Carbon foam is a typical porous material with superior properties, such as low density, high porosity, high temperature tolerance and excellent corrosion resistance[1], which can be applied in aeronautics, astronautics, chemicals, energy, environmental protection, and catalysis[2⇓-4]. The precursors of carbon foam include pitch, resin, coal or biomass[5]. Epoxy resin carbons have the advantages of high strength, high temperature resistance, corrosion resistance, and permeability resistance, etc., which can be applied in high temperature carbon composite, energy storage electrode, carbon foam materials, etc[6⇓⇓-9]. However, the research and application of carbon foam from epoxy resin (noted as EP CF) are greatly restricted by the low char yield of epoxy resin, and non-graphitization, poor mechanical strength and electrical conductivity[10]. Therefore, it is urgent to solve above problems of EP CF.
The preparation methods of carbon foam include template-assisted, foaming, direct pyrolysis, high temperature and high-pressure methods, etc[11-12]. Among these preparation methods, high temperature combined high pressure method demonstrated the advantages for tailoring the density and cell structure of carbon foam[13]. The increase of the graphitization degree of resin carbon materials can be divided into catalytic graphitization, carbon nanomaterial modified graphitization, and easy graphitization precursor modified graphitization. Compared with others, catalytic graphitization can decrease the graphitization temperature and reduce energy consumption. However, the residual catalyst in resin carbon will substantially affect the properties of carbon foam. The easy graphitization precursor modified method can improve the graphitization degree and char yield. While there may occur phase separation between easy graphitization precursor and epoxy resin, and it is difficult to prepare homogeneous carbon materials[14-15]. In recent years, many studies of carbon nanomaterials (graphene, carbon nanotube and their derivative) have been developed. Graphene has excellent thermal, mechanical and electrical properties. Therefore, graphene is considered to be a very promising carbon nanomaterial for the modification of resin precursors. As SP2 carbon material, graphene can form π-π conjugation with the aromatic ring of epoxy resin, which can promote the arrangement and stacking of resin with the graphene plane. Thus it can be expected to improve the graphitization degree and electrical conductivity of resin carbon[16-17]. In addition, graphene has excellent mechanical properties, which can be employed as a reinforcement for improving the mechanical properties of EP CF.
In this work, graphene modified EP CF was firstly prepared via heating mixing at 100 ℃ for 0.5 h with a combination of high temperature and high pressure foaming method. The structure and property of the modified EP CF were characterized by X-ray diffraction (XRD), Raman spectroscope, scanning electron microscope (SEM), high-resolution transmission electron microscope (HRTEM), digital resistance meter and electronic universal testing machine. Moreover, the study also explored the effect of graphene on the graphitization degree, electrical conductivity and compression strength of EP CF.
1 Experimental
1.1 Materials and reagents
Graphene was obtained from Northwestern Polytechnical University of Shanxi Engineering Laboratory for Graphene New Carbon Materials and Applications. The density, thickness of graphene are 0.02-0.1 g·cm-3 and 10-15 nm, respectively (Fig. S1). Epoxy resin E44 was purchased from Xi'an Resin Factory, China, with an epoxy equivalent of 210-240 and softening point temperature of 15-23 ℃. Dichloromethane was purchased from Chemical Reagent Co., Ltd (≥99.5%).
1.2 Material preparation
Typically, dichloromethane solvent was used for the mixing of epoxy resin and different content of graphene (0, 0.01%, 0.02%, 0.05%, and 0.10%, in mass). Subsequently, the mixture was put in 25 mL ceramic crucible at 100 ℃ for 0.5 h, and then foaming at 450 ℃ and 2 MPa for 3 h. Then, the obtained products were carbonized at 1000 ℃ for 3 h, and graphitized at 3000 ℃ for 0.5 h to prepare EP CF (Fig. S2(a)). In order to determine the foaming temperature, the thermogravimetric curves of epoxy resin were tested. The 60% thermal weight loss is happened in the range of 400-450 ℃. As a result, 450 ℃ was selected as the foaming temperature (Fig. S2(b)). The foaming process was shown in Fig. S2(c).
