation, fiber coil compensation and magnetic shielding, etc. The software compensation method uses a magnetometer to measure the strength of a magnetic field and then make use of the test results, compensating the magnetic field error by software method[13]. This method only focuses on the axial magnetic field[14]. In the fiber coil compensation method, multiple compensating fiber coils are installed in the IFOG as well as a sensitive fiber coil, which will make the size and weight of the IFOG increase, and make the sensitive angular velocity of the IFOG become more complicated. Magnetic shielding method is widely used in engineering[15-17]. However, in order to meet the requirements of high-precision IFOGs, it is necessary to use two or more layers of materials for shielding effectiveness, which will obviously increase the weight and volume of IFOG.
In this paper, we analyse the effect of magnetic non-reciprocity on the bias error of IFOG and propose methods of improvement that make the fiber de-twist to reduce the magnetic field sensitivity of the fiber coil and connect the shielding materials by laser welding to increase the shielding effectiveness. Through these improvements, the precision of the fiber coil in the magnetic field and temperature environment is improved.
1 Theory
Magnetic non-reciprocity includes Faraday non-reciprocity and non-Faraday non-reciprocity. Faraday non-reciprocity is a magneto-optical phenomenon, when the polarization-maintaining fiber coil which has a birefringence of Δβ is located in a magnetic field that parallels to the radial direction of the fiber coil. The two linearly polarized lights that transmit in opposite directions in fiber coil will induce a phase shift
$\Delta \mathop \phi \nolimits $:
$ \Delta \mathop \phi \nolimits_{} = \dfrac{{2\pi \Delta \beta L}}{\lambda } = 2VHL $ (1)
where V is the Verdet constant, H is the magnetic field strength.
Ideally, the two lights that propagate in opposite directions can form a closed loop, and the circular birefringence phase difference can offset each other. But when the fiber is twisted, as shown in Fig.1, it will cause additional circular birefringence and induce a phase shift as[18]:
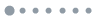
Figure 1.Schematic diagram of twisting of fiber
$ \Delta {\varphi _R} = \dfrac{{4VH}}{{\Delta \beta }}{\displaystyle\int\limits_0^L }{\tau ({\textit{z}})} {\rm{sin}}\left(\dfrac{{\textit{z}}}{r} - {\theta _0}\right){\rm{d}}{\textit{z}}$ (2)
where L is the length of the fiber coil, r is the radius of the fiber coil, τ(z) is the twist rate of the fiber, and θ0 is the angle of the magnetic field and the plane of the fiber coil.
Non-Faraday non-reciprocity effect is that when the fiber is wound into a fiber coil, the fiber will be bent, so that the refractive index of the fiber near the axis of the fiber coil is always greater than the refractive index of the fiber far from the axis, which will cause a mode drift of the transmitted light in the axial magnetic field and produce a phase shift[11] as:
$ \Delta \mathop \phi \nolimits_A {\rm{ = }}12\dfrac{{VH\lambda }}{n}N $ (3)
where N is the turn number of the fiber coil.
According to Eq.(2) and Eq.(3), the bias drift of the IFOG induced by magnetic non-reciprocity can be expressed as:
$ \Delta {\varOmega _R} = \dfrac{{4VH}}{{\Delta \beta K}}\displaystyle\int\limits_0^L {\tau ({\textit{z}})} {\rm{sin}}\left(\dfrac{{\textit{z}}}{r} - {\theta _0}\right){\rm{d}}{\textit{z}} $ (4)
$ \Delta \mathop \varOmega \nolimits_A {\rm{ = }}12\dfrac{{VH\lambda }}{{nK}}N $ (5)
where K is the scale factor of the IFOG.
It can be known from Eq.(4) and Eq.(5) that the bias drift of the IFOG is proportional to the strength of the magnetic field, either in the axial magnetic field or in the radial magnetic field. In addition, the bias error is also related to the twist rate of fiber. Therefore, in order to reduce the influence of magnetic field on the bias error of IFOG, we need to reduce the strength of magnetic field and the twist rate of fiber.
In practical application environment, in order to reduce the influence of the magnetic field, the fiber coil is usually shielded by permalloy material of high permeability[16], The shielding method is to place the fiber coil in the cavity that is formed by the base and the upper cover, and then connect the base and the upper cover by screws. As the base and the upper cover are made of permalloy, which will realize the shielding of fiber coil from the magnetic field[19]. Using this method, the magnetic field strength can be attenuated by 23 dB with 2 mm thickness permalloy material, which achieves a good magnetic shielding effectiveness and meets the using of low- and medium-precision IFOGs. However, for high-precision IFOGs, that attenuation does not meet the application requirements. As the fiber coil has a typical magnetic field sensitivity of 1 (°)·h−1·Gs−1[12], when the IFOG precision is better than 0.001 (°)/h in the geomagnetic field of 0.5 Gs, the attenuation of magnetic field strength is required to be higher than 54 dB. Thus, the above shielding method is no longer used; Besides, the 2 mm thick material will lead to an increase in the weight of the IFOG.
