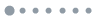
Figure 2.(Color online) CL image of (a) traditional GaN substrate. (b) GaN substrate improved by HVPE technology.
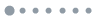
Figure 3.(Color online) (a) TEM image of InGaN/GaN SLs. (b) PL characteristics of sample A and sample B, where sample A is a conventional InGaN lower waveguide layer device, sample B is an InGaN/GaN SLs lower waveguide layer device.
In order to effectively suppress surface recombination and enhance the COD threshold of LDs, this study has incorporated ECR technology for the meticulous crafting of cavity surface thin films. Through the precise manipulation of bias voltage and power, coupled with the calibrated flow of oxygen and argon gases, we have facilitated a comprehensive material reaction and a uniform deposition process. Due to the small surface area of the GaN laser diode cavity facets, direct atomic force microscopy (AFM) measurement is very difficult. Therefore, we use polished silicon wafers as substrates, deposit the same material as the surface, and utilize AFM to measure the surface roughness of the deposited film, as shown in Fig. 4. The initial comparative interface imagery disclosed no pronounced visual disparities between the sample surfaces in their pre- and post-optimization states. In order to understand the surface characteristics more deeply, we have employed the root mean square (RMS) methodology for a quantitative assessment of surface roughness. The outcome of our data analysis elucidates that the high-reflection (HR) surface, refined through ECR technology, has witnessed a marked reduction in its RMS value from 0.43 nm to an impressive 0.13 nm. Similarly, the anti-reflection (AR) surface exhibited a decrease in RMS value from 0.2 nm to a minimal 0.11 nm. This enhancement is not solely indicative of improved surface smoothness; it also implies that the optimization of ECR technology can yield surfaces that are more conducive to curtailing the non-ideal photon escape, which in turn, augments the efficacy of LDs.
In the manufacturing process of semiconductor devices, the quality of the substrate plays an essential role. The density of substrate dislocations directly affects the uniformity of crystal growth and the final performance of the devices. In the AlInGaN material system, the traditional GaN substrate has a relatively high dislocation density, typically around 1.2 × 106 cm−2. High dislocation density not only reduces the optical and electrical performance of the crystal but can also lead to device degradation over long-term operation. Therefore, controlling the dislocation density of the substrate is particularly critical. To reduce the substrate dislocation density, in this experiment, we employed the HVPE technology, combined with multiple masking and 3D−2D growth methods, and finely optimized the epitaxial parameters. The detailed optimization growth path is shown in Fig. 1, where an approximately 4-micrometer-thick GaN buffer layer is grown by metal organic chemical vapor deposition (MOCVD), which has a high dislocation density at this stage. An SiO2 mask is then fabricated on this buffer layer using plasma-enhanced chemical vapour deposition (PECVD) at 300 degrees, with a spacing/mask ratio of 1 : 3. Subsequently, GaN crystals were sequentially grown in 3D−2D mode using HVPE technology. By growing thick GaN substrate to achieve stress self-stripping, self-supporting GaN crystal is obtained. Finally, the GaN single-crystal substrate is achieved through a process of cutting, grinding, and polishing. The GaN substrate before and after optimization was characterized in detail by cathodoluminescene (CL), as shown in Fig. 2. It is evident that within the same field of view, the dislocation density of GaN substrate optimized by HVPE technology was reduced by 60%, lowering the dislocation density to 5 × 105 cm−2. The reduction in dislocation density is primarily attributed to two factors: first, the use of multiple masking technology that prevent the upward propagation of dislocations; second, the alternating 3D−2D growth that leads to the merging and annihilation of some dislocations. This significant improvement is not only visually impressive but also theoretically suggests a reduction in dislocation diffusion during the crystal growth process, thereby potentially enhancing the crystal quality of the epitaxial layer.
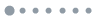
Figure 1.(Color online) Schematic diagram of optimal growth path of GaN single crystal.