1.3 Material characterization
The phase structures of EP CF were analyzed by X-ray diffractometer (XRD, D/Max 2500 V·PC-1, Cu-Kα radiation). 10% (in mass) silicon powder was used as a marker, and the scanning rate was 5 (°)/min. The graphite interplanar distance (d002), grain stacking height (Lc) and graphitization degree (g) were calculated by Bragg, Scherrer and Mering-Maire formula, respectively. The graphite structures of EP CF were studied by Raman spectroscope (Alpha 300R) with a 532 nm laser irradiation. The morphology and microstructure of the EP CF were observed by tungsten filament scanning electron microscope (VEGA3 LMU) and high-resolution transmission electron microscope (HRTEM, JEM 2100F), respectively. Thermogravimetric analysis of epoxy resin was carried out by STA449F3 thermal analyzer (Naichi, Germany), and the temperature was raised to 700 ℃ at 10 ℃·min-1 in the Ar. The electrical conductivity of EP CF was obtained by digital resistance meter. The compressive strengths of EP CF were analyzed by electronic universal testing machine. The sample size is 10 mm× 10 mm×10 mm, and the loading rate is 0.5 mm·min-1. The electrical conductivity and compressive strengths of EP CF were the average value of three tests.
2 Results and discussion
2.1 XRD and Raman analyses
Fig. 1(a) is the XRD patterns of EP CF after graphitization at 3000 ℃ for 0.5 h. The diffraction peak of (002) crystal plane of crystalline graphite is near 2θ=26°. When the graphene content is 0.02% (in mass), the angle of (002) crystal plane diffraction peak is relatively small. The angle of (002) crystal plane diffraction peak of EP CF modified by 0.05% (in mass) graphene reaches the maximum (2θ=26.27°). While the angle of (002) crystal plane diffraction peak of EP CF modified by 0.10% (in mass) graphene is smaller than the 0.05% (in mass) graphene modified EP CF. It indicates that the high graphene content could aggregate in the epoxy resin, and thus hinder the graphite crystallite growth. The microcrystalline parameters of modified EP CF after graphitization at 3000 ℃ for 0.5 h are shown in Table S1. As shown in Table S1, the d002, Lc and graphitization degree (g) of EP CF0 are 0.343 nm, 3.35 nm and 8.42%, respectively. While the d002, Lc and g of EP CF0.05 were 0.342 nm, 10.22 nm and 23.2%, respectively. The graphitization degree of graphene modified EP CF is obviously increased by proper graphene content modification. Fig. 1(b) shows the Raman spectra of EP CF. The band at 1590 cm-1 is the G (graphite) band that originates from the stretching mode of sp2 hybridized orbitals of carbon-carbon bonds. The band at 1350 cm-1 is attributed to D (disorder) band, which is the breathing mode of sp2 hybridized carbon. The intensity ratio of the G to D band increases with the increase of graphene content, indicating that the proper graphene content can induce the graphite carbon growth of modified EP CF. ID/IG values of EP CF0 and EP CF0.05 is 1.286 and 0.231, respectively. The 2D peaks at 2700 cm-1 in all modified EP CF are observed, which show that the modified EP CF is turbostratic graphite and relative high degree of stacking[18-19]. Based on the XRD and Raman results, the proper graphene content can induce the graphite crystal growth and improve the graphitization degree, which can be helpful for improving the electrical conductivity and mechanical properties of EP CF.
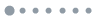
Figure 1.Structure parameters of EP CF modified by different contents of graphene after graphitization treatment at 3000 ℃ for 0.5 h(a) XRD patterns; (b) Raman spectra. Colorful figures are available on website
2.2 SEM and TEM analyses
Fig. 2 is the SEM images of modified EP CF by different graphene contents after graphitization treatment at 3000 ℃ for 0.5 h. All EP CF show 3D cell structures. With the increase of graphene content in the modified EP CF, the average cell size firstly decreases and then increases, and the cell shapes of all EP CF are round. The average cell sizes of EP CF0 and EP CF0.02 is 675 and 456 μm, respectively. However, the micropore numbers firstly increases and then decreases. The variation of average cell sizes and micropore numbers in EP CF could be substantially influenced by the heterogeneous nuclei of graphene and gas. But the excess graphene can aggregate in the epoxy resin, and decrease its heterogeneous nuclei effect for cell structure of EP CF (Fig. 2, Fig. S3)[20].