When the permalloy material is used to shield the geomagnetic field, the shielding diagram is shown in Fig.2, and the equivalent circuit diagram is given in Fig.3. Theoretically, since the magnetic resistance of the permeability material is much smaller than the air magnetic resistance, it has a good shielding effectiveness, but there is a gap when the base and the outer cover are connected by screws, which can cause an increase in magnetic resistance of the connection and result in poor shielding effectiveness. From Fig.2 and Fig.3 , the H1 can be obtained as:
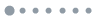
Figure 2.Shielding diagram of the geomagnetic field
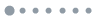
Figure 3.Shielding equivalent circuit diagram of the geomagnetic field
$ {H_1} = \dfrac{{{R_{\rm{m}}}}}{{{R_{\rm{m}}} + {R_0}}}{H_0} $ (6)
And the shielding effectiveness SE is:
$ \begin{split} S\!\!E = &20{\rm{lg}}\left( {\dfrac{{{H_0}}}{{{H_1}}}} \right)=20{\rm{lg}}\left( {\dfrac{{{R_{\rm{m}}} + {R_0}}}{{{R_{\rm{m}}}}}} \right){\rm{ = }}\\ & 20{\rm{lg}}\left( {1 + \dfrac{{{R_0}}}{{{R_{\rm{m}}}}}} \right) \end{split} $ (7)
where Rm is the magnetic resistance of the material, R0 is the magnetic resistance of the air, H1 is the strength of the magnetic field inside the shielding cavity, H0 is the strength of the magnetic field outside the shielding cavity.
It can be seen from Eq.(6) and Eq.(7) that when there is a gap in the connection of the shielding material, the magnetic resistance will increase and the shielding effectiveness will reduce. Figure 4 is the simulation relationship between the distance of the axial connection gap of the shielding material and the attenuation of the strength of the internal magnetic field. It can be seen that the shielding efficiency will decrease sharply when there is connection gap between the shielding materials.
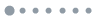
Figure 4.Relationship between the distance of the axial connection gap and the attenuation of the strength of internal magnetic field
In order to improve the shielding effectiveness, it is necessary to reduce the influence of the gap. In this paper, we connected the base and the cover by laser welding, which can avoid the connection gap. In addition, when the connection gap was welded by laser, it can also reduce the influence of air convection and improve the precision of the fiber coil[20].
From Eq.(4) we know the magnetic field sensitivity of the fiber coil S is:
$ S {\rm{ = }}{\varOmega _R}/H = \dfrac{{4V}}{{\Delta \beta K}}\displaystyle\int\limits_0^L {\tau ( {\textit{z}})} {\rm{sin}}\left(\dfrac{ {\textit{z}}}{r} - {\theta _0}\right){\rm{d}}z $ (8)
$ {\rm{set}}\;\tau ({\textit{}}{\textit{z}}) = {\tau _0}{\rm{sin}}\left(\dfrac{{\textit{z}}}{r}\right) $ (9)
$ {\rm{We }}\;{\rm{can }}\;{\rm{obtain}}\;\;\;{{S }} = \dfrac{{2V{\rm{cos}}{\theta _0}}}{{\Delta \beta K}}L{\tau _0} $ (10)
So S is proportional to the t0. When V=90 μrad·Gs−1·m−1, λ=1550 nm, r=50 mm, Δβ=2 000 rad/m, θ0=0, and τ0=100 (°)/m, we can find S=13.3 (°)·h−1·Gs−1, which cannot meet the application requirements. In fact the twist rate of fiber is not constant, but randomly distributed along the fiber. It can be from 0 (°)/m to thousands (°)/m, so it is difficult to compensate. In this paper, we make the fiber de-twist before the fiber coils were wound. The method is to measure the torque in the fiber through some sensors, and feed back the test results to the control end. The control end makes the rotating motor start work, the angle of fiber twist is offset by the angle of motor rotation, and the fiber is de-twisted.
2 Experiment setup
In order to test the effect of fiber de-twist on the field sensitivity of the fiber coil, we fabricated three fiber coils whose fiber was with de-twist and three fiber coils whose fiber was without de-twist, and test the axial magnetic field sensitivity of the fiber coil in the magnetic field of±5 Gs, ±10 Gs, ±20 Gs, ±30 Gs, ±40 Gs.
In order to test the effect of the connection gap that was welded by laser on the shielding effectiveness of the fiber coil, we made the fiber coil whose fiber has been de-twisted into three different states, as Fig.5 shows: (1) The fiber coil is not shielded, marked as state 1 (as shown in Fig.5(a)); (2) The fiber coil is shielded by the base and the upper cover that was made of permalloy material; the connection gap of the base and the upper cover was connected by screws, marked as the state 2 (as shown in Fig.5(b)) ; (3) The fiber coil is shielded by the base and the upper cover, the connection gap was welded by laser, marked as state 3 (as shown in Fig.5(c)). We put the fiber coil in the Faraday magnetic field generator system, set the magnetic field strength as ±5 Gs, ±10 Gs, ±20 Gs, ±30 Gs, ±40 Gs respectively, and the bias of the IFOG was tested.