In the realm of semiconductor device design, the architecture of the waveguide layer plays an indispensable role in boosting the device's capabilities[16, 17]. In this study, we have integrated an innovative SLs of InGaN/GaN to fabricate the waveguide layer. Specifically, we have incorporated an InGaN/GaN superlattice with a periodicity of 35 Å/8 Å in the lower section of the waveguide, to supplant the traditional InGaN waveguide layer. As shown in Fig. 3(a), the characterization results from the transmission electron microscope (TEM) clearly demonstrate the microstructure of this new configuration. The incorporation of the superlattice structure in the waveguide layer has enhanced the release of stress, thereby significantly mitigating the strain between the lower confinement layer and the quantum wells. Additionally, by leveraging the lateral migration mechanism of the GaN interlayer, the crystalline quality of the lower waveguide layer has been markedly enhanced. This approach has led to a substantial reduction in the incidence of dislocations and stacking faults, concurrently lowering the concentration of InN-rich points and diminishing the presence of non-radiative recombination centers. Subsequent photoluminescence (PL) characterization, as depicted in Fig. 3(b), demonstrates a remarkable increase of approximately 60% in the PL intensity for the optimized sample B, in comparison to the sample A with traditional InGaN lower waveguide. This notable improvement underscores that effective stress mitigation and the reduction of band tilting can substantially augment the overlap of electron and hole wavefunctions, which in turn, elevates quantum efficiency. Such enhancements not only amplify the efficiency of charge carrier recombination but also serve as a direct indicator of the device performance optimization.
In general, severe self-heating issues can significantly impact the performance of LDs under high current injection, especially when operating in continuous wave mode. The LDs fabricated in this work have not yet undergone further packaging optimization, for efficient thermal dissipation, hence they are characterized by working under pulse current, where pulse width: 200 ms, pulse duty cycle: 1%, and tested at a temperature of 25 °C. The maximum LD output power is more than 15 W, the drive current is 10 A, and the corresponding WPE is about 38%, as shown in Fig. 5(a). The slope efficiency remains at 1.8 W/A across the current region, up to 6 A, and slightly decreases due to device heating when the injection current is further increased, with the maximum WPE reaching about 46%. Fig. 5(b) presents the spectrum of the LD, with a peak wavelength of approximately 447 nm, a spectral full width at half maximum (FWHM) of 1.2 nm, tested at a current of 3A and at room temperature, with the illustration depicting the GaN laser in the act of emitting light.
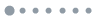
Figure 5.(Color online) (a) The Power-Current-Voltage (PIV) as well as WPE characteristics of the LD. (b) Spectra of the LD, the illustration is a microscopy image of the GaN laser during light emission.
Since Shuji Nakamura first demonstrated the nitride laser in 1996[1], the domain of semiconductor laser technology has undergone a period of remarkable growth[2, 3]. AlInGaN-based diode lasers (LDs) have proven their exceptional capabilities across a spectrum of pivotal applications, including high-density data storage, laser displays, laser lighting, and quantum technology[4]. Despite the notable progress in GaN-based LDs, there remains a significant gap in power density when compared to their GaAs-based counterparts equivalents[5]. With the relentless march of technological advancement and the escalating market demands, the performance of LDs has been put forward higher requirements[6, 7]. Enhancing power density is the key to more efficient energy conversion and more compact device designs, while ensuring long-term stability that is integral to device reliability and reduced maintenance costs. Consequently, the pursuit of increased power density and long-term stability in LDs has become a focal point of interest within both academic and industrial spheres[7].
Post-growth, the blue LD is fabricated into a ridge waveguide laser with a cavity length of 1200 μm and a ridge width of 90 μm. The manufacturing process is the same as that of a regular ridge waveguide LD, except for the facet coating process. For the p-type contact formation, an indium tin oxide (ITO) layer is deposited and annealed at a temperature of 575 °C. High-quality SiO2 thin films are utilized to passivate the surface of the device's sidewall areas, effectively suppressing any leakage currents that may arise from thermally activated surface states, while ensuring that the current is directly and concentratedly injected into the center of the ridge. Ion beam sputtering is utilized for the deposition of both P-type and N-type electrodes. Specifically, the P-type electrode is composed of layers of Cr/Pt/Au, while the N-type electrode pads are fabricated from Ti/Pt/Au. The fabricated bar was then break along m-plane, followed by deposition of high reflection (HR) film and anti-reflection (AR) film on the two cleavage crystal planes using ECR, respectively. Finally, it was diced into a chip and encapsulated in the form of TO9.