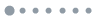
Figure 2.SEM images of modified EP CF by different graphene contents after graphitization treatment at 3000 ℃ for 0.5 h(a, a1) EP CF0; (b, b1) EP CF0.01; (c, c1) EP CF0.02; (d, d1) EP CF0.05; (e, e1) EP CF0.1
It is observed from Fig. 3 that the microcrystalline structures of EP CF0 and EP CF0.05 show obviously different. The EP CF exhibits microporous structure, entangled carbon ribbon and isotropic amorphous carbon, indicating EP CF with poor crystallinity (Fig. 3(a)). EP CF0.05 is less tangled microporous structure with longer lattice fringes and, demonstrating that the graphene can improve the ordered graphite carbon content of EP CF (Fig. 3(b)). The HRTEM result is consistent with the XRD and Raman analyses. The above carbon structure difference of EP CF can be explained from the epoxy resin molecular and graphene structure. The epoxy resin contains aromatic ring and the graphene is sp2 carbon, which can produce the π-π interaction between them. The epoxy resin molecules are arranged and grown along the plane direction of graphene in the process of melting, carbonizing and graphitizing. In addition, the volume shrinkage of graphene is smaller during the carbonization and graphitization treatment, while the epoxy resin has a larger volume shrinkage during the carbonization and graphitization treatment process. The mismatch in the thermal expansion coefficient between them can increase the interfacial thermal stress, and promote the stress graphitization of EP CF (Fig. 3(c))[17].
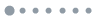
Figure 3.HRTEM images of EP CF and its graphitization mechanism(a) EP CF0; (b) EP CF0.05; (c) Schematic diagram of graphitization mechanism of EP CF treated at 3000 ℃for 0.5 h
2.3 Electrical conductivity
Electrical conductivity is an important property of carbon foam, which is used to characterize conductive ability of carbon foam. Fig. 4 and Table S2 presents the variation of electrical conductivity of modified EP CF with different contents of graphene at room temperature. It is observed that the electrical conductivity of the graphene modified EP CF firstly increases and then decreases with the graphene from 0 to 0.10% (in mass). EP CF0.05 can form a good electrical conductivity network of carbon matrix[21]. The electrical conductivity of EP CF0 and EP CF0.05 is 25.79 and 53.8 S·m-1, respectively. More graphene nanosheets in EP CF results in an increase in the crystallite growth of EP CF matrix. Thus it is beneficial to improve the electrical conductivity of the modified EP CF. In addition, the high electrical conductivity of graphene can contribute to the improvement of the electrical conductivity of EP CF. However, the electrical conductivity of the modified EP CF0.1 decreases. A possible reason is due to the aggregation of high graphene content, which hinders the carbon crystal growth and decreases the electrical conductivity of EP CF (Fig. 1, Fig. 3).
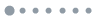
Figure 4.Electrical conductivity of EP CF modified by different contents of graphene after treatment at 3000 ℃ for 0.5 h
2.4 Compressive strength
The compressive strength of the graphene modified EP CF is shown in Fig. 5(a) and Table S2. The compressive strength of the graphene modified EP CF firstly increases and then decreases with an increase graphene content from 0 to 0.10% (in mass). The compressive strength of the EP CF0.01 and EP CF0.02 is 4.9 and 4.82 MPa, respectively. They are almost 1.5 fold of that of EP CF0. The improvement of the compressive strength could be related to the reinforcement effect from graphene, and reduce the crack elongation during the mechanical test. However, the compressive strength of the modified EP CF decreases when the graphene content increases to 0.10% (in mass) due to the aggregation of graphene content. It can significantly reduce the strength of EP CF. Fig. 5(b) shows typical stress-strain curves of the modified EP CF with different graphene contents. It is found that the three stages for the deformation mechanism of EP CF, such as elastic deformation, plastic deformation and final failure. The compressive strain of the EP CF0 is 0.0096%, whereas those of EP CF0.01, EP CF0.02, EP CF0.05 and EP CF0.1 are 0.208%, 0.228%, 0.187% and 0.1146%, respectively. The results indicate that graphene can toughening the EP CF and increase its failure strain. This can be originated from the micro-cracks and defects propagating via a deflection and blocking of graphene[22].