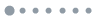
Figure 5.Diagrammatic cross-section of the fiber coils in three different states
In order to test the influence of the connection gap that was welded by laser on the temperature performance of the fiber coil, the fiber coils in state 2 and state 3 were placed in the temperature chamber. The temperature of the test is from −40 ℃ to 60 ℃, the rate of temperature change is 1 ℃/min and the hold time of the highest and lowest temperature is 60 min, and the bias of the IFOG was tested.
3 Results and discussion
The magnetic field sensitivity of the fiber coil is shown in Tab.1. It can be seen that the magnetic field sensitivity of the fiber coil whose fiber has been de-twisted is about 10.6% of that fiber without de-twist, so the fiber de-twist can effectively reduce the magnetic field sensitivity of the fiber coil.

Table 1. Magnetic field sensitivity of the fiber coil
Table 1. Magnetic field sensitivity of the fiber coil
No. | Magnetic field sensitivity of the fiber coil /(°)·h−1·Gs−1 | - | Fiber without de-twist | Fiber with de-twist | 1 | 16.235 2 | 1.810 6 | 2 | 11.383 9 | 1.052 3 | 3 | 13.802 5 | 1.528 4 | Average | 13.807 2 | 1.463 8 |
|
The bias of the IFOG in different magnetic field strength is shown as Fig.6. We find that there is a linear relationship between the bias of IFOG and the magnetic field strength: the greater the magnetic field strength is, the greater the influence on the bias is, which is consistent with the theoretical analysis. When the shielding state is different, the magnetic field sensitivity of the fiber coil will differ greatly, as shown in Fig.6 and Tab.2. Compared to the fiber coil in state 1, the fiber coil in state 2 has a good shielding effectiveness, which can achieve to 34.8 dB, but as there is a gap in the connection, the magnetic field sensitivity of the fiber coil in state 2 can only reduce to 0.026 5 (°)·h−1·Gs−1, which cannot meet the requirements of high-precision IFOG. However, when the connection gap was welded by laser, as the fiber coil in state 3, the shielding effectiveness can be improved to 64 dB, and the magnetic field sensitivity of the fiber coil can be reduced to less than 0.000 4 (°)·h−1·Gs−1, which greatly improves the precision of the fiber coil in the magnetic field.
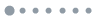
Figure 6.Bias (Y-axis) of the fiber coil in different magnetic fields. (a) Fiber coil is in state 1; (b) Fiber coil is in state 2; (c) Fiber coil is in state 3

Table 2. Magnetic field sensitivities of the coil in different states
Table 2. Magnetic field sensitivities of the coil in different states
Axial | Magnetic field sensitivity
of state 1 /(°)·h−1·Gs−1 | Magnetic field sensitivity
of state 2 /(°)·h−1·Gs−1 | Shielding effectiveness
of state 2
| Magnetic field sensitivity
of state 3 /(°)·h−1·Gs−1 | Shielding effectiveness
of state 3
| Notes: The fiber coil in state 1 was un-shielding; The fiber coil in state 2 was shielded by permalloy material, but the connection gap was not welded; The fiber coil in state 3 is shielded by permalloy material, and the connection gap was welded by laser. | X | 1.052 3 | 0.026 5 | 31.98 | 0.000 40 | 68.40 | Y | 0.584 4 | 0.018 1 | 34.83 | 0.000 31 | 64.70 | Z | 0.395 4 | 0.008 0 | 33.88 | 0.000 23 | 64.71 |
|
The bias of the IFOG in different temperatures is shown in Fig.7 and Tab.3. We can find that when the connection gap was welded by laser, the precision of the IFOG in different temperature can be improved by more than 7.5%.
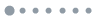
Figure 7.Bias of the IFOG in different temperatures. (a) Fiber coil is in state 2; (b) Fiber coil is in state 3

Table 3. Bias stability of the IFOG in the temperature of −40−60 ℃
Table 3. Bias stability of the IFOG in the temperature of −40−60 ℃
States | Uncompensated bias stability | Compensated bias stability | Connection gap unwelded | 0.041 0 (°)/h | 0.003 18 (°)/h | Connection gap welded | 0.036 5 (°)/h | 0.002 94 (°)/h | Performance improvements | 11.0% | 7.5% |
|
4 Conclusions
In this paper, we analyse the effect of magnetic non-reciprocity magnetic fields on the bias error of IFOG. According to the analysis results, we propose methods of improvement that make the fiber de-twist to reduce the magnetic field sensitivity of the fiber coil and connect the shielding materials by laser welding to increase the shielding effectiveness. Through the measurement of fiber de-twist, the magnetic field sensitivity of the fiber coil is reduced by 89.3%; Through the improvement of laser welding, the shielding effectiveness of the permalloy material is improved from 31 dB to at least 64 dB, the magnetic field sensitivity of the fiber coil is reduced from 0.026 5 (°)·h−1·Gs−1 to less than 0.000 4 (°)·h−1·Gs−1, the bias stability of the IFOG in different temperature is improved by more than 7.5%. These test results show that these improvements can improve the precision of IFOG in the magnetic field and temperature environment, and meet the performance requirements of high-precision IFOG.