To address the aforementioned issues, we have conducted an in-depth investigation into dislocation control during the crystal growth process, stress control in multiple quantum wells (MQWs) and the optimization of crystal facet coating technology. By employing hydride vapor phase epitaxy (HVPE) with multiple maskings and alternating 3D−2D growth, we have effectively reduced the dislocation density. We have also integrated an InGaN/GaN superlattice waveguide structure (SLs) to alleviate stress and enhance the crystal quality. Furthermore, we utilized electron cyclotron resonance (ECR) technology to refine the cavity surface coating process and optimize the COD problem under high current injection. As a result, we successfully demonstrated pulsed laser emission at a wavelength of 447 nm, achieving a maximum output power of 15 W and the corresponding wall-plug efficiency (WPE) of 38%.
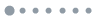
Figure 4.(Color online) AFM images of ECR-deposited (AR)-Al2O3-pre optimization (a), (HR)-Al2O3/Ta2O5-pre optimization (b), (AR)-Al2O3-post optimization (c), and (HR)-Al2O3/Ta2O5-post optimization (d) on GaN cleaved facets.
The blue high-power LD epitaxy is carried out via MOCVD, with the dislocation density of substrate optimized by HVPE technology lower than 5 × 105 cm−2. The structure of the blue LD, from bottom to top, consists of a 1.5-μm n-type AlGaN layer (low Al composition) as the lower confinement layer, a 160-nm n-type InGaN strain layer, a 1.0-micron n-type AlGaN layer (high Al composition) as the lower confinement layer, a 250-nm n-type GaN lower waveguide layer (Si-doped at 3 × 1018 cm−3), a 290-nm InGaN/GaN SLs lower waveguide layer (Si-doped at 3 × 1018 cm−3), two pairs of quantum wells in the MQWs active layer, a 250-nm InGaN upper waveguide layer (undoped), a 20-nm electron blocking layer (20% Al composition, Mg-doped at 1.5 × 1019 cm−3), a 300-nm p-type AlGaN upper confinement layer (Mg-doped at 5 × 1018 cm−3), and a 20-nm p-type GaN contact layer (Mg-doped at 1 × 1021 cm−3).
Within the AlInGaN material system, the epitaxial crystal quality is one of the most paramount factors in determining LD performance. The presence of dislocations and non-radiative recombination centers within the crystal lattice can severely compromise the efficiency and reliability of the devices[8, 9]. These dislocations not only diminish the crystal's optical and electrical properties but may also precipitate device degradation over time. On the other hand, catastrophic optical damage (COD) poses a formidable challenge for high-power LDs[10]. COD, characterized by an abrupt decline in light output under high-power conditions, is intricately linked to the surface recombination rate of the devices[10, 11]. This surface recombination not only erodes device efficiency but also engenders thermal management quandaries that can undermine long-term device stability. In the quest to curb surface recombination and elevate the COD threshold of LDs, a plethora of innovative crystal facet coating technology has been introduced by researchers[3, 12, 13]. These methodologies, which involve the deposition of high-reflectivity dielectric materials on GaN crystal facets, curtail photon escape rates, thereby augmenting device power output and thermal stability. Nonetheless, the quality of the interface between the dielectric material and the GaN crystal facet stands as a critical determinant of the coating's efficacy. The deposition of non-crystalline dielectric materials may introduce a proliferation of interface states, potentially undermining device performance[14, 15].
In short, this study is dedicated to improving the performance of blue laser diodes, focusing on enhancing their power and efficiency through meticulous studies of dislocation control during the crystal growth process and the refinement of crystal facet coating technologies. By leveraging multiple masking technology and employing an alternating 3D−2D growth method in HVPE, we have effectively reduced the dislocation density. Furthermore, the integration of an InGaN/GaN superlattice waveguide structure has facilitated stress relief, thereby enhancing the crystal quality. By optimizing ECR technology to enhance the quality of the thin films, all of this is aimed at increasing the power and efficiency of our lasers. We ultimately achieved pulsed laser emission at a wavelength of 447 nm, obtaining a maximum power output of 15 W and the corresponding WPE is 38%. The outcomes of our experiments not only substantiate the efficacy of our methodologies but also pave the way for future enhancements in the manufacturing process and the exploration of new applications. The significance of these accomplishments cannot be overstated, as they are poised to significantly impact the adoption of blue laser diodes in premium market segments, especially within the realms of laser display and laser processing technologies.