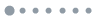
Figure 5.Mechanical properties of EP CF modified by different graphene contents after graphitization at 3000 ℃ for 0.5 h(a) Compressive strength; (b) Variation of stress with strain; Colorful figures are available on website
3 Conclusions
In this work, graphene modified EP CF was firstly prepared via a combination of high temperature and pressure, and graphitization methods. Results shows that the graphene can induce the crystal growth of EP CF, where the d002, Lc and g of EP CF0.05 are optimized to 0.342 nm, 10.22 nm and 23.2% compared to EP CF0 (0.343 nm, 3.35 nm and 8.42%). In HRTEM images, the EP CF0.05 exhibits microporous structure, longer lattice fringes and less tangled carbon ribbon. The average cell sizes and micropore numbers of EP CF can be regulated by the variation of graphene contents. With the increase of graphene content in the modified EP CF, the average cell size firstly decreases and then increases. The average cell sizes of EP CF0 and EP CF0.02 are 675 and 456 μm, respectively. Furthermore, the carbon crystal growth, electrical conductivity of EP CF can be significantly improved by the addition of graphene. Especially, the electrical conductivity of the graphene modified EP CF increases from 25.79 to 53.8 S·m-1 when the content of graphene increasing from 0 to 0.05% (in mass). Lastly, mechanical performance of EP CF could also be augmented by the incorporation of graphene. The compressive strength of the EP CF0.01 and EP CF0.02 are 4.9 and 4.82 MPa respectively. They are about 1.5 fold of that of EP CF0. Meanwhile, the compressive strain of the EP CF0 is 0.0096%, whereas the EP CF0, EP CF0.01, EP CF0.02, EP CF0.02, EP CF0.05 and EP CF0.1 are increased to 0.208%, 0.228%, 0.187% and 0.1146%, respectively. This study provides a guidance for the preparation of high performances EP CF.
Supporting Information
Supporting materials related to this article can be found at
https://doi.org/10.15541/jim20230385.
Effect of Graphene on Graphitization, Electrical and Mechanical Properties of Epoxy Resin Carbon Foam
YANG Pingjun1,2, LI Tiehu1,2, LI Hao1,2, DANG Alei1,2
1. School of Materials Science and Engineering, Northwestern Polytechnical University, Xi’an 710072, China; 2. Shaanxi Engineering Laboratory for Graphene New Carbon Materials and Applications, Xi’an 710072, China
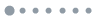
Figure S1.Graphene thickness analyzed by atomic force microscope
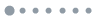
Figure S2.(a) Preparation of graphene modified EP CF; (b) Thermogravimetric curve of epoxy resin; (c) Foaming temperature curve of green EP CF

Table 1.
Crystalline parameters of EP CF modified by different graphene contents after treatment at 3000 ℃ for 0.5 h
Table 1.
Crystalline parameters of EP CF modified by different graphene contents after treatment at 3000 ℃ for 0.5 h
Sample | 2θ002/(°)
| d002/nm
| Lc/nm
| g/%
|
---|
EP CF0 | 25.9 | 0.3431 | 3.35 | 8.42 | EP CF0.01 | 25.6 | 0.343 | 3.62 | 11.22 | EP CF0.02 | 25.77 | 0.343 | 4.22 | 11.22 | EP CF0.05 | 26.27 | 0.342 | 10.22 | 23.2 | EP CF0.1 | 26.1 | 0.3425 | 4.46 | 16.5 |
|
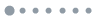
Figure S3.Cell sizes of different graphene contents modified EP CF prepared by graphitization treatment at 3000 ℃ for 0.5 h

Table 2.
Physical, electrical and mechanical properties of EP CF modified by different graphene content after graphitization treatment at 3000 ℃ for 0.5 h
Table 2.
Physical, electrical and mechanical properties of EP CF modified by different graphene content after graphitization treatment at 3000 ℃ for 0.5 h
Sample | Density/(g·cm-3)
| Electrical conductivity/(S·m-1)
| Compressive strength/MPa |
---|
EP CF0 | 0.470 | 25.79 | 3.13 | EP CF0.01 | 0.460 | 27.70 | 4.90 | EP CF0.02 | 0.469 | 27.79 | 4.82 | EP CF0.05 | 0.460 | 53.80 | 2.00 | EP CF0.1 | 0.463 | 45.90 | 3.66 |
|